Pipe roll forming machines are an efficient way to manufacture pipes, tubes, and hollow profiles. This innovative metal forming technology can produce seamless, high-quality pipes at fast production speeds. Pipe roll forming offers many benefits compared to traditional pipe manufacturing methods.
This comprehensive guide provides a deep dive into pipe roll forming. It covers how the machines work, the different components and systems, key specifications, the pipe forming process, common applications, advantages, and more. Read on to learn all about this modern and versatile pipe production method.
How Pipe Roll Forming Machines Work
Pipe roll forming utilizes a series of consecutive dies and roller stations that gradually form flat strip stock into a tubular shape. The strip stock is threaded through the inline stations of the machine. As it passes through each one, the material is continuously bent until it takes the form of a round, rectangular, or other shaped pipe.
The roll forming stations perform four key functions:
- Feeding – Feeder tables straighten the coil stock and guide it into the roll former
- Forming – Rolling dies progressively form the strip stock around a mandrel into the tubular shape
- Welding – Longitudinal welders join the formed edges together for seamless pipes
- Cutting – Cutoff dies shear the pipe into set lengths as it exits the machine
The strip stock moves through the roll former at a constant speed while the dies shape it in an efficient, continuous in-line process. This delivers high production rates and uniformity. Modern pipe roll forming lines are fully automated for minimal human input.
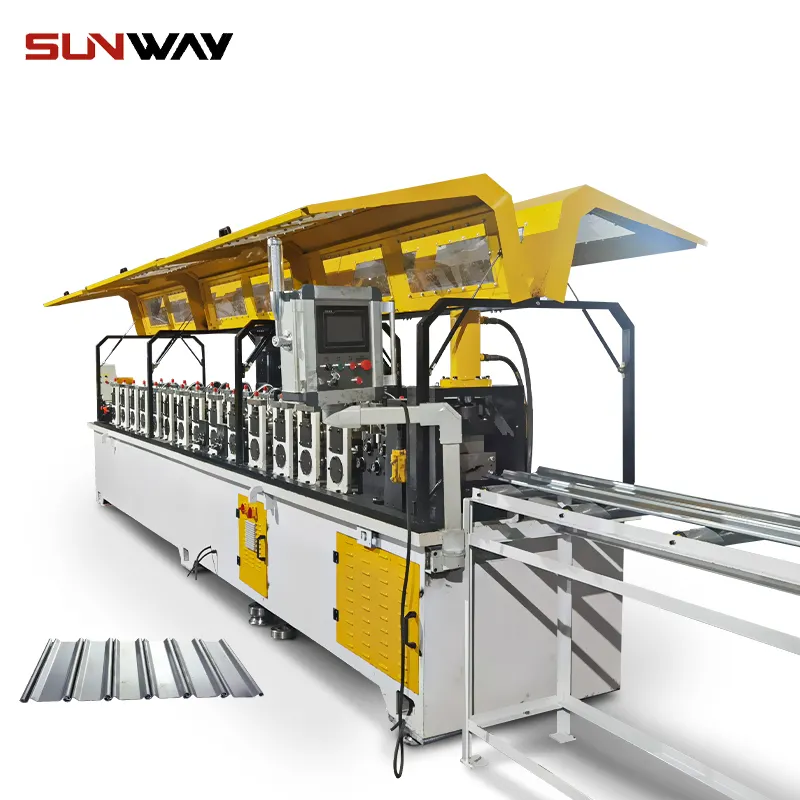
Main Components of Pipe Roll Forming Machines
Pipe roll forming equipment consists of several key components and systems that work together:
Coil Holding System
Holds large coils of flat strip stock that feeds into the roll former. Coils can weigh several tons so a sturdy unwinding system with coil loading equipment is required.
Feeder
The feeder table straightens the strip stock and guides it into the roll forming stations. This ensures smooth, kink-free feeding.
Forming Stations
Progressively apply pressure to bend the strip stock around a round, square, or other-shaped mandrel. Typically 10-16 stations form the material incrementally into the pipe shape.
Mandrel
The central forming shaft that the strip passes over as it is rolled into shape. Mandrels come in different sizes and shapes.
Welding System
Joins the formed edges together for continuous welded pipes. Usually spot, MIG, or laser welders.
Sizing Rollers
Calibrate the pipe diameter and shape immediately after welding.
Cutoff Press
Shears the pipes into individual lengths as they exit the last station. Pneumatic, hydraulic, or servo-electric presses.
Conveyors
Transports the finished cut pipes away from the roll former. Multiple conveyors stages are typical.
Control System
Computerized controls to operate all components and monitor the pipe forming process.
Key Specifications of Pipe Roll Forming Machines
Pipe roll formers come in different configurations to produce all kinds of tubular profiles. Key specifications include:
- Max pipe diameter – The biggest pipe diameter the machine can produce. Ranges from just a few inches to over 60″.
- Min/max wall thickness – The thinnest and thickest pipe walls the roll former can handle. From less than 1 mm up to 12 mm.
- Width capacity – The max strip stock width the machine accepts. Typical values between 100 – 800 mm.
- Speed – Production rate in feet/min or m/min. High-end roll formers exceed 130 ft/min.
- Main drive power – The power rating of the motor driving the forming stations. Ranges from 5 kW to over 50 kW.
- Material type – The metals the machine supports, like steel, stainless steel, aluminum, etc.
- Welding types – Welding options like MIG, TIG, laser, etc.
- Automation – Level of automated features for part handling, changeover, monitoring, etc.
Consider your product mix to select a pipe roll former with suitable capacity, speed, power, and features.
The Pipe Roll Forming Process
The pipe production process on a roll forming line generally follows this sequence:
- Decoiling – Strip stock is unwound from a coil and fed into the roll former. An automatic decoiler system is used.
- Feeding – Feed tables with positioned rollers straighten the strip stock and guide it into the first forming station.
- Pre-forming – Initial stations make light bends to start gradually forming the strip edges up.
- Forming – In the main set of stations, the strip stock flows over the round, square, or shaped mandrel while dies apply calibrated pressure to bend it into a tube.
- Welding – A longitudinal welding unit at the apex joins the formed edges together to create a continuous seamless pipe.
- Calibration – Sizing rollers calibrate the pipe shape and diameter to meet specifications.
- Cutting – A cutoff press shears the pipes into set lengths based on servo feed length controls.
- Discharging – Conveyors transport the cut pipes away from the last station for downstream processes.
- Stacking – The conveyor stages can include automatic stacking units to neatly stack the finished pipes.
Throughout this automated sequence, the control system monitors all functions and parameters like feeds, speeds, pressures, welds, etc.
Applications of Pipe Roll Forming Machines
Pipe roll forming lines produce tubular profiles out of metal coils for many applications:
- Drainage and plumbing pipes
- Structural tubes
- Scaffolding, frames, poles
- Furniture tubing
- Railings and fences
- Heat exchangers
- Exhaust pipes and mufflers
- HVAC ductwork
- Roller conveyor tubes
- Electrical conduits
- Gas cylinders
- Fire sprinkler pipes
And more. The flexible roll forming process can form quality round, rectangular, and shaped tubes from 1″ up to 80″ in diameter.
Almost any industry uses rolled metal pipes and tubes in their products, equipment, or structures. Companies invest in pipe roll forming lines to make tubes efficiently for their specific application requirements.
Benefits of Pipe Roll Forming
There are many advantages to using roll forming machines for pipe and tube production:
High Productivity – Pipe rollers generate extremely high outputs up to 10x faster than manual methods. Producing over 1000 feet per minute is possible.
Low Tooling Costs – Only a set of relativity inexpensive roller dies are needed. New shapes just require a die set change.
Flexibility – Quick roll set changeovers facilitate frequent product changeovers. Many different tube sizes and shapes can be made on one machine.
Consistent Quality – Pipe properties stay uniform since material moves continuously through synchronized stations. No batch-to-batch deviations.
Great Accuracy – Advanced controls precisely monitor all process parameters for high dimensional accuracy and wall thickness consistency.
Material Savings – No material wasted from welding or machining. Near 100% material utilization is achievable.
Lower Energy Use – Roll forming is more energy efficient than other pipe production techniques.
Improved Safety – Fully automated operation reduces risk of worker injuries.
Reduced Costs – The productivity, efficiency, and simplicity of roll forming results in lower overall manufacturing costs.
For most companies, the fast speeds, flexibility, quality, and cost savings of modern pipe roll forming machines deliver major benefits over previous tube manufacturing methods.
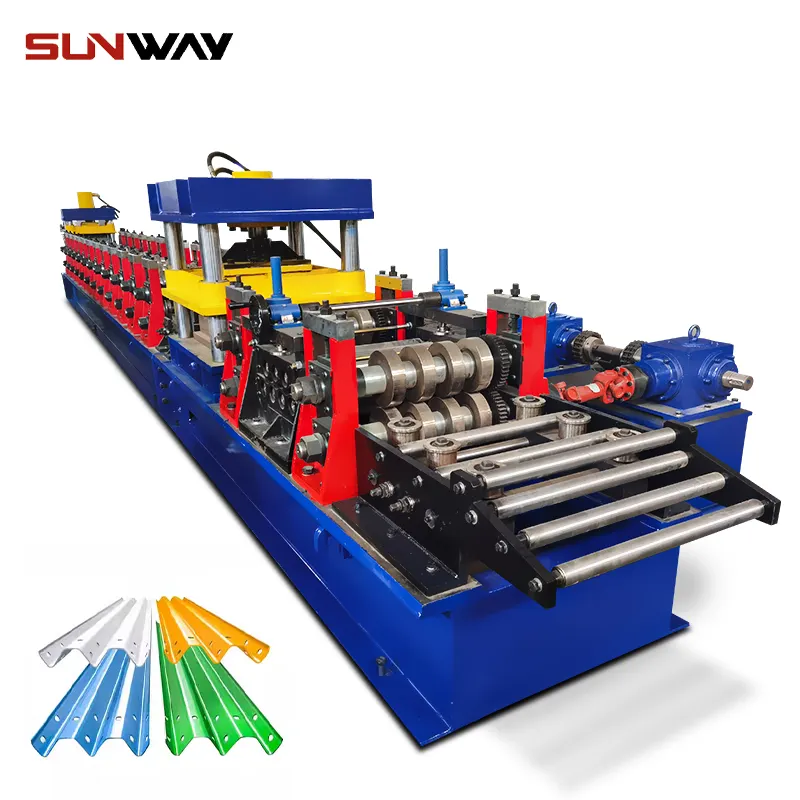
Typical Defects in Pipe Roll Forming
While pipe roll forming is a reliable, high-precision process, some defects can arise if machines are not properly set up and controlled:
- Weld flaws – Incomplete welds, cracks, inadequate penetration, burnt or oxidized seams. Caused by issues in the welding stage.
- Dimensional deviations – Incorrect pipe diameter, wall thickness, out-of-roundness. Often from worn, misaligned, or improperly spaced/adjusted roll dies.
- Shape distortions – Ovality, flat spots, fluting. Results from uneven roll pressures on the strip.
- Surface marks – Roller indentation, scratches, galling. Due to contaminated, damaged, or misaligned roll dies.
- Internal stresses – Excess residual stresses in the material. From improperly adjusted roll pressures and metal properties.
- End cut defects – Ragged, skewed, or inconsistent cut ends from worn, misaligned, or incorrectly spaced cutoff dies.
The most common remedies involve inspecting and refurbishing roll dies, adjusting die pressures and roller alignments, cleaning strip stock, and optimizing weld parameters. The production speed may also need to be reduced.
Tips for Buying a Pipe Roll Forming Machine
If you are looking to purchase pipe roll forming equipment, keep these tips in mind:
- Get quotes from at least 3-4 machine manufacturers/OEMs to compare pricing. Chinese suppliers often offer significant cost savings.
- Choose a supplier with a proven track record in pipe roll forming. Look for extensive experience, installed bases, and case studies.
- Specify your product requirements – dimensions, materials, volumes, changeovers, etc. The supplier can recommend the properly sized machine.
- Ask about available automation features for coil loading, conveyors, stacking, part handling, and changeovers. This boosts efficiency and consistency.
- Inquire about after-sales technical support, maintenance contracts, spare parts availability, and training. Reliable long-term support is crucial.
- If possible, visit the supplier’s facility, view their in-house testing, and request references to confirm capabilities.
- Negotiate warranties, guarantees, and payment terms. Extended warranties are ideal to ensure equipment performance.
Selecting the right pipe roll forming equipment for your specific needs will maximize manufacturing productivity, quality, and profitability.
Leading Manufacturers of Pipe Roll Forming Machines
Some of the top global manufacturers of high-quality pipe roll forming machines include:
- Mewag Tech (Switzerland) – Offers the Rolla-V pipe roll forming system for tubes up to 80″ diameter.
- Gasparini (Italy) – The Spiralpipe range produces tubes from 10-63″ diameter.
- Bradbury (USA) – Leading supplier of pipe roll forming lines for over 70 years.
- Formtek (USA) – Provides lines for HVAC, sprinkler, and customized pipe applications.
- Samco (South Korea) – Manufactures pipe roll forming machinery for 20-200 mm diameter tubes.
- Rollvis (India) – Rolls pipes from 15-150 mm diameter with MIG/TIG welding options.
- Jouanel (France) – Makes longitudinal and spiral pipe roll forming equipment.
- Wuxi Zhanzhong (China) – Supplies very cost-effective pipe roll forming machines.
These top brands offer advanced equipment engineered for high speeds, changeover flexibility, and top quality pipes. Most can customize machinery to your specifications.
Pipe Roll Forming Machine Costs
The cost of a new pipe roll forming line varies substantially based on:
- Machine size – Max pipe diameter/width, output speed, and power requirements primarily influence cost.
- Features – More automated systems for coil handling, welding, stacking, etc. add expense.
- Brand – Major international brands typically cost 50-100% more than Chinese manufacturers.
- Customization – Specialized tooling, controls, and configurations increase costs.
As a rough guideline, small pipe roll formers start around $50,000. Large high-production lines from major brands can cost over $500,000. Most fall in the $100,000 – $250,000 range.
Operational expenses are reasonable. Roller dies last for years and electricity usage is modest. With proper maintenance, pipe roll formers deliver significant long-term value.
Conclusion
Pipe roll forming machines offer a highly efficient method to mass produce seamless metal tubes. The technology continues to expand as manufacturers recognize the benefits over conventional tube production techniques.
With their fast speeds, flexibility, quality, and cost advantages, pipe roll formers are the premier tubular profile solution for many industries. This guide provided a comprehensive overview of how pipe roll forming machinery works, processes, applications, specifications, benefits, top brands, costs, and more.
FAQ
Here are answers to some frequently asked questions about pipe roll forming technology:
What materials can be roll formed into pipes?
Almost any ductile metal strip stock is suitable, including low carbon steel, stainless steel, aluminum, copper, and brass. Pre-coated and pre-painted coils can also be roll formed.
What shapes of pipes can be produced?
Round, rectangular, square, and oval are standard. Special shaped mandrels enable more complex triangular, channel, and custom profiles.
How are different pipe diameters changed over?
A simple mandrel change to match the required diameter is all that is needed in most cases. It takes 15-30 minutes.
Can a single pipe roll forming machine make multiple products?
Yes. With a set of quick-change tooling, one machine can switch between various pipe sizes, geometries, and metals.
What thickness of material can be roll formed into pipes?
Around 0.5 – 12 mm is standard. Thinner/thicker gauges are possible with specialized configurations.
What welding methods are used on pipe roll formers?
MIG welding is most common. TIG, laser, and plasma welding are also options for high-end applications.
How long do pipe roll forming machines last?
With proper use and maintenance, pipe roll formers typically provide 20-30 years of productive service before major overhauls are needed.
How are roll formed pipes cut to length?
Pneumatic or hydraulic cutoff presses shear the pipes at high speed to precise lengths based on digital length controls.
Does pipe roll forming require secondary finishing steps?
Minimal finishing is needed since the automated process ensures tight tolerances. Just simple end deburring and surface cleanup is required.