Corrugated metal has become a go-to choice for siding due to its durability, aesthetic appeal, and versatility. Whether you’re a homeowner, contractor, or architect, choosing corrugated metal for your siding project can enhance the overall look and function of your structure. But with a variety of options, materials, and installation methods, where do you begin?
In this comprehensive guide, we will dive deep into corrugated metal siding, discussing everything from different types of metal sheets, their properties, the installation process, machine efficiency, key components, and even the pros and cons. Let’s get started!
Overview: What is Corrugated Metal Siding?
Corrugated metal siding consists of metal sheets, often aluminum, steel, or zinc, that are shaped into ridges or grooves. These ridges, or corrugations, increase the strength of the metal without adding much weight. This makes it an excellent choice for siding as it provides superior durability while maintaining an industrial and modern aesthetic.
Corrugated metal siding is popular for its:
- Durability: Resists harsh weather conditions, rust, and impact.
- Aesthetic appeal: Offers a modern, sleek, and industrial look.
- Cost-effectiveness: Relatively affordable compared to other materials.
- Versatility: Can be used for residential, commercial, and industrial applications.
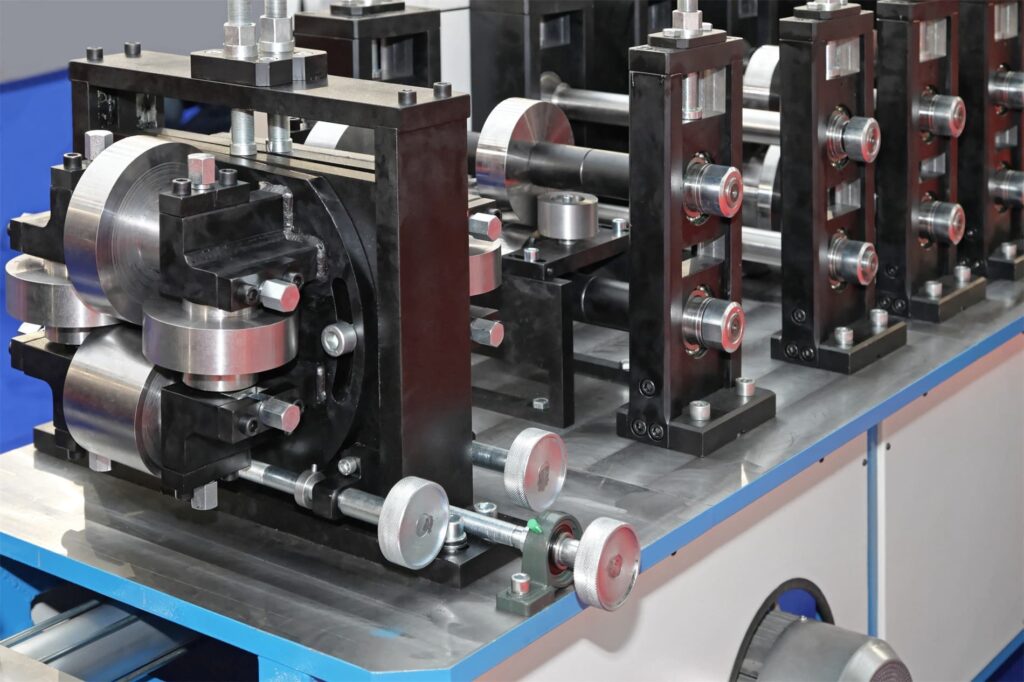
Types of Corrugated Metal for Siding
When selecting corrugated metal for siding, it’s important to understand the types of metals available. Different metals have varying levels of durability, corrosion resistance, weight, and appearance. Here’s a breakdown of popular corrugated metals:
Type of Metal | Properties | Applications | Aesthetic Appeal | Corrosion Resistance | Weight |
---|---|---|---|---|---|
Galvanized Steel | Coated with zinc for corrosion protection | Residential, Commercial | Industrial, Sleek | High | Medium |
Aluminum | Lightweight, corrosion-resistant | Coastal, Residential | Sleek, Modern | Excellent | Very Light |
Weathering Steel (Corten) | Forms a stable rust-like appearance | Outdoor, Industrial | Rustic, Weathered | Moderate | Heavy |
Copper | Develops a patina over time | High-end, Decorative | Distinctive, Elegant | Moderate | Heavy |
Stainless Steel | High resistance to corrosion | Industrial, Coastal | Polished, Clean | Excellent | Medium |
Zinc | Naturally self-healing, low-maintenance | Residential, Custom Homes | Smooth, Matte Finish | Excellent | Light |
Galvanized Steel vs. Aluminum: Which is Better?
If you’re wondering which material to choose, galvanized steel is more affordable and provides excellent durability in non-coastal environments. However, for coastal areas or areas with high moisture, aluminum is better because of its high resistance to corrosion and rust.
Corrugated Iron Sheets: A Complete Guide
Corrugated iron sheets are one of the most popular materials for siding due to their high strength-to-weight ratio, affordability, and ease of installation. Iron sheets have been used for decades in both residential and commercial projects.
Here are some popular corrugated iron sheet models:
Model | Description | Thickness | Weight per m² | Best Use Case |
---|---|---|---|---|
Galvalume G-90 | Galvanized with a blend of zinc and aluminum for extra corrosion resistance | 0.7 mm | 7 kg | Residential Siding |
Ultra-Rib | High corrugations for extra rigidity | 0.5 mm | 6 kg | Industrial Buildings |
Corten A588 | Weathering steel, forms a protective rust layer | 1.2 mm | 12 kg | Outdoor, Weather-exposed Structures |
Aluminum T-36 | Lightweight, excellent for humid environments | 0.45 mm | 4 kg | Coastal Siding |
Stainless Steel S-18 | Extremely durable and rust-proof | 0.8 mm | 8 kg | Industrial and Commercial Buildings |
Copper V-9 | Premium option with unique appearance, develops patina | 1.0 mm | 10 kg | Decorative or High-End Siding |
These models provide various options in terms of thickness, weight, and use cases. For example, Corten A588 is perfect for outdoor applications because it develops a protective rust layer that resists further corrosion. On the other hand, Aluminum T-36 is great for coastal environments due to its natural resistance to saltwater corrosion.
How Corrugated Metal Siding Works
The process of installing corrugated metal siding involves preparing the surface, measuring and cutting the metal sheets, securing them to the building’s frame, and sealing joints. Here’s an overview of the process:
- Preparation: Ensure the wall or surface where the siding will be applied is even, and remove any debris or old material.
- Measurement: Accurately measure the height and width of the wall to determine the number of sheets required.
- Cutting: Use tin snips or a circular saw to cut the sheets to the desired length.
- Installation: Starting from the bottom, attach the sheets to the wall using screws or nails at the ridges.
- Sealing: Apply a sealant to the joints between sheets to prevent moisture penetration.
Key Components of Corrugated Metal Siding
Component | Function |
---|---|
Corrugated Sheets | The main material that covers the structure, providing protection and aesthetic appeal. |
Fasteners | Screws or nails used to attach the metal sheets to the structure securely. |
Trim | Metal pieces that cover edges, corners, and openings for a clean finish. |
Sealant | A waterproof material applied between sheets to prevent water infiltration. |
Furring Strips | Thin wooden or metal strips installed on walls to create a flat surface for attaching the corrugated sheets. |
Underlayment | A protective layer applied under the metal siding to prevent moisture from reaching the building’s walls. |
-
Carriage Board Roll Forming Machine
-
Highway Guardrail End Terminal Forming Machine
-
Highway U/C Post Roll Forming Machine
-
2 Waves Highway Guardrail Roll Forming Machine
-
3 Waves Highway Guardrail Roll Forming Machine
-
Vineyard Post Roll Forming Machine
-
Auto Size Changeable Sigma Purlin Roll Forming Machine
-
Electrical Cabinet Frame Roll Forming Machine
-
Din Rail Roll Forming Machine
Machine Efficiency in Corrugated Metal Siding Production
When producing corrugated metal sheets, machine speed and efficiency are critical factors. Here’s a quick comparison of common machines used in the production process:
Machine Model | Speed (sheets/hour) | Efficiency (%) |
---|---|---|
Roll Former 5000 | 300 | 90% |
Corrugator X-700 | 250 | 88% |
MetalForm 2000 | 400 | 92% |
SheetPro RS-360 | 350 | 91% |
Higher efficiency machines, such as the MetalForm 2000, can produce more sheets per hour, making them a better choice for large-scale projects. However, for smaller operations, a machine like the Corrugator X-700 may be sufficient.
Customized Mechanical Parameters for Corrugated Metal Siding
Customization is a critical aspect of corrugated metal production, allowing clients to specify parameters such as thickness, corrugation height, and width. Below are customizable mechanical parameters for different types of siding:
Parameter | Range | Function |
---|---|---|
Sheet Thickness | 0.3 mm – 1.5 mm | Determines the strength and weight of the metal siding. |
Corrugation Height | 15 mm – 45 mm | Impacts the rigidity and appearance of the siding. |
Width | 600 mm – 1200 mm | Affects the coverage area of each sheet. |
Length | 1 m – 6 m | Customizable based on wall height or project requirements. |
Applications of Corrugated Metal for Siding
Corrugated metal siding is incredibly versatile and can be used in a variety of settings:
Application | Description |
---|---|
Residential | Used for exterior cladding of homes to create a modern, industrial aesthetic. |
Commercial | Popular for storefronts, warehouses, and office buildings, providing a sleek, durable finish. |
Agricultural | Commonly used for barns, silos, and other farm structures due to its low maintenance and strength. |
Industrial | Ideal for factories and industrial buildings because of its resistance to harsh environments. |
Architectural | Corrugated metal can also be used in high-end architectural projects for its unique appearance and design flexibility. |
Installation, Operation, and Maintenance of Corrugated Metal Siding
Proper installation, operation, and maintenance are key to ensuring the longevity of your corrugated metal siding. Here’s a basic guide:
Task | Description |
---|---|
Installation | Attach the metal sheets with screws or nails, starting from the bottom and working upwards. Make sure to overlap each sheet to ensure watertightness. |
Operation | Corrugated metal siding is a passive product, requiring little day-to-day operation. |
Maintenance | Regularly inspect for rust (on non-aluminum products), and clean the siding with a mixture of water and mild detergent. Reapply sealant to joints every 5-10 years, depending on environmental conditions. |
Choosing the Right Supplier for Corrugated Metal Siding
Choosing the right supplier can make or break your project. Here’s a list of some leading suppliers
and their price ranges for corrugated metal siding:
Supplier | Price Range (per m²) | Location | Specialty |
---|---|---|---|
ABC Metal Roofing | $15 – $30 | USA | Custom lengths and colors |
Metal Sales | $12 – $25 | USA | Large variety of materials |
Fabral | $10 – $22 | USA | Sustainable, eco-friendly options |
Stratco | $18 – $35 | Australia | High-quality galvanization |
Kingspan | $20 – $40 | UK | Insulated metal panels |
How to Choose the Best Supplier for Corrugated Metal Siding
Here are a few things to consider when choosing the best supplier for your corrugated metal siding needs:
Factor | Description |
---|---|
Reputation | Look for reviews and testimonials from previous clients. |
Product Variety | Does the supplier offer a variety of metals, colors, and finishes? |
Customization | Can the supplier meet specific project requirements, such as size and finish? |
Lead Time | How quickly can the supplier deliver your order? |
Price | Compare the price per square meter and ensure it aligns with your budget. |
Pros and Cons of Corrugated Metal Siding
As with any material, corrugated metal siding comes with its advantages and limitations. Here’s a quick comparison:
Advantages | Disadvantages |
---|---|
Durability: Can last up to 50 years with proper maintenance. | Noise: Can be noisy during heavy rain or hailstorms. |
Low Maintenance: Requires minimal upkeep compared to wood or vinyl. | Cost: Premium metals like copper or stainless steel can be expensive. |
Aesthetic Appeal: Provides a modern, industrial look that’s in trend. | Corrosion (non-aluminum): Certain metals can rust if not properly maintained. |
Versatile: Can be used in residential, commercial, and industrial settings. | Limited Insulation: Metal is not the best insulator, and additional layers may be needed. |
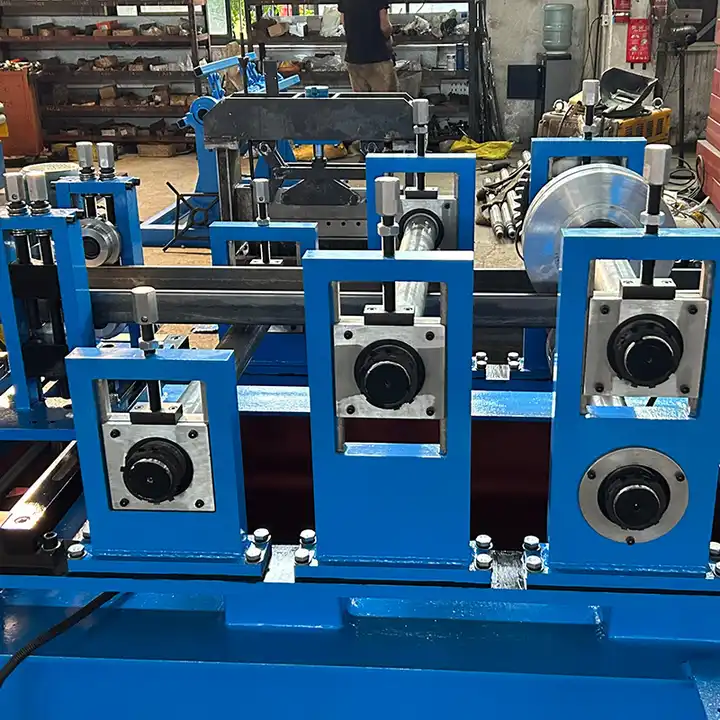
FAQ
Question | Answer |
---|---|
What is the lifespan of corrugated metal siding? | Depending on the material and maintenance, corrugated metal siding can last anywhere from 30 to 50 years. |
Can corrugated metal be painted? | Yes, corrugated metal can be painted in a variety of colors to match your design. It’s recommended to use a weather-resistant, metal-specific paint. |
Is corrugated metal siding energy efficient? | Metal reflects sunlight, which can help in reducing cooling costs during summer, but you may need additional insulation during colder months. |
How do I clean my corrugated metal siding? | A simple mix of water and mild detergent, along with a soft brush or cloth, will do the trick. Rinse thoroughly with water. |
What’s the best metal for coastal areas? | Aluminum is the best choice for coastal areas because it’s naturally resistant to saltwater corrosion. |
Conclusion
Corrugated metal siding is a durable, versatile, and aesthetically pleasing option for a variety of buildings. Whether you choose galvanized steel, aluminum, or a premium material like copper, it provides excellent protection and a sleek, modern look. By understanding the different types, installation process, and machine efficiency, you can make an informed decision that aligns with your project’s needs.
Whether you’re a DIY homeowner or a contractor, corrugated metal siding can be tailored to your specifications, making it a cost-effective and long-lasting solution for any project.