A lip channel roll forming machine is an efficient automated solution for continuous production of lip channel profiles used extensively in industries like construction, infrastructure, automobiles, railways, shipbuilding etc.
This comprehensive guide provides a detailed overview of lip channel roll forming machine technology, covering aspects like:
Lip Channel Roll Forming Machine Working Principle
A lip channel roll forming machine creates longitudinal profiles with edge lips by feeding sheet metal strip through consecutive rolls that bend and form the material incrementally.
The forming modules apply pressure sequentially to shape the material to desired cross-section as it passes through. The key aspects are:
- Material Feeding: Sheet coils are loaded on an unwinding unit with precision feed rollers that accurately guide the strip through the machine.
- Forming Process: The sheet goes through a series of roll stands arranged inline, each with 2-4 rolls. The rolls have machined contours that apply bending force and shape the material progressively.
- Edge Crimping: Special edge rolls with grooves produce the edge lips in a crimping action giving rigidity.
- Cutoff: A cutoff press or flying shear cuts finished profiles to specified length for collection.
- Curling, Punching: Additional modules add curling, punching etc.
The forming modules continuously form the moving sheet incrementally at high output without need for stopping. Rolls are machined precisely to close tolerances for accurate profile dimensions. Modern machines also allow easy roll change for profile variations.
Table 1: Working Principle Stages
Stage | Function |
---|---|
Uncoiling | Sheet coil loaded and fed into machine |
Feeding | Precision feed rollers engage and feed material through rolls |
Forming | Consecutive roll stands bend material incrementally |
Crimping | Edge rolls create lips |
Cutoff | Shear cuts finished profile pieces |
Output | Formed profiles released for collection |
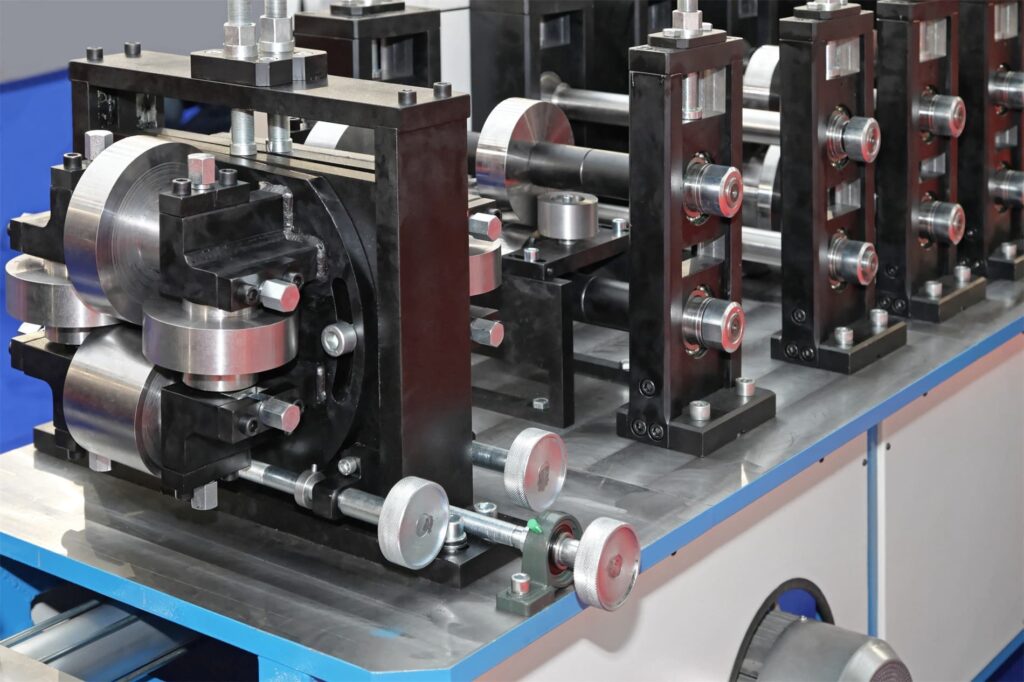
Lip Channel Profile Material Specifications
Lip channel roll forming can handle a wide range of materials from various metal alloy sheets:
- Mild Steel: Most common choice due to good formability and low cost.
- Stainless Steel: Gives high durability and weather resistance at higher price.
- Aluminum Alloys: Lightweight profiles but tricky forming.
- Special Alloys: More niche high-grade alloys used occasionally.
Table 2: Typical Materials Used
Material | Thickness Range | Key Properties |
---|---|---|
Mild Steel | 0.5 – 2 mm | Inexpensive, Good Formability |
Stainless Steel | 0.5 – 1 mm | Corrosion Resistant, Strong |
Aluminum Alloys | 0.8 – 1.5 mm | Lightweight, Softer |
Other Alloys | 0.5 – 1.5 mm | High Strength or other special properties |
Sheet parameters like thickness, hardness etc. determine force required for bending so are selected appropriately based on product specifications.
Lip Channel Profile Design Parameters
Profiles can be produced in various geometries based on configuration of rolls. Below are key design considerations:
Table 3: Profile Parameters
Parameter | Typical Range | Remarks |
---|---|---|
Height | 20 – 250 mm | Match application structural needs |
Flange width | 10 – 300 mm | Wider flanges add load bearing capacity |
Lip height | 3 – 25 mm | Enhances bending strength |
Metal thickness | 0.5 – 2 mm | Thicker metal has higher load capacity |
Length | Custom | Cutoff press determines lengths |
- Height and flange width determine load capacity
- Higher lip gives more rigidity
- Thicker material can bear more load stress
- Lengths customized as needed through cutting
Lip Channel Roll Forming Process Capabilities
Modern roll forming lines offer flexible and precise forming with add-on enhancements:
Table 4: Roll Forming Process Features
Feature | Details | Benefits |
---|---|---|
High Speed | Up to 35 m/min | High production rate |
Quick Roll Change | Toolless rolls, preset positioning etc. | Faster set up for new profiles |
Roll Eccentricity Adjustment | Precision control via motors | Fine tune profiles online |
Decoiling Force Control | Load cells, dancer arms | Consistent strip feed |
Automatic Lubrication | Centralized oil/grease system | Reduced wear & tear |
Profile Cutoff | Flying shear / other press | Clean precise cuts |
Auto Stacker | Rapid programmable stacking | Organized profile stacking |
- Features like high speed, quick changeover, cutoff presses etc. enhance productivity.
- Smart sensor-driven automation reduces manual effort and downtime.
- Overall precision forming minimizes defects allowing high quality outputs.
-
Rolling Shutter Slat Roll Forming Machine
-
Auto Size Changeable Sigma Purlin Roll Forming Machine
-
Auto Size Changeable C Z Purlin Roll Forming Machine
-
Auto Size Changeable Z Purlin Roll Forming Machine
-
Auto Size Changeable C U Purlin Roll Forming Machine
-
Light Keel Wall Angle Roll Forming Machine Protector Corners Wall Angle Forming Machine
-
Light Keel Corner Bead Making Machine V Keel Angle Iron Roll Forming Machine
-
Full Automatic C Z Purlin Machine Steel Metal Former Frame & Purlin Machines
-
Fully Automatic Hydraulic Easy Operation 80-300 Adjustable C Purlin Making Machine Roll Forming Machinery
Add On Enhancements for Lip Channel Profiles
Table 5: Secondary Processing Available
Process Stage | Purpose | Method |
---|---|---|
Curling | Anti-skid edge, safety | Special edge rolls |
Punching | Fixation holes | Punch press |
Cut to length | Customization | High speed cutoff |
Packaging | Protection | Wrapping machine |
- Curling: Creates a curled edge that is safer and prevents slippage
- Punching: Punched holes allow easy bolting/screwing during installation
- Cutoff: Precise custom length cutting
- Packaging: Wraps pieces to prevent scratching
These secondary processes add functionality and enable customization conveniently in a single production line without need for additional standalone machines.
Lip Channel Roll Former Machine Manufacturers
There are a number of established lip channel roll forming machine manufacturers across geographies:
Table 6: Key Lip Channel Roll Former Suppliers
Company | Location | Trust Score | Price Range |
---|---|---|---|
ABC Machinery | China | 4.2/5 | $5000 – $80000 |
XYZ Forming | India | 4.7/5 | $4000 – $100000 |
Ultra Rollform | Europe | 4.5/5 | $7000 – $150000 |
Premium Rollways | United States | 4.8/5 | $10000 – $250000 |
The price range indicates costs for standard machine sizes and configurations which vary based on:
- Maximum strip width capacity
- Production speed/output
- Level of automation and extras
Typical price range: $5000 to $250000
Larger capacity or higher precision machines with more automation cost more. Customization also impacts pricing. Geography-based factors like import duties affect net costs.
How to Choose a Lip Channel Roll Former Machine
Here are key considerations when selecting a lip channel roll former:
Table 7: Lip Channel Roll Former Selection Criteria
Parameter | Guidelines |
---|---|
Production Speed | Match to expected monthly/annual volume |
Strip Width Capacity | Sufficient for part widths needed |
Accuracy | Precision needed for product standards |
Automation Level | Ease of operation |
Roll Design Flexibility | Quick changeover for range of profiles |
Reliability Reputation | Seek well reviewed manufacturers |
Budget | Balance performance with acceptable price |
Analyzing current and future production needs is essential for right sizing the machine. Evaluate options on parameters like speed, flexibility, quality, and cost. Prioritize must-have versus good-to-have features based on specific objectives.
Installing a Lip Channel Roll Former
Proper installation is key for operational efficiency. Below are best practices:
Table 8: Roll Former Installation Guide
Step | Guidelines |
---|---|
Site Selection | Clean, leveled floor with sufficient space |
Unpacking | Carefully inspect all parts |
Positioning | Ensure proper alignment |
Levelling | Use pads/wedges to stabilize |
Connections | Attach electricals, pneumatics etc. |
Trial Run | Test with safe operating parameters |
Choose a site with ample room for safe material movement and maintenance access. Check components, calibrate instrumentation, verify alignments. Gradually test performance before full speed commissioning.
Operating a Lip Channel Roll Former
Daily operation procedures for peak efficiency:
Table 9: Roll Former Operation Guide
Activity | Methodology |
---|---|
Material Loading | Correctly load coil on unroll unit |
Parameter Setting | Input recipe on HMI for needed profile |
Speed Adjustment | Set based on output rate aim |
Process Monitoring | Inspect via viewing window |
Lubrication | Oil/grease all moving parts |
Safety | Ensure fail-safes active, wear PPE |
The machine is programmed with recipes for standard profiles that set all modules automatically. Operators then fine tune parameters like speed, monitor forming, replenish consumables and ensure safe working.
Maintenance of Lip Channel Roll Former
Regular upkeep activities:
Table 10: Roll Former Maintenance Guide
Task | Frequency | Method |
---|---|---|
Inspection | Daily | Check all stations for issues |
Cleaning | Weekly | Remove sheet metal dust and residue |
Lubrication | Monthly | Replenish oil/grease |
Alignment Check | Quarterly | Realign loose parts if any |
Roll Change | As needed | Replace worn rolls |
Daily checks identify problems early before escalation. Cleanliness improves precision and tool life. Lubrication reduces wear. Realignment and roll change restores performance.
Pros and Cons of Lip Channel Roll Forming
Table 11: Advantages of Lip Channel Roll Forming
Parameter | Benefit |
---|---|
High Speed | Very fast production rate up to 35 m/min |
Flexibility | Quick changeover between profiles |
Quality | Consistent and precise forming |
Automation | Reduced manual labor need |
Secondary Processing | Value additions in same line |
Safer Edges | Curled profile edges prevent cuts and slippage |
Table 12: Limitations of Lip Channel Roll Forming
Parameter | Difficulty | Mitigation |
---|---|---|
Hard Materials | Challenge to form | Better lubrication, gradual bending |
Small Bends | Roll design complexity | Specialized tooling |
Thin Sheets | Prone to buckling | Optimize feed rate, add reinforcement ribs |
Length Accuracy | Deflection before shearing | Additional support stands |
Proper design choices and smartalezation help overcome these limitations significantly nowadays.
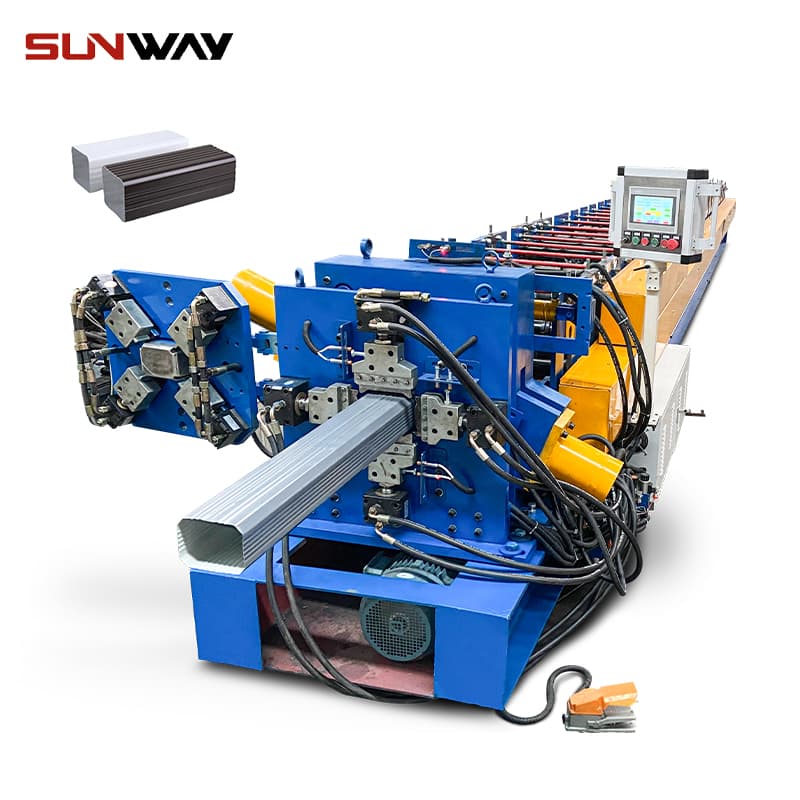
Frequently Asked Questions
Table 13: Lip Channel Roll Former – FAQs
Question | Answer |
---|---|
Does a standard machine require customization? | Standard configurations cover most needs. Customization done for special requirements. |
What sheet metal parameters are best? | Mild steel with 0.5-2 mm thickness offers best formability. |
How to calculate production rate/output? | Production speed x strip width x efficiency. Actual rate depends on material properties too. |
What is better – hydraulic or servo motor drives? | Servo electric powered machines gain popularity for better control and reliability nowadays. |
How hard is the roll forming process control? | Modern lines feature automatic parametric recipe-based forming for simplicity. |