The Bemo roof panel making machine, also known as a Bemo standing seam roll forming machine, is a sophisticated piece of equipment designed for the efficient production of metal roofing panels. These panels, characterized by their interlocking seam design, are renowned for their durability, weather resistance, and sleek aesthetic. They are a popular choice for a wide range of applications, from commercial and industrial buildings to residential structures and architectural marvels.
But what exactly makes the Bemo roof panel making machine stand out? Let’s delve deeper into its intricacies, exploring its components, functionalities, and the diverse applications it empowers.
Components of Bemo Roof Panel Making Machine
The Bemo roof panel making machine is a complex system comprised of several key components working in unison to transform metal coils into precise roof panels. Here’s a breakdown of the essential elements:
- Decoiler: This apparatus efficiently unwinds the metal coil, feeding it smoothly into the forming process.
- Roll forming stations: These stations consist of a series of precisely designed rollers that progressively shape the metal sheet into the desired profile. The number and configuration of these stations determine the final panel profile.
- Cutting unit: This unit precisely shears the formed panel to the required lengths, ensuring clean and accurate cuts.
- Control system: The control system, often computer-aided, governs the entire process. It manages parameters like forming speed, cutting length, and machine operation, ensuring consistent and high-quality production.
- Stacker: The stacker automatically collects and stacks the finished panels, facilitating efficient handling and storage.
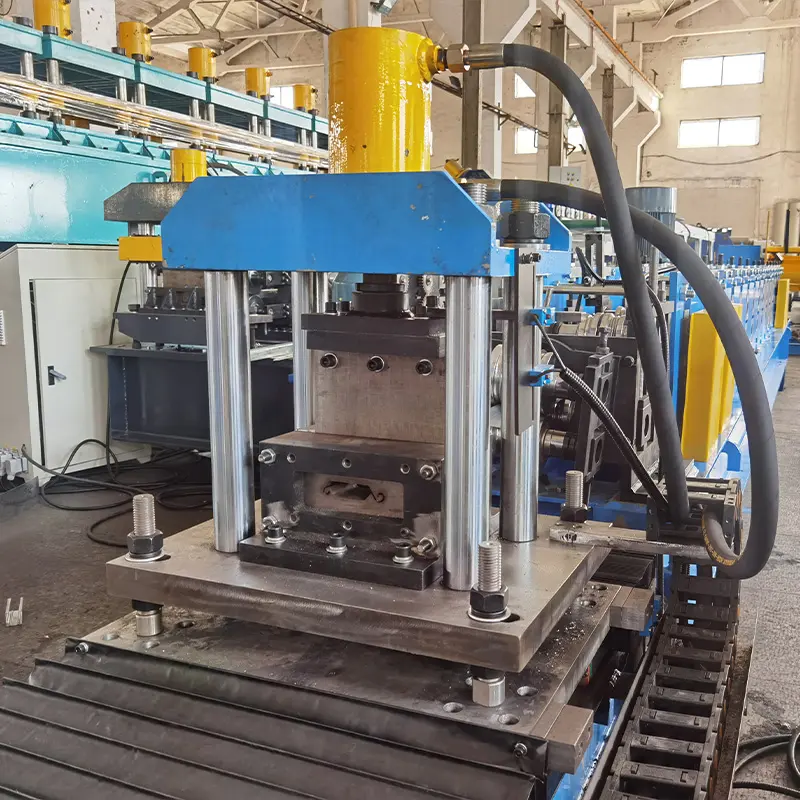
Functionality and Process of Bemo Roof Panel Making Machine
The Bemo roof panel making machine operates through a well-defined process:
- Metal coil loading: The metal coil, typically made of aluminum or steel, is loaded onto the decoiler.
- Feeding and uncoiling: The decoiler feeds the metal sheet into the initial roll forming station.
- Progressive forming: As the sheet progresses through the subsequent stations, each set of rollers meticulously shapes it into the designated profile. The intricate design of these rollers ensures precise bending and folding, creating the characteristic standing seam.
- Cutting to length: Upon reaching the designated length, the cutting unit shears the formed panel cleanly.
- Stacking: The finished panel is then conveyed to the stacker for organized collection.
The entire process is automated and efficient, allowing for high-volume production of consistent, high-quality roof panels.
Industrial Applications of Bemo Roof Panel Making Machine
The versatility of the Bemo roof panel making machine extends to a wide range of industrial applications:
- Commercial and industrial buildings: Bemo panels are a popular choice for warehouses, factories, and commercial buildings due to their durability, weather resistance, and long lifespan.
- Residential roofing: These panels offer a sleek and modern aesthetic, making them a sought-after option for contemporary residential projects.
- Agricultural buildings: Bemo panels provide excellent weather protection for barns, storage facilities, and other agricultural structures.
- Architectural projects: The aesthetic appeal and versatility of Bemo panels make them suitable for various architectural applications, from curved roofs to intricate facades.
Advantages of Bemo Roof Panel Making Machine
There are several compelling reasons why the Bemo roof panel making machine is a preferred choice for manufacturers:
- High production efficiency: The automated process enables the machine to produce large quantities of panels quickly, meeting the demands of high-volume projects.
- Consistent quality: The precise control of the forming process ensures consistent panel dimensions and profiles, leading to reliable and predictable results.
- Versatility: The machine can be configured to create a variety of panel profiles, catering to diverse architectural needs.
- Durability: Bemo panels are known for their longevity and resistance to harsh weather conditions, minimizing maintenance requirements.
- Sustainable solution: Bemo panels offer a sustainable building material, as they are often made from recycled metal and can be recycled at the end of their lifespan.
-
Highway Guardrail End Terminal Forming Machine
-
Highway U/C Post Roll Forming Machine
-
2 Waves Highway Guardrail Roll Forming Machine
-
3 Waves Highway Guardrail Roll Forming Machine
-
Electrical Cabinet Frame Roll Forming Machine
-
Din Rail Roll Forming Machine
-
Two waves highway guardrail machine
-
Three waves highway guardrail machine
-
Cable Ladder Roll Forming Machine
Considerations and Potential Limitations
While the Bemo roof panel making machine boasts numerous advantages, it’s essential to consider some potential limitations:
- Initial investment: The initial cost of acquiring the machine can be significant, which might be a deterrent for smaller businesses.
- Technical expertise: Operating the machine effectively often requires specialized training and understanding of the equipment and its functionalities.
- Customization limitations: While the machine offers some level of customization for panel profiles, extensive modifications might necessitate additional equipment or specialized expertise.
FAQs
QuestionAnswerWhat types of metals can be used with the Bemo machine?Bemo machines are typically compatible with a range of pre-coated and uncoated sheet metals, including: * Aluminum * Steel * CopperWhat are the different types of Bemo panel profiles?Bemo machines can produce a variety of standing seam profiles, each offering unique aesthetic and functional characteristics. Some common examples include: * Single lock * Double lock * Snap lockHow fast can a Bemo machine produce panels?Production speeds vary depending on the model and panel complexity, but typically range from 30 to 60 meters per minute.Does the machine automatically cut the panels to size?Some models come with integrated or automated cutting systems, while others might require manual intervention for specific lengths.What features do the control systems offer?Advanced control systems offer functionalities like: * Production monitoring * Data logging * Recipe management * These features contribute to consistent quality and efficient operation.How much space and weight do I need to consider for the machine?The size and weight of the machine vary depending on its capabilities and production capacity. It’s crucial to consult with the manufacturer to determine the specific space and foundation requirements for your chosen model.What is the typical cost of a Bemo machine?The initial cost can range from tens of thousands to hundreds of thousands of dollars, depending on the model, features, and capacity.How can I justify the initial investment?The potential benefits of a Bemo machine can outweigh the initial cost, leading to a strong return on investment (ROI) due to factors like: * Increased production efficiency * Enhanced product quality * Reduced waste * Versatility and market demandWhat factors should I consider when choosing a Bemo machine?When selecting a Bemo machine, consider: * Production needs: Volume, desired profiles, material requirements. * Budget: Initial investment and potential ROI. * Technical expertise: Availability of trained personnel. * Manufacturer reputation and support: Choose a reputable company with proven quality, reliability, and responsive customer support.Where can I find more information and assistance?Consulting with reputable Bemo machine manufacturers and distributors is recommended. They can provide in-depth insights and personalized recommendations based on your specific needs. |
---|