Imagine a bustling construction site. Cranes reach for the sky, welders spark, and workers navigate a maze of scaffolding. These temporary platforms, vital for reaching high points and creating safe workspaces, rely on a crucial component: the scaffolding plank. But where do these ubiquitous planks come from? Enter the scaffolding plank making machine, the unsung hero that churns out the foundation for safe and efficient construction.
Function of Scaffolding Plank Making Machine
At its core, a scaffolding plank making machine is a specialized metal forming machine. It takes a long sheet of steel coil and transforms it into the sturdy planks used in scaffolding structures. Here’s a breakdown of the process:
- Uncoiling: The machine unwinds the steel coil, feeding it into the production line.
- Leveling: Any unevenness in the sheet is corrected to ensure a consistent starting point.
- Servo Feeding: Precisely controlled feeding mechanisms guide the steel through the forming process.
- Punching: Holes or slots are punched into the sheet as needed for plank design and functionality.
- Roll Forming: A series of rollers progressively bend and shape the steel into the final profile of the plank. This profile creates a ribbed or corrugated surface, enhancing strength and slip resistance.
- Cutting: Once formed, the machine cuts the steel to the desired plank length. This can be programmed for various standard sizes or customized as needed.
- Stacking: The finished planks are automatically stacked or conveyed for further processing or packaging.
The entire process is automated and efficient, allowing for high-volume production of consistent, high-quality scaffolding planks.
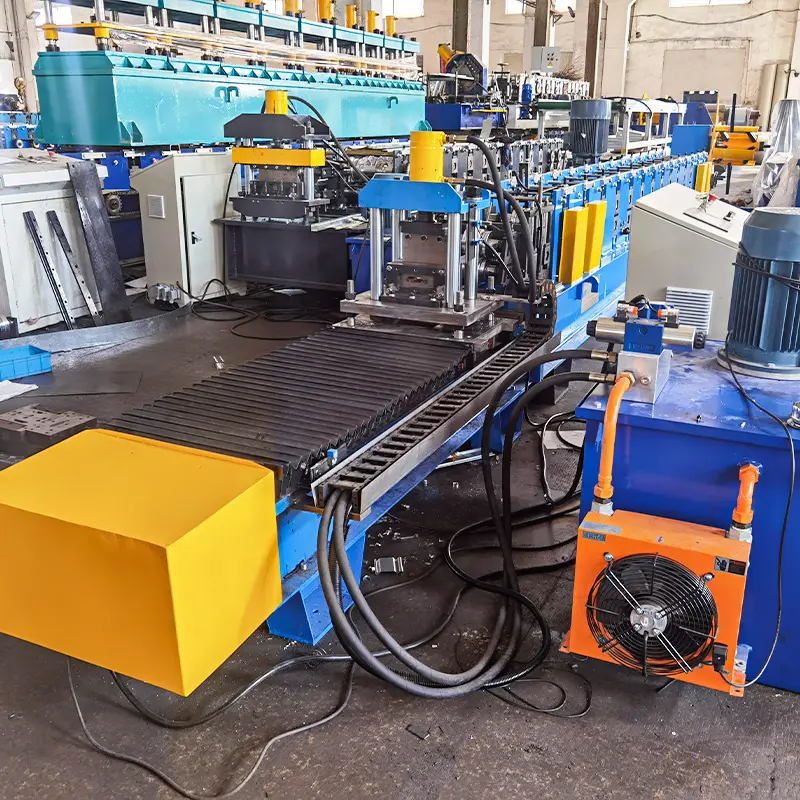
Types of Scaffolding Plank Making Machines
The world of scaffolding plank making machines isn’t a one-size-fits-all affair. Here’s a breakdown of the two main types:
- Roll Forming Machines: These are the most common type, offering versatility and efficient production. They can create a variety of plank profiles, thicknesses, and lengths by adjusting the forming rolls and cutting settings.
- Press Brake Machines: Less common but offering higher forming force, press brake machines are used for thicker planks or those with complex profiles. They utilize a series of bending tools to shape the steel sheet.
Additional Considerations:
- Automation Level: Machines range from semi-automatic, requiring operator intervention for loading and unloading, to fully automatic with minimal human interaction.
- Production Speed: Output varies depending on machine size and complexity. High-speed machines can churn out hundreds of planks per hour.
- Customization Options: Certain manufacturers offer machines that can be configured to create planks with specific features, like hooks or integrated end pieces.
Function Comparison: Roll Forming vs. Press Brake
Feature | Roll Forming Machine | Press Brake Machine |
---|---|---|
Versatility | High – wide range of profiles possible | Lower – suited for specific, complex profiles |
Production Speed | Generally faster | Slower forming cycle |
Complexity | Less complex setup and operation | More complex tooling and setup |
Cost | Generally lower | Higher due to more robust construction and tooling needs |
Material Thickness | Suitable for a wide range of thicknesses | Better suited for thicker materials |
The choice between a roll forming and press brake machine depends on your specific production needs. Roll forming machines excel in high-volume, versatile production, while press brakes offer the power to handle thicker materials or specialized designs.
Applications of Scaffolding Plank Making Machines
The primary application of scaffolding plank making machines is, of course, the production of planks for scaffolding structures. These planks provide safe and stable walking surfaces for construction workers at various heights. However, their application extends beyond construction:
- Event Staging: Scaffolding planks are commonly used as platforms for temporary stages in concerts, festivals, and other events.
- Shipbuilding and Maintenance: These planks offer sturdy walkways in shipyards and for ship maintenance.
- Industrial Access Platforms: In factories and industrial settings, scaffolding planks create temporary access platforms for maintenance and repairs.
The versatility and strength of scaffolding planks make them a valuable tool in various industries.
Advantages of Scaffolding Plank Making Machines
Investing in a scaffolding plank making machine offers several advantages:
- Increased Efficiency: Compared to manual plank fabrication, these machines significantly boost production speed and output.
- Consistent Quality: Automated production ensures consistent plank dimensions and strength, meeting safety standards.
- Reduced Labor Costs: With minimal manual intervention, these machines reduce labor requirements, impacting bottom-line costs.
- Material Savings: Automated machines minimize material waste compared to manual cutting and fabrication.
- Increased Control: Manufacturers gain greater control over plank production schedules and quality standards.
- Reduced Lead Times: In-house production allows for faster response to project demands and reduces reliance on external suppliers.
- Customization Potential: Some machines offer the ability to create planks with specific features, catering to niche market needs.
Beyond Efficiency: Safety and Sustainability
The benefits of scaffolding plank making machines extend beyond pure production efficiency. Automated production helps to:
- Enhance Safety: Consistent quality control minimizes the risk of defective planks entering the market, promoting workplace safety on construction sites.
- Promote Sustainability: By reducing material waste and optimizing steel usage, these machines contribute to a more sustainable manufacturing process.
These advantages highlight the crucial role scaffolding plank making machines play in ensuring safe and efficient construction practices while minimizing environmental impact.
-
Highway Guardrail End Terminal Forming Machine
-
Highway U/C Post Roll Forming Machine
-
2 Waves Highway Guardrail Roll Forming Machine
-
3 Waves Highway Guardrail Roll Forming Machine
-
Electrical Cabinet Frame Roll Forming Machine
-
Din Rail Roll Forming Machine
-
Two waves highway guardrail machine
-
Three waves highway guardrail machine
-
Cable Ladder Roll Forming Machine
Disadvantages of Scaffolding Plank Making Machines
While offering significant advantages, there are also some considerations when evaluating scaffolding plank making machines:
- High Initial Investment: The cost of acquiring and installing a machine can be substantial, requiring careful planning and return on investment calculations.
- Maintenance Requirements: Like any complex machinery, regular maintenance is crucial to ensure optimal performance and avoid costly downtime.
- Space Requirements: Setting up a scaffolding plank making machine requires dedicated production space to accommodate the equipment and material handling.
- Skillset for Operation: While some machines are user-friendly, operating them effectively might require training for staff on aspects like machine setup, maintenance, and quality control.
Weighing the Pros and Cons:
The decision to invest in a scaffolding plank making machine depends on your specific needs and business model. If you anticipate high-volume production and require consistent quality control, the advantages can outweigh the initial investment. However, for smaller operations or those with limited space or budget, partnering with a reliable scaffolding plank supplier might be a more suitable option.
Scaffolding Plank Making Machine Suppliers
The market offers a variety of scaffolding plank making machine suppliers, each with its strengths and areas of expertise. Here are some key factors to consider when choosing a supplier:
- Machine Reputation: Research the manufacturer’s reputation for quality, reliability, and customer service.
- Machine Capabilities: Ensure the machine meets your production needs in terms of speed, capacity, and plank profile options.
- After-Sales Support: Reliable after-sales support, including spare parts availability and technical assistance, is crucial for smooth operations.
- Price and Payment Options: Compare pricing structures and explore financing options to fit your budget.
Supplier Pricing (Indicative):
It’s important to note that pricing for scaffolding plank making machines can vary significantly depending on factors like:
- Machine size and capabilities
- Brand reputation and technology
- Level of automation
- Additional features
Here’s a table providing a general range for budgeting purposes (USD):
Machine Type | Indicative Price Range |
---|---|
Basic Roll Forming Machine | $50,000 – $100,000 |
High-Speed Roll Forming Machine | $100,000 – $200,000 |
Press Brake Machine | $150,000 – $300,000+ |
Remember, these are just starting points. Contacting potential suppliers for specific quotes is essential for accurate pricing.
By carefully evaluating your needs and researching potential suppliers, you can find the right scaffolding plank making machine to optimize your business operations and contribute to a safe and efficient construction industry.
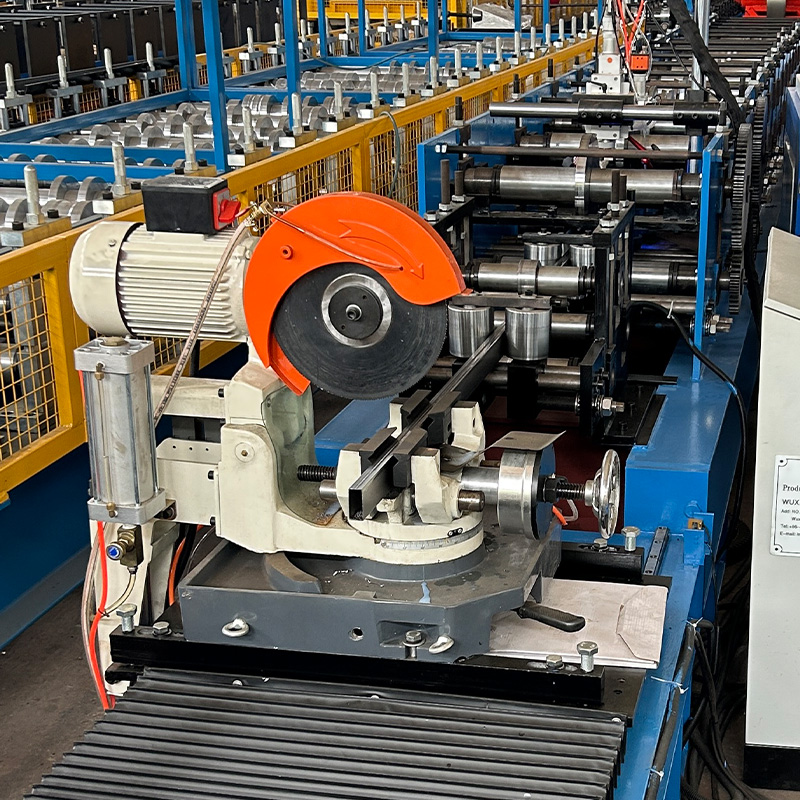
FAQ
Q: What are the typical safety features of a scaffolding plank making machine?
A: Safety features can vary depending on the machine model, but some common ones include:
- Emergency stop buttons
- Pinch point guards
- Light curtains to prevent operator access during operation
- Proper grounding to prevent electrical hazards
Q: How long do scaffolding plank making machines typically last?
A: With proper maintenance, a well-built scaffolding plank making machine can last for decades. Regular maintenance schedules and prompt replacement of worn parts are crucial for maximizing lifespan.
Q: What are some of the challenges associated with operating a scaffolding plank making machine?
A: Here are some potential challenges:
- Maintaining consistent material quality: Fluctuations in steel coil quality can impact plank consistency.
- Ensuring proper setup and calibration: Regular machine calibration is essential for maintaining accurate plank dimensions.
- Managing scrap metal: Developing a system for handling and recycling scrap metal generated during production is crucial.
Q: Are there any regulations governing scaffolding plank production?
A: Yes, scaffolding planks must comply with specific safety standards to ensure their load-bearing capacity and overall safety. These standards can vary by region, so consult with local authorities for specific requirements.