Introduction
Roofing is an integral part of any construction project, and the demand for high-quality roofing materials continues to grow. To meet this demand efficiently, the roofing industry has embraced advanced manufacturing technologies, including the use of Roofing Sheet Roll Forming Machines.
What is a Roofing Sheet Roll Forming Machine?
A Roofing Sheet Roll Forming Machine is a specialized piece of equipment designed to convert metal coils into continuous roofing sheets of various profiles and shapes. The process involves feeding metal coils into the machine, which then goes through a series of rollers to form the desired roofing profile.
How Does a Roofing Sheet Roll Forming Machine Work?
The working principle of a Roofing Sheet Roll Forming Machine is based on continuous bending and shaping of metal sheets. The machine consists of a series of rollers that progressively shape the metal as it passes through them. The sheet is cut to the required length, and the process is repeated for the next sheet.
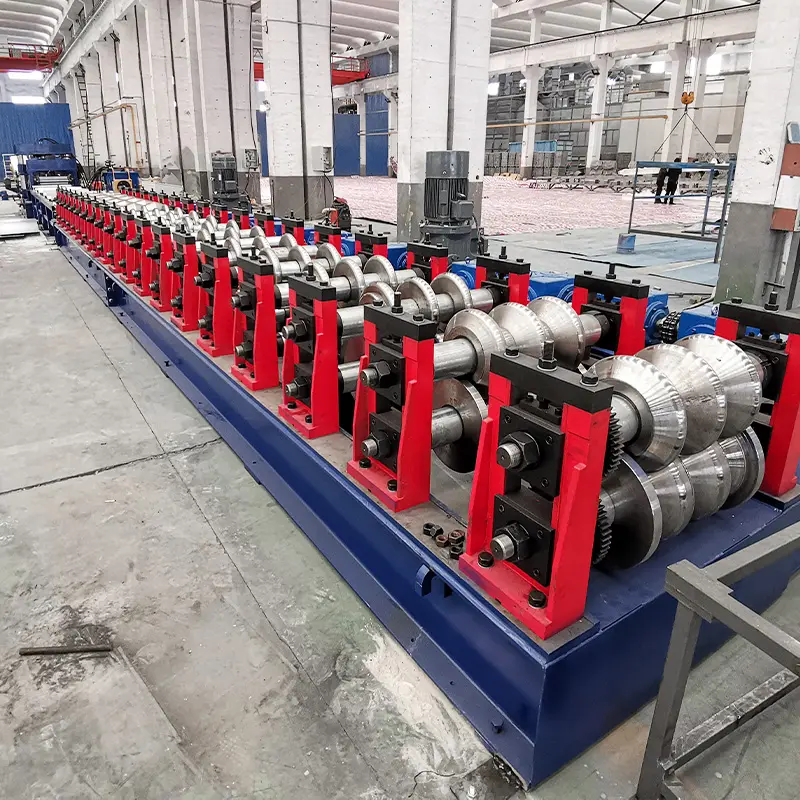
Types of Roofing Sheet Roll Forming Machines
There are several types of Roofing Sheet Roll Forming Machines available, each catering to specific roofing profiles and requirements:
Single Roofing Sheet Roll Forming Machine
The single roofing sheet roll forming machine produces a single type of roofing profile at a time. It is ideal for manufacturers focusing on one specific design.
Double Layer Roofing Sheet Roll Forming Machine
The double layer machine can produce two different roofing profiles, offering more versatility for manufacturers with varied product offerings.
Corrugated Roofing Sheet Roll Forming Machine
The corrugated roofing sheet machine creates the iconic wavy pattern and is commonly used in residential and agricultural roofing.
Standing Seam Roofing Sheet Roll Forming Machine
The standing seam machine produces roofing with raised seams, providing a sleek and modern appearance often used in commercial buildings.
Advantages of Using a Roofing Sheet Roll Forming Machine
Using a Roofing Sheet Roll Forming Machine offers several advantages:
Cost-Effective Production
Roll forming allows for continuous and high-speed production, reducing labor costs and increasing overall efficiency.
Customization Options
Manufacturers can easily adjust the machine to produce different roofing profiles, catering to specific customer needs.
High Efficiency and Productivity
The automated nature of roll forming machines ensures consistent and precise results, leading to higher productivity.
Reduced Material Waste
Roll forming minimizes material waste compared to traditional roofing manufacturing methods.
Durability and Consistency
Roofing sheets produced by roll forming are uniform and durable, providing long-lasting and reliable roofing solutions.
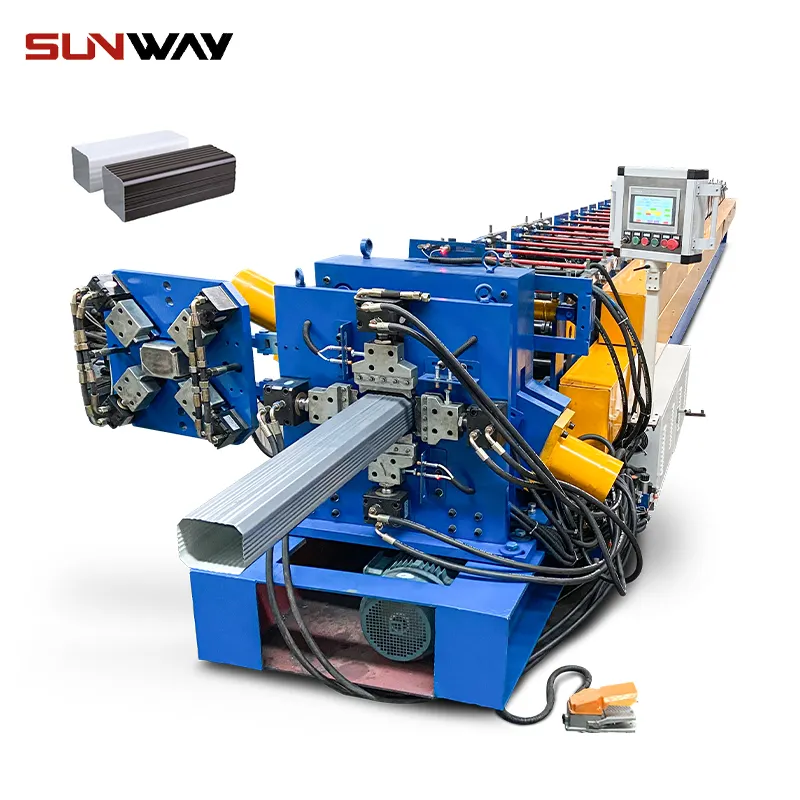
Factors to Consider When Choosing a Roofing Sheet Roll Forming Machine
Before investing in a Roofing Sheet Roll Forming Machine, several factors should be taken into consideration:
Material Compatibility
Ensure that the machine is compatible with the type and thickness of metal you intend to use.
Production Speed
Consider the production speed of the machine to meet your required output.
Profile Design Flexibility
Choose a machine that allows flexibility in creating various roofing profiles.
Machine Size and Space Requirements
Ensure that the machine fits your available workspace and can be installed without issues.
Automation and Control System
Check the level of automation and the ease of controlling the machine for efficient operations.
Maintenance and Care of Roofing Sheet Roll Forming Machines
To ensure the longevity and optimal performance of your Roofing Sheet Roll Forming Machine, regular maintenance is crucial:
Regular Cleaning and Lubrication
Clean the machine regularly to remove debris and dust that can affect its performance. Lubricate moving parts to reduce friction and prevent wear.
Inspection and Replacement of Parts
Inspect the machine periodically for any signs of wear or damage. Replace worn-out or damaged parts promptly to avoid breakdowns.
Training and Skill Development
Train your operators on proper machine operation and maintenance to minimize errors and accidents.
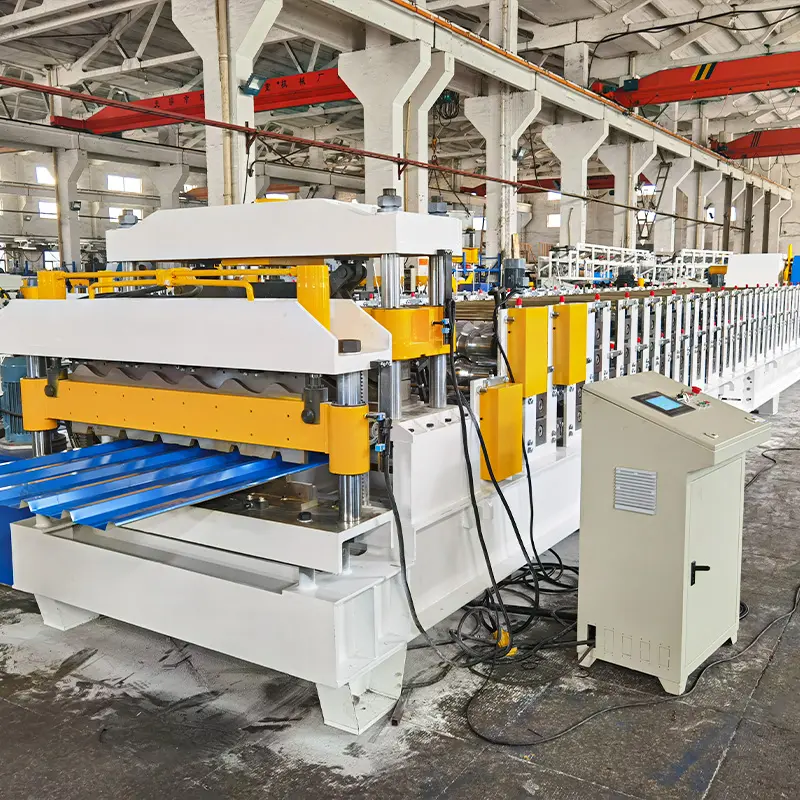
How to Maximize the Efficiency of Your Roofing Sheet Roll Forming Machine?
To get the most out of your Roofing Sheet Roll Forming Machine, consider these strategies:
Optimize Material Handling
Efficient material handling and storage can streamline the production process and reduce downtime.
Regular Equipment Maintenance
Scheduled maintenance and servicing prevent unexpected breakdowns and optimize performance.
Operator Training and Skill Improvement
Invest in training your operators to enhance their proficiency and understanding of the machine.
Continuous Process Improvement
Analyze production data and identify areas for improvement to increase overall efficiency.
Safety Precautions When Using Roofing Sheet Roll Forming Machines
Safety should be a top priority when working with any industrial machinery, including Roofing Sheet Roll Forming Machines:
Proper Training and Certification
Ensure that all operators are adequately trained and certified to operate the machine.
Machine Guarding and Safety Features
Install safety guards and features on the machine to prevent accidents and injuries.
Personal Protective Equipment (PPE)
Require operators to wear appropriate PPE, such as safety goggles and gloves, while working with the machine.
Emergency Stop Protocols
Establish clear procedures for emergency situations, and ensure all operators are familiar with them.
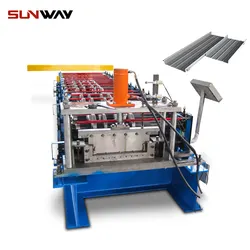
Future Trends in Roofing Sheet Roll Forming Technology
The roofing industry continues to evolve, and several trends are shaping the future of Roofing Sheet Roll Forming Machines:
Advanced Materials and Coatings
Incorporating advanced materials and coatings can enhance the durability and performance of roofing sheets.
Integration of AI and Automation
AI-powered automation can optimize machine operation and increase productivity.
Sustainability and Green Roofing Solutions
With a growing focus on sustainability, roofing manufacturers are exploring eco-friendly materials and production methods.
Applications of Roofing Sheet Roll Forming Machines
Roofing Sheet Roll Forming Machines find applications in various sectors:
Residential Roofing
The machines are widely used to produce roofing sheets for residential buildings, including houses and apartments.
Commercial and Industrial Roofing
Many commercial and industrial structures use roofing sheets produced by roll forming machines due to their efficiency and durability.
Agricultural Roofing
Agricultural buildings, such as barns and storage facilities, often utilize roofing sheets made by roll forming machines.
Tips for Buying a Roofing Sheet Roll Forming Machine
When purchasing a Roofing Sheet Roll Forming Machine, consider these tips to make an informed decision:
Research and Compare Different Brands
Research various manufacturers and compare their machines’ features, prices, and customer reviews.
Check Customer Reviews and Testimonials
Reading feedback from existing customers can provide valuable insights into the machine’s performance and reliability.
Request Machine Demonstrations
If possible, request a live demonstration of the machine to see it in action and assess its capabilities.
Consider After-Sales Support and Warranty
Ensure that the manufacturer provides excellent after-sales support and a comprehensive warranty for the machine.
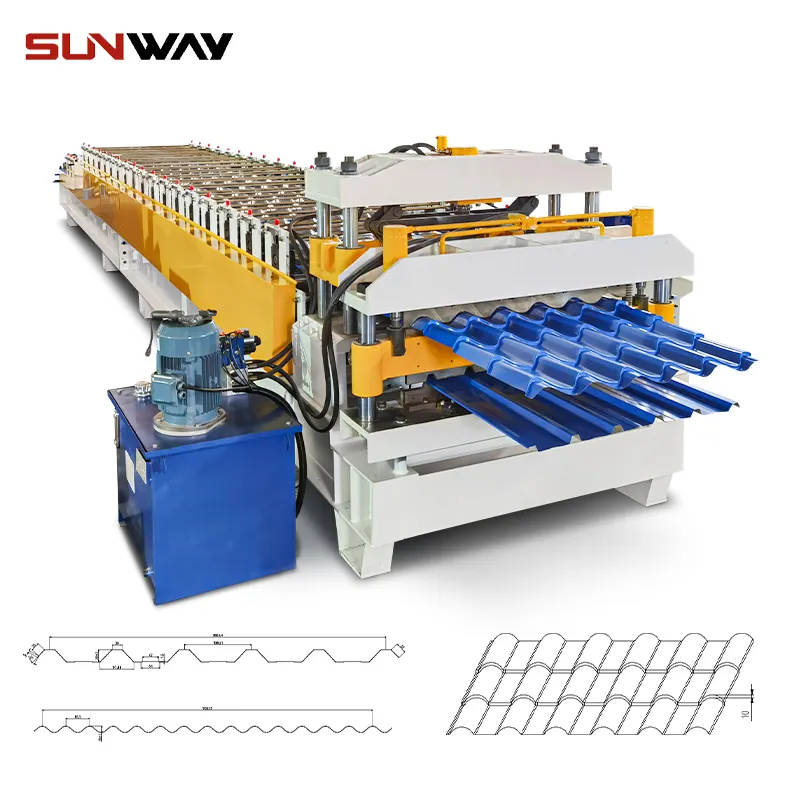
Conclusion
Roofing Sheet Roll Forming Machines have revolutionized the roofing industry, offering efficient, cost-effective, and durable solutions for various roofing needs. These machines provide manufacturers with the flexibility to produce different roofing profiles while minimizing material waste and ensuring consistent quality. By following safety protocols and maintaining the machines properly, manufacturers can maximize their efficiency and productivity. As the roofing industry continues to advance, embracing the latest technologies and trends will be crucial for staying competitive and meeting the demands of the market.
FAQs
What is the typical production speed of a roofing sheet roll forming machine?
The production speed of a roofing sheet roll forming machine can vary depending on the machine’s design and complexity. Generally, these machines can produce roofing sheets at speeds ranging from 10 to 60 meters per minute.
Can a roofing sheet roll forming machine produce different profiles?
Yes, most modern roofing sheet roll forming machines are designed to produce various roofing profiles. By adjusting the machine settings and tooling, manufacturers can switch between different profiles easily.
Is it necessary to have prior experience to operate the machine?
While prior experience in manufacturing or metalworking can be beneficial, many roofing sheet roll forming machines come with user-friendly interfaces and training materials. With proper training and guidance, operators can quickly learn to operate the machine effectively.
How long does it take to learn the basics of using the machine?
Learning the basics of operating a roofing sheet roll forming machine typically takes a few days to a few weeks, depending on the complexity of the machine and the operator’s familiarity with similar equipment.
Can a roofing sheet roll forming machine work with stainless steel materials?
Yes, roofing sheet roll forming machines can work with various materials, including stainless steel. However, the machine’s specifications and tooling may need adjustments to handle different materials effectively.