The transportation industry thrives on efficiency and durability. Trucks, the workhorses of this sector, demand components built to withstand demanding workloads. Carriage boards, also known as truck sideboards, play a crucial role in constructing sturdy truck bodies. But how are these essential panels manufactured? Enter the carriage board roll forming machine, a marvel of metalworking engineering.
This article delves deep into the world of carriage board roll forming machines, exploring their intricate workings, operational aspects, and the applications that benefit from their output. We’ll unpack the technical details in an easy-to-understand manner, using relatable examples and metaphors to bring the information to life. So, buckle up and get ready to discover the fascinating world of metal shaping!
Components of Carriage Board Roll Forming Machine
Imagine a giant metal cookie cutter, but instead of stamping out shapes, it continuously forms long sheets of metal into a desired profile. That’s the basic principle behind a carriage board roll forming machine. Here’s a breakdown of its key components:
- Decoiler: This motorized spool feeds the raw material, typically galvanized steel coils, into the machine.
- Roll Forming Stations: The heart of the machine, these stations consist of pairs of precisely machined rolls that progressively bend the sheet metal into the final carriage board profile. The number of stations varies depending on the complexity of the desired shape.
- Straightener: As the metal sheet exits the forming stations, it might develop minor bends. The straightener ensures a perfectly flat final product.
- Punching Unit (Optional): This adds cutouts or holes to the carriage board for rivets, fasteners, or other purposes.
- Shearing Unit: This cuts the formed sheet to the desired length, creating individual carriage boards.
- Run-Out Table: The finished carriage boards exit the machine onto a run-out table for stacking or further processing.
- Hydraulic Pump and Control System: This powers the machine’s various functions, ensuring smooth operation and precise control over the forming process.
Think of it this way: Each roll forming station acts like a stage in an origami folding process. With each pass through the precisely contoured rolls, the flat metal sheet transforms into a three-dimensional carriage board, ready to become a vital part of a truck body.
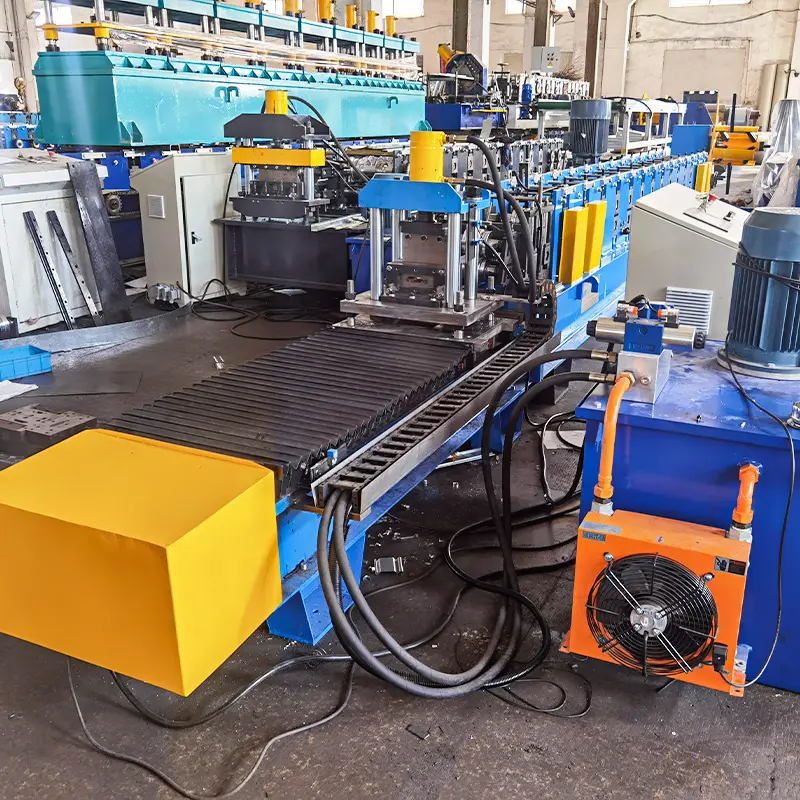
How Does a Carriage Board Roll Forming Machine Work?
The process starts with loading a coil of steel onto the decoiler. The motorized unit feeds the sheet metal into the first roll forming station. Here, the initial bending of the sheet occurs, shaping it closer to the final profile. The sheet then progresses through subsequent stations, each introducing a new bend or fold until the desired carriage board profile is achieved.
The straightener ensures a consistently flat final product. The punching unit (if present) creates any necessary holes or cutouts. Finally, the shearing unit cuts the formed sheet to the precise length of each carriage board. The finished boards travel along the run-out table for collection or further processing, such as painting or adding reinforcements.
Imagine this: The roll forming process is like meticulously guiding a metal ribbon through a series of sculpted molds. With each mold, the ribbon takes on a more defined shape, culminating in the creation of a strong and functional carriage board.
Industrial Applications of Carriage Board Roll Forming Machines
Carriage boards are the workhorses of truck body construction, providing structural support and enclosing the cargo area. Here are some key applications of carriage board roll forming machines:
- Dry Van Trailers: These enclosed trailers are the backbone of long-haul transportation, and carriage boards form their walls and roof.
- Refrigerated Trailers: The temperature-controlled environment of refrigerated trailers demands strong and durable sideboards, often made with insulated materials formed by carriage board roll forming machines.
- Dump Trucks: The ability to withstand heavy loads is crucial for dump truck bodies. Carriage boards, formed from high-strength steel, provide the necessary robustness.
- Container Bodies: Intermodal shipping containers rely on sturdy side panels, which carriage board roll forming machines can produce efficiently.
- Specialty Truck Bodies: From tankers to concrete mixers, carriage boards offer a versatile solution for diverse truck body applications.
In essence, carriage board roll forming machines are the silent heroes behind the scenes, shaping the very foundation of countless trucks that keep our economies and societies moving.
Choosing a Carriage Board Roll Forming Machine
Selecting the right carriage board roll forming machine requires careful consideration of several factors:
- Desired Carriage Board Profile: Different applications require specific profiles for optimal strength and functionality. Choose a machine that can produce the exact profile you need.
- Production Capacity: Consider the volume of carriage boards you plan to produce. Machines come in various capacities, from small-scale operations to high-production facilities.
- Material Compatibility: Ensure the machine can handle the desired material thickness and type. Common options include galvanized steel, aluminum, and even pre-painted steel coils.
- Roll Forming Speed: Throughput is crucial. Machines have varying speeds, impacting production efficiency. Analyze your needs and choose a machine that meets your desired output rate.
- Level of Automation: Consider the level of automation you require. Manual machines demand more operator involvement, while CNC-controlled models offer greater automation and precision.
- Brand Reputation and After-Sales Support: Invest in a machine from a reputable brand known for quality and reliable after-sales support. Easy access to spare parts and technical assistance is crucial for smooth operations.
Think of it like this: Choosing the right carriage board roll forming machine is akin to selecting the perfect tool for the job. Analyze your specific needs, desired output, and budget to find the machine that delivers optimal performance and value.
-
Highway Guardrail End Terminal Forming Machine
-
Highway U/C Post Roll Forming Machine
-
2 Waves Highway Guardrail Roll Forming Machine
-
3 Waves Highway Guardrail Roll Forming Machine
-
Vineyard Post Roll Forming Machine
-
Auto Size Changeable Sigma Purlin Roll Forming Machine
-
Electrical Cabinet Frame Roll Forming Machine
-
Din Rail Roll Forming Machine
-
Two waves highway guardrail machine
Cost Considerations for Carriage Board Roll Forming Machines
Carriage board roll forming machines are significant capital investments. The price varies depending on several factors:
- Machine Complexity: Machines that produce simple profiles are generally less expensive than those that create intricate shapes.
- Level of Automation: CNC-controlled machines with advanced features typically carry a higher price tag compared to manual models.
- Brand and Reputation: Established brands with a proven track record might command a premium compared to lesser-known manufacturers.
Here’s a helpful analogy: Imagine buying a car. Basic models with essential features are more affordable, while feature-rich luxury cars come at a steeper price. Similarly, carriage board roll forming machines offer a spectrum of options at varying price points.
While upfront costs are important, consider the long-term return on investment (ROI). A high-quality, efficient machine can significantly boost production output, improve product quality, and ultimately contribute to increased profitability.
Benefits of Using a Carriage Board Roll Forming Machine
There are numerous advantages to incorporating a carriage board roll forming machine into your operation:
- Increased Efficiency: Compared to traditional fabrication methods, roll forming offers a much faster and more automated way to produce carriage boards. This translates to higher production volumes and reduced labor costs.
- Consistent Quality: The precise control offered by roll forming machines ensures consistent dimensions and profiles for each carriage board, leading to a more uniform and high-quality final product.
- Reduced Material Waste: The roll forming process minimizes material waste compared to manual cutting and fabrication techniques. This translates to cost savings and environmentally friendly production.
- Versatility: Carriage board roll forming machines can be configured to produce a wide range of profiles, catering to diverse truck body applications.
- Scalability: As your business grows, you can upgrade your roll forming machine or even add additional machines to meet your increasing production demands.
In essence, carriage board roll forming machines are a game-changer for truck body manufacturers. They offer a combination of speed, precision, and versatility, enabling businesses to produce high-quality carriage boards efficiently and cost-effectively.
Maintenance Tips for Carriage Board Roll Forming Machines
Like any complex machinery, proper maintenance is essential for ensuring optimal performance and longevity of your carriage board roll forming machine. Here are some key tips:
- Regular Cleaning: Accumulated metal shavings and debris can hinder smooth operation. Regularly clean the rolls, straightener, and other machine components.
- Lubrication: Proper lubrication according to the manufacturer’s recommendations is crucial to minimize friction and wear on moving parts.
- Roll Inspection: Regularly inspect the forming rolls for any signs of wear or damage. Worn rolls can compromise the quality of the produced carriage boards.
- Preventative Maintenance: Schedule preventative maintenance checks with qualified technicians to identify and address potential issues before they escalate into major problems.
Think of it like this: Your carriage board roll forming machine is a valuable asset. By following these simple maintenance practices, you’re ensuring its smooth operation for years to come, maximizing your return on investment.
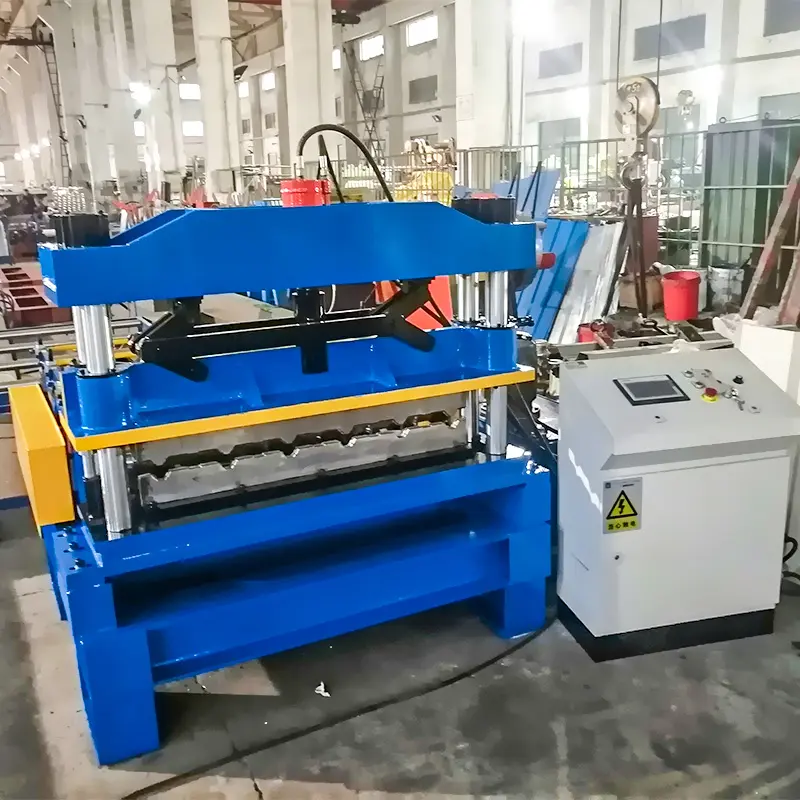
FAQ
Q: What is the typical lifespan of a carriage board roll forming machine?
A: With proper care and maintenance, a well-built carriage board roll forming machine can last for decades.
Q: Can I produce carriage boards with different thicknesses using the same machine?
A: This depends on the machine’s capabilities. Some machines can handle a range of material thicknesses, while others might be limited to a specific range.
Q: What safety precautions should I take when operating a carriage board roll forming machine?
A: Always follow the manufacturer’s safety instructions. This typically includes wearing appropriate personal protective equipment (PPE) such as gloves, safety glasses, and ear protection.
Conclusion
Carriage board roll forming machines play a vital role in the production of sturdy and reliable truck bodies. By understanding their components, operation, and benefits, you can make informed decisions about incorporating this technology into your metal fabrication processes. From increased efficiency and consistent quality to reduced waste and scalability, carriage board roll forming machines offer a compelling solution for businesses seeking to elevate their truck body production capabilities.
So, whether you’re a seasoned truck body manufacturer or just starting out, consider the potential of carriage board roll forming machines. They might just be the key to unlocking a new level of productivity and success in your operations.