Introduction
Welcome to our comprehensive guide on sheet metal roll forming machines. In this article, we will explore the various aspects of these machines, including their working principles, benefits, applications, and more. Sheet metal roll forming machines play a crucial role in the manufacturing industry, enabling the efficient and cost-effective production of metal components with complex shapes and profiles. Whether you are new to roll forming or seeking to expand your knowledge, this article will provide you with valuable insights into this fascinating technology.
What is a Sheet Metal Roll Forming Machine?
A sheet metal roll forming machine is a specialized equipment used to shape and transform flat metal sheets into desired profiles or cross-sections. It utilizes a continuous bending process, where the metal sheet is gradually shaped by passing through a series of rollers. By carefully controlling the roller configurations and adjustments, manufacturers can produce a wide range of complex shapes and profiles with high precision and consistency.
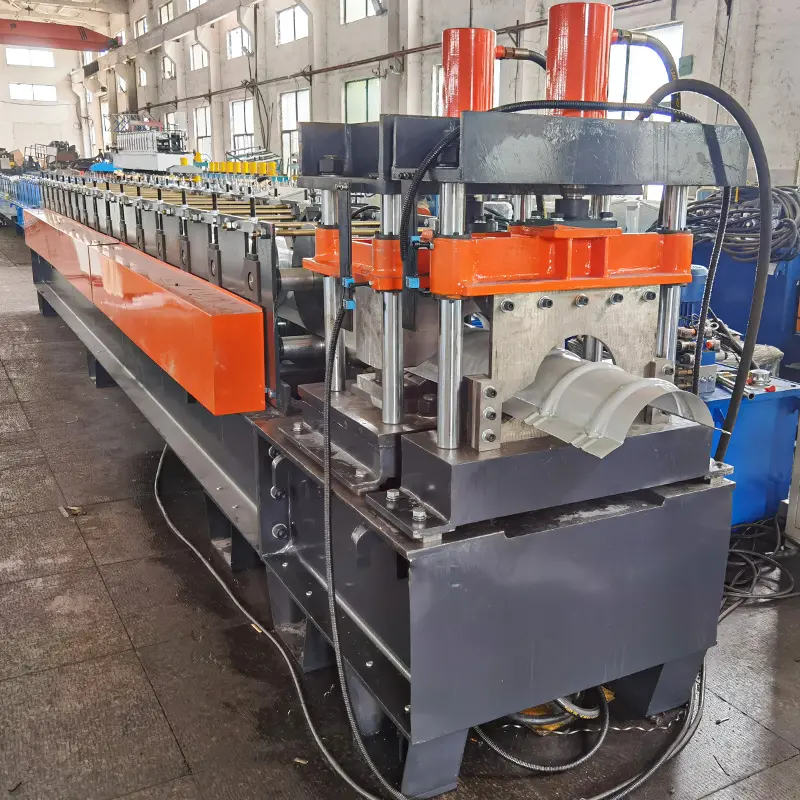
Benefits of Using a Sheet Metal Roll Forming Machine
3.1 Increased Efficiency and Productivity
One of the primary advantages of using a sheet metal roll forming machine is the significant increase in efficiency and productivity it offers. Unlike traditional fabrication methods that require multiple steps and operations, roll forming can produce finished parts in a continuous and automated manner. This eliminates the need for manual handling and reduces production time, resulting in higher output rates and improved overall efficiency.
3.2 Cost-Effective Manufacturing Process
Sheet metal roll forming is a cost-effective manufacturing process, especially for large-scale production. The automated nature of roll forming minimizes labor costs and reduces the dependency on skilled operators. Additionally, the process eliminates the need for secondary operations like welding or riveting, further reducing the overall production costs. By utilizing a sheet metal roll forming machine, manufacturers can achieve cost savings while maintaining high-quality output.
3.3 Versatile and Customizable Designs
Sheet metal roll forming machines offer immense versatility when it comes to designing and producing various shapes and profiles. The flexibility of the machine allows for customization according to specific project requirements. Whether it’s simple profiles or intricate designs, roll forming can handle a wide range of shapes and dimensions, enabling manufacturers to meet diverse customer demands.
3.4 Enhanced Material Strength and Durability
Roll forming not only shapes the metal but also improves its structural integrity. The continuous bending process imparts strength and durability to the metal, making it suitable for demanding applications. With precise control over the forming parameters, manufacturers can optimize the material properties and ensure consistent quality throughout the production process.
3.5 Reduced Waste and Environmental Impact
sheet metal roll forming machine is a highly efficient process that generates minimal waste compared to other fabrication methods. The precise shaping and bending of the metal sheet minimize material losses, resulting in less scrap. Additionally, roll forming machines can utilize recycled or pre-coated materials, further reducing the environmental impact and promoting sustainability.
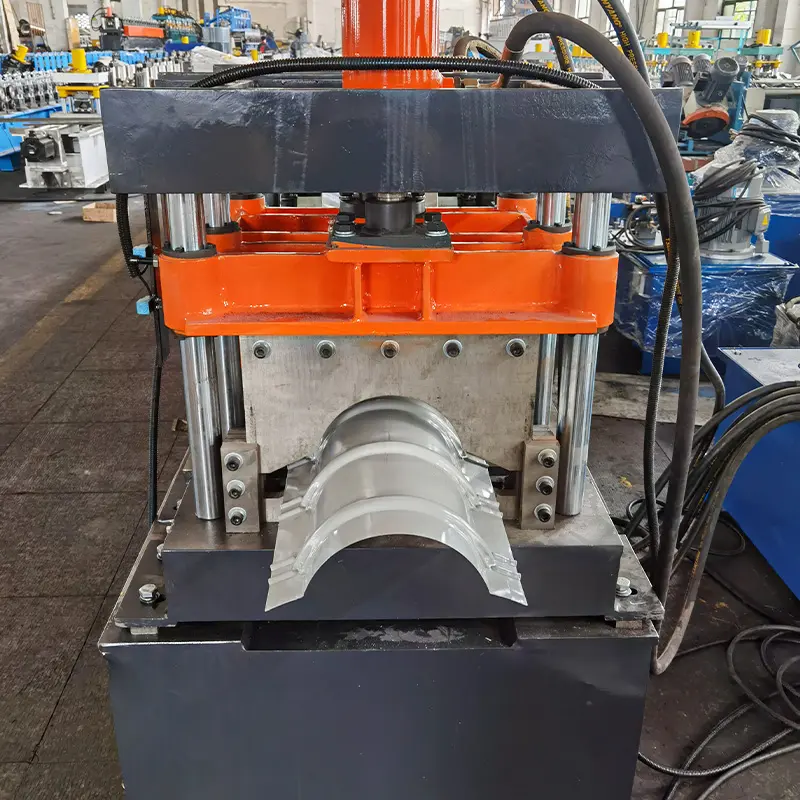
Different Types of Sheet Metal Roll Forming Machines
There are several types of sheet metal roll forming machines available, each designed for specific applications and production requirements. Let’s explore some of the common types:
4.1 Single-Side Roll Forming Machine
A single-side roll forming machine operates by bending the metal sheet from one side only. It is suitable for producing simple profiles with consistent cross-sections.
4.2 Double-Side Roll Forming Machine
A double-side roll forming machine can bend the metal sheet from both sides simultaneously. This allows for the production of more complex profiles with asymmetrical shapes.
4.3 Duplex Roll Forming Machine
A duplex roll forming machine consists of two roll forming units placed parallel to each other. It enables the simultaneous production of two different profiles, increasing productivity and reducing production time.
4.4 Automatic Roll Forming Machine
An automatic roll forming machine is equipped with advanced control systems that automate the entire production process. It eliminates the need for manual adjustments and enables high-speed and precise manufacturing.
4.5 CNC Roll Forming Machine
A CNC (Computer Numerical Control) roll forming machine is controlled by computer programs, offering enhanced precision and customization. It can produce complex profiles with intricate designs, meeting the most demanding specifications.
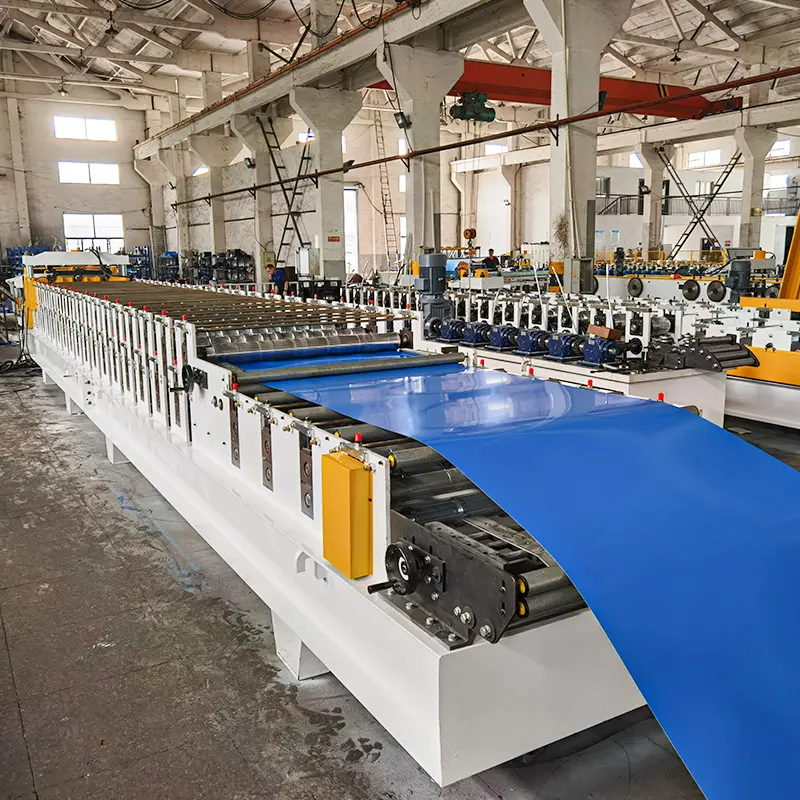
Key Components and Working Principles
A sheet metal roll forming machine consists of several key components that work together to shape the metal sheet. Let’s explore these components and their working principles:
5.1 Entry Section
The entry section of the sheet metal roll forming machine is where the metal sheet enters the machine for processing. It often includes a decoiler, which holds the coil of metal and feeds it into the machine. The decoiler unwinds the metal sheet and provides a continuous supply for the roll forming process.
5.2 Forming Section
The forming section is the heart of the roll forming machine, where the metal sheet undergoes shaping and bending. It consists of a series of rollers that gradually deform the sheet into the desired profile. The rollers are carefully positioned and can be adjusted to achieve the precise dimensions and shape of the profile.
5.3 Cutting Section
After the metal sheet is formed into the desired profile, the cutting section comes into play. This section incorporates cutting tools or shearing mechanisms that trim the profile to the required length. The cutting process is synchronized with the speed of the roll forming machine to ensure accurate and consistent cuts.
5.4 Exit Section
The exit section marks the end of the roll forming process. It includes mechanisms to support and collect the finished profiles as they are discharged from the machine. Depending on the production requirements, additional operations such as hole punching, embossing, or notching may be integrated into the exit section to add further features or functionality to the profiles.
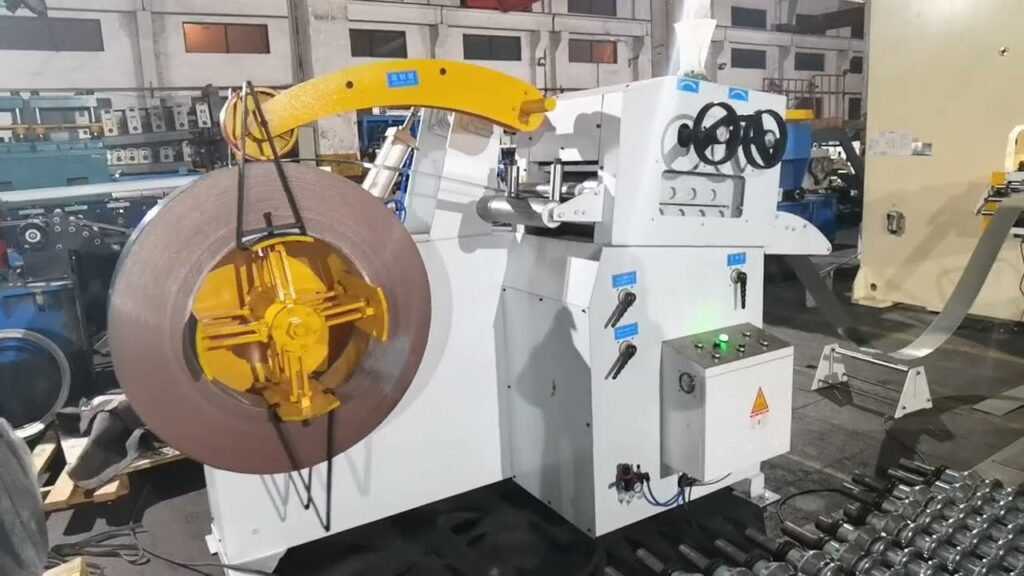
Applications of Sheet Metal Roll Forming Machines
Sheet metal roll forming machines find extensive applications across various industries. Let’s explore some of the key sectors where roll forming technology is commonly used:
6.1 Construction Industry
In the construction industry, sheet metal roll forming machines are utilized to produce components such as roofing panels, wall claddings, gutter systems, and framing profiles. The ability to create customized shapes and sizes makes roll forming ideal for construction projects that require precise and durable metal components.
6.2 Automotive Industry
Automotive manufacturers rely on sheet metal roll forming machines to produce a wide range of automotive parts, including body panels, chassis components, and structural reinforcements. The high-strength and consistent quality of roll-formed profiles contribute to the safety and performance of vehicles.
6.3 HVAC Industry
The HVAC (Heating, Ventilation, and Air Conditioning) industry extensively uses roll-formed components for ductwork, air distribution systems, and HVAC equipment enclosures. Roll forming enables the production of ducts with precise dimensions and intricate designs, ensuring efficient airflow and temperature control.
6.4 Furniture Industry
In the furniture industry, roll forming machines are employed to manufacture metal components for cabinets, shelving systems, desks, and chairs. The ability to create unique profiles and decorative designs adds aesthetic appeal and functionality to furniture products.
6.5 Electrical Industry
Sheet metal roll forming machines are widely used in the electrical industry to produce electrical enclosures, cable trays, and conduit systems. The accurate and consistent dimensions of roll-formed profiles ensure proper fit and protection for electrical equipment and wiring.
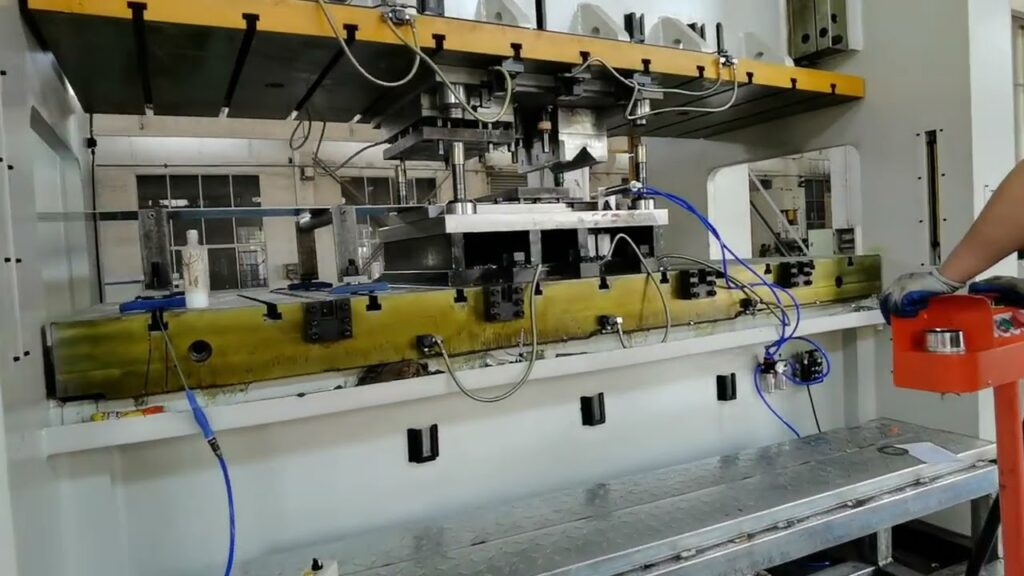
Factors to Consider When Choosing a Sheet Metal Roll Forming Machine
When selecting a sheet metal roll forming machine, several factors should be taken into consideration to ensure the best fit for your manufacturing needs. Here are some key factors to consider:
7.1 Material Thickness and Width
Different roll forming machines have varying capabilities regarding the maximum thickness and width of the metal sheets they can process. It is crucial to choose a machine that can handle the specific material dimensions required for your production.
7.2 Production Speed and Capacity
The production speed and capacity of a roll forming machine determine the output rate and overall efficiency of your manufacturing process. Consider the desired production volume and choose a machine that can meet your required speed and capacity specifications.
7.3 Machine Flexibility and Customization
Evaluate the flexibility of the roll forming machine in terms of its ability to produce a wide range of profiles and designs. Look for machines that offer easy tooling changes and adjustments to accommodate diverse product requirements.
7.4 Maintenance and Support
Consider the maintenance requirements of the roll forming machine and the availability of technical support from the manufacturer. Regular maintenance ensures optimal performance and longevity of the machine, while reliable support helps address any operational issues efficiently.
7.5 Cost and Return on Investment
Factor in the initial investment cost of the roll forming machine and assess the potential return on investment. Consider the long-term benefits, such as increased productivity, reduced labor costs, and improved product quality, to determine the machine’s overall value for your business.
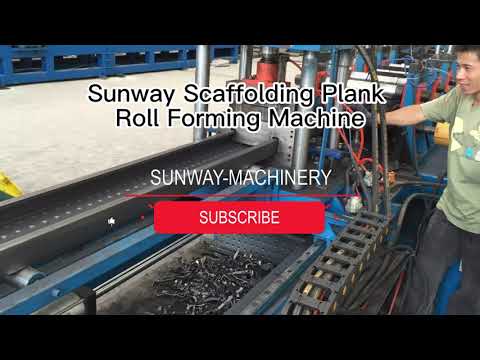
Common Challenges and Solutions in Sheet Metal Roll Forming
While sheet metal roll forming offers numerous advantages, it is essential to be aware of potential challenges that may arise during the process. Here are some common challenges and their solutions:
8.1 Material Defects and Inconsistencies
Sheet metal may contain defects or inconsistencies that can affect the quality of the roll-formed profiles. Proper material selection, quality control measures, and regular inspection can help minimize these issues.
8.2 Forming and Deformation Issues
Complex profiles or certain material properties may pose challenges in achieving the desired shape and avoiding deformation during the roll forming process. Careful design of the tooling and adjustments of the machine parameters can help overcome these challenges and ensure accurate forming.
8.3 Misalignment and Dimensional Accuracy
Misalignment of the metal sheet or inaccuracies in the roll forming machine setup can result in profiles with dimensional deviations. Regular calibration, precise alignment, and thorough quality checks can address these issues and maintain dimensional accuracy.
8.4 Tooling and Die Maintenance
Wear and tear of the roll forming tooling and dies can impact the quality of the profiles and the performance of the machine. Regular maintenance, including cleaning, lubrication, and replacement of worn components, is crucial to ensure consistent and efficient operation.
8.5 Quality Control and Inspection
Implementing a robust quality control system is essential to identify any defects or deviations in the roll-formed profiles. Regular inspections, dimensional checks, and adherence to quality standards can help maintain high product quality and customer satisfaction.
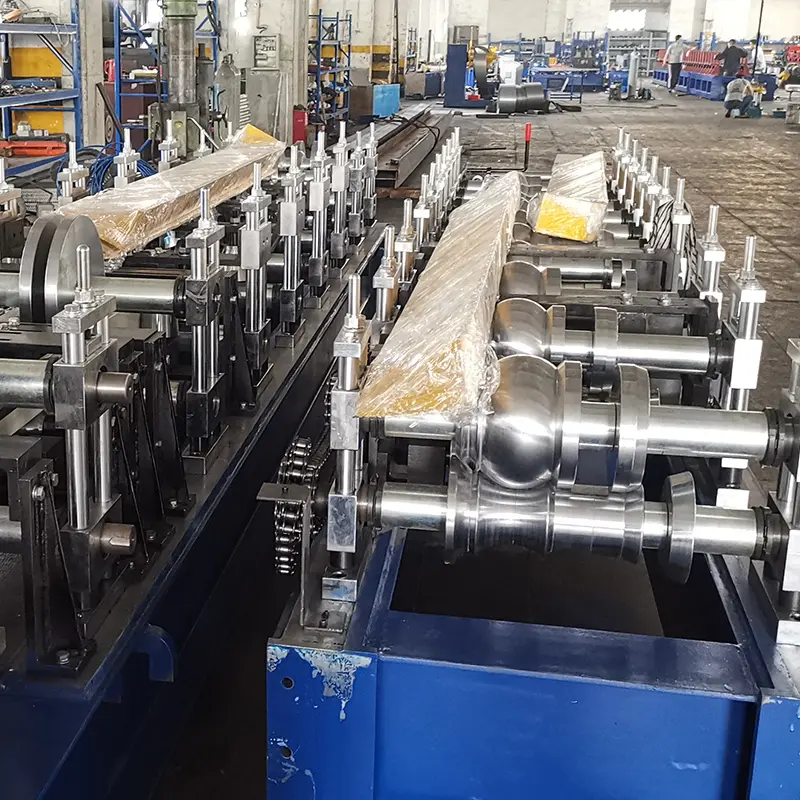
Future Trends in Sheet Metal Roll Forming Technology
The field of sheet metal roll forming continues to evolve, driven by technological advancements and industry demands. Here are some future trends to watch out for:
9.1 Advanced Automation and Robotics
Automation and robotics are increasingly being integrated into roll forming processes, enabling higher levels of precision, efficiency, and productivity. Automated material handling, robotic tooling changes, and real-time monitoring systems are becoming more prevalent in modern roll forming setups.
9.2 Integration with Industry 4.0 Technologies
Sheet metal roll forming machines are being connected to digital systems, leveraging the capabilities of Industry 4.0 technologies. Integration with data analytics, cloud-based platforms, and smart sensors allows for real-time monitoring, predictive maintenance, and improved process optimization.
9.3 Lightweight and Sustainable Materials
With the growing emphasis on sustainability, roll forming technology is adapting to incorporate lightweight and eco-friendly materials. This includes the use of high-strength alloys, composite materials, and recyclable substrates, promoting energy efficiency and reducing environmental impact.
9.4 Enhanced Precision and Quality Control
Advancements in sensors, measurement systems, and control algorithms enable enhanced precision and quality control in roll forming processes. Real-time monitoring of critical parameters, closed-loop feedback systems, and advanced inspection techniques contribute to improved product consistency and reduced wastage.
9.5 Improved Energy Efficiency
Efforts are being made to optimize energy consumption in sheet metal roll forming. This includes the development of energy-efficient drive systems, intelligent power management, and the utilization of renewable energy sources. Energy-saving measures not only reduce operational costs but also promote sustainability in the manufacturing industry.
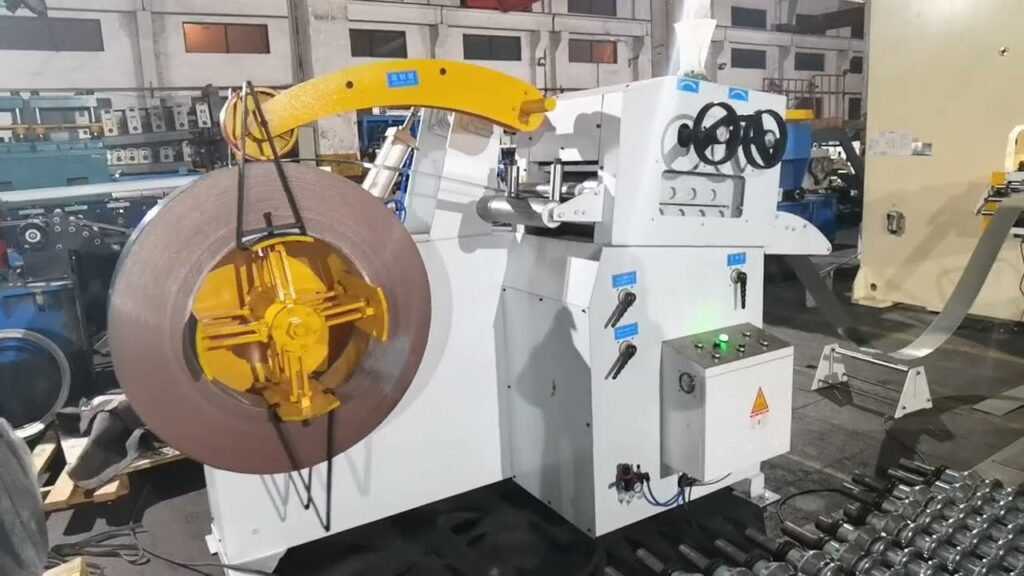
Conclusion
Sheet metal roll forming machines are integral to modern manufacturing, offering numerous benefits such as increased efficiency, cost-effectiveness, and versatile production capabilities. The ability to shape and transform metal sheets into complex profiles makes roll forming a preferred choice in industries ranging from construction to automotive. By understanding the key components, working principles, and applications of roll forming machines, as well as considering factors like material thickness and customization options, manufacturers can make informed decisions when choosing the right machine for their needs. While roll forming poses certain challenges, proper maintenance, quality control, and adherence to best practices can overcome these hurdles and ensure successful production. Looking ahead, the future of sheet metal roll forming technology holds exciting possibilities with advanced automation, integration with Industry 4.0, lightweight materials, precision enhancements, and energy efficiency advancements.
FAQs
Q1. What is the difference between roll forming and stamping?
Roll forming and stamping are both metal forming processes but differ in their approach. Roll forming gradually shapes a continuous metal sheet using a series of rollers, while stamping involves pressing or punching the metal sheet with a die to create the desired shape. Roll forming is suitable for producing long profiles with consistent cross-sections, while stamping is often used for forming flat or three-dimensional shapes with intricate details.
Q2. Can sheet metal roll forming machines handle different types of metals?
Yes, sheet metal roll forming machines can handle a variety of metals, including steel, stainless steel, aluminum, copper, and more. The suitability of a specific metal for roll forming depends on its ductility, thickness, and other material properties. Manufacturers can adjust the machine parameters and tooling to accommodate different types of metals.
Q3. What is the typical speed of a sheet metal roll forming machine?
The speed of a sheet metal roll forming machine can vary depending on factors such as the complexity of the profile, material thickness, and machine capabilities. Typical speeds can range from 10 to 100 feet per minute (3 to 30 meters per minute). However, it’s important to note that speed should be optimized based on the specific requirements of the production process to ensure quality and accuracy.
Q4. How can I ensure the quality of roll-formed profiles?
To ensure the quality of roll-formed profiles, several steps can be taken. This includes implementing a robust quality control system that involves regular inspections, dimensional checks, and adherence to industry standards. Additionally, proper maintenance of the roll forming machine, including cleaning, lubrication, and tooling maintenance, is essential. Monitoring and addressing any material defects or inconsistencies can also contribute to maintaining high-quality output.
Q5. Is roll forming a cost-effective manufacturing process?
Yes, roll forming is considered a cost-effective manufacturing process, especially for large-scale production. The automated nature of roll forming reduces labor costs and eliminates the need for secondary operations like welding or riveting. The efficient use of materials and the ability to produce complex profiles with minimal waste further contribute to cost savings. However, the cost-effectiveness of roll forming should be evaluated based on specific project requirements and the expected return on investment.