Overview of China glazed tile roll forming machine
China glazed tile roll forming machine refers to continuous cold roll-forming equipment engineered specifically for producing colorful ceramic-coated steel roofing tiles rapidly from coil stock. These versatile Chinese roll formers shape flat metal strip into popular interlocking roof tile profiles at high volumes serving construction markets.
Key features:
- Efficiently mass produces metal shingles at low costs
- Widths from 300mm up to 1000mm
- Metal thickness from 0.3mm to 0.8mm
- Glazed ceramic coatings in variety of colors
- Support interlocks on leading/trailing edges
- Quick changeover tooling modifies profiles
- Automatic bundle strapping/packaging solutions
China manufacturers offer unmatched value producing quality roll formed glazed steel tiles for global buyers.
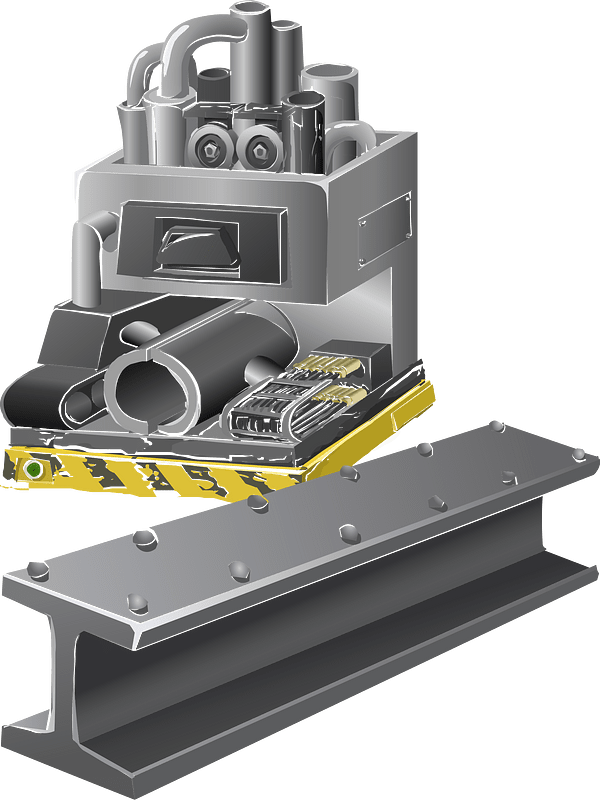
Machine Types
Type | Description |
---|---|
Fully Automatic | Inline decoiler, forming, cutting, stacker |
Standard Tile widths | 300mm to 1000mm profiles |
Structural Section | Heavy frames suit thickest metals |
Table 1: Main glazed tile roll former types by automation level and construction
Higher degree of automation boosts output rates to maximize efficiency. Structural capabilities handle steel thickness over 0.6mm.
Working Principle
The progressive cold roll-forming process shapes popular roofing tile profiles:
- Prepainted coil strip enters the line from a decoiler
- Gradually formed by 10+ bending & shaping stations
- Upper/lower rolls emboss 3D texture and interlocks
- Punch or saw cutoff separates into set lengths
- Formed tiles conveyed for automatic stacking
Servo feed controls combined with PLCs precisely index coil through equipment synchronizing multi-step tile forming.
Machine Components
Component | Description |
---|---|
Decoiler | Feeds strip from main coil payload |
Forming Dies | Progressively cold-work sheet into wave profiles |
Texturing Rollers | Emboss top surface relief and graining |
Cutoff Module | Punch or saw cuts tiles to length |
Exit Conveyors | Catch formed parts for bundle stacking |
Control Cabinet | Stores recipes; monitors operation |
Table 2: Overview of primary subsystems in a glazed tile cold roll former line
Latest servo electric designs provide precision alignment of components for optimizing accuracy during high speed production.
-
Vineyard Post Roll Forming Machine
-
Auto Size Changeable Sigma Purlin Roll Forming Machine
-
PV Mounting Bracket C Shape Profile Roll Forming Machine
-
C Z Purlin Channel Cold Roll Forming Machine Full Auto Galvanized Steel Profile
-
PV Mounting Bracket Roll Forming Machine (HAT / Omega Profile)
-
PV Mounting Bracket Z Shape Profile Roll Forming Machine
Materials and Sizes
Common glazed tile specifications accommodated:
Parameter | Range |
---|---|
Tile Width | 300mm, 450mm, 600mm, 750mm, 1000mm |
Material Thickness | 0.35mm to 0.80mm |
Materials | Ceramic coated galvanized steel coils |
Coil Width | Up to 1250mm |
Tile Length | 300mm to 1000mm variable programmed |
Table 3: Variable dimensions and materials for glazed steel roofing tiles mass produced on China roll forming equipment
Discuss all specification requirements with machinery manufacturers during design to deliver customized tooling.
Customization of China glazed tile roll forming machine
Capabilities meeting customer-specific aesthetic needs:
- Width changes through quick-change roller heads
- Texture variations – flat pans, shakes, Mediterranean profiles
- Interlocking leading/trailing edges for weatherlap
- Printed logos, tags or other custom markings
- Different length punching or saw cutting
- Packaging personalization options
- Shipping assistance for overseas clients
Table 4: Roll formed steel roof tile customization options offered on China production lines
Close customer collaboration during design finalization ensures manufacturability.
Suppliers and Pricing
Manufacturer | Location | Average Pricing |
---|---|---|
Fujian GSAWN | Fujian | $120,000 – $480,000 |
Botou Xianfa | Hebei | $100,000 – $350,000 |
Hebei Shengrun | Hebei | $160,000 – $600,000 |
Table 5: Sample of major Chinese glazed tile roll former exporters with cost indicators
Total cost varies based on hourly output targets, level of post-forming automation, and extent of customization impacting tooling/fabrication expenses.
Installation and Operation
Installing modern high speed lines requires planning:
- Site – Reinforced, flat concrete flooring
- Power – Voltage, loads for decoiler/hydraulics/cutoff
- Layout – Linear work flow preventing backtracking
- Controls – Color touchscreen HMIs for monitoring
- Safety – Guarding, e-stops per CE regulations
- Manuals – Thorough documentation provided
- Training – On-site guidance from technicians
Coordinate building provisions in advance for rapid commissioning. Validate all safeguards before operation.
Maintenance
Reliable functioning requires consistent maintenance:
- Schedule – Prescribed intervals for lubrication, inspection
- Lubrication – Bearings, slides, conveyors, decoiler
- Hydraulics – Pressures, cylinders, valves
- Filters – Replace oils, elements as needed
- Wiring – Check terminals, junctions
- Alignment – Confirm decoiler, guides, and straightener
- Safety – Inspect e-stops, guarding, lights
Follow maintenance manuals from machinery producers to sustain uptime.
Choosing a Glazed Tile Roll Former Manufacturer
Consider several supplier factors:
- Experience – Years serving niche glazed steel tile market
- Production Rates – Balance costs against output targets
- Customization – Openness to unique aesthetic options
- Quality Reputation – Case studies with proven installations
- Support – Installation technicians provided, manuals
- Responsiveness – Critical for overseas collaboration
- Standards – CE certificates help ensure safety compliance
Get multiple bids while scrutinizing component suppliers used. Compare proposals beyond just bottom line pricing differentials during vendor selection.
Pros and Cons
Advantages | Disadvantages |
---|---|
High productivity from 18,000-25,000 tiles per shift | Tile widths limited by coil supplier capabilities |
Interlocking ends self-align during rooftop installation | Fixed tooling suits repeating orders without variation |
Color coil substrate ensures fade-resistance | Longer lead times for unique aesthetic requests |
Compact versus tandem press lines with huge footprint savings | Special forklifts often needed for coil payloads >5000 kg |
Intelligent touchscreen controls simplify operation | Initial tooling investment required |
Table 6: Roll formed glazed tile production tradeoffs
When volume demands exist, productivity merits equipment costs and space savings over intermediate tandem line approaches.
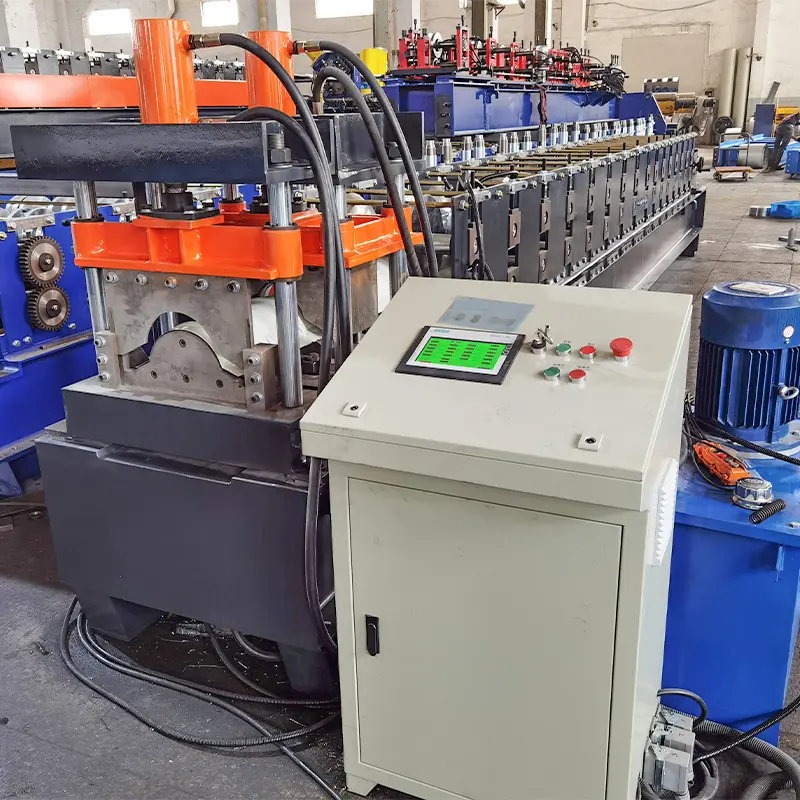
FAQs
Q: What is recommended thickness and grade for prepainted glazed tile steel coils?
A: Architectural standard 0.45mm to 0.47mm (20 ga) grade ID high-strength low-alloy S250GD + Z275 galvanized steel offers optimal dent resistance and formability. Discuss minimum mechanical properties with your coil supplier while designing tiles.
Q: What tests help qualify glazed tile coatings for long term exterior durability?
A: 5000+ hour salt spray testing per ASTMB117 ensures paint adhesion surviving sea coast humidity/salt air exposure over 30+ year life. Florida outdoor testing confirms gloss retention exceeding color Delta E of 4 even after UV degradation.
Q: Can a single machine make different tile profiles by changing roll dies?
A: Within maximum frame width limits, flexible roll formers reuse infeed tables while changing only profiling heads to transition between pan types, Mediterranean profiles and flat shingles reducing secondary tooling investment otherwise required. Product transitions average under 4 hours offline.
Q: What factors maximize glazed tile production line efficiency?
A: Utilizing dedicated forklifts for 24/7 coil loading improves uptime by ensuring fresh inventory queued close for changeovers in under 15 minutes. Streamlined warehouses keep 10+ main coils pre-slit for various width tools minimizing material shortages from delayed trucks that disrupt output momentum.
Q: How do European and Asian roll formed tile equipment for roofing differ?
A: Premier global suppliers implement mechatronic servo feed plus PLC controls enabling easier diagnosis during rapid troubleshooting by fewer maintenance staff compared to simpler electromechanical American lines requiring redundant skill sets sustaining uptime. Parameter-driven designs allow adjusting individual stations to fine-tune material tracking dynamically.