Sheet metal roll forming machines are pivotal in various industries, offering precision and efficiency in shaping metal sheets. Whether you’re in construction, automotive, or manufacturing, understanding the ins and outs of these machines can dramatically improve your production process. Let’s dive into everything you need to know about sheet metal roll forming machines, from their types and components to their applications and maintenance.
Overview of Sheet Metal Roll Forming Machines
Sheet metal roll forming machines are designed to bend metal sheets into desired shapes through a continuous bending process. These machines are essential in creating consistent, high-quality metal components with minimal waste. They come in various models tailored to specific tasks, each with unique features and capabilities.
Key Details:
- Function: Continuous bending of metal sheets
- Industries: Construction, automotive, manufacturing
- Benefits: High precision, efficiency, minimal waste
Roll forming machines operate by feeding a sheet of metal through a series of rollers. Each set of rollers incrementally bends the metal, achieving the desired cross-section. These machines can handle various metals, including steel, aluminum, and copper, providing versatility in production.
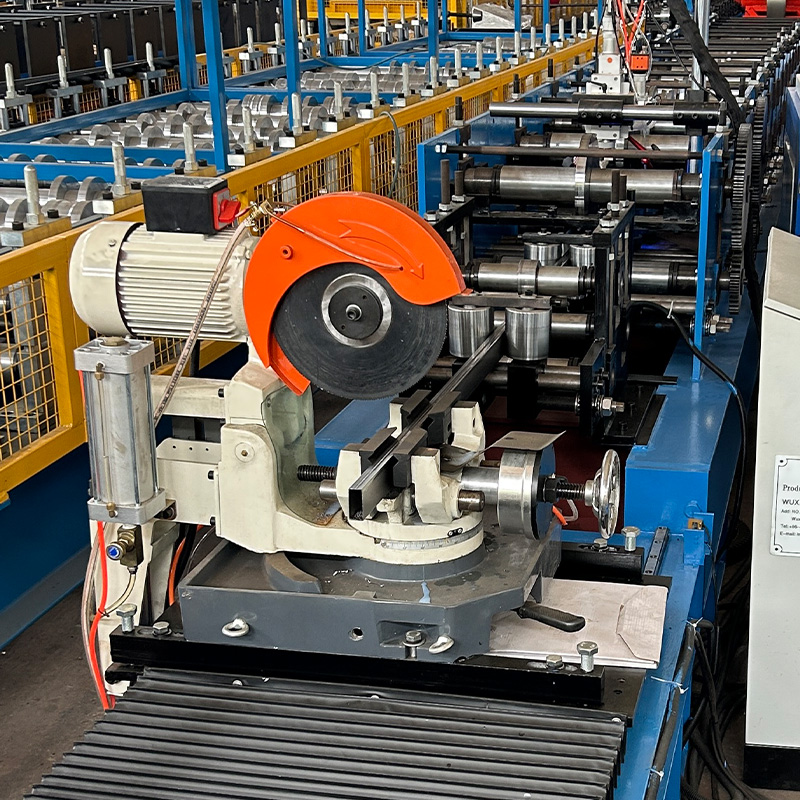
Types of Sheet Metal Roll Forming Machines
Machine Type | Description |
---|---|
Single Roll Forming Machine | Designed for simple, linear shapes. Ideal for smaller projects. |
Double Roll Forming Machine | Capable of forming two profiles simultaneously, increasing efficiency. |
Universal Roll Forming Machine | Versatile machine for a wide range of profiles and shapes. |
Compact Roll Forming Machine | Smaller footprint for limited space environments, suitable for light-duty tasks. |
Heavy-Duty Roll Forming Machine | Built for thicker metals and high-volume production. |
Multi-Profile Roll Forming Machine | Can switch between different profiles quickly, suitable for diverse production needs. |
Portable Roll Forming Machine | Mobile units for on-site projects, offering flexibility and convenience. |
High-Speed Roll Forming Machine | Optimized for rapid production with advanced automation features. |
Precision Roll Forming Machine | High accuracy for complex shapes, often used in specialized industries. |
Automated Roll Forming Machine | Fully automated with minimal human intervention, enhancing productivity and consistency. |
Working Process of Sheet Metal Roll Forming Machine
The working process of a sheet metal roll forming machine involves several stages, each contributing to the final shape of the metal sheet. Here’s a detailed look at the process:
- Feeding: The metal sheet is fed into the machine.
- Roller Stages: The sheet passes through multiple roller stages, each bending the metal slightly.
- Shaping: As the sheet progresses, it gradually takes on the desired profile.
- Cutting: Once formed, the sheet is cut to length by an integrated cutting mechanism.
- Output: The finished product is ejected from the machine, ready for use or further processing.
Key Components and Their Functions
Component | Function |
---|---|
Decoiler | Feeds the metal sheet into the machine. |
Rollers | Incrementally bend the metal to the desired shape. |
Cutting Mechanism | Cuts the formed sheet to the required length. |
Control System | Manages the operation and parameters of the machine. |
Hydraulic System | Powers the cutting and pressing functions. |
Frame | Provides structural support and stability. |
Guides and Guards | Ensure the sheet moves correctly and safely through the machine. |
-
Highway Guardrail End Terminal Forming Machine
-
Highway U/C Post Roll Forming Machine
-
2 Waves Highway Guardrail Roll Forming Machine
-
3 Waves Highway Guardrail Roll Forming Machine
-
C Section Bracing Omega Storage Rack Upright Post Roll Forming Machine
-
Steel Box Plate Making Roll Forming Machine
-
Box Beam Steel Roll Forming Machine For Shelf Column
-
Pallet Racking Step Beam P Beam Roll Forming Machine
-
Warehouse Shelf Upright Roll Forming Machine
Machine Speed and Efficiency
Machine Type | Speed (m/min) | Efficiency |
---|---|---|
High-Speed Roll Forming | Up to 60 | Excellent for large volumes |
Standard Roll Forming | 20 – 30 | Good for medium volumes |
Heavy-Duty Roll Forming | 15 – 25 | Ideal for thick materials |
Compact Roll Forming | 10 – 20 | Suitable for small batches |
Customized Mechanical Parameters
Parameter | Description |
---|---|
Material Thickness | Range of thicknesses the machine can handle. |
Profile Width | Maximum width of the profile. |
Roller Material | Type of material used for rollers, affecting durability and performance. |
Automation Level | Degree of automation, from manual to fully automated systems. |
Power Requirements | Electrical or hydraulic power specifications. |
Applications and Uses
Industry | Application |
---|---|
Construction | Roofing, siding, structural components. |
Automotive | Body panels, chassis components. |
Manufacturing | HVAC systems, machinery parts. |
Aerospace | Aircraft panels, structural supports. |
Energy | Solar panel frames, wind turbine parts. |
Agriculture | Equipment panels, structural parts. |
Installation, Operation, and Maintenance
Aspect | Details |
---|---|
Installation | Site preparation, machine setup, alignment. |
Operation | Operator training, machine settings, safety protocols. |
Maintenance | Regular inspections, roller adjustments, lubrication, part replacement. |
Suppliers and Price Range Details
Supplier | Price Range |
---|---|
ABC Machinery | $30,000 – $50,000 |
XYZ Industries | $40,000 – $70,000 |
FormTech | $35,000 – $60,000 |
MetalWorks | $45,000 – $80,000 |
Precision Rollers | $50,000 – $90,000 |
Choosing the Right Supplier
Criteria | Considerations |
---|---|
Reputation | Customer reviews, industry standing. |
Quality | Durability, performance of machines. |
Support | After-sales service, technical support. |
Customization | Ability to provide tailored solutions. |
Price | Competitive pricing, value for money. |
Pros and Cons of Sheet Metal Roll Forming Machines
Aspect | Advantages | Limitations |
---|---|---|
Precision | High accuracy in forming metal sheets. | Initial cost can be high. |
Efficiency | Fast production rates with minimal waste. | Requires skilled operators for optimal performance. |
Versatility | Can handle various metals and profiles. | Maintenance can be complex. |
Durability | Machines are robust and long-lasting. | Space requirements might be significant for larger machines. |
Automation | Reduces human error and increases productivity. | Fully automated systems can be expensive to implement. |
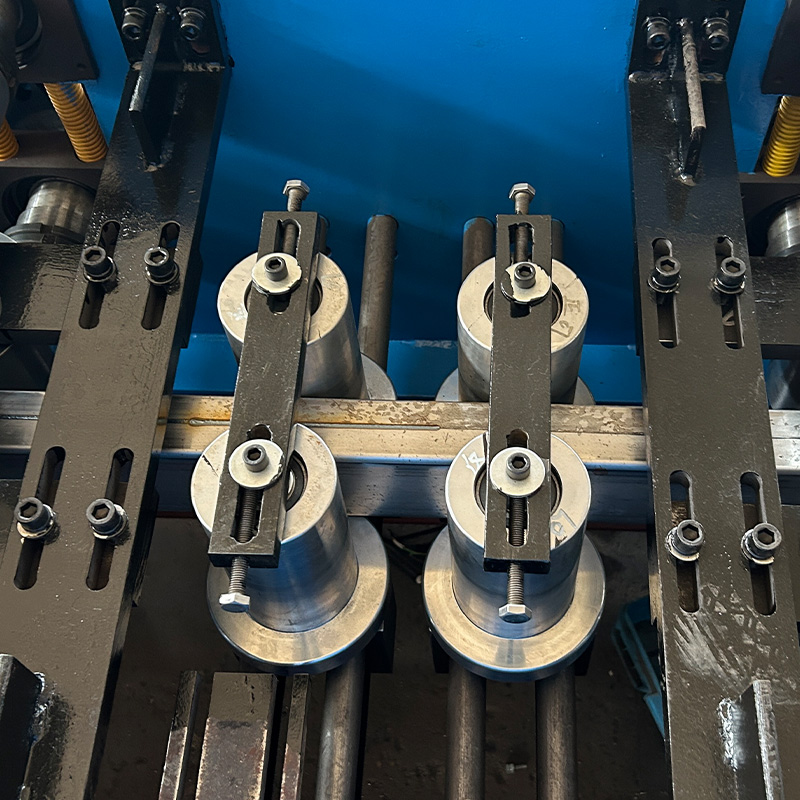
FAQ
Question | Answer |
---|---|
What metals can be processed by roll forming machines? | Common metals include steel, aluminum, copper, and more. |
How do I choose the right roll forming machine for my needs? | Consider your production volume, material type, and desired profile. |
What are the maintenance requirements for these machines? | Regular inspections, lubrication, and part replacements are necessary to ensure optimal performance. |
Can roll forming machines be customized? | Yes, many suppliers offer customization options to meet specific production needs. |
How much does a typical roll forming machine cost? | Prices range from $30,000 to $90,000 depending on the machine type and features. |
What are the benefits of automated roll forming machines? | They offer higher productivity, consistency, and reduced labor costs. |
Are portable roll forming machines effective? | Yes, they provide flexibility for on-site projects, though they may have limitations compared to stationary models. |