C purlins are widely used for roofing and wall framing in industrial and commercial buildings. This article provides a comprehensive guide on c purlin roll forming machine prices from different manufacturers.
Overview of c purlin roll forming machine price
C purlin roll forming machines are used to form continuous C-shaped purlin sections from metal coil. The purlins serve as secondary roof and wall supports.
Key features:
- High production speeds up to 40m/min
- Capable of forming thick-gauge sheets
- Flexible roll tooling for size changes
- Robust steel frame construction
- Advanced safety protections
- Easy operation and maintenance
Main Components
The major components include:
Components | Description |
---|---|
Uncoiler | Holds the sheet coil for de-coiling |
Feeder | Feeds metal sheet into forming stations |
Forming stands | Progressively form C-shape with rollers |
Hydraulic system | Provides power to work stations |
Control system | Automates and monitors the machine |
Cutoff shear | Cuts purlins to length |
Working Principle
The working principle involves:
- Sheet coil loaded and fed into the feeder
- Forming rollers progressively bend the sheet
- Hydraulic rams provide force to stations
- Formed C-purlin cut to length by shear
- Produced purlins stacked automatically
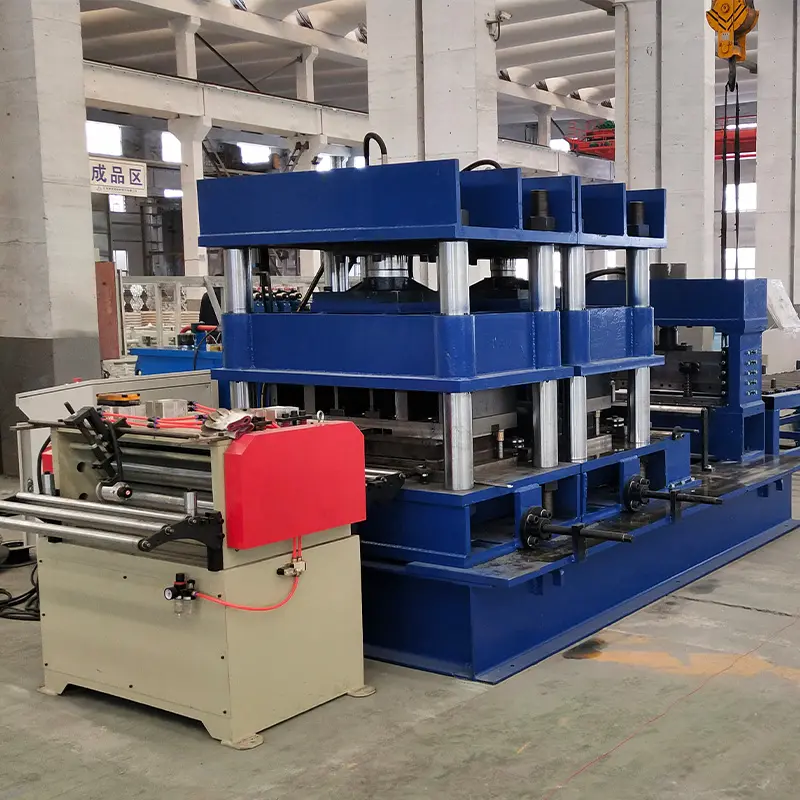
Types of C Purlin Roll Formers
C purlin roll forming machines are available in different types:
Number of Roller Stands
- 10 stands for light sections
- 16 stands for regular sections
- 21 stands for heavy sections
Automation Level
- Manual material handling
- Automatic stacking units
- Fully automated with conveyors
Production Speed
- Regular speed up to 25 m/min
- High speed up to 40 m/min
Sheet Width
- Narrow up to 600mm
- Medium up to 800mm
- Wide up to 1000mm
Applications of C Purlin Machines
The C purlins produced find uses in:
- Roof purlins in industrial buildings
- Wall girts in pre-engineered structures
- Cladding supports in factories
- Rail and solar panel supports
- Mezzanine and storage platforms
- Agricultural and warehouse sheds
- Commercial and aviation hangars
C purlins provide an efficient and strong building framework for roofs and walls.
Technical Specifications
The key technical specifications include:
Parameters | Typical Values |
---|---|
Forming Speed | 18 – 40 m/min |
Sheet Thickness | 1.2 – 3 mm |
Sheet Coil Width | 600 – 1000 mm |
Purlin Height | 100 – 300 mm |
Purlin Length | 2500 – 12000 mm |
Roller Stands | 10 – 21 stands |
Main Drive Motor | 7.5kW to 22kW |
Power Supply | 380V, 50Hz, 3 Phase |
Machine Weight | 8000 – 15000 kg |
Advanced machines can form up to 8mm thick sheets and produce very long span purlins.
Design and Construction
The C purlin roll former has a sturdy fabricated steel structure:
- Frame – Made from welded steel I-beams for rigidity
- Housing – Fabricated from thick steel plates
- Rolls – Hardened alloy steel with machined grooves
- Bearings – Heavy-duty housed units to take radial loads
- Drives – Ground gearbox with sprocket-chain drive
- Controls – PLC + HMI touchscreen controls
- Safety – Full safeguarding as per CE norms
Precision machined components and sturdy construction provide reliability and durability to the machine.
Roll Tooling Design Standards
The roll dies follow international standards:
- C purlin dimensions as per AISI, AS/NZS
- Rolls made from DIN EN10263 grade steel
- Optimal hardness between 50-60 HRC
- Surface finish of Ra 0.4μm to 0.8μm
- Roll concentricity within 0.01mm
- ISO tolerances for profile dimensions
- RoHS compliance for eco-friendliness
The tooling quality ensures high output standards.
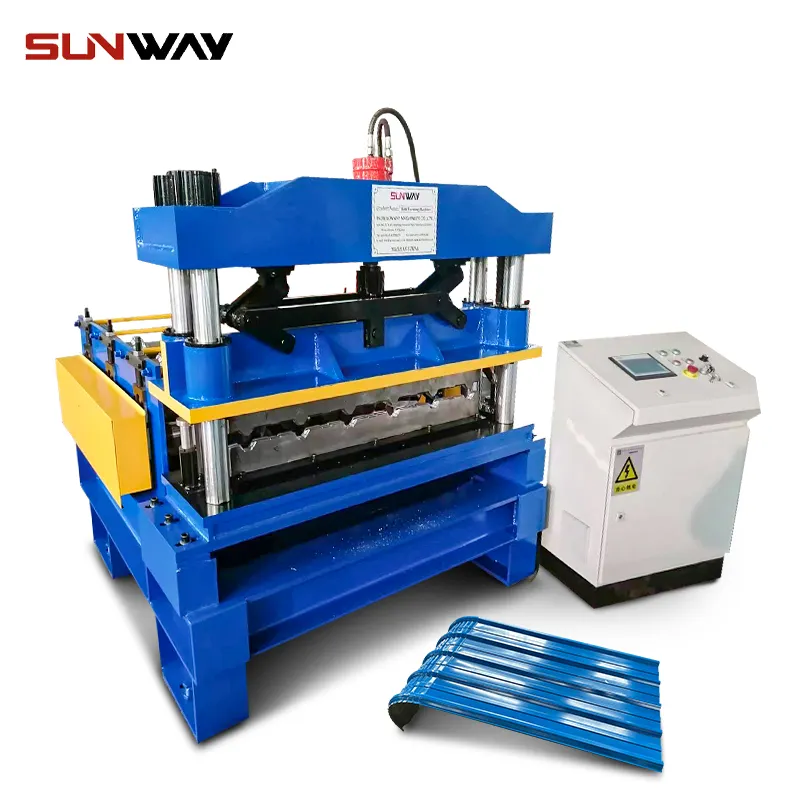
Manufacturing Capabilities
The C purlin roll former can handle:
Sheet Thickness
- Light gauge sheets of 1.2 to 2.0mm
- Heavy gauge sheets of 2.5 to 8.0mm
Sheet Width
- 600mm for small sections
- 800mm for standard sections
- 1000mm for wide flange sections
Section Heights
- 100mm to 300mm in different sizes
Section Length
- Up to 12m long purlins in NC cutoff machines
Holes and Slots
- Hole punching up to Ø20mm
- Slot punching for easy installation
Optional Accessories
- Decoilers for sheet handling
- Automatic stackers
- Online cutting and hole punching
- Packaging strappers
Suppliers and Pricing
Some major C purlin roll former manufacturers and price range:
Manufacturer | Location | Price Range |
---|---|---|
Roswu Tech | China | $35,000 – $55,000 |
Anhui Cechen | China | $45,000 – $88,000 |
Kingsland Engineering | UK | $55,000 – $120,000 |
Metform | Turkey | $48,000 – $100,000 |
Shaanxi Best | China | $28,000 – $65,000 |
Cost Factors:
- Speed and output requirements
- Level of automation
- Optional accessories
- Production volume discounts
Entry-level – $35,000 to $55,000
Advanced – $85,000 to $150,000
Higher speed and automated machines cost more but deliver faster payback from high productivity.
Installation and Commissioning
Installing a C purlin roll former involves:
- Positioning the machine on leveled ground
- Securing the machine properly to the floor
- Removing securing bolts and foam supports
- Checking and tightening all fasteners
- Leveling the machine with precision
- Connecting electric power supply
- Checking direction of motor rotation
- Installing hydraulic oil and lubricants
- Jogging the machine for initial checks
- Setting machine parameters and limits
- Testing safety functions
- Running in Produktion mode and optimizing
The machine vendor provides complete installation guidelines in the product documentation. Certified technicians also support the commissioning process. Proper installation ensures smooth startup and working of the purlin forming line.
Operation and Working
Operating a C purlin roll former requires:
Pre-operation checks:
- Machine safety guards in place
- Electrical and hydraulic systems ready
- Roll gap spacing and alignment
- Feeder ready with sheet coil
- Conveyors and exit table clear
Starting procedure:
- Switch ON main electrical supply
- Start hydraulics station and set pressure
- Jog inching to check forming stations
- Set process parameters on control panel
- Thread sheet through forming rollers
- Start automatic operation cycle
Running mode:
- Monitor current consumption by motors
- Check formed purlin quality continuously
- Watch for any abnormal noise or vibration
- Observe line speed and make adjustments
- Count produced purlins with length inspection
- Stack finished purlins properly by end-type
Stopping and shutdown:
- Stop the line by pressing emergency stop button
- Switch off main power after line stops fully
- Remove any remaining sheets from the line
- Clean machine and coil debris
Safety:
- Ensure safeguards are always in working condition
- Allow maintenance only by trained personnel
- Follow standard safety procedures during operation
Proper operating guidelines must be followed for optimum performance.
Maintenance and Lubrication
Regular maintenance activities:
Daily:
- Clean machine debris and sheet dust
- Check hydraulic oil level and refill
- Inspect bearings, gears for abnormalities
- Check and tighten loose parts and fasteners
Weekly:
- Grease bearings and gearbox
- Check tooling wear and clearances
- Verify pneumatic system for leaks
- Inspect electrical connections
Monthly:
- Inspect all safety features
- Check alignment of shafts, gears, motors
- Test emergency stop function
- Adjust roll gap spacing if required
Yearly:
- Complete inspection and overhaul
- Replace worn consumables
- Update machine software
- Implement preventive modifications
- Coat machine for corrosion protection
Proper maintenance as per schedule improves availability and lifespan.
How to Select Right C Purlin Machine
The selection factors for the ideal C purlin roll former include:
1. Production Requirements
- Type of purlin sections
- Metal thickness and strengths
- Output volume needed
2. Machine Capabilities
- Forming speed
- Sheet width and thickness range
- Purlin size range
- Automation level
3. Technical Factors
- Roller stand design
- Roll tooling quality
- Drives and power capacity
- Control systems
4. Additional Features
- Coil handling options
- Punching and cutting
- Stackers and conveyors
5. Vendor Credentials
- Experience and past installations
- Local support capabilities
- Compliance with standards
- Design expertise
- Value-added services
Comparing machines on these parameters ensures the right machine selection for cost-effective purlin production.
Comparison Between Two Models
Below is a comparison between two C purlin roll former models:
Machine | Maxima RM-20 | Ultima NU-25 |
---|---|---|
Speed | 25 m/min | 35 m/min |
Sheet Width | 800mm | 1000mm |
Thickness | 1.5 – 3mm | 1.2 – 4mm |
Purlin Height | 80 – 250mm | 100 – 300mm |
Power | 15kW | 22kW |
Automation | Auto cut-off | Fully auto stacker |
Controls | PLC | HMI + PLC |
Price | $92,000 | $128,000 |
The Ultima NU-25 has higher speed, width, automation and power. But the Maxima RM-20 provides a more economical solution for medium production needs.
Pros and Cons
Advantages
- High production rates and output
- Robust construction for longevity
- Flexible roll dies for size changes
- Consistent and precise C sections
- Low operating costs
- High-quality end products
Limitations
- High initial capital investment
- Regular maintenance and servicing
- Roll changing needs downtime
- Limited sheet thickness
- Fixed purlin sizes as per tooling
- Requires skilled workforce
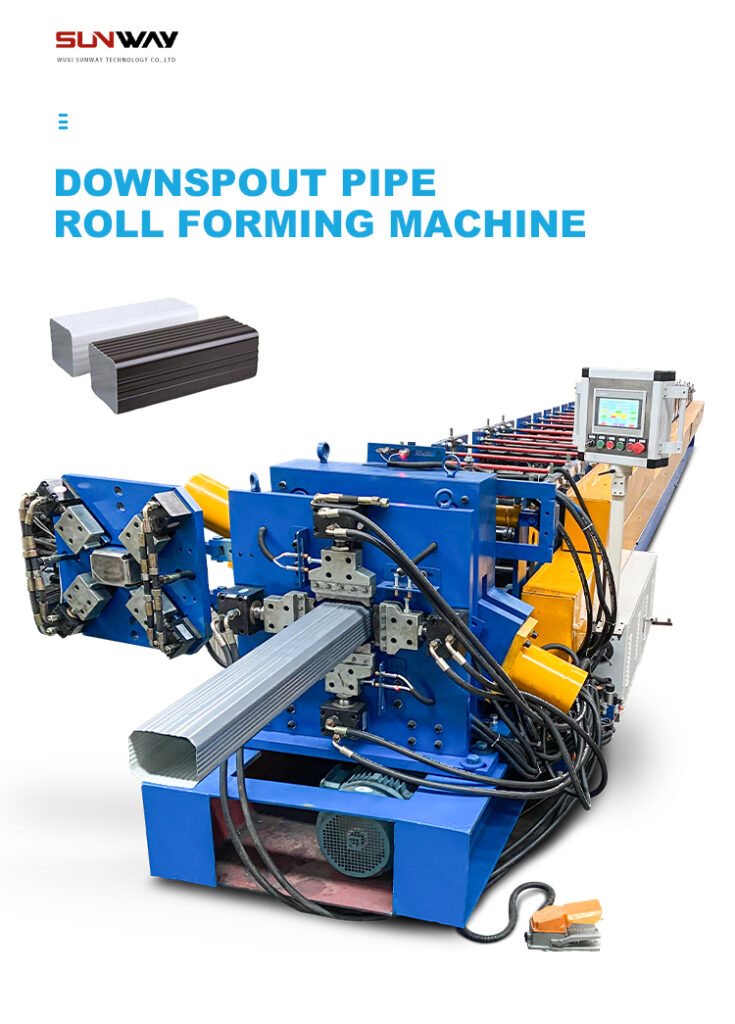
FAQs
Q: What materials can be formed into C purlins?
A: Typically low carbon steel sheets, galvanized steel, and aluminum sheets.
Q: What thickness is recommended for purlin sections?
A: 1.5 to 3 mm sheets for regular purlins. Up to 6mm sheets for heavy purlins.
Q: What determines the price of the machine?
A: Speed, automation level, power specs, sheet width capacity, and optional accessories impact the pricing.
Q: What is the typical production rate?
A: 25-40 meters per minute based on model, sheet thickness, and purlin size.
Q: Are slotted/holed purlins available?
A: Yes, punching units can provide slotting or holes for easy installation.
Q: How quick is size changeover on the line?
A: Roll changing takes 10-20 minutes. Section change needs 1-2 hour roll adjustment.
Q: What safety features are provided?
A: Emergency stops, limit switches, light curtains, door interlocks, safeguarding, etc.
Q: How should purlin quality be inspected?
A: Check dimensions at multiple points, flange buckling, twist, bow, inside radii, etc.
Conclusion
The C purlin roll forming machine enables efficient mass production of cold-formed C-sections for the construction industry. With advanced forming technology, robust build, and automation – these machines offer high production rates, flexible operations, and consistent quality output to meet structural building needs. The price range starts from $35,000 for basic models and goes up to $150,000 for high-capacity automated lines. By selecting the appropriate C purlin roll former based on production goals, throughput, line speed, and budget – manufacturers can benefit from an optimized and cost-effective purlin forming solution.