Steel stud roll forming machines are widely used in the construction industry for manufacturing cold formed steel studs and tracks used in wall framing. The versatile roll forming process allows steel coils to be formed into a variety of profiles that serve many applications. Here are the main application fields of steel stud roll forming machines:
Wall Framing
The most common application of light-gauge steel studs and tracks is constructing interior wall framing for residential and commercial buildings. Steel stud framing is used to build non-load bearing interior walls.
The roll formed steel studs provide a strong and stable wall framing solution that is resistant to rot, mold, and termites. Steel studs are faster to install compared to wood studs. They are also consistent in size and straightness, ensuring walls are plumb and frames are square.
The roll formed steel tracks are used at the top and bottom of the wall. The studs are then inserted between the tracks and fastened using self-drilling screws. This creates a highly customizable modular system for constructing interior walls.
Compared to wood stud walls, steel stud walls provide increased structural strength and fire resistance ratings. The dimensional stability of steel minimizes the potential for warped, bowed or twisted wall framing.
Curtain Wall Framing
Curtain wall systems or curtain walls are exterior covering of a building. Steel studs and tracks are used to construct the framing or backbone of curtain walls.
The curtain wall framing provides the structural support for holding the glass, panels, louvers and other exterior wall elements. The steel profiles created by roll forming machines are either bolted, welded or screwed together to create highly customizable curtain wall frames.
Using steel studs allows large expanses of glass and openings to be spanned between floors. This increases daylighting and provides unobstructed views. Steel curtain wall framing is also non-combustible and has excellent thermal insulation properties.
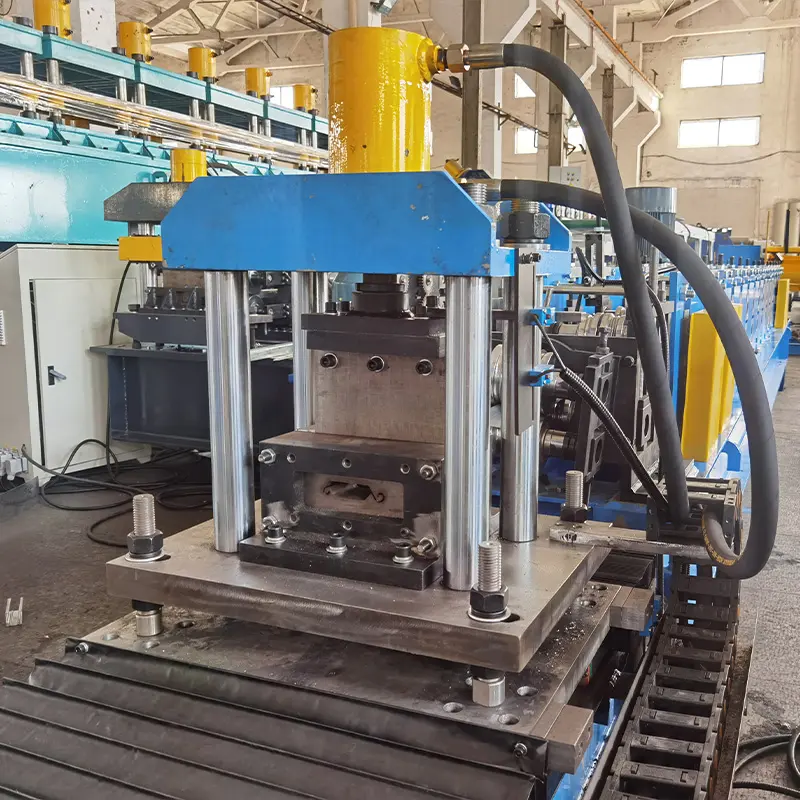
Shaft Wall Framing OF steel stud roll forming machine
Shaft walls are specialized walls built around elevator shafts, stairwells, mechanical shafts and other vertical penetrations through a building’s floors. Steel studs and tracks are commonly used to frame shaft walls.
Roll formed steel profiles provide a straight and plumb framing solution that creates a safe enclosure. Steel shaft walls have high fire resistance ratings. This prevents fire and smoke from spreading from floor to floor through the shafts. Steel shaft wall framing is also thin, maximizing rentable space in a building.
Additionally, steel studs are able to span the height between floors without intermediate support. The roll formed steel tracks securely tie the studs to the structural floor slabs. This resists lateral loads imposed on the shaft walls.
Framing Floor and Soffit Systems
Corrugated steel decking is frequently used in commercial buildings to frame floors and create soffit systems. The steel deck panels, made by roll forming machines, span between steel beams to form the base of a concrete floor slab.
The decking panels have recesses that allow concrete to interlock with the flutes. This composite action creates floors that are strong and lightweight. The steel deck also acts as formwork, eliminating the need for other temporary supports.
For soffits, the steel deck panels are installed beneath beams. They form a ceiling that conceals electrical and mechanical systems. Perforated deck panels can be used for acoustical performance. The roll formed panels are efficient to transport and install compared to precast concrete planks.
Stairs and Railings
Cold formed steel studs and tracks produced by roll forming can be used to construct framing for staircases. Studs are ideal for stringers as they can be custom bent to create slopes and landings. Steel framing for stairs is thinner and lighter compared to concrete or wood.
Steel panels are also easily roll formed into ornamental pickets and balusters for railings. This allows steel stairs and railings to be supplied as complete ready-to-install systems. The roll formed components are precision made and engineered to comply with codes. Steel resists deterioration from weather, providing long-lasting stairs and railings.
Steel Roof Trusses
Light-gauge steel studs and tracks are commonly used together with steel plates to fabricate trusses for roof framing. The roll formed steel components provide an efficient way to span long distances without interior columns.
Compared to wooden trusses, steel trusses are lighter, stronger and won’t warp, twist or bend. Steel trusses allow for longer spans, thinner roof sections and open concept spaces. The straight and true steel members also make installation easier.
Steel trusses can be designed to allow ductwork and electrical conduits to be run through the chords. This reduces the need for dropped ceilings. Steel trusses also have high fire resistance and reduce risk of fire spread.
Door and Window Frames
U-shaped steel tracks produced by roll forming machines make excellent head and sill tracks for doors and windows. The tracks provide a precise, straight foundation for anchoring frames. This allows doors and windows to operate smoothly.
Roll formed steel studs can also be used as side jambs for door and window frames. Compared to wood frames, steel provides consistent dimensions that won’t shrink or warp. Steel frames better resist weather and wear-and-tear.
Steel door and window frames also offer increased security. The strength of steel makes it hard to force open. The metal frames can be designed to accommodate electronic access control systems.
Furring Channels
Furring channels are U-shaped steel profiles used to furr out walls or ceilings. The channels create a gap for running electrical wires, insulation, or for installing additional interior finishes. Furring channels are roll formed to precise dimensions.
The channels are installed perpendicular to steel studs. This allows the spacing between studs to be adjusted to meet finish requirements. For example, furring channels allow gypsum boards to be hung with joints that do not align with the studs. This improves fire resistance ratings.
Furring channels also improve acoustical isolation when spacing walls away from exterior walls. The channels are lightweight yet strong, providing excellent support for wall and ceiling finishes.
Structural Framing
Advancements in steel grades and roll forming technology allows light-gauge steel studs to be used as structural framing. Load bearing steel stud walls can replace interior columns and beams. This allows floors and roofs to be supported by the steel stud walls.
Structural steel studs are roll formed from high strength steel and designed to withstand axial, bending, and shear stresses. They can be installed to create shear walls that resist lateral wind and seismic loads. The roll formed studs are lighter and faster to erect compared to hot-rolled steel counterparts.
Because the steel studs are pre-engineered, framing drawings are simplified. Jobsites can be kept cleaner and safer since there is less cutting and welding. Roll formed structural steel studs minimize errors and reduce construction schedule.
Automotive Applications
Roll forming machines produce lightweight, high strength steel components used in vehicle construction. Examples include bumpers, door beams, roof beams, truck frames and motorhome chassis.
The automotive steel parts are made from advanced high-strength and ultra-high-strength steel grades. Roll forming allows complex shapes to be created that optimize strength-to-weight ratios. This leads to increased fuel efficiency and lower emissions.
Roll formed automotive components also have tight tolerances that aid fit-up of body panels and crash performance. The flexibility of roll forming allows rapid prototyping and adjustments to be made in designs. Steel parts can be efficiently mass produced to meet auto manufacturing demands.
Solar Panel Frames
Steel profiles produced by roll forming are increasingly used to construct supporting frames for solar panels in large solar farms and rooftop solar PV systems. The roll formed steel rails and purlins create lightweight support structures for the solar module arrays.
Steel is an ideal material for solar panel frames given its high strength, recyclability, and corrosion resistance. Steel frames maximize land usage since they minimize footprint requirements. The thin but sturdy steel components also help resist wind and seismic forces.
Roll forming allows cost-effective mass production of solar panel frames. The continuity of the process results in minimal waste. Steel profiles can be formed to specialized shapes that aid solar panel installation and wire management.
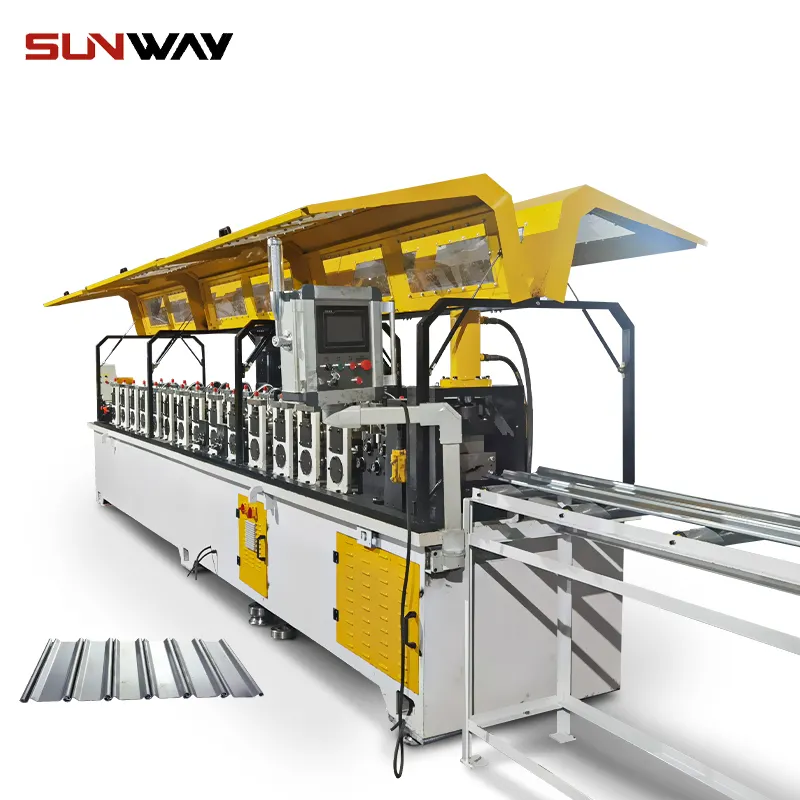
Façade and Siding Profiles
Architectural steel cladding profiles for exterior building façades and siding are commonly produced using roll forming. Roll forming allows flat steel strips to be shaped into interlocking panels with custom grooves, ribs, flutes, and reveals.
Profiles can be created to imitate traditional materials like brick, stucco, stone, or lap siding. Unique modern profiles and textures can also be formed. Roll formed steel cladding is lightweight, durable, and provides good insulation. The variety of colors and finishes available allow designers great flexibility.
Roll forming produces facade and siding panels with consistent quality and dimensions. Steel cladding installs quickly compared to other façade materials. The formed profiles are designed to shed water and resist high winds.
FAQ
Steel stud roll forming machines are an efficient method of producing wall framing studs and tracks from coiled sheet steel. Here are answers to some common questions about steel stud roll forming technology:
What are the main components of a steel stud roll forming machine?
A typical steel stud roll forming machine consists of a coil reel stand to hold the sheet steel coil, a decoiler mechanism that feeds the strip into the machine, a series of forming stations with rolls that progressively shape the steel, a cutoff device to cut the steel to length, and a discharge table to collect the finished product.
How does the roll forming process work?
Roll forming works by gradually bending flat sheet steel through a series of rolls or dies. Each set of rolls forms the steel into a specific incremental shape. As the steel passes through each successive roll station it gains more of the final profile until the desired cross-section is obtained. This cold forming process forms the steel without heat or melting.
What types of profiles can be produced on a steel stud roll forming mill?
Steel stud roll forming mills can produce a variety of profiles including C-shape studs, U-shape tracks, furring channels, straps, studkickers, joists,roof deck panels, solar panel components, and custom architectural or structural shapes. The roll sets are changeable to switch between different profiles.
What size studs and tracks can be roll formed?
The most common stud widths that can be roll formed are 3-5/8 inches and 6 inches. Thicknesses vary from 18 gauge to 33 gauge, with 20 to 25 gauge being typical. The height of C-shape studs can range from 2 to 12 inches. Common track widths range from 2 to 6 inches in thicknesses from 18 to 30 gauge. The lengths can be customized.
What types of steel can be used for roll forming studs and tracks?
Common steel grades used are ASTM A653 galvanized sheet steel and ASTM A792 galvanized steel with a G90 zinc coating. Higher grades include galvannealed A653 steel, ASTM A1039 grade 50 steel, and ASTM A653 grade 80 steel for high strength structural framing. Stainless steel can also be roll formed.
What are the advantages of using roll formed steel studs and tracks?
Benefits include consistency in dimensions and quality, high production rates, versatility of profiles produced, cost-efficiency, made from recycled materials, less jobsite waste, recyclable after use, non-combustible, insect and moisture resistant, compatible for MEP systems.
Does roll forming allow custom profiles to be produced?
Yes, with adjustable and interchangeable roll tooling, custom profiles tailored to specific applications can be designed and produced. The flexibility of roll forming allows quick implementation of custom designs.
What should I look for when choosing a steel stud roll forming machine?
Look for robust construction and stiffness of the mill frame, precision and rigidity of roll stations, type and positioning of drive units, adjustability of forming rolls, material thickness capacity, speed and cut-to-length precision. Also ensure the machine has safety protections and guards.
What safety precautions should be followed when operating a steel stud roll forming machine?
Safety precautions include:
- Proper machine guarding around pinch points
- Lockout/tagout procedures for maintenance
- Ensure emergency stops are working
- Do not exceed load/speed capacities
- Use protective eyewear and gloves
- Avoid loose clothing and jewelry
- Keep work area clean and unobstructed
How much production speed can I expect from a steel stud roll forming machine?
Production speeds vary by machine but range from about 10 to 40 feet per minute for a typical C-shape steel stud profile. Maximum speeds depend on the steel grade, thickness, and complexity of the profile. Larger roll forming mills often have speeds up to 100 ft/min.
What are the maintenance needs for steel stud roll forming machines?
Regular maintenance includes lubricating roll bearings, inspecting tooling for wear, checking oil levels in gearboxes, cleaning and removing metal shavings and dust buildup, and calibrating machines to ensure dimensional tolerances. Roll changing may be needed when switching profiles.