Purlins are an essential component of any roofing or construction project. They provide structural support to the roof or wall cladding and transfer loads to the primary structure. However, the manufacturing process of purlins can be time-consuming and labor-intensive. This is where purlin roll forming comes into play. By using this technology, manufacturers can produce purlins at a faster rate, with higher accuracy, and lower labor costs. In this post, we will discuss the importance of purlin roll forming in roofing and construction, and why it has become a vital aspect of the manufacturing process for purlins.
what purlins are?
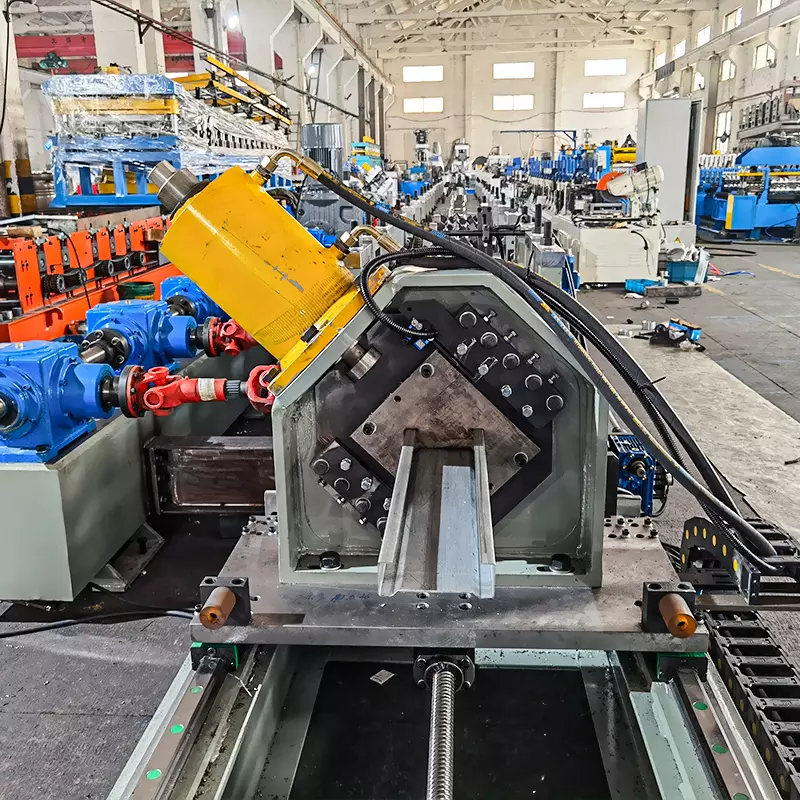
Purlins are horizontal structural members that play a crucial role in the stability and strength of roofing and wall systems in construction. They are commonly used to support the roof or wall cladding and transfer loads to the primary structure, which is typically the building’s frame or other load-bearing components. Without purlins, the weight of the roof or wall cladding would be too heavy for the structure to bear, resulting in collapse or damage to the building.
Purlins are available in a range of materials, including wood, steel, and aluminum, with steel being the most commonly used material in commercial and industrial construction. The choice of material is dependent on factors such as the design loads, environmental conditions, and building codes. Purlins are typically installed parallel to each other and perpendicular to the primary structure.
Overall, purlins are a vital component in roofing and construction, providing essential support and stability to ensure the safety and longevity of a building’s structure.
Benefits of purlin roll forming
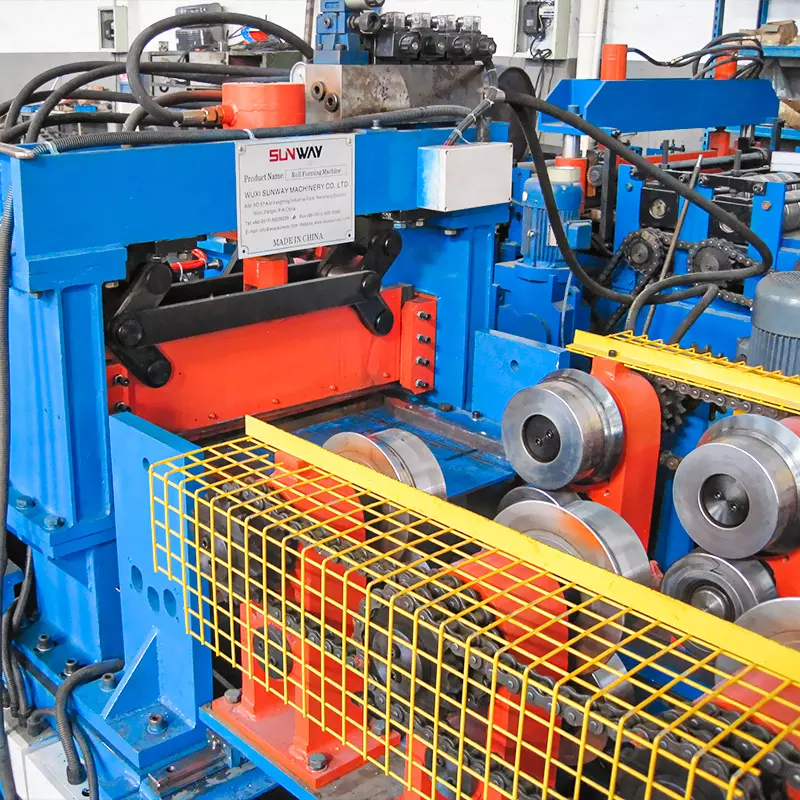
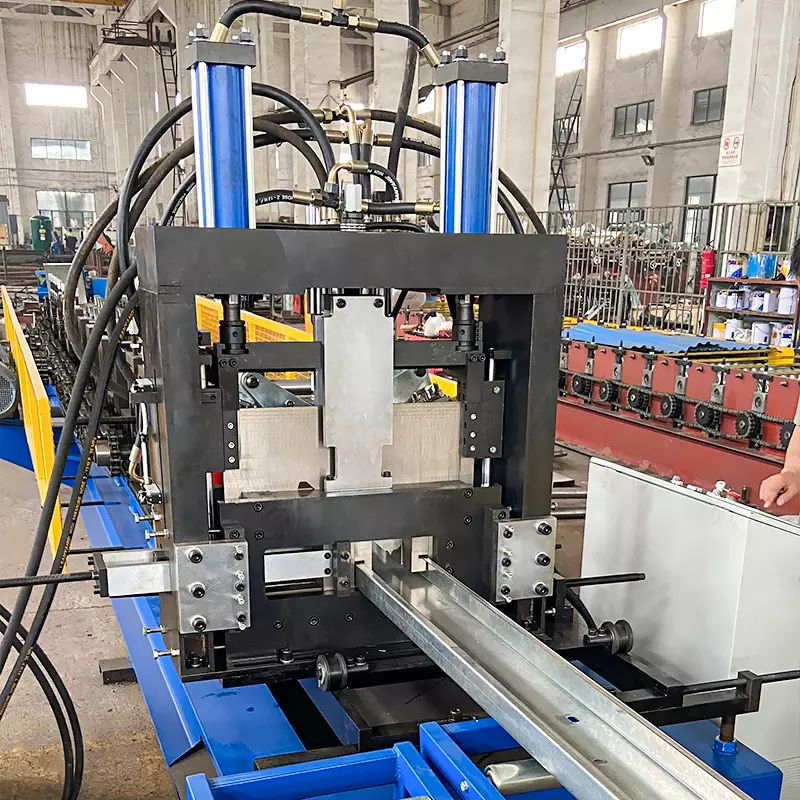
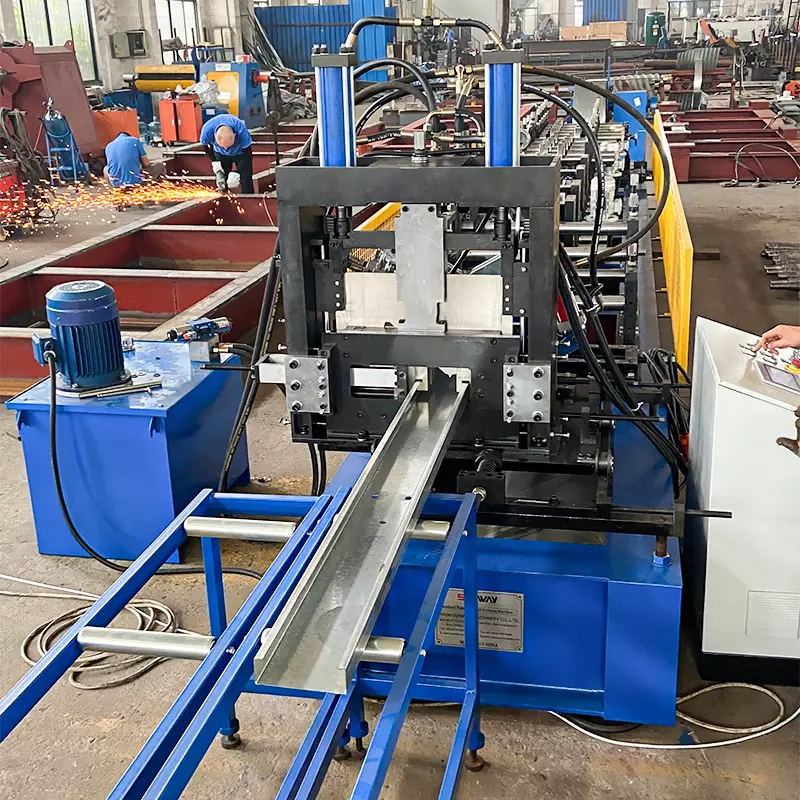
One of the significant advantages of using purlin roll forming for the manufacturing process is the faster production time. With the use of computer-controlled machines, purlin roll forming can produce a high volume of purlins in a short period. This method eliminates the need for manual labor, which means manufacturers can produce purlins more efficiently and with greater consistency.
Another benefit of purlin roll forming is the lower labor costs associated with the manufacturing process. As the process is automated, fewer workers are required to operate the machinery, resulting in lower labor costs. This cost-saving factor can lead to a more competitive price point for purlins, making them a more cost-effective option for builders and contractors.
Purlin roll forming also offers increased accuracy in measurements compared to traditional manufacturing methods. The computer-controlled machines used in the roll forming process ensure that each purlin produced is of the same precise length and shape. This accuracy means that the purlins can be quickly and easily installed on-site, reducing the risk of errors or rework.
In summary, the benefits of purlin roll forming are faster production times, lower labor costs, and increased accuracy in measurements. These advantages make it a popular choice for manufacturers in the construction industry, providing a reliable and efficient way to produce purlins for various construction applications.
Types of purlins
There are various types of purlins used in construction and roofing applications. Here are three common types of purlins and their unique features and benefits:
- Z-purlins: Z-purlins are named after their shape, which resembles the letter “Z.” These purlins have a high strength-to-weight ratio, making them an excellent choice for large buildings or structures with heavy loads. Z-purlins are also highly resistant to bending and twisting, providing exceptional structural stability. Additionally, Z-purlins are easy to install and are available in a range of thicknesses, making them versatile and suitable for a wide range of applications.
- C-purlins: C-purlins have a shape that resembles the letter “C.” These purlins are commonly used in industrial and commercial applications due to their high load-bearing capacity. C-purlins are an economical choice, as they require less material than Z-purlins but still provide reliable support. Additionally, they are easy to install and can be used in a variety of roofing and cladding systems.
- Sigma purlins: Sigma purlins are similar in shape to C-purlins but have a slight curve, giving them a unique appearance. They are often used in curved roofs or where a particular aesthetic is desired. Sigma purlins are highly versatile and can be used in various applications due to their high strength-to-weight ratio. They are also highly resistant to corrosion, making them a popular choice in coastal areas or other environments where rust and decay are a concern.
In conclusion, Z-purlins, C-purlins, and Sigma purlins are the most commonly used types of purlins in construction and roofing applications. Each type has its unique features and benefits, making them suitable for different applications depending on the load-bearing requirements, design, and aesthetic preferences. It is essential to choose the appropriate type of purlin for each project to ensure the stability, durability, and safety of the structure.
Applications of purlin roll forming
Purlin roll forming has a wide range of applications in the construction industry. Here are some examples:
- Roofing and Cladding: Purlin roll forming machines are commonly used to manufacture purlins that are used in roofing and cladding systems. These purlins provide essential support for the roofing or cladding material, and the roll-forming process ensures that they are produced accurately and efficiently.
- Prefabricated Buildings: Purlin roll forming machines are also used to produce purlins for prefabricated buildings. The roll-forming process allows for the quick and accurate production of purlins, which are then shipped to the construction site for assembly.
- Industrial and Commercial Buildings: Purlin roll forming machines are often used in the construction of industrial and commercial buildings. These buildings require large, sturdy purlins to support the heavy loads associated with their use. The roll-forming process ensures that the purlins are produced quickly and accurately, allowing for efficient construction of these types of buildings.
- Infrastructure: Purlin roll forming machines can also be used to produce purlins for infrastructure projects, such as bridges and tunnels. These structures require durable, lightweight purlins that can withstand harsh environmental conditions. The roll-forming process allows for the production of high-quality purlins that meet the necessary strength and durability requirements.
- Residential Homes: Purlin roll forming machines are also used to produce purlins for residential homes, particularly for larger homes with sloping or vaulted roofs. The roll-forming process allows for the efficient production of purlins that provide reliable support for the roof and walls, allowing for more open floor plans and larger spans.
Overall, purlin roll forming has a wide range of applications in the construction industry, providing a reliable and efficient way to produce purlins for various construction applications.
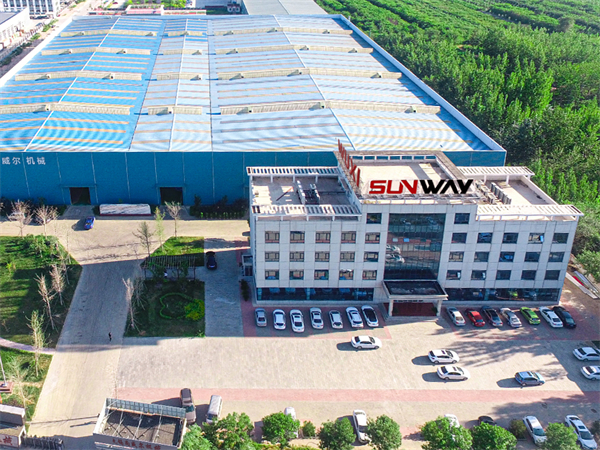
In summary, Purlin roll forming has revolutionized the production of purlins in roofing and construction. With faster production times, lower labor costs, and increased accuracy, purlin roll forming has become a popular choice for manufacturers in the industry. Purlins are critical in providing structural support and stability to roofing and wall systems in various construction applications, including agricultural, commercial, and residential buildings, as well as infrastructure projects. By understanding the different types of purlins available and their unique features and benefits, builders and contractors can select the appropriate purlins for each project, ensuring the stability, durability, and safety of the structure.