c roll forming machine is a metal forming process used extensively in the automotive manufacturing industry. Roll formed parts and components are found throughout vehicles, serving both structural and aesthetic fudnctions. As automotive manufacturing has evolved and vehicle designs become more complex, roll forming has proven to be an adaptable and efficient production method able to meet the needs of the industry.
An overview of c roll forming machine and its advantages
Roll forming is a continuous bending operation in which sheet or coil metal stock is gradually formed into the desired cross-sectional profile through a series of consecutive forming stations. The forming stations consist of matching male and female roller dies that progressively shape the metal as it moves through the roll former. The resulting parts have a uniform cross-section along the length produced.
Some key advantages of roll forming include:
- High production rates – Roll forming is extremely fast, capable of producing up to 15,000 feet of finished product per hour. The continuous in-line process has a constant material feed and product flow.
- Efficiency – Material waste is minimized with roll forming. The process has material utilization rates of up to 95%. Scrap metal can be easily recycled.
- Flexibility – Roll formers can produce parts with complex profiles and shapes by changing the roller dies. Quick die changeovers allow for efficient production of small batches or prototyping.
- Strength – The incremental bending in roll forming work hardens the metal, resulting in finished parts with excellent tensile strength. The uniform profile gives optimal load-bearing capacity.
- Cost-effectiveness – Roll forming requires relatively low tooling investment costs compared to other mass production methods like stamping. It eliminates the need for large presses and dies.
These attributes make roll forming well suited for the high production volumes, diversity of components, and structural demands of automotive manufacturing.
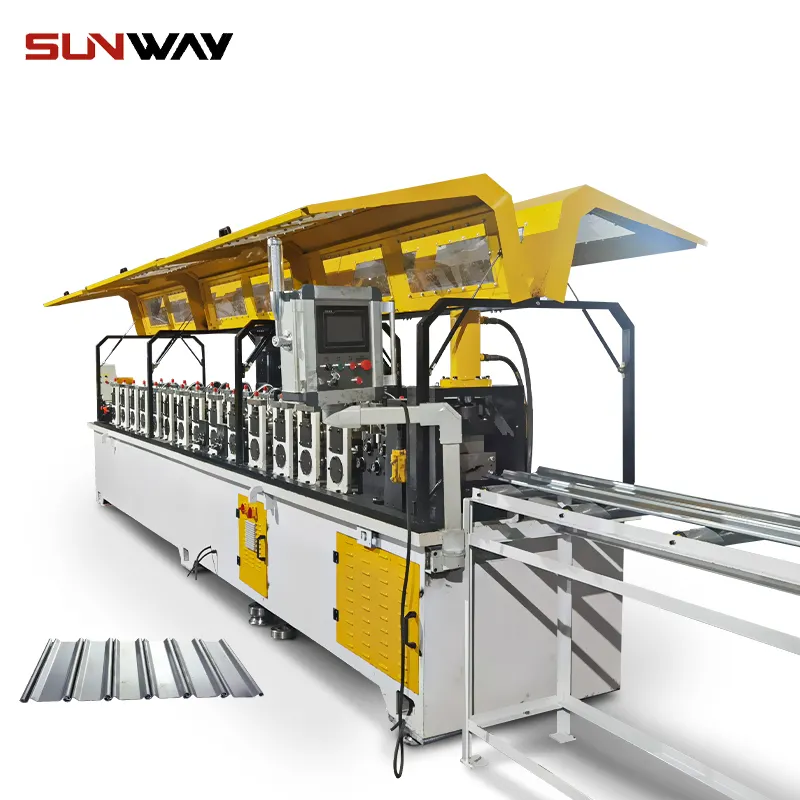
Roll formed parts used in automotive bodies
The body of a vehicle consists of hundreds of individual parts that must come together to form an integrated, lightweight, and high strength structure. Roll forming is used to produce many of the essential components that give the body its shape, safety, and durability.
Structural framework
The chassis and structural framework of a vehicle body relies on various roll formed parts. These include:
- Rocker panels – Extend along the lower edges of a vehicle between the front and rear wheels. They reinforce the floorpan and door openings.
- Pillars – Vertically oriented structures like the A, B, C, and D pillars reinforce the body and provide support between windows.
- Roof rails – Run longitudinally along the edge of the roof to give it strength and stiffen the overall body.
- Windshield and door frames – Outline and reinforce window and door openings.
- Bumpers – Absorb impact at the front and rear of the vehicle.
- Underbody components – Like subframes and cross members provide mounting points and distribute stresses.
Roll forming allows these parts to have the complex shapes and continuous sections needed for body integrity. High throughput production with roll forming keeps up with automotive manufacturing demands.
Outer body panels
Visible outer body panels that shape the exterior of a vehicle commonly emerge from the roll forming process. Examples include:
- Fenders – Surround the wheel wells to protect mechanical components from road debris.
- Hoods – Lift to access the engine bay. The large expanse of sheet metal requires rolled stiffeners for reinforcement.
- Doors – Provide entry and exit points for passengers. Inner door panels may also be roll formed.
- Trunk lids – Allow access to storage compartments. Like hoods, large surface areas require stiffening roll formed substructures.
- Roof panels – Span the top of passenger compartments to complete the exterior shell.
Roll formed outer body panels involve higher quality standards than structural components. Smooth surfaces and precisely shaped profiles are necessary for optimal fit and finish in the final assembled vehicles.
Benefits of roll forming for automotive bodies
There are a number of important benefits that make roll forming the manufacturing process of choice for producing automotive body components:
Strength and safety
The work hardening of metal during roll forming results in finished parts that meet the high strength-to-weight ratios required in vehicle bodies while reducing overall mass. This improves both robustness and fuel efficiency. Impact tests have shown the superior crashworthiness of roll formed structural parts compared to stamped or laser cut components.
Design flexibility
The ability to create complex custom cross-sections with roll forming provides automotive designers and engineers the freedom to optimize components. Parts can be tailored for function, aesthetics, and space savings.
Fast changeovers
Quick roller die changeovers allow roll forming production to rapidly adapt to new vehicle models and design changes. This speed and flexibility helps automakers shorten time-to-market for their latest products.
Material savings
Roll forming generates less scrap metal compared to stamping. Material utilization is up to 95% efficient. These material savings reduce environmental impact and manufacturing costs.
Cost-effectiveness
Relatively low equipment investment costs, minimal secondary processing requirements, and competitive long production runs make roll forming economical for automotive production volumes. The simple principles of roll forming also promote reliability and easy maintenance.
Trends and developments in automotive roll forming
Roll forming continues to evolve along with the automotive industry. Some current trends include:
Lightweighting initiatives
Efforts to reduce vehicle weight has led to wider use of advanced high-strength steels, aluminum alloys, and even composite materials in automotive roll forming. Lighter materials allow for additional mass reduction in roll formed parts.
In-die rolling and finishing
Secondary operations like edge conditioning, hole punching, and embossing are being integrated into the roll forming process through in-die rolling and finishing stations. This improves quality and reduces overall production time.
Flexible, reconfigurable roll formers
Quick-change tooling technologies facilitate fast changeovers between different roll formed parts on the same production line. This allows for economical low and high volume production.
Roll-hydroforming hybrids
Combining roll forming and hydroforming allows complex tubular sections and pre-stressed components to be created for improved structural efficiency.
Roll forming analysis software
Powerful simulation programs help automotive engineers optimize roll formed parts for functionality, manufacturability, and cost-effectiveness prior to prototyping.
As automotive manufacturing demands intensify, roll forming will continue adapting to help produce safe, durable, and affordable vehicles.
Roll formed parts used in automotive powertrains and drivetrains
In addition to vehicle bodies, many components in automotive powertrains and drivetrains emerge from the roll forming process. These include:
Engine parts
- Rocker arms – Pivoting valve actuators with complex profiles.
- Timing chains – Roller link chains for camshaft drive systems.
- Oil pans – Structural reservoirs for oil at the bottom of engine blocks.
- Engine cradles – Structural mounting components for powertrain assemblies.
Transmission and drivetrain parts
- Gear box housings – Enclose and protect transmission gears and synchronizers.
- Drive shafts – Tubular steel torque tubes connecting transmission and differential.
- Cross members – Structural transmission mounts under the floor.
- Control arms – Suspension components locating wheel hubs.
- Sway bars – Stabilizer bars to improve handling and reduce body roll.
Exhaust components
- Catalytic converter shells – Outer housings for emission control devices.
- Muffler cans – Outer shells of engine silencing chambers.
- Tail pipes – Tubular sections routing exhaust rearward.
Roll formed drivetrain parts meet the durability and quality standards for drivetrain performance. High production rates accommodate large automotive volumes.
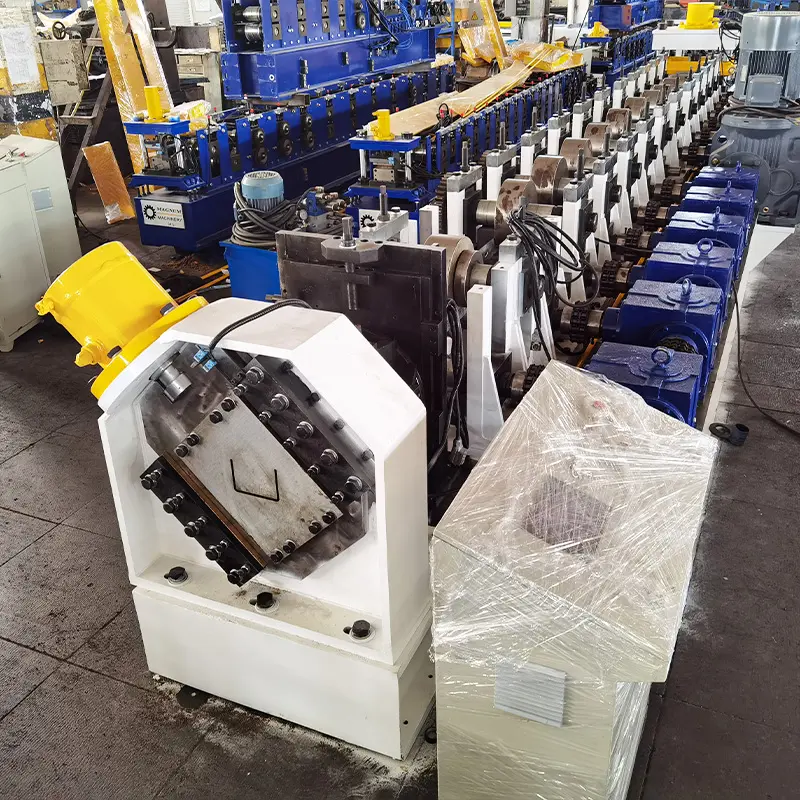
Benefits of automotive drivetrain roll forming
There are several advantages to using roll forming for powertrain and drivetrain components:
Strength and fatigue resistance
The work hardening of roll forming creates incredibly strong drivetrain parts that maintain long term durability. This prevents premature failures under demanding automotive service conditions.
Complex sections
Roll forming can create hollow, tubular, and irregular shapes needed for many drivetrain components. Sections like driveshafts are difficult to produce with other processes.
Dimensional precision
Some drivetrain components require extremely tight dimensional tolerances and locating features. Roll forming delivers this precision for proper part function.
Corrosion resistance
Sensitive drivetrain parts are often roll formed with galvanized, stainless, and aluminum materials to improve corrosion protection in harsh underbody environments.
Design flexibility
Engineers have great freedom in optimizing drivetrain component designs for weight savings, performance, and packaging constraints thanks to roll forming’s flexibility.
Fast production
High volume roll forming production keeps pace with automotive assembly line demands while keeping costs competitive with other manufacturing methods.
As performance demands intensify for modern powertrains, roll forming continues to provide an efficient production solution for improved drivetrains.
Roll formed supplementary automotive parts
In addition to major structural, exterior, and drivetrain components, roll forming produces many smaller supplementary parts throughout vehicles:
Interior parts
- Window channels – Guide and seal window glasses in door frames
- Seat frames – Structural foundations for seat cushioning and trim
- Door locks and latches – Secure closure mechanisms
- Seat tracks – Allow adjustment of seat positions
Vehicle frames and attachments
- Wheelhouse panels – Inner fender walls covering tire treads
- Hitches – Receivers for towing attachments
- Roof racks – Attachments for exterior luggage carriers
HVAC parts
- Ducts – Channels for routing conditioned air
- Outlets and vents – Aiming flows for passenger comfort
- Housings – Outer shells protecting components
Suspension and braking components
- Coil springs – Formed helical compression springs
- Brake lines – Route pressurized fluid in hydraulic systems
- Backing plates – Mounting points for brake assemblies
Miscellaneous
- Fuel tank filler necks – Fill tube openings
- Battery trays – Mounting platforms for batteries
- Wheel trim – Decorative hubcaps and rims
These supplementary items may not be as functionally critical as body structures or drivetrains, but roll formed parts throughout a vehicle contribute to overall quality, performance, and aesthetics.
The future of roll forming in automotive manufacturing
Roll forming will continue expanding its presence in automotive manufacturing. Here are some future trends and predictions:
Increasing use of aluminum
Auto makers will turn to lighter aluminum alloys for roll formed parts as fuel economy standards rise. Aluminum is also more amenable to complex roll forming geometries.
Integration of secondary operations
More finishing processes will be incorporated into roll formers for a one-step production of completed parts. This may include welding, piercing, hemming, and more.
Roll-hydroforming hybrids
Combining roll forming and hydroforming in creative ways will allow more innovative lightweight structures to be produced.
Roll forming analysis and simulation
Improved CAD and FEA software tools will help automotive engineers design optimal roll formed components digitally before production.
Nanosteel and advanced alloys
Stronger steels and alloys developed through nanotechnology may emerge in roll formed structural and safety components.
Smart roll tooling
Roll formers may incorporate sensing and automation technologies for self-adjustment during production, quality control, and maintenance.
E-mobility designs
New fully electric and autonomous vehicle designs will inspire creative applications of roll forming as the automotive landscape evolves.
Roll forming has been an integral part of automotive manufacturing for decades thanks to its versatility, efficiency, and reliability. As automotive innovations continue, roll forming machines and the skilled technicians operating them will adapt to meet the challenges ahead.
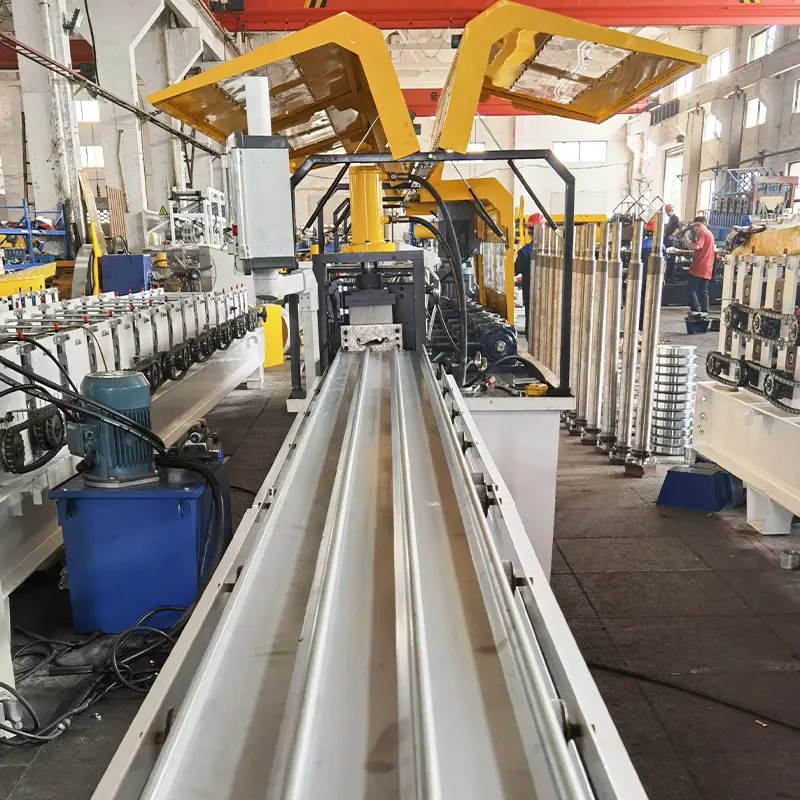
FAQ
What automotive components are commonly roll formed?
Roll forming produces structural body parts, exterior body panels, drivetrain components, and many supplementary parts found throughout vehicles. Major examples include rocker panels, roof rails, hoods, drivetrains, wheel wells, exhaust parts, and seat frames.
How does roll forming create such strong auto parts?
The incremental bending and shaping of material through a series of forming rollers induces beneficial work hardening. This cold working increases tensile strength up to 20% above that of the original sheet or coil stock.
How precise can roll forming get?
With modern CNC-controlled roll formers, dimensional precision up to ±0.5 mm on critical features like holes and slots is achievable. Sections that require tight tolerances may utilize rollers with machined grooves rather than simple round profiles.
What rapid changeover technologies are used?
Roll forming lines designed for flexible production may incorporate features like automatic die extraction, quick-connect fluid couplings, part chutes, and pre-threaded bolts to expedite roller die changeovers when switching between parts.
Can other metal forming methods integrate with roll forming?
Secondary processes like stamping, punching, cutting, and hydroforming can combine with roll forming in hybrid machines. This allows additional forming and finishing in one production line for improved efficiency.
How does roll forming analysis software work?
CAD-based programs simulate the progressive bending of a part through a virtual roll former. Engineers can digitally refine parts, create roller profiles, and evaluate production feasibility before physical prototyping.
Does roll forming require secondary machining and finishing?
Thanks to continuous support of the material throughout the process, roll formed parts require little additional machining beyond simple shearing, sawing, drilling, or trimming. The process produces finished components.
What safety tests do automotive roll formed parts undergo?
Structural body parts must undergo rigorous crash, impact, and roof strength tests. Roll bars may be analyzed through computer modeling and then physically crash tested with simulated occupants.
Can roll forming help make cars more sustainable?
Yes, roll forming’s material and energy efficiency, combined with its flexibility to use lighter metals and advanced materials, gives it great potential to support automotive sustainability initiatives.