Introduction
In the world of manufacturing and construction, efficiency and precision are paramount. One of the technologies that have significantly contributed to achieving these goals is the Beam Roll Forming Machine. This remarkable piece of equipment has revolutionized the way structural components are produced, making the process faster, more cost-effective, and highly customizable.
Understanding Beam Roll Forming Machines
At its core, a Beam Roll Forming Machine is a specialized piece of machinery used to shape metal sheets into various cross-sectional profiles, particularly those resembling beams. This process involves feeding a continuous strip of metal through multiple sets of rollers, each designed to gradually bend and shape the metal until it matches the desired profile. The result is a precisely formed beam that maintains uniform dimensions throughout its length.
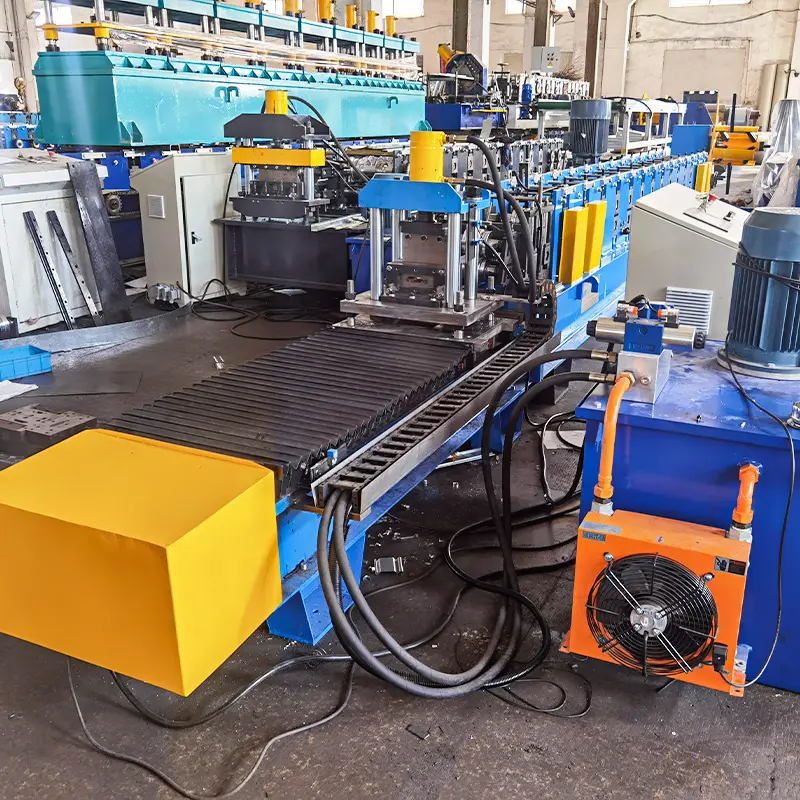
Advantages of Beam Roll Forming Machines
Beam Roll Forming Machines offer a range of advantages that have positioned them as a preferred choice in the manufacturing and construction industries. Some of these advantages include:
- High Efficiency: The continuous and automated nature of the roll forming process allows for high-speed production, ensuring a steady output of beams.
- Cost-Effectiveness: Traditional methods of beam production can be labor-intensive and time-consuming. Beam roll forming machines reduce labor costs and minimize material waste.
- Design Flexibility: These machines can create a wide array of beam profiles, catering to diverse project requirements.
- Consistency and Precision: The automated process guarantees uniformity in the dimensions and shape of each beam produced.
Types of Beam Roll Forming Machines
There are several types of Beam Roll Forming Machines, each catering to specific beam profiles and production volumes:
- Single Stand Machines: Ideal for producing a limited range of beam profiles and suitable for lower production volumes.
- Duplex Stand Machines: These machines have two sets of rollers, allowing for the production of a broader range of beam profiles.
- Multi-Stand Machines: Equipped with multiple sets of rollers, these machines offer extensive design versatility and are suitable for high-volume production.
Key Components and Working Principle
A typical Beam Roll Forming Machine consists of the following key components:
- Uncoiler: This component holds the coil of metal that will be fed into the machine.
- Rollers: The heart of the machine, these rollers gradually shape the metal as it passes through them.
- Gears and Transmission: These components ensure synchronized movement of the rollers and accurate shaping of the beam.
- Cut-off System: Some machines come with an integrated cutting mechanism to produce beams of specific lengths.
The working principle involves feeding the metal coil through the machine’s rollers, with each set of rollers performing a specific bending action. The rollers work progressively, with the final set producing the desired beam shape.
Applications of Beam Roll Forming Machines
Beam Roll Forming Machines find application in various industries, including:
- Construction: They are used to manufacture beams for structural frameworks in buildings and bridges.
- Automotive: These machines produce beams used in the chassis and framework of vehicles.
- Storage Systems: Beam roll forming machines create beams for shelves and storage racks.
- Infrastructure: They contribute to the production of beams used in infrastructure projects like railways and highways.
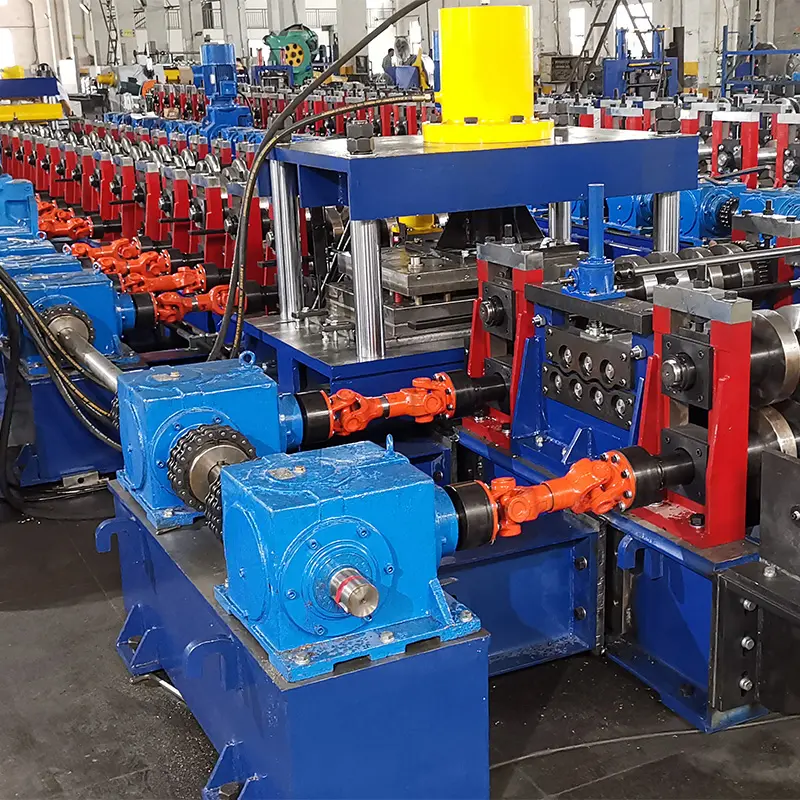
Factors to Consider When Choosing a Beam Roll Forming Machine
When selecting a beam roll forming machine, several factors come into play:
- Required Beam Profile: Choose a machine that can produce the specific beam profiles needed for your projects.
- Production Volume: Consider the volume of beams you need to produce; this will determine the machine’s size and capacity.
- Material Compatibility: Ensure the machine can work with the type and thickness of metal you intend to use.
- Automation Level: Decide between semi-automated and fully automated machines based on your production requirements.
Maintenance and Care Tips
To ensure the longevity and optimal performance of your beam roll forming machine, follow these maintenance tips:
- Regularly lubricate moving parts to prevent friction-related wear.
- Inspect and replace worn-out rollers or components promptly.
- Keep the machine clean from metal shavings and debris to prevent damage.
Innovations in Beam Roll Forming Technology
The field of beam roll forming is continually evolving, with advancements such as:
- Digital Controls: Modern machines feature digital controls for precise adjustments, reducing setup time.
- Advanced Materials: Machines are being developed to accommodate a wider range of metals and alloys.
Future Trends in Beam Roll Forming
As technology progresses, several trends are likely to shape the future of beam roll forming:
- Increased Automation: Expect further integration of automation for higher efficiency and reduced human intervention.
- Advanced Forming Simulation: Simulations will become more accurate, aiding in the design and optimization of complex beam profiles.
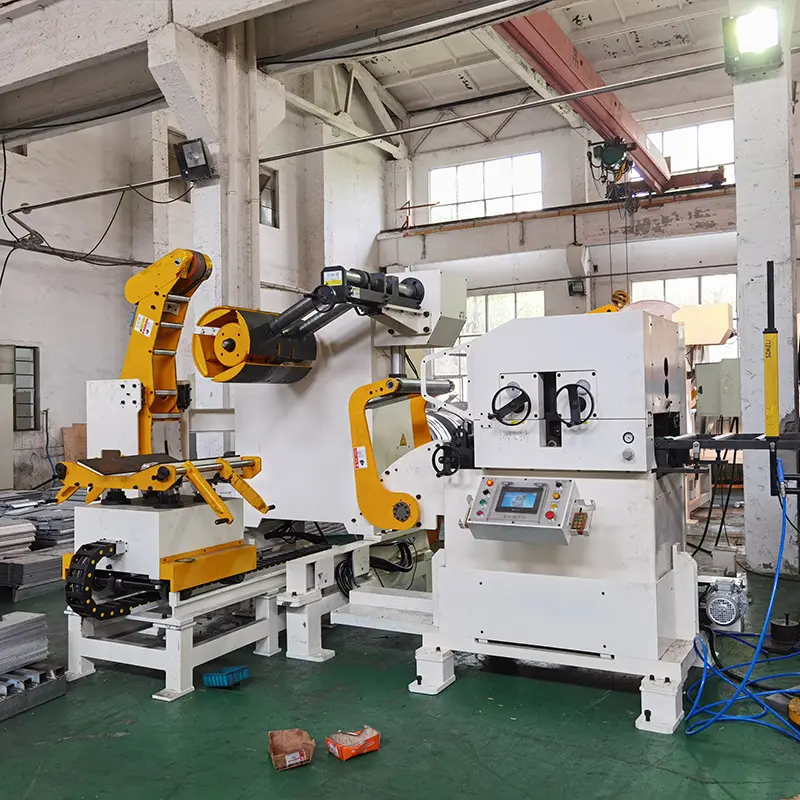
Conclusion
The beam roll forming machine has undoubtedly revolutionized the manufacturing and construction sectors. With its ability to produce precisely shaped beams efficiently and cost-effectively, it has become an indispensable tool for various industries. As technology continues to advance, we can only anticipate even more sophisticated and capable machines that will drive innovation and progress in structural component production.
FAQs
- What materials can be used with beam roll forming machines?Beam roll forming machines can work with a wide range of materials, including steel, aluminum, and even certain alloys.
- Are beam roll forming machines suitable for small-scale production?Yes, there are machines available that cater to small-scale production needs, offering flexibility and efficiency.
- Can custom beam profiles be created with these machines?Absolutely, one of the key advantages of beam roll forming machines is their ability to create custom and complex beam profiles.
- How does beam roll forming compare to traditional fabrication methods?Beam roll forming is more efficient, cost-effective, and produces consistent results compared to traditional fabrication methods.
- What safety measures should be taken when operating these machines?Operators should receive proper training, wear appropriate protective gear, and follow established safety protocols to prevent accidents during operation.