Overview
Corrugated metal sheets are a staple in construction, agriculture, and industrial applications due to their durability, strength, and versatile uses. These sheets are characterized by their wavy surface, which enhances their structural integrity and aesthetic appeal. This article dives into the intricacies of corrugated metal sheets, from their production process to their various applications, and everything in between.
Roll Forming Machine Guide
Roll forming machines are essential in the production of corrugated metal sheets. These machines shape metal into the desired corrugated pattern through a continuous bending process. Here’s a brief guide on how they work:
- Loading: Metal coils are fed into the machine.
- Forming: Rollers progressively shape the metal into the corrugated profile.
- Cutting: The formed metal sheet is cut to the required length.
- Output: Finished sheets are stacked and prepared for transportation.
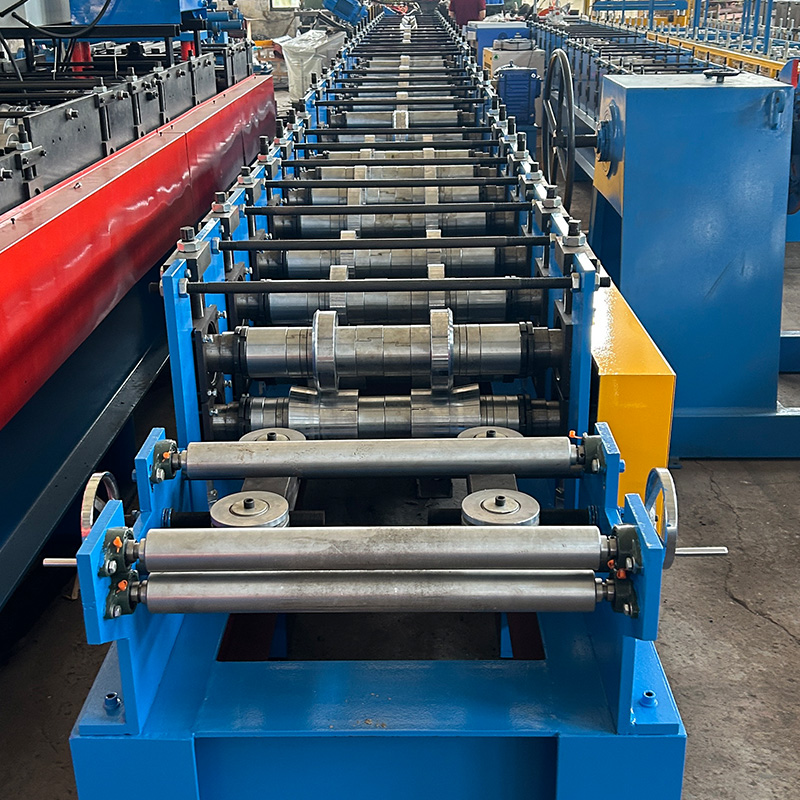
Types of Corrugated Metal Sheets
Type | Description |
---|---|
Galvanized Steel | Highly resistant to rust and corrosion, ideal for outdoor applications. |
Stainless Steel | Offers superior strength and corrosion resistance, often used in harsh environments. |
Aluminum | Lightweight and resistant to corrosion, suitable for both residential and commercial use. |
Copper | Highly durable and offers a unique aesthetic appeal, often used for architectural purposes. |
Zinc | Provides excellent corrosion resistance and is eco-friendly, commonly used in roofing. |
PVC Coated Steel | Combines the strength of steel with the weather resistance of PVC, suitable for harsh climates. |
Fiberglass | Lightweight and resistant to moisture, used in environments with high humidity. |
Polycarbonate | Extremely durable and impact-resistant, often used in industrial settings. |
Titanium | Extremely strong and lightweight, with excellent resistance to corrosion, often used in specialized industrial applications. |
Colorbond Steel | Pre-painted steel that offers both durability and aesthetic variety, widely used in residential and commercial buildings. |
Working Process of Corrugated Metal Sheets
The production of corrugated metal sheets involves several critical steps to ensure quality and consistency. Here’s a detailed look into the working process:
- Material Selection: High-quality metal coils are chosen based on the intended application.
- Cleaning and Preparation: The metal coils are cleaned to remove any impurities that might affect the forming process.
- Roll Forming: The cleaned metal coils are fed into the roll forming machine, where rollers gradually bend the metal into the desired corrugated shape.
- Cutting and Sizing: After forming, the continuous metal strip is cut into sheets of specified lengths.
- Surface Treatment: Depending on the type of metal, various surface treatments such as galvanizing, painting, or coating are applied to enhance durability and aesthetics.
- Quality Control: Finished sheets undergo rigorous quality checks to ensure they meet industry standards.
- Packaging and Shipping: Approved sheets are packaged and prepared for delivery to customers.
Key Components and Their Functions
Component | Function |
---|---|
Rollers | Shape the metal into the corrugated profile. |
Cutting Mechanism | Cuts the formed metal into the required lengths. |
Feeder | Ensures continuous feeding of metal coils into the machine. |
Control System | Regulates the speed, pressure, and other parameters of the roll forming process. |
Guides | Keep the metal aligned and ensure accurate formation. |
Surface Treatment Unit | Applies coatings or treatments to the metal surface for enhanced durability and aesthetic appeal. |
-
Highway Guardrail End Terminal Forming Machine
-
Highway U/C Post Roll Forming Machine
-
2 Waves Highway Guardrail Roll Forming Machine
-
3 Waves Highway Guardrail Roll Forming Machine
-
C Section Bracing Omega Storage Rack Upright Post Roll Forming Machine
-
Steel Box Plate Making Roll Forming Machine
-
Box Beam Steel Roll Forming Machine For Shelf Column
-
Pallet Racking Step Beam P Beam Roll Forming Machine
-
Warehouse Shelf Upright Roll Forming Machine
Machine Speed and Efficiency
Machine Type | Speed (m/min) | Efficiency (%) |
---|---|---|
Standard Roll Former | 20-30 | 85 |
High-Speed Roll Former | 40-50 | 90 |
Custom Roll Former | 25-35 | 88 |
Customized Mechanical Parameters
Parameter | Range |
---|---|
Thickness | 0.2mm – 2.0mm |
Width | 600mm – 1500mm |
Length | Customizable |
Material | Steel, Aluminum, etc. |
Coating | Galvanized, Painted, etc. |
Applications or Uses
Application | Description |
---|---|
Roofing | Durable and weather-resistant, suitable for residential, commercial, and industrial buildings. |
Wall Cladding | Provides structural strength and aesthetic appeal, commonly used in modern architecture. |
Fencing | Offers security and durability, ideal for agricultural and industrial properties. |
Sheds and Outbuildings | Easy to install and maintain, perfect for temporary and permanent structures. |
Greenhouses | Lightweight and corrosion-resistant, ideal for creating controlled environments for plants. |
Vehicle Garages | Strong and weatherproof, suitable for protecting vehicles from the elements. |
Interior Design | Adds a rustic or industrial look to interior spaces, popular in modern and contemporary home designs. |
Shipping Containers | Durable and secure, used for transporting goods and converting into modular living or office spaces. |
Agricultural Buildings | Resistant to weather and pests, commonly used for barns, silos, and other agricultural structures. |
Industrial Enclosures | Provides protection for machinery and equipment, used in various industrial settings. |
Installation, Operation, and Maintenance
Stage | Details |
---|---|
Installation | Ensure a level surface, use appropriate fasteners, and follow manufacturer guidelines. |
Operation | Regularly inspect for damage, clean surfaces to prevent corrosion, and ensure proper ventilation. |
Maintenance | Periodically check for loose fasteners, repair any damages promptly, and reapply protective coatings as needed. |
Suppliers and Price Range Details
Supplier | Price Range (per square meter) | Description |
---|---|---|
ABC Metals | $5 – $10 | Offers a wide range of galvanized and stainless steel sheets. |
XYZ Sheets | $6 – $12 | Specializes in custom sizes and coatings. |
MetalWorks | $7 – $15 | High-quality aluminum and copper sheets. |
SteelCo | $8 – $14 | Focuses on heavy-duty industrial-grade sheets. |
EcoMetals | $6 – $13 | Provides eco-friendly zinc and PVC-coated sheets. |
How to Choose a Supplier
When choosing a supplier for corrugated metal sheets, consider the following factors:
- Quality: Ensure the supplier offers high-quality materials that meet industry standards.
- Variety: Look for suppliers that provide a wide range of materials and customization options.
- Price: Compare prices from different suppliers to get the best deal.
- Reputation: Check reviews and ratings to gauge the supplier’s reliability and customer service.
- Delivery: Ensure the supplier can deliver to your location within a reasonable timeframe.
- Support: Choose suppliers who offer excellent after-sales support and warranties.
Pros and Cons: Advantages and Limitations
Aspect | Advantages | Limitations |
---|---|---|
Durability | Long-lasting and resistant to weather and pests. | Can be prone to rust if not properly treated. |
Strength | High structural integrity, suitable for various applications. | Heavier materials can be challenging to handle and install. |
Versatility | Available in various materials and finishes. | Customization can increase cost. |
Aesthetics | Offers a modern and industrial look. | May not be suitable for all architectural styles. |
Cost | Generally cost-effective compared to other materials. | High-quality options can be expensive. |
Maintenance | Low maintenance with proper treatment. | Requires periodic inspection and maintenance to prevent damage. |
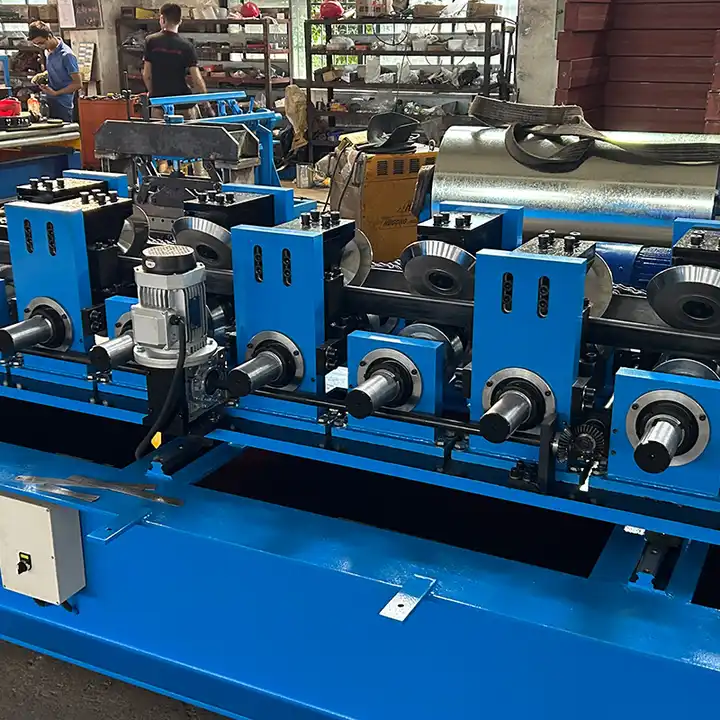
FAQ
Question | Answer |
---|---|
What are corrugated metal sheets used for? | They are used in roofing, wall cladding, fencing, sheds, greenhouses, garages, interior design, shipping containers, agricultural buildings, and industrial enclosures. |
What is the lifespan of corrugated metal sheets? | With proper maintenance, they can last 20-50 years or more, depending on the material and environmental conditions. |
How do you install corrugated metal sheets? | Installation involves ensuring a level surface, using appropriate fasteners, and following manufacturer guidelines for alignment and spacing. |
Are corrugated metal sheets eco-friendly? | Some types, like zinc and aluminum, are eco-friendly and recyclable. Suppliers like EcoMetals offer environmentally friendly options. |
Can corrugated metal sheets be painted? | Yes, they can be painted or coated for added protection and aesthetic appeal. Pre-painted options like Colorbond steel are also available. |
What is the best way to clean corrugated metal sheets? | Regular cleaning with water and mild detergent helps prevent corrosion and maintain appearance. Avoid abrasive cleaners that can damage the surface. |
Do corrugated metal sheets provide good insulation? | While they offer some thermal insulation, additional insulation materials are often used to enhance energy efficiency in buildings. |
Can they be used in coastal areas? | Stainless steel and aluminum sheets are particularly suitable for coastal areas due to their high resistance to saltwater corrosion. |
What are the customization options? | Customization options include material type, thickness, width, length, surface coatings, and colors to suit specific needs and preferences. |
In conclusion, corrugated metal sheets offer a versatile, durable, and cost-effective solution for a variety of applications. By understanding the production process, key components, and considerations for choosing a supplier, you can make an informed decision that meets your specific needs. Whether you’re looking for roofing, wall cladding, or any other application, there’s a corrugated metal sheet option that fits the bill.