A shelf roll forming machine is an essential equipment used for rolling metal sheets into customized shelf profiles and structures. This guide provides a comprehensive overview of shelf roll forming machine technology, types, working principles, key specifications, suppliers, applications, installation and maintenance.
Overview of Shelf Roll Forming Machine
A shelf roll forming machine forms metal coil strips into various shelf profiles using a series of consecutive roll forming stations. The process involves gradually bending the strip material through contoured rolls to produce the desired cross-sectional shelf shape.
Key features:
- Highly customizable roll tooling to produce shelves of different sizes and shapes. Common profiles include rectangular, square, round, curved, C-shaped, Z-shaped.
- Capable of processing various metal materials – cold rolled steel, stainless steel, aluminum.
- Forms metal coils into ready shelf profiles continuously at high speeds.
- Automated operation for high production efficiency and precision forming.
- Quick roll set changeover for flexible manufacturing of different profiles.
- Offered in various widths up to 2000 mm for shelves of different widths.
- Roll forming lines can be customized with additional operations like punching, cutting, welding, powder coating.
Types of Shelf Roll Forming Machines
Type | Description |
---|---|
Standard Roll Forming Line | Basic roll line with entry guides, forming stations, exit guides for continuous production of linear shelves. Suitable for long production runs. |
CNC Roll Forming Line | Equipped with CNC controls for automatic adjustment of forming parameters, more flexible for small batch production. |
All-Electric Roll Forming Line | Powered fully by servo motors instead of mechanical drives. Enables highly precise and energy-efficient roll forming. |
High-Speed Roll Forming Line | Advanced lines with faster rpm, quick-change tooling to achieve higher production speeds. |
Customized Roll Forming Lines | Tailor-made lines incorporating additional prep operations like decoiling, leveling, pre-punching and post operations like cutoff, punching, bending, welding as per application requirements. |
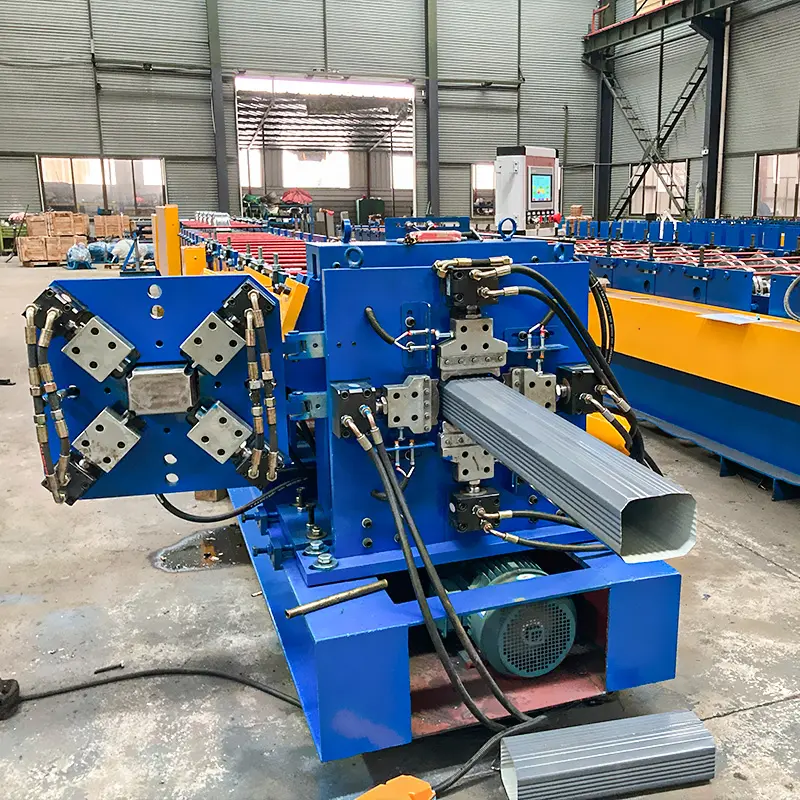
Working Principle of Roll Forming Machine
The working principle involves:
- Sheet metal coil stock is loaded at the decoiler station.
- The strip gets straightened and fed into the entry guides.
- It passes through a series of roll forming stations each with contoured rollers.
- At each station, the rolls bend the strip progressively to the desired profile.
- Roller contours along the line are designed to gradually form the final shelf shape.
- Finished formed profile exits continuously at the end and sent for further processing.
- Roll forming stations can be added/removed to modify the bending sequence for new profiles.
- The key components are the forming rollers, feeding mechanism, roll housing and base structure.
- Rollers apply pressure on the strip to bend it without scratches or deformation.
- Feeding mechanism precisely feeds the strip through each station at set speed.
- Roll housing provides supports and enclosures for the roll tooling.
- Base frame builds the foundation to hold the entire line rigidly.
Specifications of Shelf Roll Forming Machine
Parameters | Typical Values |
---|---|
Forming Speed | 10 – 25 m/min |
Maximum Coil Width | Up to 2000 mm |
Minimum Bending Radius | 1T (T=Thickness) |
Thickness of Material | 0.3 mm to 3 mm |
Main Drive Power | 3 kW to 15 kW |
Roller Diameter | 100 to 250 mm |
Roller Material | Alloy steel, high speed steel |
Roller Hardness | 50-60 HRC |
Roll Housing | Fabricated steel housing |
Frame | Steel welded frame |
Controller | PLC based |
Power Supply | 380V, 50 Hz 3 Phase |
Applications and Uses of Shelf Roll Forming Machine
Shelf roll forming machines are ideal for producing shelves for a wide range of applications:
Application | Description |
---|---|
Supermarket Shelves | For produce racks, store shelves, point of purchase displays in retail stores and supermarkets. |
Industrial Shelves | Racking, mezzanine floors, platforms, walkways for factories and warehouses. |
Commercial Shelves | Shelving systems for offices, institutions, auditoriums, libraries. |
Kitchen Shelves | Customized shelves for kitchen cabinet units, pantries, larders. |
Laboratory Shelves | Specialized chemical resistant shelves for laboratories, scientific facilities. |
Pharmacy Shelves | Shelves for pharmacies, medicine storage in hospitals. |
Fast Food Shelves | Durable shelves for fast food joints, cafeterias, restaurants. |
Home Shelves | Custom shelves for living rooms, bedrooms, garages in homes. |
Shelf Roll Forming Machine Suppliers
There are many equipment manufacturers providing shelf roll forming machines:
Supplier | Location | Product Details |
---|---|---|
ZHONGXING ROLL FORMING MACHINERY | Taizhou, China | CNC roll lines, max speed 30 m/min, width 1400mm |
AKYAPAK MAKINA SAN. TIC. LTD. | Istanbul, Turkey | Standard and customized roll lines, max width 2000mm |
UCALERTS | Ahmedabad, India | Electric and manual adjust roll lines, speed 10-15 m/min |
VORESO | Urmia, Iran | Offer turnkey projects for roll forming lines |
PLANETA-STANKO | Chelyabinsk, Russia | High speed roll forming lines, speed up to 45 m/min |
Pricing is dependent on speed, width, automation level, and can range from $8000 for manual lines to $50000 for CNC high speed lines. Chinese manufacturers offer cost-effective lines whereas European suppliers provide high precision equipment. Careful selection of machinery is needed based on production needs and budgets.
Installation and Maintenance of Roll Forming Lines
- Proper foundation needs to be constructed for installing the machine.
- Leveling and alignment of the line should be done precisely.
- Electrical, pneumatic and hydraulic connections must be hooked up by technicians.
- Trial runs help tune the equipment for optimal performance.
- Daily cleaning and lubricating of rolls is needed for smooth operation.
- Regular inspection of rollers, bearings, guides for wear and tear.
- Timely replacement of damaged rollers and components.
- Roll calibration should be done when changing profiles.
- Only authorized technicians should troubleshoot and undertake repairs.
- A maintenance log must be maintained by operators.
- Regular upkeep and overhaul extends machine life and productivity.
How to Select Shelf Roll Forming Machine Supplier
Consider the following when choosing roll forming equipment supplier:
- Experience and reputation in roll forming machinery.
- Range of standard and custom machines offered.
- Use of quality materials and components.
- Precision and consistency of formed profiles.
- Technical expertise for design support.
- Responsiveness to service calls and support.
- Flexibility for design changes and customization.
- Training support for operators.
- Availability of spare parts and consumables.
- Competitive pricing and payment terms.
- Adherence to timelines for manufacturing and delivery.
- Strong client references and testimonials.
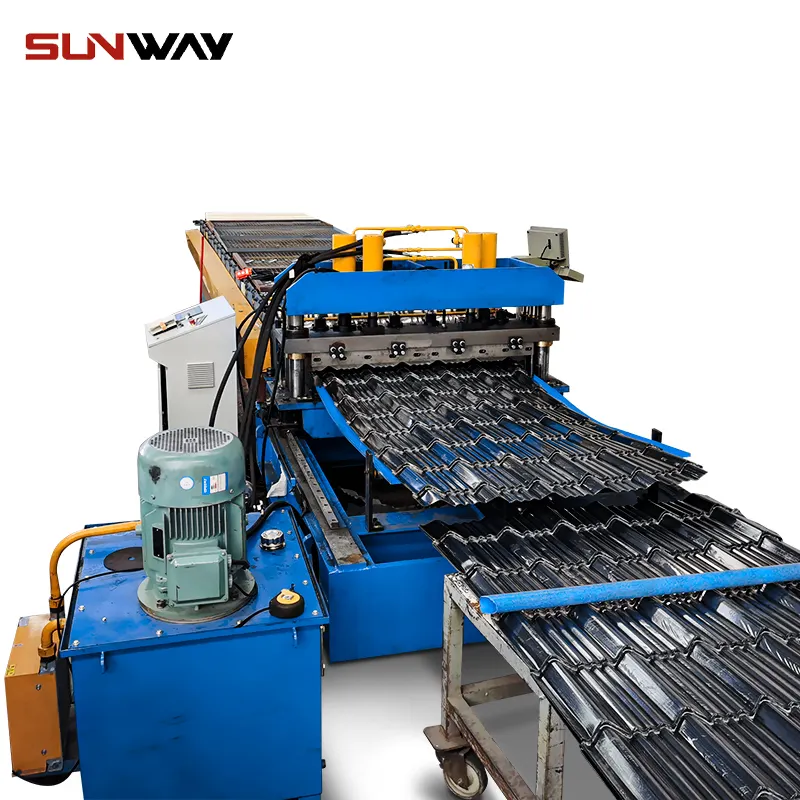
Comparison Between Types of Roll Forming Machines
Parameters | Standard Roll Line | CNC Roll Line | All Electric Line | High Speed Line |
---|---|---|---|---|
Set-up Time | Manual setup takes time | Quick setup with CNC | Average manual setup | Very quick setup |
Changeover Time | Long due to roll change | Reduced due to CNC | Average manual changeover | Minimum with quick change tooling |
Accuracy | Average accuracy | High accuracy and repeatability | High accuracy | Average accuracy |
Forming Speed | Average speed | Flexible adjustable speed | Energy efficient speed | Very high forming speed |
Automation | Manual operation | Automated operation | Manual operation | Semi-automated features |
Cost | Economical price | Higher investment cost | Average cost | Expensive, premium pricing |
Production Scale | Large volume batches | Small to medium batches | Medium to large batches | Large batch production |
Advantages of Shelf Roll Forming Machine
- Highly flexible roll tooling design for customized shelf profiles.
- Continuous and efficient forming of long length shelves.
- Consistent and superior quality end product.
- Minimal material wastage compared to other methods.
- Low labor involvement in automated lines resulting in cost savings.
- Quick changeover and set up enables responding faster to changing demands.
- Compact machines requiring less space in production facilities.
- Production scalability possible by adding more forming stations.
- Limited upkeep and maintenance since no heating or pressing needed.
- Long service life expectancy up to 15-20 years for machine.
Limitations of Shelf Roll Forming Machines
- High initial machinery purchase and tooling cost compared to other techniques.
- Roll forming limited to only linear profiles, not complex 3D shapes.
- Design and production of profiling tools needs expertise.
- Modification of rolls time-consuming if design changes made after purchase.
- Limits on minimum bending radius and material thickness.
- Potential for strips to spring back after forming.
- Troubleshooting roll wear and tear requires experience.
- Regular fine tuning needed to account for material property variations.
- Higher noise levels due to rotating equipment.
- Require foundation preparation and controlled environments.
FAQ
What materials can be roll formed into shelves?
- Most commonly cold rolled steel, stainless steel, galvanized steel, aluminum. Other materials like brass, copper can also be formed.
What thickness of sheets can be roll formed?
- Standard roll lines can process 0.3 mm to 3 mm thickness material. Beyond 3 mm requires higher capacity specialty lines.
What controls are used in roll forming machines?
- Standard lines use manual controls whereas CNC roll lines employ computer numeric controls for automatic operation. Servo motors provide precision movement.
How to design roll tooling for new shelf profile?
- It requires determining the sequential bending steps, mapping the roller contours mathematically, followed by machining of the profiled rolls accordingly. FE simulation helps optimize the process.
How much technical skill is needed to operate roll forming machines?
- Setup and routine operation can be learned relatively quickly. But design, maintenance and troubleshooting requires technical expertise in mechanics, controls, and roll forming process.
How to maintain roll forming machine performance?
- Schedule periodic cleaning, lubrication, inspection and replacement of wear items like bearings, rolls, guides. Control environment for dust and moisture. Conduct regular validation checks.
What safety measures are important for roll forming machines?
- Enclosing the rotating components, interlocks for safe access, E-stops, controlling electrical hazards from the PLC system, alarms, and personal protective gear.
How to reduce defects like twist or curl in rolled shelves?
- Check alignment, perform roll calibration, use anti-friction guides, adjust hold-down rollers, modify feed speed, and ensure uniform material properties.
What are the typical production rate and cost for roll formed shelves?
- With 10-20 m/min speeds, 6000-10000 feet can be produced per 8 hour shift. Roll formed shelves can cost $2 to $4 per linear foot depending on specifications.
Conclusion
Roll forming enables efficient mass production of shelves to meet exact specifications at low costs. With versatile roll tooling designs and reliable equipment from leading manufacturers, high quality shelves can be manufactured for diverse applications ranging from retail stores to industrial warehouses. However, appropriate due diligence is required during machinery selection and process monitoring to achieve results. When utilized effectively, shelf roll forming machines offer an economical solution for metal fabricators to serve various shelving demands.