Overview
Corrugated metal roofing has grown in popularity over the years, offering a blend of durability, aesthetic appeal, and cost-effectiveness. Whether you’re considering it for residential, commercial, or agricultural purposes, understanding its nuances can make a significant difference in your roofing decisions. In this guide, we’ll explore the intricacies of corrugated metal roofing, its types, the manufacturing process, and much more to provide a thorough understanding.
Roll Forming Machine Guide
Roll forming is a continuous bending operation in which a long strip of metal is passed through consecutive sets of rolls mounted on stands. Each set performs only an incremental part of the bend, until the desired cross-section profile is obtained.
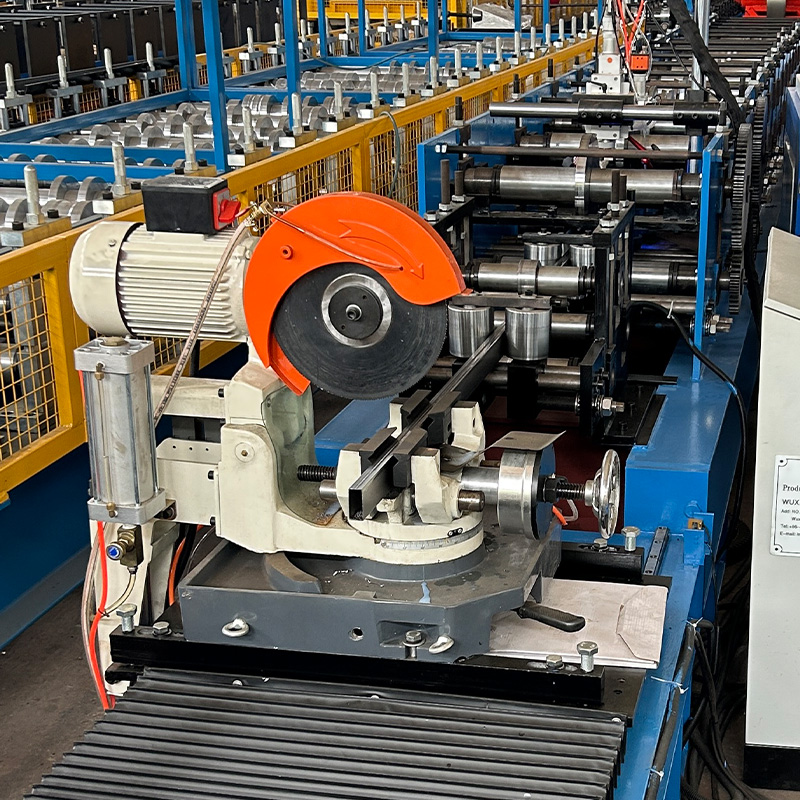
Types of Corrugated Metal Roofing
Type | Description |
---|---|
Galvanized Steel | Known for its zinc coating, offering excellent rust resistance and durability. |
Aluminum | Lightweight and resistant to corrosion, making it ideal for coastal areas. |
Copper | Offers a unique aesthetic appeal and excellent durability, though it’s more expensive. |
Stainless Steel | Highly resistant to corrosion and offers a sleek, modern look. |
Zinc | Known for its longevity and self-healing properties, zinc is a sustainable option. |
Tin | A traditional choice, often used in historical buildings and restorations. |
Hybrid Materials | Combines different metals for enhanced properties and performance. |
Powder Coated Metal | Offers additional protection and a variety of color options. |
Stone-Coated Metal | Mimics the look of traditional shingles with the durability of metal. |
Painted Metal | Provides aesthetic versatility with different colors and finishes. |
Working Process of Corrugated Metal Roofing
The working process of corrugated metal roofing involves several stages, each crucial for ensuring the quality and durability of the final product.
- Material Selection: Choosing the right type of metal based on the intended application and environmental factors.
- Cutting: The metal sheets are cut to the desired size using precision cutting tools.
- Corrugation: The sheets are passed through a roll-forming machine that bends the metal into the corrugated shape.
- Coating: Depending on the type, the metal may be coated with zinc, paint, or other protective layers.
- Quality Control: Each sheet undergoes rigorous testing to ensure it meets the required standards.
Key Components and Their Functions
Component | Function |
---|---|
Metal Sheets | The primary material that provides the roofing surface. |
Fasteners | Secure the metal sheets to the roofing structure. |
Sealants | Ensure watertight seals between sheets and fasteners. |
Underlayment | Provides an additional layer of protection against moisture. |
Flashing | Prevents water from entering at joints and edges. |
Trim | Covers the edges and corners for a finished look. |
Vents | Allow for proper airflow and ventilation. |
Gutters | Direct water away from the roof and foundation. |
-
Highway Guardrail End Terminal Forming Machine
-
Highway U/C Post Roll Forming Machine
-
2 Waves Highway Guardrail Roll Forming Machine
-
3 Waves Highway Guardrail Roll Forming Machine
-
C Section Bracing Omega Storage Rack Upright Post Roll Forming Machine
-
Steel Box Plate Making Roll Forming Machine
-
Box Beam Steel Roll Forming Machine For Shelf Column
-
Pallet Racking Step Beam P Beam Roll Forming Machine
-
Warehouse Shelf Upright Roll Forming Machine
Machine Speed and Efficiency
Machine Type | Speed | Efficiency |
---|---|---|
Standard Roll Former | 30-60 ft/min | High |
High-Speed Roll Former | 60-120 ft/min | Very High |
Custom Roll Former | Variable | Depends on customization |
Customized Mechanical Parameters
Parameter | Standard Value | Custom Range |
---|---|---|
Thickness | 0.3-0.8 mm | 0.2-1.0 mm |
Width | 800-1250 mm | 600-1500 mm |
Length | Up to 12 m | Variable |
Coating Thickness | 20-275 g/m² | 10-300 g/m² |
Corrugation Depth | 18-76 mm | 10-100 mm |
Applications and Uses
Application | Description |
---|---|
Residential Roofing | Offers a modern look and long-term durability. |
Commercial Roofing | Ideal for large structures due to its strength and efficiency. |
Agricultural Buildings | Provides excellent protection for barns and silos. |
Industrial Facilities | Durable and able to withstand harsh conditions. |
Architectural Projects | Used for aesthetic purposes in modern architecture. |
Sheds and Garages | Easy to install and maintain. |
Fencing | Used for decorative and protective fencing solutions. |
Interior Design | Utilized for unique interior elements like ceilings and walls. |
Installation, Operation, and Maintenance
Aspect | Details |
---|---|
Installation | Requires precise alignment and fastening; typically done by professionals. |
Operation | Minimal operational needs once installed; primarily involves periodic inspections. |
Maintenance | Regular cleaning, checking for rust and corrosion, and ensuring all fasteners are secure. |
Suppliers and Price Range
Supplier | Price Range (per sq. ft.) |
---|---|
ABC Metal Roofing | $2.50 – $5.00 |
Metal Sales Manufacturing | $2.00 – $4.50 |
MBCI | $2.25 – $5.25 |
Fabral | $2.75 – $5.50 |
Central States Manufacturing | $2.40 – $4.80 |
Reed’s Metals | $2.30 – $4.70 |
Union Corrugating | $2.20 – $5.00 |
Klauer Manufacturing | $2.50 – $5.10 |
McElroy Metal | $2.60 – $5.40 |
Berridge Manufacturing | $2.80 – $5.60 |
Choosing a Supplier
Selecting the right supplier for your corrugated metal roofing can make a significant difference in both quality and cost.
- Reputation: Look for suppliers with positive reviews and a solid reputation in the industry.
- Quality: Ensure the supplier provides high-quality materials that meet industry standards.
- Customization: If you need custom sizes or coatings, check if the supplier can accommodate your requirements.
- Pricing: Compare prices among different suppliers to find the best deal without compromising quality.
- Customer Service: Good customer support can help address any issues or questions you may have during the installation process.
Advantages and Limitations
Aspect | Advantages | Limitations |
---|---|---|
Durability | Long-lasting and resistant to extreme weather. | Can be noisy during rain or hail. |
Aesthetic Appeal | Available in various colors and styles. | Some people may prefer the look of traditional shingles. |
Cost | Cost-effective over the long term due to low maintenance. | Higher initial cost compared to some other materials. |
Environmental Impact | Often made from recycled materials and fully recyclable. | Energy consumption during production. |
Installation | Quick and easy installation process. | Requires professional installation for best results. |
Equipment Parameters, Price Ranges, and Forming Process
Parameter | Details |
---|---|
Roll Forming Machine Cost | $50,000 – $150,000 |
Sheet Metal Thickness | 0.3-0.8 mm |
Sheet Width | 800-1250 mm |
Forming Speed | 30-120 ft/min |
Applications Area
Area | Details |
---|---|
Residential | Homes, garages, sheds. |
Commercial | Warehouses, offices, stores. |
Agricultural | Barns, silos, storage buildings. |
Industrial | Factories, plants, processing facilities. |
Architectural | Unique designs, facades, interior elements. |
Installation, Operation, Maintenance Details
Aspect | Details |
---|---|
Installation | Ensure proper alignment, use correct fasteners, follow manufacturer guidelines. |
Operation | Regular inspections, minimal day-to-day operation. |
Maintenance | Clean periodically, check for corrosion, tighten fasteners as needed. |
How to Choose a Supplier
When it comes to selecting a supplier for corrugated metal roofing, consider the following factors:
- Quality Assurance: Ensure the supplier provides a warranty and adheres to industry standards.
- Range of Products: A diverse product range allows for better customization and choice.
- Customer Reviews: Look for feedback from previous customers to gauge reliability.
- Support Services: Good after-sales support can help with installation and maintenance queries.
- Price Comparison: Get quotes from multiple suppliers to ensure competitive pricing.
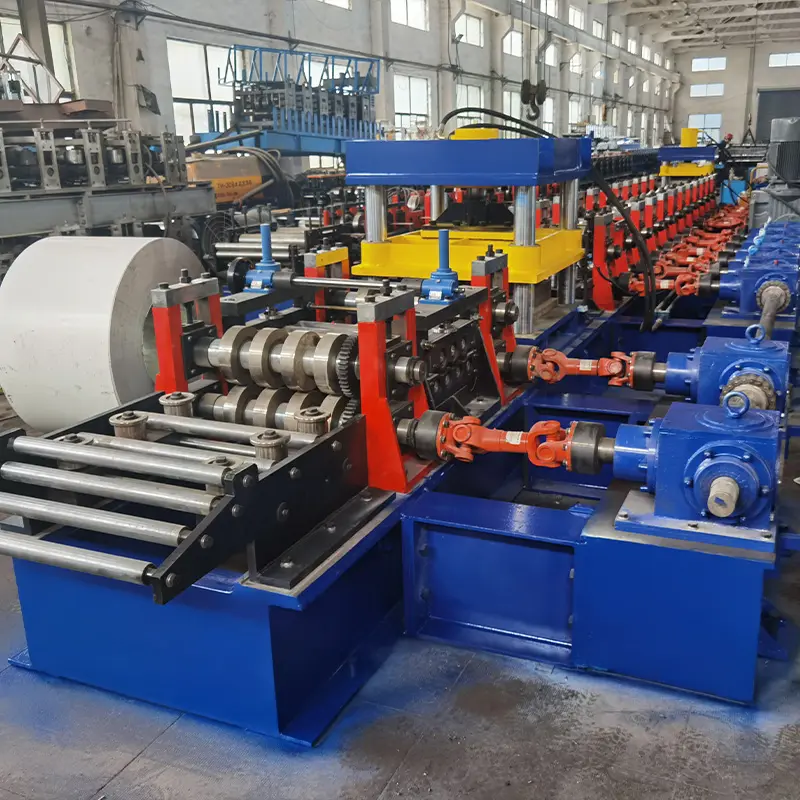
FAQ
Question | Answer |
---|---|
What is corrugated metal roofing? | Corrugated metal roofing is a type of roofing material made from metal sheets formed into a wave-like pattern. |
Why choose corrugated metal roofing? | It is durable, cost-effective, and provides a modern aesthetic. |
How long does corrugated metal roofing last? | It can last between 30-50 years, depending on the material and maintenance. |
Is it noisy during rain? | Yes, it can be noisier than other roofing materials, but proper insulation can reduce noise. |
Can it be installed DIY? | While possible, professional installation is recommended for best results. |
What maintenance is required? | Regular cleaning and inspection for rust or loose fasteners are essential. |
Is it environmentally friendly? | Yes, most corrugated metal roofing is made from recycled materials and is fully recyclable. |
What are the cost considerations? | Initial cost is higher, but low maintenance and longevity make it cost-effective in the long run. |
Can it be painted? | Yes, many types of corrugated metal roofing can be painted to match your aesthetic preferences. |
What are the common applications? | Residential homes, commercial buildings, agricultural structures, and industrial facilities. |
Conclusion
Corrugated metal roofing offers a plethora of benefits that make it a top choice for various applications. From its durability and cost-effectiveness to its aesthetic appeal and versatility, this roofing material has much to offer. By understanding the types, manufacturing process, key components, and supplier options, you can make an informed decision that meets your needs and ensures long-term satisfaction. Whether you’re building a new structure or replacing an old roof, corrugated metal roofing is a robust and reliable option that stands the test of time.