metal stud roll forming machine for sale is an efficient process to mass produce light gauge steel wall framework and structures for the construction industry. This article provides a comprehensive guide on procuring various types of metal stud roll forming equipment available for sale from international suppliers and manufacturers.
Metal Stud Roll Forming Machine Models
There are several equipment configuration types used for roll forming metal studs and tracks suitable for framing walls and light structures:
Machine Type | Description |
---|---|
Coil Lines | Feed raw coil stock into process |
Roll Forming Lines | Form stud profiles from coils |
Punching Lines | Punch web holes for services |
Cutting Lines | Cut to length and stack |
Specialty Lines | Add crimping, embossing etc. |
Framing Lines | Make full wall frame sections |
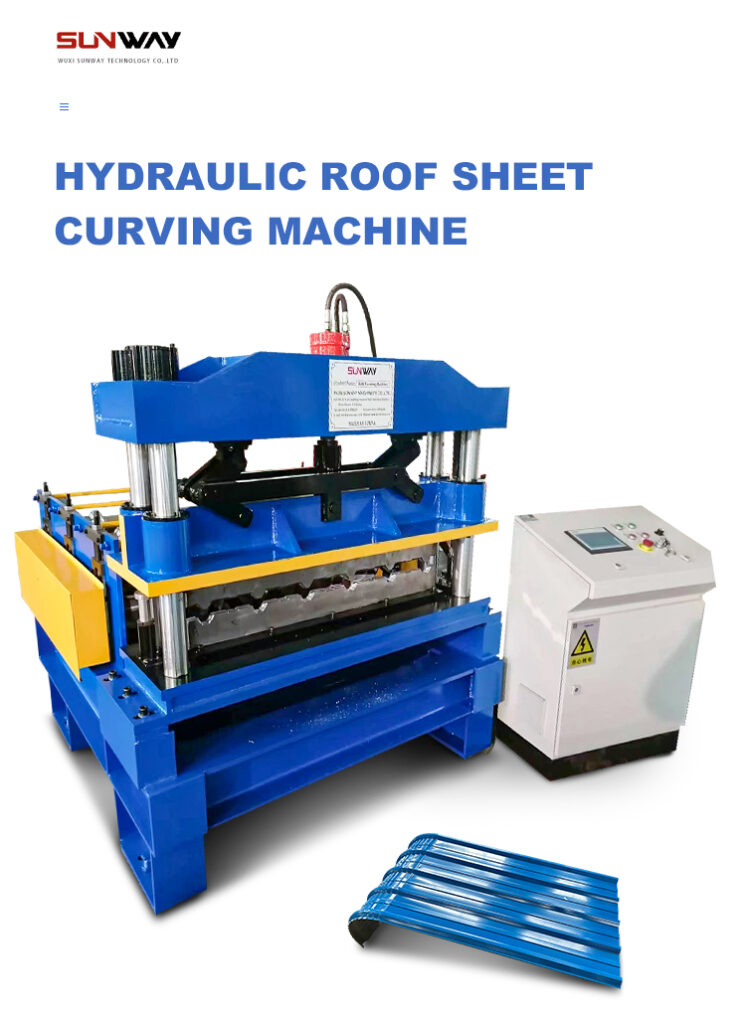
Working Process of a Metal Stud Roll Forming Machine
The industrial process involves decoiling steel strips, feeding into consecutive roll forming stands to shape into C or U channels, punching service holes in the profile web, cutting into lengths, specialized enhancements and finally stacking the finished studs.
The forming process is completely automated using servo electric drives and PLC controllers for very high production volumes meeting international building standards. Quick die change designs allow fast profile changes.
Material Feeding
Coils of cold rolled galvanized steel strips of widths ~100 mm to 300 mm are loaded onto powered de-coilers and fed into the roll tooling stations through straightening units.
Profile Forming
Progressive sets of rolling dies bend the steel sheet into stud profiles with web and flange elements of specified dimensions. Various stud depths can be formed on the same line by changing the roll sets.
Hole Punching
Rotary web hole punching units make holes in the stud webs spaced as per standards for carrying building services like electrical conduits, plumbing pipes etc.
Slicing
High speed circular rotary shears precisely cut the formed profiles into lengths from 300mm to 6000mm as required for walls of different heights.
Custom Enhancements
Additional enhancements like crimping ends, adding specialized slots and other features can also be integrated by incorporating extra working heads.
Stacked Output
Formed studs are automatically stacked and banded on platforms ready for transport to job sites for quick framing.
Major Manufacturers and Suppliers of Metal Stud Roll Machines
There are many international premium metal stud roll former equipment manufacturers and suppliers to choose from:
Brand | Location | Sample Models |
---|---|---|
Elitech | China | SS1904 Automatic Metal Stud & Track Roll Former |
Gasparini | Italy | GASPEG modular framing lines |
Metform | Turkey | IOS Series Roll Forming Machines |
Boxer | UK | Boxer UltraFlex modular Roll Former |
Metecno | Belgium | Steel Framing Roll Forming Lines |
Output speeds range from 8 to 15 meters per minute with capacities between 35,000 to 65,000 square meters per day for machines having 5-7 roll forming stations.
Price Range of Metal Stud Roll Forming Equipment
The average pricing scale from international manufacturers for automatic multi-profile metal stud rolling mills are:
Output Capacity | Price Range |
---|---|
10,000 m2 per day | $50,000 to $120,000 |
30,000 m2 per day | $120,000 to $300,000 |
50,000 m2+ per day | $300,000+ |
Domestic manufacturers in China supply basic lines from $30,000 onwards. Buying quality second hand lines helps lower investment costs.
Installation of Metal Stud Roll Machines
- On-site assembly is done by manufacturer technicians.
- Hydraulic power packs, motors, controls need to be properly installed.
- Commissioning runs are performed to validate profiles meet standards.
- Operators are trained on machine usage, control software and safety aspects.
-
Standing Seam Roof Panel Curving Machine
-
Barrel Corrugated Roll Forming Machine
-
Stand Seaming Roof Panel Roll Forming Machine
-
Downspout Pipe Roll Forming Machine
-
Gutter Roll Forming Machine
-
Trapezoidal Panel Roll Forming Machine
-
Ridge Cap Roll Forming Machine
-
Double Layer Panel Roll Forming Machine
-
Roof Tile Panel Roll Forming Machine
Operation and Control Features
- Touchscreen HMIs allow fast recipe setup for different metal stud specifications.
- Automatic belt feeds, servo electric drives provide unmatched forming precision.
- Advanced IoT data analytics optimize overall equipment efficiency (OEE).
- Predictive maintenance avoids downtime.
Maintenance Aspects
- Scheduled cleaning, lubrication and inspections maximize production uptime.
- Prompt replacement of wear items like bearings, punches etc. reduces scrappage.
- Keeping adequate spare parts inventory on-site ensures minimum downtimes.
- Hardware upgrade contracts facilitate technology refresh every 2-3 years.
How to Select a Metal Stud Roll Forming Machine Brand
When procuring metal framing roll formers, buyers must evaluate overall supplier competency to get peak performing equipment matched to their production volumes and quality benchmarks.
Parameter | Description |
---|---|
Order History | Number of similar lines installed globally. |
Location and Logistics | Machines reaching your nearest dry port quickly. |
Production Scale | Peak output speed and capacity ratings. |
Profile Range | Catalogue coverage of global framing standards. |
Customization Skills | Holistic in-house engineering for specialized designs |
Cost Effectiveness | Optimized pricing relative to features offered. |
Warranties | Coverage terms for hardware, electronics, hydraulics etc. |
Technical Support | Responsiveness for troubleshooting, spares supply, upgrades. |
Buyers must get systematic technical demos, evaluate factory testing protocols and discuss future-proofing possibilities to maximize long term equipment value.
Pros and Cons of Automated Metal Stud Roll Lines
Advantages
- 90% faster profile forming vs. semi-automatic machines
- High precision and consistency in stud dimensions
- Quick motorized die changeovers
- Advanced diagnostics and preventive maintenance
- Safer operation with full safety guarding
- Better overall equipment efficiency
Limitations
- Much higher initial capital investment
- Complex troubleshooting of PLC controls
- Dependent on incoming coil quality
- Proprietary electronic spare parts
- Skilled technicians required for maintenance
- Regular fine tuning required
For most mass production buyers, the exponential productivity and quality benefits outweigh automation complexity factors of metal stud roll forming lines.
Application Areas for Metal Stud Roll Machines
The roll formed light gauge steel studs, tracks, trusses produced find widespread usage in:
Modular Housing: Prefabricated homes, apartments, villas, hostels, labor camps made quickly.
Commercial Spaces: Offices, shops, malls, hospitals, schools employ rapid drywall construction.
Infrastructure: Metro stations, warehouses, factories, plant buildings needing large open spaces.
Temporary Structures: Disaster relief shelters, exhibition canopies, outdoor event pandals.
Agricultural: Crop storage sheds, poultry cage batteries, greenhouse frameworks.
Automated metal stud rolling lines help scale prefab construction projects using light steel frameworks hundreds of times faster.
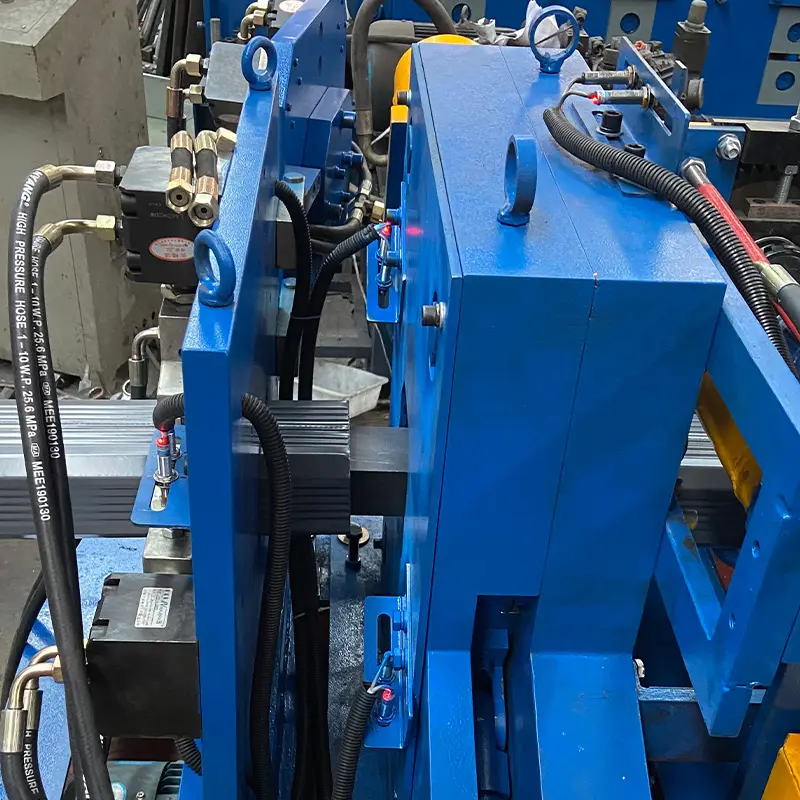
FAQs
Q: What testing certifications are provided with metal stud roll forming equipment?
A: Reputed manufacturers get international CE, UL etc. certifications and provide extensive factory acceptance testing for:
- Stud profile dimensional accuracy
- Hole punching alignment
- Cutting length precision
- Speed/feedforce optimization
- PLC-HMI functionality and safety
This ensures clients get independently verified equipment quality exceeding global benchmarks.
Q: Does the machine factory offer design engineering services for custom profiles?
A: Yes, full profile design engineering services provided:
- Consultation for optimal cross-section design
- Custom roll tool modeling
- Structural analysis with FEA
- Prototype sample production
- Virtual fitting modeling and clearances check
- Tolerancing for ease of site assembly
Q: What level of after-sales technical support is provided?
A: Manufacturers have global technical partnerships with extensive support infrastructure including:
- Video call troubleshooting assistance
- Maintaining inventory of electronics spares
- Hardware/software upgrade packages
- Annual maintenance contracts
- Machine refurbishing services
- Operator technical helplines
This ensures any issues are promptly resolved for maximum production uptime.
Q: What Factors Affect Metal Stud Quality and Consistency?
Critical parameters impacting product consistency:
- Incoming coil thickness variations
- Roll tool concentricity and surface finish
- Profile station alignment precision
- perforation die condition
- shear blade sharpness
- control of line speed variations
Statistical data analytics combined with machine learning algorithms optimize the forming parameters in real-time. This facilitates top-notch quality standards.
Conclusion
Acquiring high speed automated roll forming equipment from internationally reputed metal stud machine manufacturers allows prefab builders to gain exponential productivity improvements and faster construction project turnarounds to maximize profits. Partnering with competent suppliers over the long run ensures access to the latest technological upgrades while getting full technical support. Investing in modern equipment future-proofs the mass production infrastructure for sustainable growth.