Introduction
In the world of modern manufacturing, efficiency and precision are paramount. One remarkable innovation in this realm is the sandwich panel roll forming machine, a technological marvel that plays a pivotal role in producing high-quality building materials. This article delves into the fascinating world of these machines, uncovering their significance, operation, and benefits.
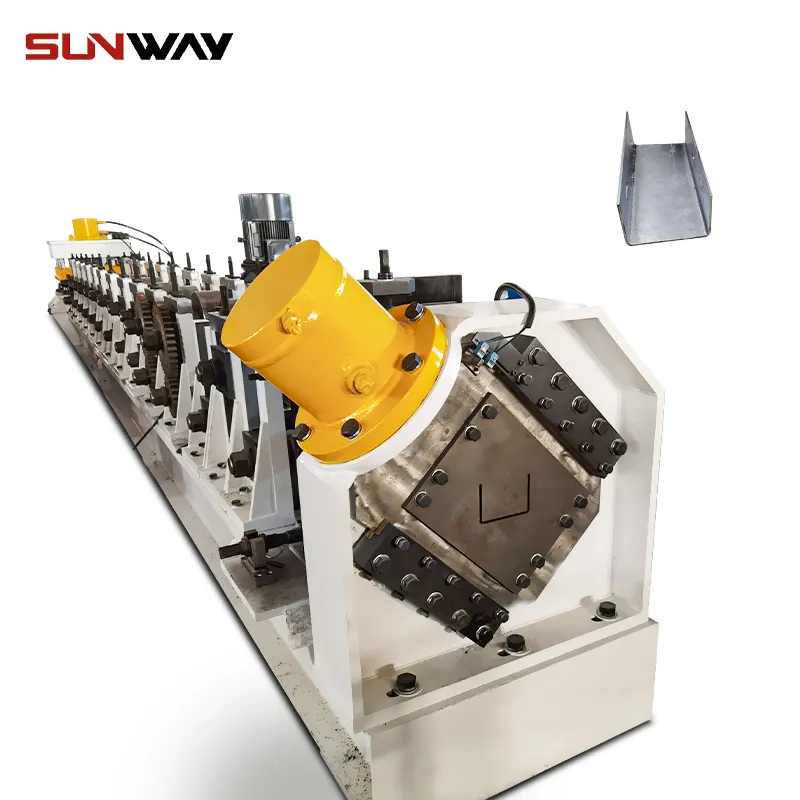
Understanding Sandwich Panels
What are Sandwich Panels?
Sandwich panels are composite materials used extensively in the construction industry. They consist of three main layers: two external layers, often made of metals such as steel, aluminum, or even fiberglass, and a core material in between, which can be anything from foam, mineral wool, to polyurethane. This unique combination results in a material that boasts remarkable thermal and acoustic insulation properties, making it an ideal choice for constructing energy-efficient buildings.
Applications of Sandwich Panels
The versatility of sandwich panels has led to their wide application in various industries. From industrial warehouses and commercial buildings to residential homes, sandwich panels find their use due to their lightweight nature, excellent insulation, and aesthetic appeal. They have become a staple in cold storage rooms, cleanrooms, and even in the aerospace sector.
The Role of Roll Forming Machines
What is a Roll Forming Machine?
At the heart of producing sandwich panels lies the roll forming machine. This specialized piece of equipment transforms flat metal sheets into complex cross-sectional profiles with a continuous process. It involves a series of rollers that progressively shape the metal, ensuring precision and consistency in the final product.
Importance of Roll Forming in Manufacturing
Roll forming holds immense importance in the manufacturing industry. Unlike traditional methods that involve cutting, bending, and welding, roll forming is a continuous process that minimizes material waste and speeds up production. This is particularly crucial in the creation of sandwich panels, where precision and uniformity are paramount.
The Working Mechanism of Sandwich Panel Roll Forming Machines
Step-by-Step Process of Sandwich Panel Production
The production of sandwich panels using roll forming machines follows a systematic sequence. First, the external metal layers are fed into the machine, where they undergo profiling by the rollers. Simultaneously, the core material is injected between the two metal layers. The layers are then bonded together, creating a sturdy composite material. The continuous nature of roll forming ensures a seamless end product, ready for installation.
Stay tuned for the second part of this article, where we’ll explore the different types of sandwich panel roll forming machines and their advantages in the manufacturing process.
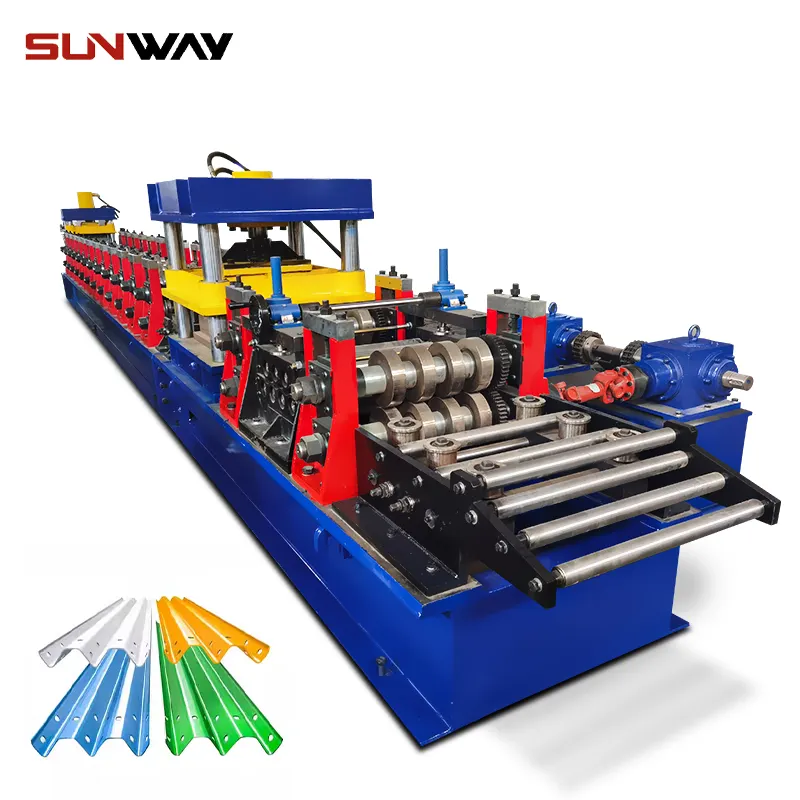
Types of Sandwich Panel Roll Forming Machines
Continuous Line vs. Discontinuous Line Machines
Sandwich panel roll forming machines come in two main types: continuous line and discontinuous line machines. Continuous line machines are designed for high-volume production and offer a continuous process from raw materials to the finished panel. On the other hand, discontinuous line machines are suitable for smaller production batches and allow for more flexibility in design and customization.
Single Belt vs. Double Belt Machines
Another categorization of sandwich panel roll forming machines is based on the number of belts used in the production process. Single belt machines have one set of rollers and belts, which streamline the production process but might limit certain design possibilities. Double belt machines, on the other hand, provide more design flexibility by allowing different profiles on each belt.
Advantages of Using Sandwich Panel Roll Forming Machines
Precision and Consistency in Production
One of the remarkable advantages of using sandwich panel roll forming machines is the precision they offer. The systematic shaping process ensures that each panel produced is consistent in dimensions and quality. This level of accuracy is crucial in construction, where even the slightest variation can lead to inefficiencies and structural issues.
Flexibility and Customization
Roll forming machines allow for the creation of a wide range of panel profiles. Whether it’s for architectural aesthetics or specific insulation requirements, these machines can be tailored to meet diverse needs. The ability to customize not only enhances the creative possibilities but also ensures that the panels fit seamlessly into various construction projects.
Increased Production Efficiency
In a competitive manufacturing landscape, efficiency is key. Sandwich panel roll forming machines excel in this aspect by significantly reducing production time and material waste. With a continuous process that requires minimal manual intervention, these machines boost overall productivity and contribute to cost savings.
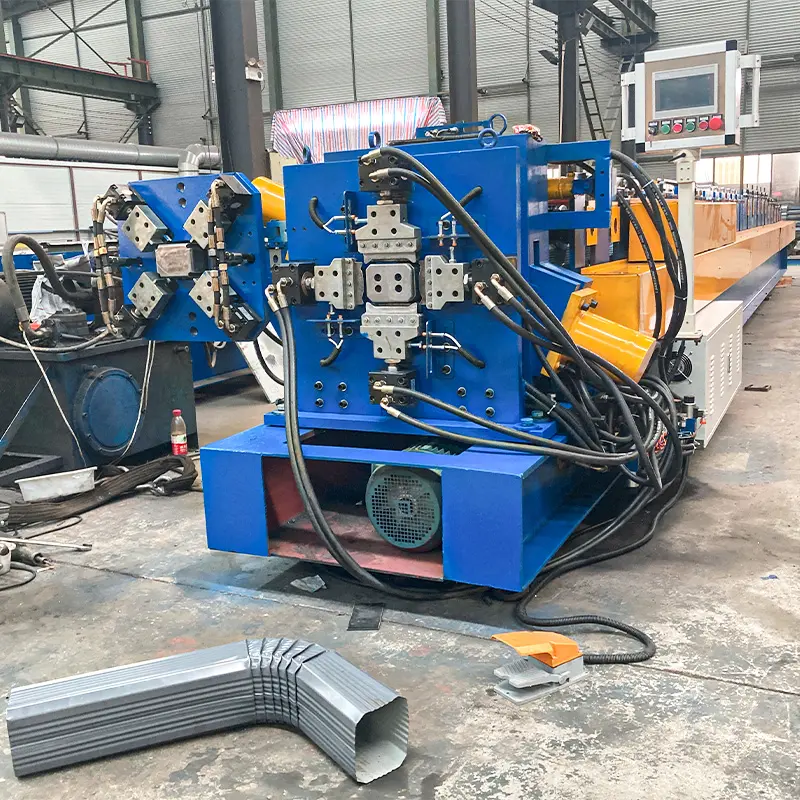
Factors to Consider When Choosing a Sandwich Panel Roll Forming Machine
Material Compatibility
Selecting the right material for your sandwich panels is crucial. The roll forming machine’s compatibility with the chosen materials, whether it’s steel, aluminum, or others, should be thoroughly assessed. Compatibility ensures optimal shaping and bonding during the production process.
Production Speed and Capacity
Depending on the scale of your production, the speed and capacity of the roll forming machine play a vital role. High-volume production demands machines that can deliver output efficiently without compromising quality.
Machine Flexibility and Setup
Consider the flexibility of the machine in accommodating different panel profiles. Additionally, the ease of setup and changeover between different designs is essential for maintaining a smooth workflow and minimizing downtime.
Maintenance and Upkeep of Roll Forming Machines
Regular Maintenance Practices
To ensure the longevity and consistent performance of sandwich panel roll forming machines, regular maintenance is paramount. Cleaning, lubrication, and routine inspections prevent wear and tear, ultimately leading to a prolonged lifespan of the equipment.
Common Issues and Troubleshooting
Like any machinery, roll forming machines can encounter issues. These might include misalignment of rollers, material feed problems, or irregular panel shapes. Familiarizing oneself with common troubleshooting techniques can prevent production delays and ensure a seamless operation.
Future Trends in Sandwich Panel Roll Forming Technology
Automation and Smart Manufacturing
The future of manufacturing lies in automation and smart technologies. Sandwich panel roll forming machines are no exception. Integration of automation, robotics, and data-driven processes can enhance efficiency, reduce human error, and optimize the production workflow.
Sustainable Manufacturing Practices
With an increasing emphasis on sustainability, the manufacturing industry is moving towards eco-friendly practices. Sandwich panel roll forming machines are likely to adopt more sustainable materials and energy-efficient processes, aligning with global environmental goals.

Conclusion
In the world of construction and manufacturing, sandwich panel roll forming machines have revolutionized the way we create building materials. Their precision, efficiency, and adaptability have positioned them as essential tools for producing high-quality panels that meet the diverse needs of modern architecture. As technology continues to evolve, these machines will undoubtedly play a pivotal role in shaping the future of construction.
FAQs
- Q: Can sandwich panel roll forming machines handle different core materials?
- A: Yes, these machines can work with various core materials like foam, mineral wool, and polyurethane.
- Q: Are discontinuous line machines suitable for large-scale production?
- A: Discontinuous line machines are better suited for smaller production batches and increased design flexibility.
- Q: How often should I perform maintenance on a roll forming machine?
- A: Regular maintenance should be conducted according to the manufacturer’s guidelines, typically on a monthly basis.
- Q: What advantages do double belt machines offer over single belt machines?
- A: Double belt machines provide greater design flexibility by allowing different profiles on each belt.
- Q: What role will automation play in the future of sandwich panel roll forming?
- A: Automation will enhance efficiency and accuracy, leading to more streamlined and productive manufacturing processes.