Roll forming is a continuous bending operation in which sheet or strip metal is progressively formed into a desired cross-sectional profile through a series of contoured rolling stands. Barrel type roll forming machines are a specialized type of roll former used to produce metal barrels, drums, pails, and other round metal containers.
Barrel Type Roll Former Equipment Guide
Equipment Type | Description |
---|---|
Barrel roll former | Primary forming machine to shape metal coil into round profile |
Decoiler | Feeds metal coil strip into roll former |
Guide boxes | Aligns strip through forming stands |
Forming stands | Series of stands with contoured rolls to bend metal |
Welder | Joins formed profiles into cylinders |
Cutoff device | Cuts cylinders to required lengths |
Beader | Rolls edges for seaming and closure |
Working Process of Barrel Roll Forming
The barrel making process starts by loading a coil of thin gauge metal strip into a powered decoiler which feeds the strip through a series of guide boxes into the forming stands. The stands each make a slight increment of the bend using a series of top and bottom contoured rolls. As the strip passes through each stand, it takes on more of the round profile.
After all stands complete the forming operation, the rolled profile proceeds to a welder which joins the two ends together to create a cylinder. An cutoff device then cuts the cylinder to the required length for the barrels. Finally, a beader unit rolls the edges of the open ends to prepare it for seaming or closure. The finished barrels are then inspected, packed and shipped to customers.
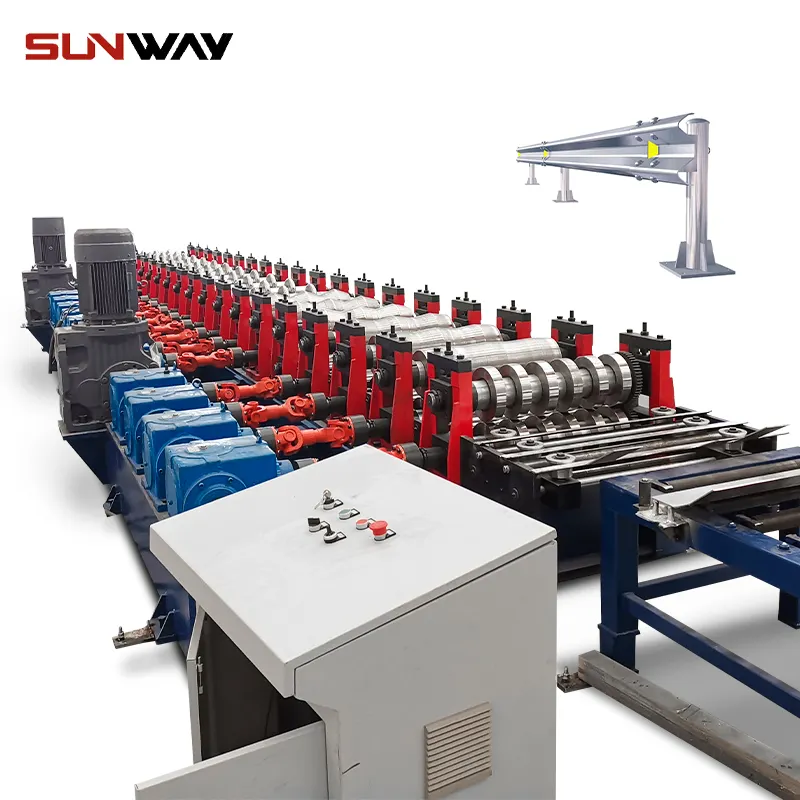
Material Feeding in Barrel Roll Formers
Method | Description |
---|---|
Decoiler | Powered unwinding unit holding metal coil |
Straightener | Roller type straightening device |
Feed table | Roller table for guiding strip |
- Decoilers hold the coil of metal to be formed and feed it into the roll former
- Streamlining units like roller straighteners align the strip
- Feed tables with rollers guide the strip in a straight line path through the forming sections
Profile Forming in Barrel Machines
Method | Description |
---|---|
Forming stands | Contoured top and bottom rolls |
Roll design | Profile matches part shape |
Roll materials | Various steel alloys |
Adjustment | Manual or automatic |
- Forming in done in a series of stands with contoured rolls
- Rolls are machined to the match the profile being formed
- Rolls made from wear-resistant steels for long life
- Roll adjustment can be manual or automatic on some models
Common Design in Barrel Roll Formers
Design | Description |
---|---|
Round | For circular drums and pails |
Oval | For oval containers |
Conical | For tapered shapes |
Custom | Unique profiles |
- Most common design is round barrels
- Oval, conical and custom profiles also produced
- Custom profiles requires specialty tooling
-
Rolling Shutter Slat Roll Forming Machine
-
Highway Guardrail End Terminal Forming Machine
-
Highway U/C Post Roll Forming Machine
-
2 Waves Highway Guardrail Roll Forming Machine
-
3 Waves Highway Guardrail Roll Forming Machine
-
Electrical Cabinet Frame Roll Forming Machine
-
Din Rail Roll Forming Machine
-
Two waves highway guardrail machine
-
Three waves highway guardrail machine
Length Cutoff Device in Barrel Lines
Method | Description |
---|---|
Flying cutoff | Rotating saw blade |
Stop gauge | Sets cut length |
Conveyor | Moves cut blanks |
- Cutoff is done using a rotating circular saw blade
- Cut length is set by adjustable mechanical stop
- Conveyor transfers cut cylinders for next operation
Edge Preparation and Seaming
Method | Description |
---|---|
Beader | Rolls edges |
Seamer | Joins rolled edges |
- Beader unit rolls edges for seaming
- Seamer clamps and crimps edges together
- Lock or snap seam created
Customization in Barrel Roll Formers
Option | Description |
---|---|
Custom profiles | Unique shapes |
Size change | Diameter and length |
Quick change | Modular tooling |
Automation | Robots and handling |
- Custom and non-standard profiles supported
- Flexible design allows size changes
- Quick-change forming assemblies for fast changeover
- Automated material handling possible
Suppliers of Barrel Type Roll Forming Machines
Manufacturer | Location | Price Range |
---|---|---|
Anhui Jingming | China | $10k – $50k |
Botou Xianfa | China | $16k – $80k |
Dimeco | USA | $30k – $120k |
Gasparini | Italy | $70k – $300k |
Metform | Turkey | $25k – $100k |
- Wide range of standard and custom barrel roll formers
- Prices vary by speed, width and automation features
- Chinese models are more cost competitive
- European and American machines offer heavier duty construction
Installation and Operation
Activity | Description |
---|---|
Site preparation | Foundations, power, compressed air |
Positioning | Work flow, safety, maintenance access |
Commissioning | Assembly checks, dry runs, tooling setup |
Operator training | Safety, startup, control functions |
Production | Monitor strip feed, consistency checks |
- Installation requires adequate foundations and utilities
- Equipment positioned properly in work cell
- Commissioning verifies assemblies and test runs
- Operators trained on all functions and safety
- Ongoing production monitoring required
Maintenance of Barrel Roll Forming Machines
Method | Description | Frequency |
---|---|---|
Cleaning | Remove dirt, grease, metal chips | Daily |
Lubrication | Oil or grease on bearings and gears | Weekly |
Adjustment | Align forming rolls | Monthly |
Inspection | Check roll wear, loose parts | Quarterly |
Overhaul | Major repairs, component replacement | Annually |
- Regular cleaning to prevent buildup
- Lubrication reduces wear on moving parts
- Periodic adjustment keeps rolls in alignment
- Inspect wear items and catch loose components
- Major overhauls extend equipment lifetime
Choosing a Barrel Roll Former Supplier
Factor | Description |
---|---|
Price | Upfront cost and total operating cost |
Delivery | Lead time for new equipment |
Experience | Track record and years in business |
Customization | Flexibility for unique requirements |
Support | Installation help and after sales service |
Parts | Inventory of spare parts |
Certification | Meets quality management standards |
- Price should consider lifetime operating costs
- Delivery lead times can vary greatly
- Choose supplier with extensive barrel industry experience
- Custom options may require more expensive models
- Local agents can assist with support needs
- Availability of parts impacts uptime
- Certified suppliers indicate better quality management
Pros and Cons of Barrel Type Roll Formers
Advantages
- Efficient continuous production in long lengths
- Consistent quality with roller leveling and guides
- Capable of high production rates in automated lines
- Low tooling cost compared to press brakes or stamping
- Flexible in handling multiple widths and diameters
- Safer operation compared to fabrication methods
- Simple design requires less maintenance than other processes
- Small footprint relative to production capacity
Limitations
- Limited to profiles producible from bendable strip
- Not as strong as seamless spun barrels in same gauge material
- More costly than manual sheet metal barrel fabrication
- Size range constrained by forming stand dimensions
- Larger units require greater floor space
- Fine gauge and high tensile materials require specialized machines
Applications of Barrel Type Roll Formers
Barrel roll formers produce round cylindrical and conical shaped containers for a wide variety of industries including:
- Food and beverage drums and pails
- Paint and coating cans
- Lubricant and oil cans
- Chemical transport drums
- Pharmaceutical containers
- Cosmetic packaging
- Promotional barrels and buckets
Common materials used are low carbon steel, stainless steel, and aluminum. Gauges range from thin sheets around 0.5 mm to thick plates of 2 mm.
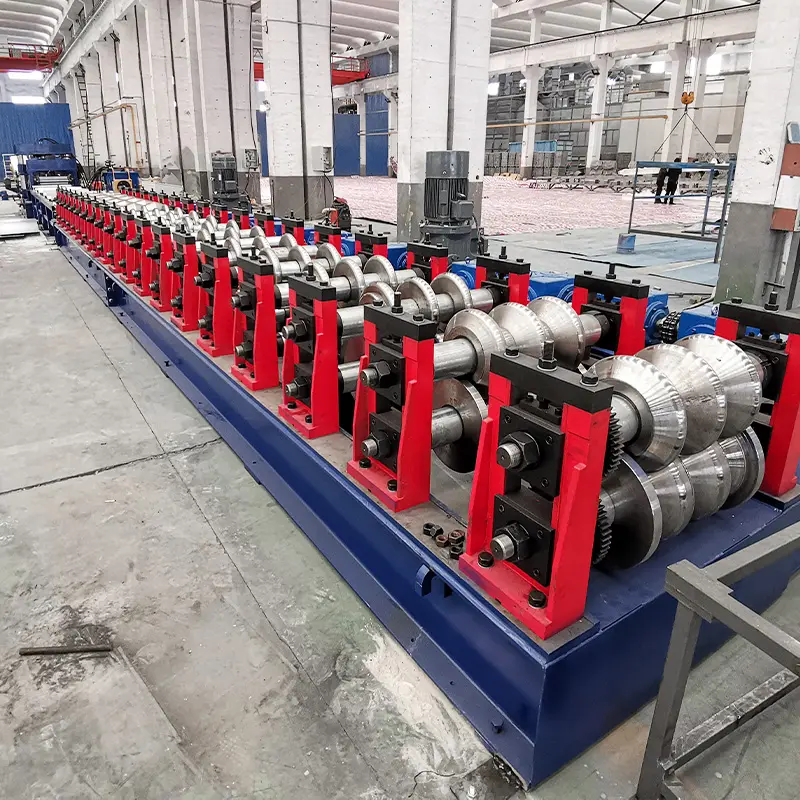
FAQ
What are the key functions in a barrel roll forming line?
The key functions are coil feeding, pre-forming straightening, profile forming through stands, welding into cylinders, cutting to length, beading edges, and automated transfer between stations.
What diameter barrels can be formed on these machines?
Standard max diameter is around 700 mm depending on the roll former width. Larger diameters up to 1500 mm are possible on custom machines.
What metals can be formed into barrels?
Most common materials are low carbon steel, stainless steel, and aluminum alloys. Other formable alloys like brass and copper are also possible.
What thicknesses and widths of metal can be formed?
Thickness from 0.5 mm to 2 mm can be typically formed. Narrower strips down to 100 mm and wider coils over 1250 mm can be run depending on machine capacity.
What are typical production rates for barrel machines?
Production rates vary widely based on part size and automation level, but around 10-20 barrels per minute is typical for average models. Some high speed automated lines produce over 50 per minute.
What processes are required after roll forming the barrels?
After roll forming the cylinders, further processes like trimming, beading, printing, cleaning, testing and packing are required before shipping the final product.
How long do barrel roll formers last before needing replacement?
With proper operation and maintenance, the lifespan often exceeds 20 years. Major mechanical components can be rebuilt or replaced to extend the working life further.
What safety measures are important for these machines?
Strict lockout procedures, emergency stops, light curtains, and guarding around rotating parts and pinch points are crucial. Mandatory safety training and PPE for operators is also vital.
How much do replacement roll former rolls cost?
Roll costs vary depending on size, materials and any special coatings or finishing. Typical range is $500 – $1500 per set, but complex custom profiles can be over $5000.