Imagine this: you’re neck-deep in a roofing project, and the thought of waiting for pre-fabricated panels or being limited by standard sizes sends shivers down your spine. What if there was a superhero in the metalworking world that could swoop in and create custom corrugated roof panels on-demand? Well, fret no more, because the Corrugated Roof Panel Roll Forming Machine is here to save the day!
what is a Corrugated Roof Panel Roll Forming Machine?
Think of it as a high-tech metal origami master. It takes continuous coils of sheet metal and, through a series of precisely formed rollers, transforms them into various corrugated shapes. These corrugated panels, with their distinctive wavy pattern, are lightweight yet incredibly strong, making them ideal for a variety of roofing applications.
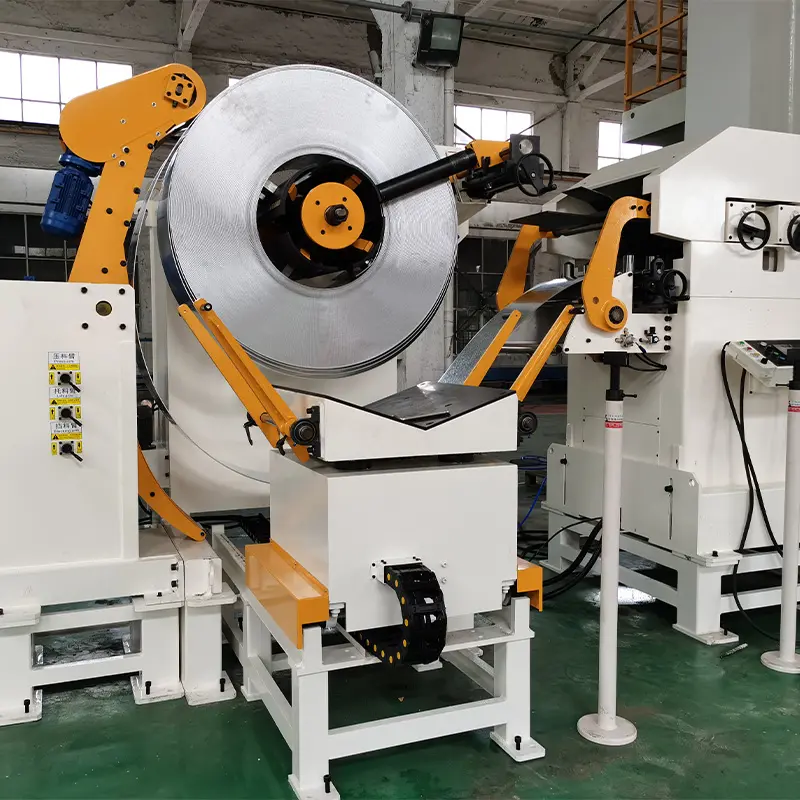
How Does a Corrugated Roof Panel Roll Forming Machine Work?
The process is like watching a well-rehearsed ballet. Here’s a breakdown of the key steps:
- Feeding the Machine: The metal sheet, in coil form, is loaded onto a feeding mechanism that unwinds it steadily.
- Roll Forming Stations: The sheet then progresses through a series of rollers, each one strategically shaped to bend and mold the metal into the desired corrugated profile. The number of rollers can vary depending on the complexity of the profile.
- Cutting and Coiling: Once the desired length is reached, a cutting mechanism precisely severs the formed panel from the coil. Some machines offer coiling functions for easy storage of finished panels.
- Control Panel Magic: The entire operation is orchestrated by a sophisticated control panel. Here, you can program the machine for specific panel lengths, thicknesses, and profile types.
types of Corrugated Roof Panel Variations
The beauty of roll forming machines lies in their versatility. They can produce a wide range of corrugated profiles, each catering to specific needs:
- Sinusoidal Wave: This classic profile, resembling a gentle sine wave, is known for its balanced strength and drainage efficiency.
- trapezoidal Profile: Imagine a trapezoid on its side – that’s the basic shape. This profile offers superior strength and is popular for industrial and commercial buildings.
- U-Shaped Profile: Simple yet effective, the U-shaped profile is lightweight and often used for agricultural buildings and temporary structures.
the Applications of Corrugated Roof Panel Roll Forming Machines
Corrugated panels are true utility players, extending their reach far beyond rooftops. Here are some unexpected applications:
- Wall Cladding: These panels can create durable, weather-resistant walls for sheds, garages, and even prefabricated buildings.
- Fences and Gates: Corrugated panels provide a secure and attractive option for fencing projects.
- Soffit Panels: The underside of your roof overhang can be beautifully finished with corrugated soffit panels.
the Advantages and Disadvantages of a Corrugated Roof Panel Roll Forming Machine
Owning a Corrugated Roof Panel Roll Forming Machine presents a compelling set of advantages:
- Customization Freedom: No more being confined to pre-made panel sizes or styles. You have complete control over the length, thickness, and profile of your panels.
- Reduced Costs: Eliminate the middleman! Producing your own panels can significantly reduce overall roofing material costs, especially for large projects.
- On-Demand Production: Need panels urgently? No problem! With a roll forming machine, you can manufacture panels exactly when you need them, eliminating wait times.
- Inventory Management: Say goodbye to the hassle of storing large quantities of pre-fabricated panels.
However, it’s important to acknowledge the flip side of the coin:
- Initial Investment: Roll forming machines are significant investments. The cost can vary depending on the features, complexity, and brand.
- Operational Expertise: Operating a roll forming machine requires a certain level of training and familiarity with metalworking principles.
- Space Requirements: These machines are not exactly compact. You’ll need a dedicated workspace to house the machine comfortably.
-
Standing Seam Roof Panel Curving Machine
-
Barrel Corrugated Roll Forming Machine
-
Stand Seaming Roof Panel Roll Forming Machine
-
Downspout Pipe Roll Forming Machine
-
Gutter Roll Forming Machine
-
Trapezoidal Panel Roll Forming Machine
-
Ridge Cap Roll Forming Machine
-
Double Layer Panel Roll Forming Machine
-
Roof Tile Panel Roll Forming Machine
Choosing a Corrugated Roof Panel Roll Forming Machine
The perfect roll forming machine, much like a superhero’s utility belt, depends on your specific needs and circumstances. Here are some crucial factors to consider:
- Production Volume: How many panels do you anticipate producing? High-volume operations may require a more robust machine.
- Desired Panel Profiles: The machine’s capabilities should align with the types of corrugated profiles you need.
- Sinusoidal Wave: This classic profile, resembling a gentle sine wave, is known for its balanced strength and drainage efficiency.
- trapezoidal Profile: Imagine a trapezoid on its side – that’s the basic shape. This profile offers superior strength and is popular for industrial and commercial buildings.
- U-Shaped Profile: Simple yet effective, the U-shaped profile is lightweight and often used for agricultural buildings and temporary structures.
- Labor Costs: Factor in any additional labor required for operating the machine and handling the finished panels.
- Downtime Costs: Consider potential downtime due to maintenance or repairs.
By carefully analyzing your roofing project needs and factoring in the cost-saving potential, you can determine if a corrugated roof panel roll forming machine is a financially sound investment.
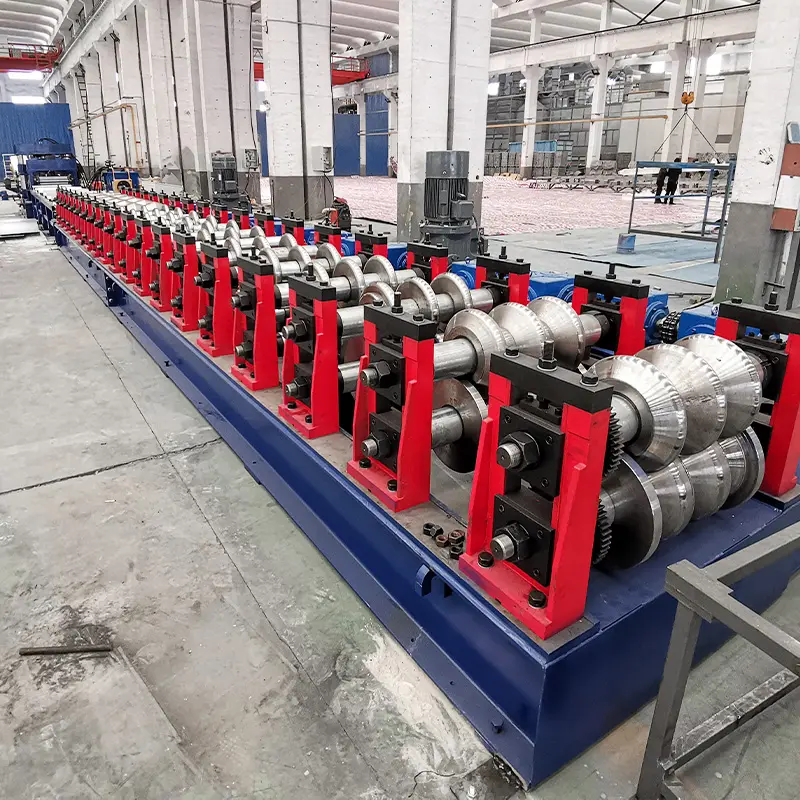
FAQ
Here’s a table addressing some of the most frequently asked questions regarding corrugated roof panel roll forming machines:
Question | Answer |
---|---|
What are the typical applications of corrugated roof panels produced by these machines? | Corrugated roof panels are primarily used for roofing applications on residential, commercial, and industrial buildings. However, their applications extend to wall cladding, fences, gates, soffit panels, and even temporary structures. |
What are the advantages of using corrugated roof panels? | Corrugated panels offer a winning combination of benefits: affordability, lightweight construction, exceptional strength, easy installation, and weather resistance. |
Are there any disadvantages to using corrugated roof panels? | Compared to some other roofing materials, corrugated panels might offer slightly less insulation and noise dampening. Additionally, the visual aesthetics may not be suitable for all architectural styles. |
How difficult is it to learn how to operate a corrugated roof panel roll forming machine? | The learning curve depends on the specific machine’s complexity. Basic models might require minimal training, while advanced machines with computer-controlled operations might benefit from a more in-depth learning process. Regardless, consulting the user manual and potentially seeking manufacturer-provided training can significantly ease the learning curve. |
What safety measures are essential when operating a corrugated roof panel roll forming machine? | Wearing proper PPE (safety glasses, gloves, footwear), maintaining a safe distance from moving parts, being aware of pinch points, and keeping loose clothing and jewelry away from the machine are paramount safety practices. Familiarity with the emergency stop button is also crucial. |
How often does a corrugated roof panel roll forming machine require maintenance? | Regular cleaning, lubrication (as per manufacturer recommendations), and periodic roller inspections are essential for optimal performance and longevity. Additionally, staying updated on software updates can further enhance the machine’s functionality. |
In Conclusion
Corrugated roof panel roll forming machines are more than just metalworking marvels; they are tools that empower you to take control of your roofing projects. By understanding their capabilities, operational considerations, and the potential return on investment, you can make an informed decision about whether this innovative technology is the perfect fit for your needs.
So, if you’re looking to add customization, cost-efficiency, and on-demand production to your roofing endeavors, a corrugated roof panel roll forming machine might just be your next roofing project superhero!