Introduction
In the construction industry, efficient production of structural components is crucial for ensuring timely completion of projects. C purlins, which are widely used for structural support, require precise manufacturing processes to achieve consistent quality and dimensional accuracy. This is where a C purlin roll forming machine plays a vital role. This article delves into the details of C purlin roll forming machines, their benefits, working principles, applications, and factors to consider when choosing one.
What is a C Purlin Roll Forming Machine?
A C purlin roll forming machine is a specialized piece of equipment used to manufacture C purlins, which are cold-formed steel channels widely utilized in the construction industry. The machine takes flat metal coils and gradually bends and forms them into the desired C-shaped cross-section. This continuous roll forming process ensures consistent dimensions and high production efficiency.
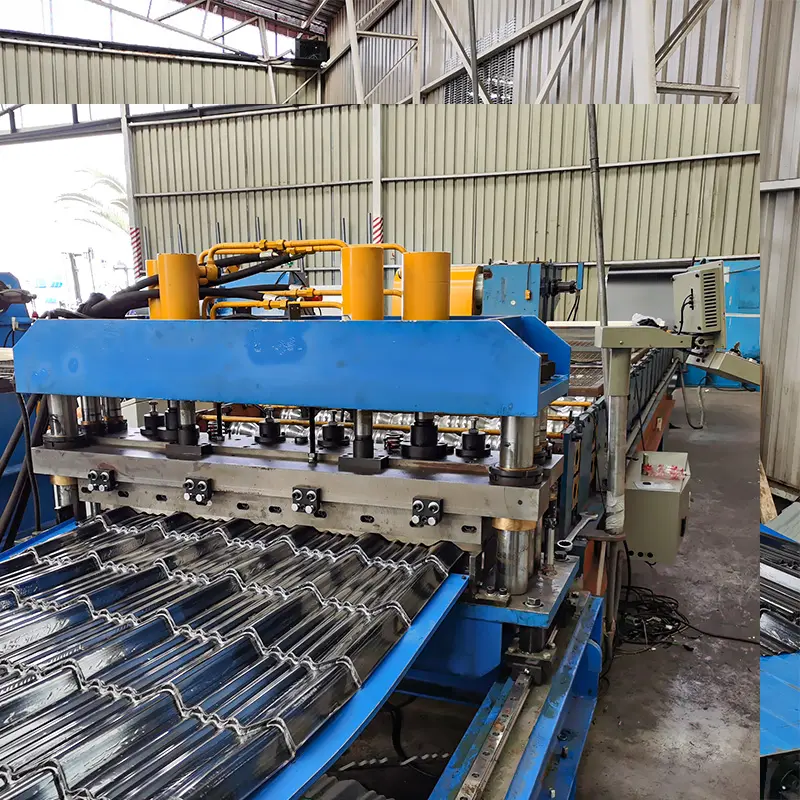
Benefits of Using a C Purlin Roll Forming Machine
Using a C purlin roll forming machine offers several advantages, including:
- Efficiency: Roll forming machines can produce C purlins at high speeds, significantly increasing production efficiency compared to traditional fabrication methods.
- Consistency: The machine ensures uniform dimensions, shapes, and hole patterns throughout the production process, leading to consistent product quality.
- Flexibility: C purlin roll forming machines can be adjusted to produce purlins of different sizes and profiles, providing flexibility to meet various project requirements.
- Cost savings: Automated production and reduced material waste result in cost savings over time, making C purlin roll forming machines a cost-effective choice.
- Improved strength: The cold-forming process enhances the strength and load-bearing capacity of C purlins, making them ideal for structural applications.
- Time savings: With quick setup and high production speeds, roll forming machines save significant time compared to manual fabrication methods.
Key Features of a C Purlin Roll Forming Machine
A typical C purlin roll forming machine comprises the following key features:
- Uncoiler: This component holds the metal coil and feeds it into the machine.
- Rollers: The rollers gradually shape the metal strip into the desired C-shaped profile.
- Cutting Mechanism: A flying shear or a post-cutting mechanism is used to cut the formed purlins to the desired lengths.
- Control System: Modern roll forming machines incorporate advanced control systems that ensure precise control over the entire production process.
- Safety Features: Safety mechanisms such as emergency stop buttons, safety guards, and sensors are incorporated to ensure operator safety during machine operation.
- Adjustability: C purlin roll forming machines often offer adjustable settings for width, height, and hole patterns, allowing for customization according to specific project requirements.
- Material Handling System: Some machines include an automated material handling system that simplifies the feeding and positioning of metal coils, enhancing overall efficiency.
- Monitoring and Feedback: Advanced machines feature monitoring systems that provide real-time feedback on the production process, allowing operators to identify and address any issues promptly.
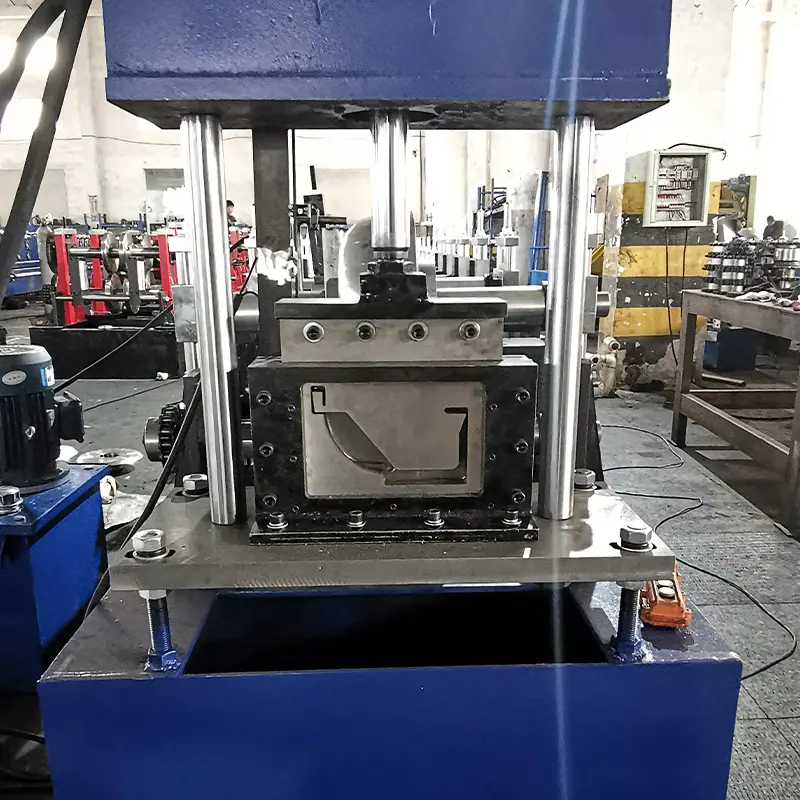
Types of C Purlin Roll Forming Machines
There are different types of C purlin roll forming machines available, each suited for specific production requirements. The following are the commonly used types:
5.1 Single Station C Purlin Roll Forming Machine
The single station C purlin roll forming machine is a compact and versatile option suitable for small-scale production. It typically consists of a single set of rollers that progressively form the C-shaped profile.
5.2 Continuous C Purlin Roll Forming Machine
The continuous C purlin roll forming machine is designed for large-scale production and offers high-speed operation. It features multiple sets of rollers that form the purlin profile in a continuous manner.
5.3 Adjustable C Purlin Roll Forming Machine
The adjustable C purlin roll forming machine provides flexibility in producing C purlins of various sizes. It allows for easy adjustment of roller positions, width, height, and hole patterns to accommodate different project specifications.
Working Principle of a C Purlin Roll Forming Machine
The working principle of a C purlin roll forming machine involves several sequential steps:
- Uncoiling: The metal coil is loaded onto the uncoiler, which feeds it into the machine.
- Guiding: The coil passes through a set of guiding rollers that ensure proper alignment and tension.
- Roll Forming: The metal strip gradually passes through a series of rollers, each set responsible for shaping and forming a specific section of the C purlin profile.
- Cutting: Once the desired length is reached, a cutting mechanism, such as a flying shear or a post-cutting system, cuts the formed purlin to the required size.
- Stacking: The cut purlins are stacked or conveyed to a collection area for further processing or packaging.
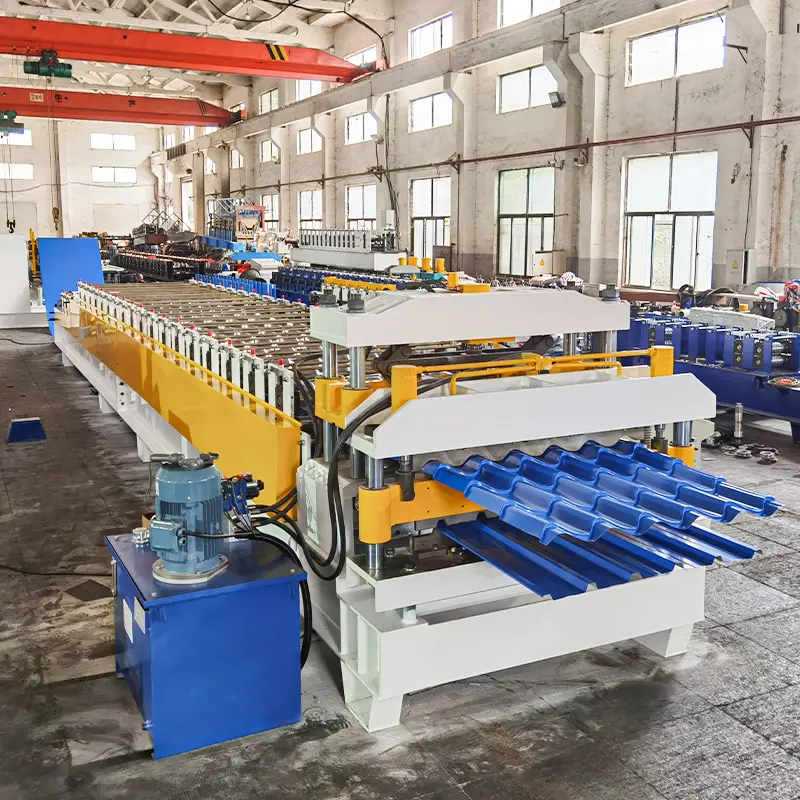
Advantages of Using a C Purlin Roll Forming Machine
The utilization of a C purlin roll forming machine provides several advantages:
- High Production Efficiency: Roll forming machines can produce C purlins at high speeds, allowing for large volumes of production within a shorter time frame.
- Consistent Quality: The machine ensures uniform dimensions, shapes, and hole patterns throughout the production process, resulting in consistent product quality.
- Customization: C purlin roll forming machines can be easily adjusted to produce purlins of different sizes and profiles, catering to specific project requirements.
- Cost-effectiveness: Automated production and reduced material waste contribute to cost savings over time, making roll formed C purlins a cost-effective choice.
- Enhanced Strength: The cold-forming process enhances the strength and load-bearing capacity of C purlins, providing structural reliability.
- Reduced Labor Dependency: Roll forming machines reduce the reliance on manual labor, resulting in increased productivity and reduced labor costs.
Applications of C Purlin Roll Forming Machines
C purlin roll forming machines find extensive use in various construction applications, including:
- Roofing Systems: C purlins are commonly used in roofing systems to provide structural support and stability. The roll formed C purlins create a strong framework that can withstand the weight of roof materials and adverse weather conditions.
- Wall Framing: C purlins are also utilized in wall framing, where they serve as horizontal supports for attaching exterior cladding materials. The precise dimensions and consistency achieved through roll forming ensure proper alignment and structural integrity.
- Steel Structures: C purlins find applications in steel structures such as warehouses, factories, and industrial buildings. They are used as primary structural members, providing support for roof and wall panels, as well as reinforcing the overall structure.
- Agricultural Buildings: C purlins are commonly used in the construction of agricultural buildings such as barns, sheds, and livestock shelters. They provide the necessary strength and stability to withstand the demands of agricultural environments.
- Mezzanine Floors: C purlins are employed in the construction of mezzanine floors, which are intermediate floors built within a building. The roll formed purlins create a robust framework that supports additional levels for storage, offices, or retail spaces.
- Solar Panel Mounting: C purlins are utilized in solar panel mounting systems. The precise dimensions and strength of the roll formed purlins ensure secure attachment of solar panels to rooftops or ground structures, optimizing energy generation.
- Infrastructure Projects: C purlins play a vital role in infrastructure projects such as bridges and tunnels. They are used as structural components in the construction of support systems and frameworks for these large-scale projects.
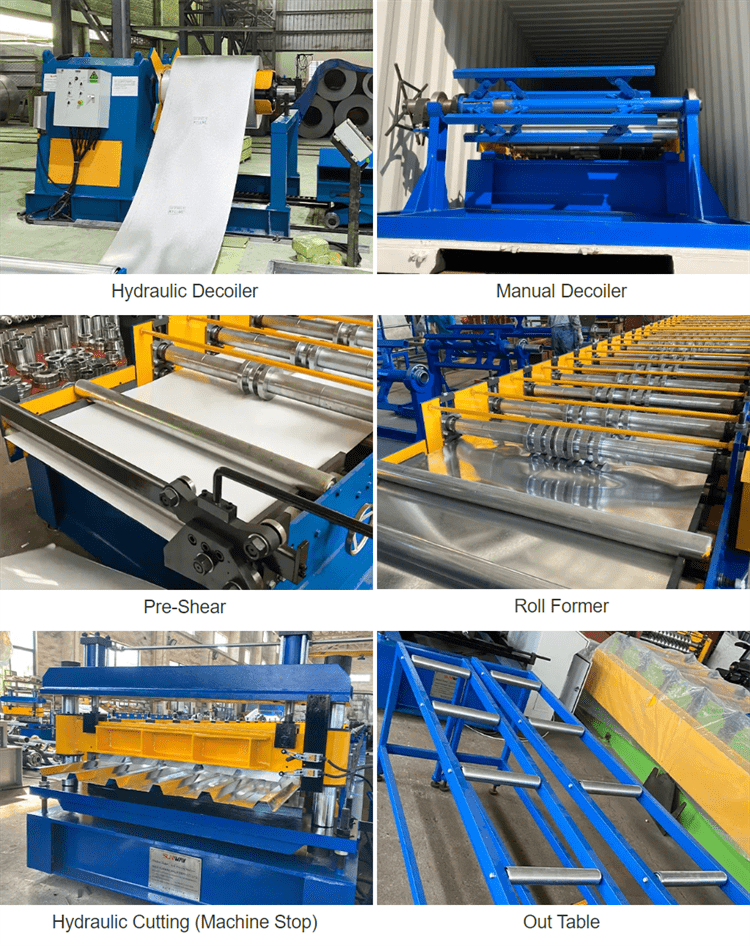
Factors to Consider When Choosing a C Purlin Roll Forming Machine
When selecting a C purlin roll forming machine, several factors should be taken into consideration:
- Production Capacity: Assess the required production capacity to determine the appropriate machine size and speed that can meet the production demands.
- Material Compatibility: Ensure that the roll forming machine is compatible with the specific metal material, gauge, and coating requirements for producing C purlins.
- Profile Flexibility: Consider the machine’s ability to produce different C purlin profiles, widths, heights, and hole patterns to accommodate varying project specifications.
- Automation and Control: Evaluate the level of automation and control features offered by the machine, such as advanced control systems, monitoring capabilities, and automation of material handling.
- Machine Reliability: Research the reputation and reliability of the manufacturer and the machine itself. Read customer reviews and assess the machine’s durability, maintenance requirements, and after-sales support.
- Cost and ROI: Compare the costs of different machines, considering the initial investment, operating expenses, and potential return on investment based on production efficiency and cost savings.
- Space and Power Requirements: Evaluate the space availability in your facility and ensure that the machine’s dimensions and power requirements are compatible with your setup.
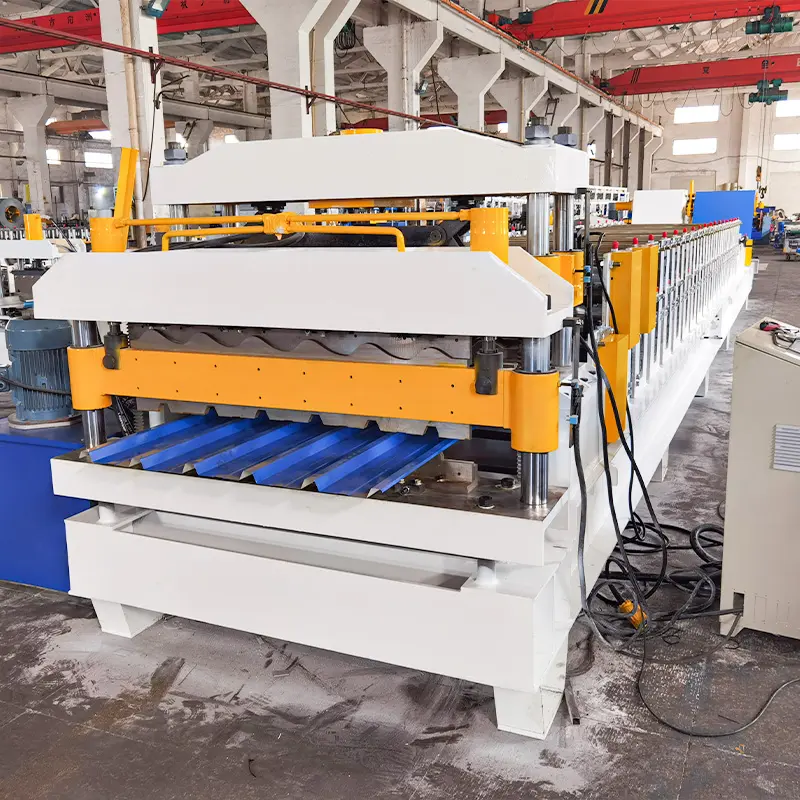
Maintenance and Care for a C Purlin Roll Forming Machine
To ensure optimal performance and longevity of a C purlin roll forming machine, proper maintenance and care are essential. Here are some key maintenance practices to follow:
- Regular Lubrication: Keep the machine’s moving parts well lubricated to minimize friction and prevent premature wear. Follow the manufacturer’s guidelines for lubrication frequency and use appropriate lubricants.
- Cleaning and Inspection: Regularly clean the machine to remove debris and accumulated dirt. Conduct routine inspections to identify any signs of damage, misalignment, or wear on rollers, cutting mechanisms, and other components.
- Tension and Alignment Checks: Check and adjust the tension of the material feeding system and ensure proper alignment of rollers to maintain consistent product quality.
- Electrical and Control System Maintenance: Regularly inspect and maintain the electrical and control systems of the roll forming machine. Check for loose connections, damaged cables, and malfunctioning components. Clean control panels and ensure proper calibration of sensors and switches.
- Safety Measures: Ensure that all safety features, such as emergency stop buttons and safety guards, are functioning properly. Regularly inspect and test these safety mechanisms to guarantee the safety of operators and prevent accidents.
- Operator Training: Provide proper training to machine operators on the maintenance procedures, safety protocols, and optimal operating practices. Encourage operators to report any issues or abnormalities promptly.
- Documentation and Records: Maintain a comprehensive record of maintenance activities, including lubrication schedules, inspection reports, and any repairs or replacements performed. This documentation helps track maintenance history and facilitates troubleshooting.
By following these maintenance practices, you can maximize the lifespan of your C purlin roll forming machine, minimize downtime, and ensure consistent and high-quality production.
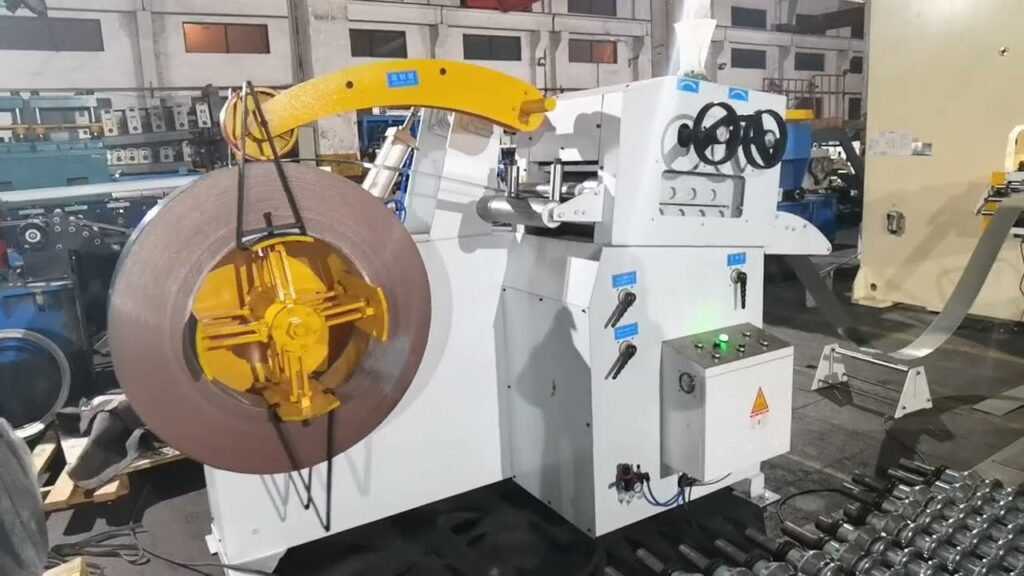
Common Issues and Troubleshooting
While C purlin roll forming machines are designed for reliable operation, occasional issues may arise. Here are some common problems and possible troubleshooting steps:
- Uneven Profile: If the formed C purlin exhibits variations in width or height, check for misalignment or damage to the rollers. Adjust or replace the affected rollers to ensure uniform profile dimensions.
- Material Jamming: If the metal strip gets stuck or jams during the roll forming process, inspect the material feeding system for obstructions or misalignment. Clear any debris or adjust the tension to allow smooth material flow.
- Inaccurate Hole Patterns: If the punched holes on the C purlin are not aligned or have irregular shapes, examine the punching mechanism and dies. Ensure that the punching mechanism is properly calibrated and the dies are in good condition.
- Cutting Issues: If the cut purlins have rough edges, uneven lengths, or inconsistent angles, check the cutting mechanism and blades. Sharpen or replace the blades as necessary and ensure proper alignment of the cutting components.
- Electrical Malfunctions: If the machine experiences electrical issues, such as power fluctuations or control panel errors, consult the machine’s manual and contact a qualified technician to diagnose and repair the electrical system.
Always follow the manufacturer’s guidelines for troubleshooting and seek professional assistance if needed to address complex issues and ensure the safe and efficient operation of your C purlin roll forming machine.
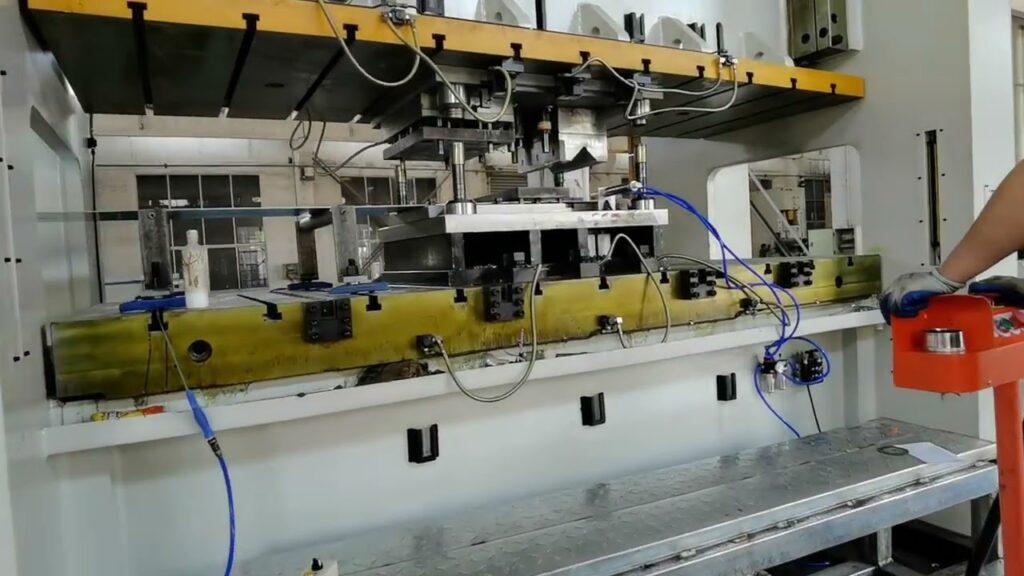
Top Manufacturers of C Purlin Roll Forming Machines
When considering the purchase of a C purlin roll forming machine, it is important to choose a reliable and reputable manufacturer. Here are some top manufacturers known for their quality roll forming machines:
- SUNWAY : WUXI SUNWAY MACHINERY CO., LTD is a professional manufacturer and exporter that are concerned with the design, development and production of cold roll forming machines.
- Samco Machinery: Samco Machinery is a renowned manufacturer of roll forming machines, including C purlin roll formers. They provide customizable solutions to meet specific production requirements.
- Formtek: Formtek offers a variety of roll forming machines, including C purlin roll formers. They are known for their innovative designs, robust construction, and reliable performance.
- Zhangjiagang City Saibo Science & Technology Co., Ltd.: Saibo is a leading manufacturer of roll forming machines, including C purlin roll formers. They offer a range of models with advanced features and precise profile accuracy.
- Hangzhou Zhongyuan Machinery Factory: Zhong yuan Machinery Factory is a reputable manufacturer known for its C purlin roll forming machines. They provide high-quality machines that offer efficiency, flexibility, and consistent production results.
When considering a specific manufacturer, it is important to evaluate their reputation, customer reviews, after-sales support, and the specific features and capabilities of their C purlin roll forming machines.
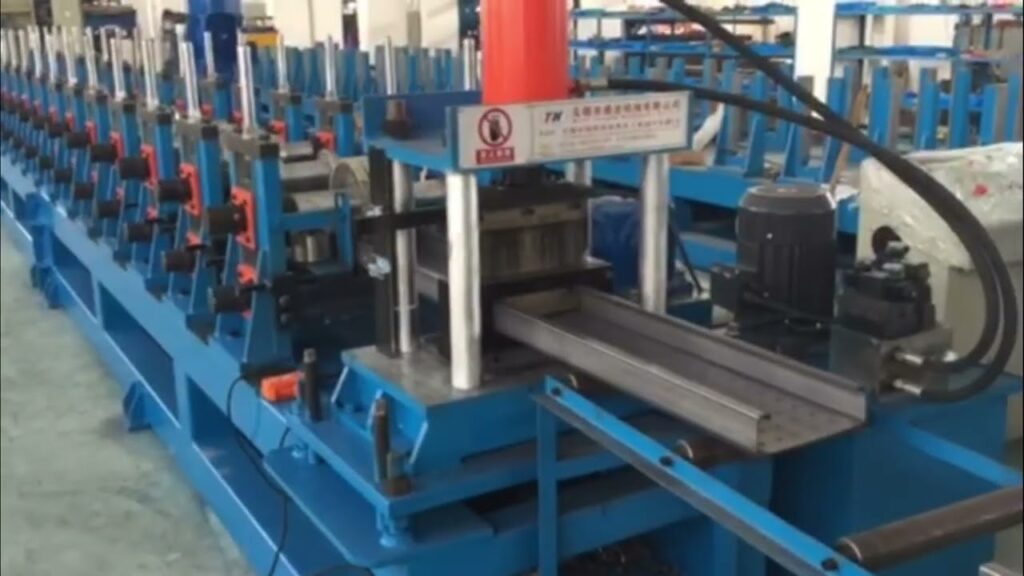
Cost and Investment Considerations
The cost of a C purlin roll forming machine can vary based on factors such as machine size, features, automation level, and brand reputation. It is important to consider the following cost and investment considerations:
- Machine Price: The price of a C purlin roll forming machine can range from several thousand dollars for small-scale machines to hundreds of thousands of dollars for high-capacity, fully automated systems.
- Operating Expenses: Consider the ongoing operating expenses, including energy consumption, maintenance costs, tooling replacement, and material waste. Efficient machines with lower maintenance requirements can result in cost savings over time.
- Return on Investment (ROI): Assess the potential ROI based on increased production efficiency, labor savings, reduced material waste, and the overall cost-effectiveness of the machine. Consider the payback period and long-term profitability.
- Financing Options: Explore financing options provided by manufacturers or financial institutions to ease the upfront investment. Evaluate the terms, interest rates, and repayment plans to determine the most suitable financing arrangement.
- Manufacturer Support: Consider the level of after-sales support provided by the manufacturer, including warranty, technical assistance, spare parts availability, and training opportunities. Reliable support can contribute to smooth machine operation and minimize downtime.
When making a decision, it is crucial to balance the initial investment with the long-term benefits and the specific requirements of your production needs. Consulting with multiple manufacturers, conducting cost comparisons, and thoroughly evaluating the features and capabilities of the machines will help in making an informed investment decision.
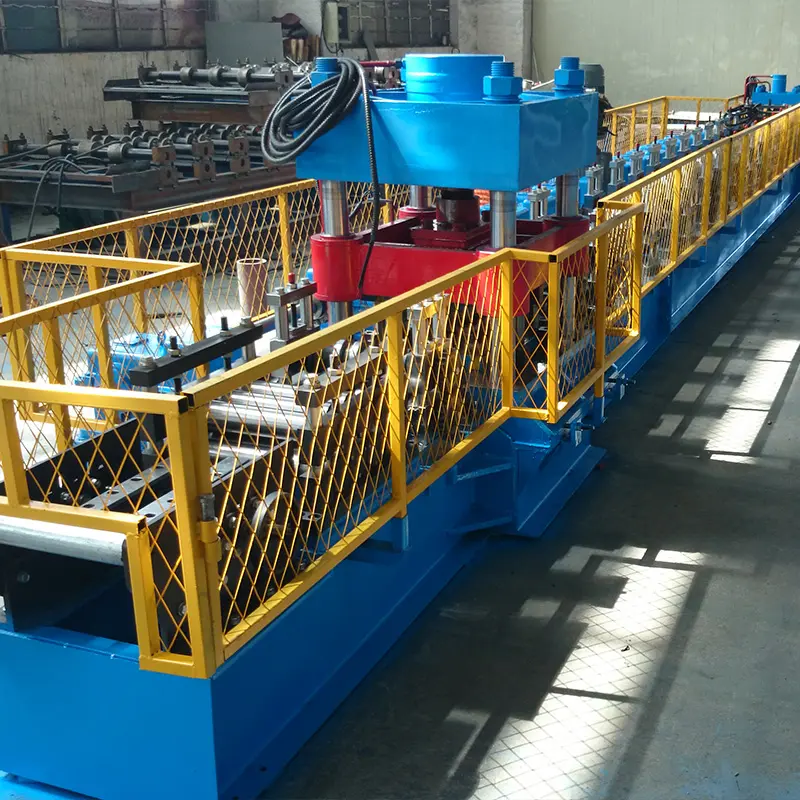
Conclusion
C purlin roll forming machines play a vital role in the efficient and precise production of C purlins, which are essential structural components in the construction industry. These machines offer numerous benefits, including increased production efficiency, consistent quality, flexibility, cost savings, and enhanced strength.
By understanding the key features, working principles, applications, and maintenance requirements of C purlin roll forming machines, you can make an informed decision when selecting the right machine for your needs. Consider factors such as production capacity, material compatibility, profile flexibility, automation level, and overall investment cost to ensure a successful and cost-effective implementation.
Investing in a reliable C purlin roll forming machine from a reputable manufacturer can significantly improve your production process, optimize resource utilization, and enhance the overall quality and reliability of your structural components.
FAQs (Frequently Asked Questions)
1. Q: Are C purlin roll forming machines suitable for small-scale production?
A: Yes, there are compact and versatile C purlin roll forming machines available that are suitable for small-scale production.
2. Q: Can C purlin roll forming machines produce purlins of different sizes and profiles?
A: Yes, adjustable C purlin roll forming machines allow for easy customization of purlin sizes, heights, hole patterns, and profiles to meet specific project requirements.
3. Q: What are the advantages of using C purlins in construction?
A: C purlins offer advantages such as high strength, cost-effectiveness, flexibility in design, and efficient load-bearing capabilities, making them ideal for various construction applications.
4. Q: How can I ensure the longevity and optimal performance of my C purlin roll forming machine?
A: Regular maintenance, including lubrication, cleaning, inspection, and adherence to safety protocols, is crucial for the longevity and optimal performance of your C purlin roll forming machine.
5. Q: Are C purlins suitable for both residential and commercial construction projects?
A: Yes, C purlins are widely used in both residential and commercial construction projects due to their strength, versatility, and cost-effectiveness in providing structural support.