Galvanized standing seam roll forming machines are equipment used to produce arched or linear roofing and wall panels from metal coil stock. This comprehensive guide provides detailed information on various types, working processes, materials, design, customization, suppliers, installation, operation, maintenance and more for these versatile machines.
Overview of Galvanized Standing Seam Roll Forming Machines
Galvanized standing seam roll forming machines transform flat metal coils into panels with raised, interlocking seams for roofing and walls. Key features:
- Make galvanized, aluminum, stainless steel, titanium zinc panels
- Form linear or arched panels up to 2 inches high
- Range from portable machines to high-output industrial lines
- Automated processes: feeding, forming, slicing, stacking
- Used for commercial, industrial, agricultural buildings
- Lower cost than other panel forming methods
- Custom profiles and widths possible
The galvanizing provides corrosion resistance while the seams allow expansion/contraction and water drainage on installed panels. Continue reading for in-depth parameters, comparisons, considerations and guidance on specifying and using these machines.
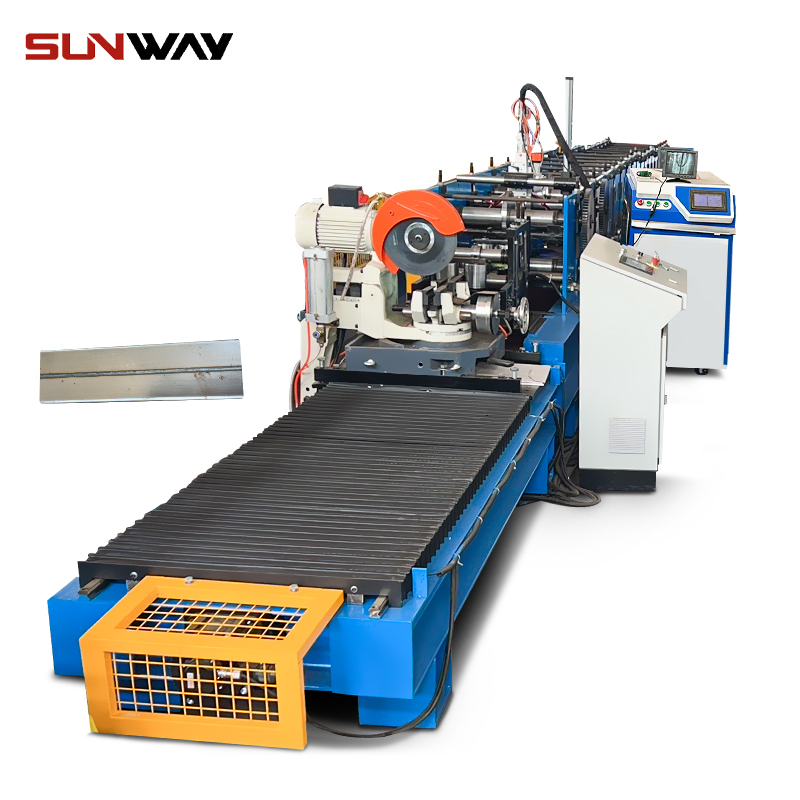
Types of Galvanized Standing Seam Roll Forming Machines
There are portable as well as stationary industrial galvanized standing seam roll forming machines available depending on production needs:
Type | Description |
---|---|
Portable | Compact, movable units with 1-3 forming heads for on-site and low volume production. Output up to 20 panels per hour. Better for infrequent small projects, custom profiles. Lower investment cost. |
Stationary Industrial | Fixed in place production lines designed for high volume continuous operation. Up to 16 automated forming heads for up to 40 panels per hour. Require permanent shop space and high initial cost. Better for regular large orders and standard profiles. |
Portable Machines: Offer flexibility in production location and ability to create custom, specialty profiles on demand. The low cost machines are moved near project sites for faster delivery. Well suited for small scale orders. Limited in speed and volume.
Industrial Lines: Engineered for 24/7 high speed mass production of panels in fixed factory settings. Computerized parametric control allows fast changeovers between standard profiles. High uptime and volumes offset initial capital expenditure over time. Ideal for large orders.
Choose type based on projected order size, customization needs, available workshop space and budget.
Working Process of Roll Forming Machines
The automated forming process generally involves:
1. Feeding: Coiled sheet metal loaded onto a de-coiler and fed into machine
2. Forming: Sheet passes through consecutive rolling stands with shaped dies
3. Slicing: Formed panels cut to specified length by built-in slicer
4. Stacking: Cut panels stacked automatically or manually
Step-by-Step Process Explained:
- Operator loads metal coil of specified thickness and width onto a powered de-coiler
- De-coiler feeds metal sheet into the leveler for initial flattening
- Sheet enters forming section with multiple rolling heads making gradual bends
- Forming heads shape sheet into desired panel profile with raised seams
- Formed panel exits and passes through a rotary scorer and slicing device
- Slicer cuts panels to pre-set length for easy handling
- Conveyors transport cut panels for automatic or manual stacking
- Stacked panels are removed by forklift and prepared for shipment
Precise feed control and adjustable forming stations allow flexibility in material gauge and panel dimensions. Next we examine material considerations and customization.
-
Highway Guardrail End Terminal Forming Machine
-
Highway U/C Post Roll Forming Machine
-
2 Waves Highway Guardrail Roll Forming Machine
-
3 Waves Highway Guardrail Roll Forming Machine
-
Electrical Cabinet Frame Roll Forming Machine
-
Din Rail Roll Forming Machine
-
Two waves highway guardrail machine
-
Three waves highway guardrail machine
-
Cable Ladder Roll Forming Machine
Material, Design and Customization
Galvanized standing seam roll forming machinery can handle:
Materials: Mild steel, stainless steel, aluminum, copper, zinc coated steel
Thickness: 18 gauge (1.2mm) to 22 gauge (0.8mm) coils
Width: 850mm standard. Custom widths possible.
Coatings: Pre-painted, galvanized, Galvalume coatings available
Profiles: Standard as well as custom arches, ribs possible
Performance: Wind uplift, water tightness, fire ratings
Standards: ASTM A653, A792, BS EN 508-1, AS 1397 etc.
The correct material must be selected based on application, lifetime needed, weather conditions and specifications. Custom profiles are possible but require additional tooling investment and process qualification.
Next we examine the standard features and available options.
Features and Accessories
Roll forming lines come with different levels of functionality, automation and options:
Standard Features
- 10-22 automated forming stations
- Programmable PLC control
- Touchscreen HMI
- Decoiler, Leveler, Forming heads
- Rotary scorer, Panel cutter
- Conveyors, Stacking tables
- Safety enclosures, Guards
Optional Accessories
- Panel hemming, seam sealing
- Printer, Embossing, punching
- Powered decoilers
- Packaging tables
- Custom tooling
- UL/CE compliance
Ensure all needed operations are included in initial machine purchase to avoid additional costs later. We next look at factors influencing overall equipment cost.
Galvanized Standing Seam Roll Forming Machine Price Range
Prices vary from $28,000 to $580,000 based on:
Factor | Impact |
---|---|
Type | Portable or Industrial |
Size | Width, Output rate |
Automation level | Manual or Automated |
Functions | Basic forming or Added operations |
Controls | Basic or Parametric PLC |
Tooling | Standard or Custom profiles |
Compliance | UL/CE or non-certified |
Freight & Support | Included or additional |
Economical Range: $28,000 to $180,000
- Portable machines
- Narrower widths
- Manual stacking
- Basic forming & control
- Standard tooling
Premium Range: $250,000 to $580,000
- Industrial lines
- Wider coils
- Automated processes
- Advanced control, options
- Customized tooling
- Certifications
Seeking quotes from 3-4 suppliers is recommended for balanced pricing. We examine supplier choices next.
Choosing Galvanized Standing Seam Roll Forming Machine Manufacturers & Suppliers
Select manufacturers with care based on:
Parameter | Importance |
---|---|
Experience | Number of years in business |
Specialization | Focus on roll forming equipment |
Capabilities | Range of machines offered |
Customization | Ability to develop new tooling |
Quality | Certifications, approvals |
Service | Installation support offered |
Pricing | Product cost, freight, warranties |
Responsiveness | Communication ease |
Recommended suppliers:
Company | Location | Contact |
---|---|---|
BT Metal Corp | California, USA | +1 209 353 3435 |
Formtek | Ontario, Canada | +1 905 564 1155 |
Sinowell | Hebei, China | +86 311 8771 6337 |
Tips when ordering:
- Share operational requirements
- Request machine drawings
- Compare multiple quotations
- Clarify delivery, warranties
With the machine selected, we now discuss installation and setup at the production site.
Installation and Setup
Installation procedure:
- Offload components safely from truck
- Assemble machine base frame
- Position and align forming heads
- Install decoiler, leveler, slicer, conveyors
- Connect wiring for controls, motors
Programming and Setup
- Input product parameters
- Jog machine for initial run
- Test sample panels
- Adjust forming pressures, feeds
- Program PLC for recipe storage
Personnel training
- Operator controls, safety
- Material loading, feeding
- Parameter adjustments
- Troubleshooting, maintenance
Proper machine calibration and test runs are vital before starting production. Smooth ongoing operation also requires following good practices.
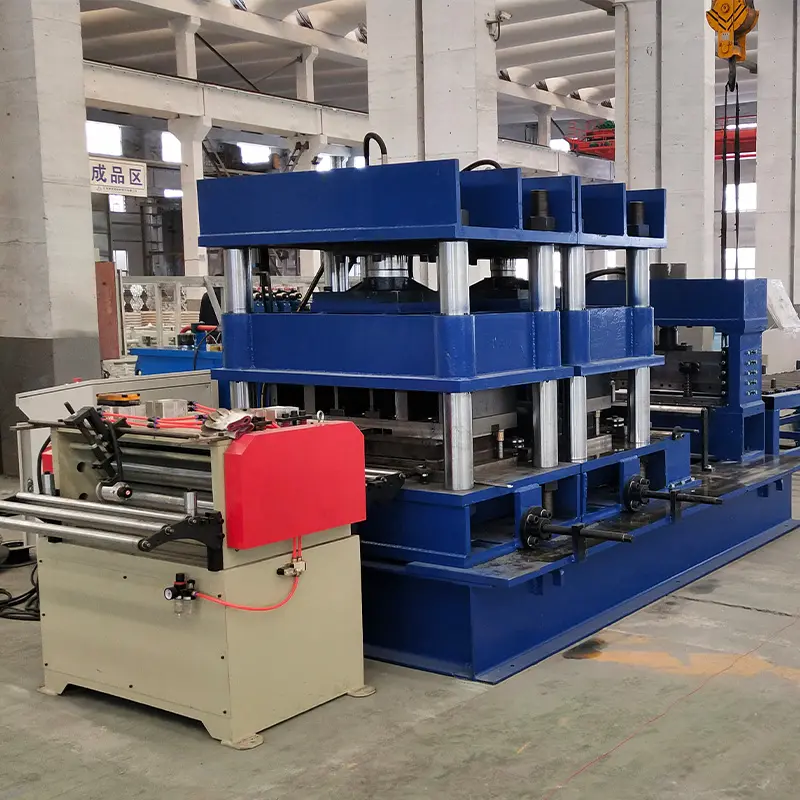
Operation and Maintenance
Operation guidelines
- Select appropriate material gauge and width
- Ensure coils are cleanly frayed and straight edge is perpendicular
- Perform regular preventive maintenance checks
- Monitor machine operation and stop for faults
- Clean forming stations; lubricate moving parts
- Manage scrap material discharge
Maintenance activities
- Inspect electrical, mechanical, hydraulic systems
- Check chain and gear wear
- Test emergency stop circuits
- Backup control parameters
- Replace worn forming rollers
- Touch up paint chips to prevent corrosion
The next section answers common questions on these versatile machines.
FAQ
Q: What safety measures are required?
A: Enclosures around moving parts, E-stops, light curtains, control reliability per ISO 13849 are typical.
Q: What accuracy is possible in panel dimensions?
A: Length +/- 2mm, Width +/- 1mm is achievable based on machine capabilities.
Q: How often do the forming rollers need replacement?
A: On average after 300,000 linear feet of material formed. Depends on material hardness.
Q: What is the influence of temperature and humidity?
A: Controlling environment is recommended for material stability and grease life.
Q: How much skilled labor is needed to operate the equipment?
A: After initial training, semi-skilled operators can run the automated processes.
Q: What production rates can be expected?
A: 15-40 finished panels per hour based on width, automation and order complexity.
Please reach out with any other questions!