When it comes to manufacturing metal parts for construction projects, businesses and individuals have several options available. Two popular methods are purlin roll forming and traditional fabrication. While both methods are capable of producing high-quality parts, they have significant differences in terms of speed, cost, and customizability. In this post, we will explore the advantages and disadvantages of purlin roll forming and traditional fabrication, and help you determine which method is the best fit for your project needs.
overview of purlin roll forming and traditional fabrication
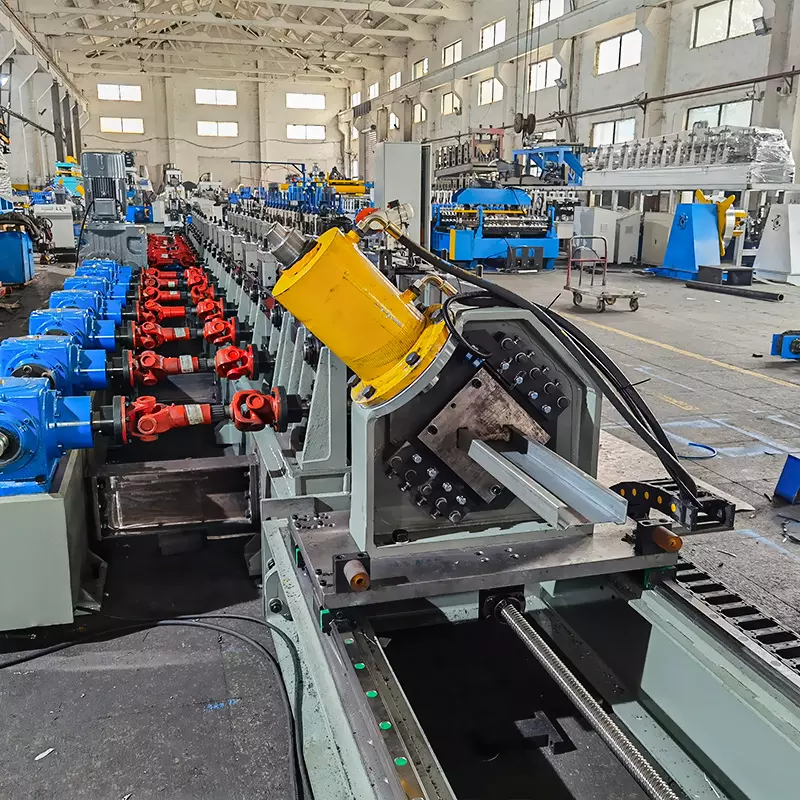
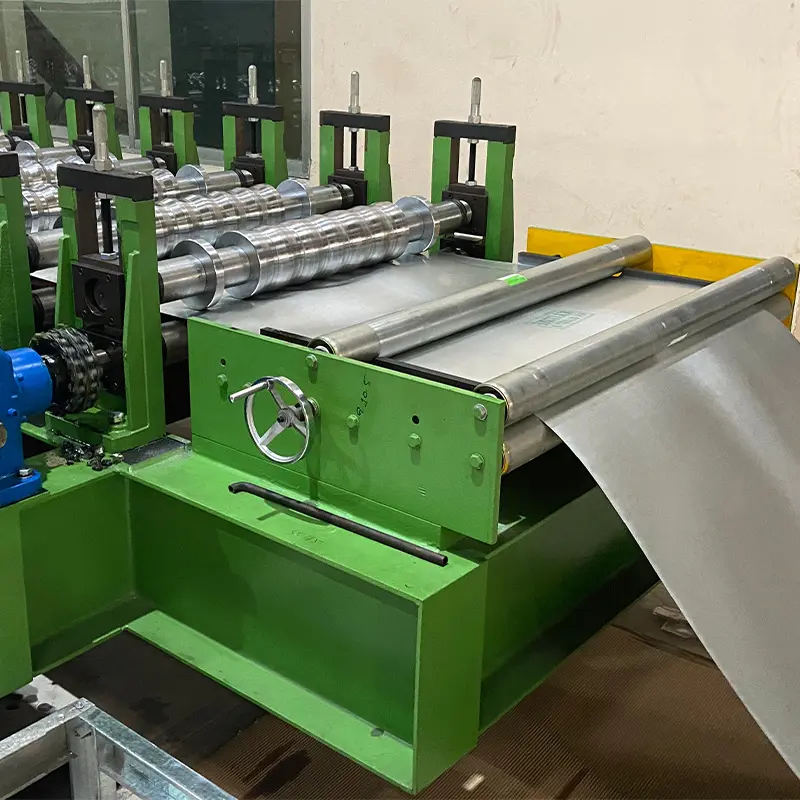
Purlin roll forming and traditional fabrication are two common methods used to manufacture metal parts for construction projects. Here’s an overview of each method and the differences between them:
Purlin Roll Forming: Purlin roll forming is a manufacturing process that involves shaping metal into a specific profile or shape using a roll forming machine. The metal strip is fed into the machine, where it passes through a series of rollers that gradually form it into the desired shape. Purlin roll forming is a fast, efficient, and cost-effective method for producing high-volume runs of standardized parts. It is also highly accurate, producing parts with consistent quality and precision.
Traditional Fabrication: Traditional fabrication involves the manual cutting, bending, and shaping of metal parts using specialized tools and equipment. This method allows for greater customization and flexibility in terms of the shape and size of the parts. However, traditional fabrication can be time-consuming and labor-intensive, which can increase costs and lead times. It also requires skilled labor to ensure the parts are fabricated accurately and consistently.
The main differences between purlin roll forming and traditional fabrication are speed, cost, and customizability. Purlin roll forming is faster and more cost-effective for producing standardized parts in high volumes, while traditional fabrication is better suited for producing custom parts that require greater flexibility and precision. When deciding which method to use, businesses and individuals should consider their project needs, budget, timeline, and desired output.
purlin roll forming
The purlin roll forming process involves the use of a roll forming machine to shape metal into a specific profile or shape. Here are the basic steps involved:
- Material Preparation: The process begins with a long strip of metal, which is fed into the roll forming machine. The metal strip can be made from a variety of materials, including galvanized steel, stainless steel, and aluminum.
- Roll Forming: As the metal strip passes through the roll forming machine, it goes through a series of rollers that gradually shape it into the desired profile. Each set of rollers applies pressure and bends the metal in a specific way to form the profile. The shape and position of each roller are critical to producing the desired shape accurately.
- Cut-Off: Once the metal has been formed into the desired shape, it moves to the cut-off section of the machine, where it is cut to the appropriate length.
- Finishing: The finished parts are typically stacked and packaged for shipping or further processing.
The advantages of purlin roll forming include speed, accuracy, and cost-effectiveness. Roll forming machines can produce high volumes of parts quickly and consistently, which can help businesses meet customer demands and improve their bottom line. Additionally, roll forming machines use precision tools and processes to produce parts with consistent quality and accuracy, reducing waste and rework.
Purlin roll forming is also cost-effective because it reduces the need for manual labor and can produce parts at a lower cost than traditional fabrication methods. This makes it a popular choice for businesses in the construction industry who need to produce standardized parts in high volumes.
Overall, purlin roll forming is a highly efficient and accurate manufacturing process that can produce a wide range of metal shapes and profiles. By using precision tools and processes, roll forming machines can produce parts that meet or exceed industry standards, making them a valuable investment for businesses in a range of industries.
Traditional Fabrication
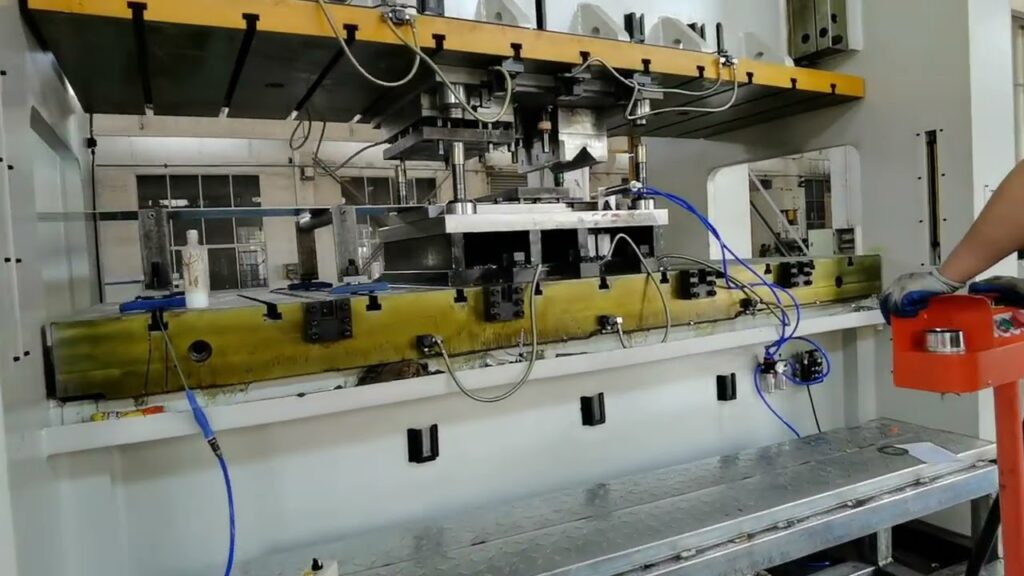

Traditional fabrication is a manual process that involves cutting, bending, and shaping metal parts using specialized tools and equipment. Here are the basic steps involved:
- Design: The process begins with a design or blueprint for the part or component that needs to be fabricated.
- Material Selection: A metal material, such as steel or aluminum, is selected based on the requirements of the part.
- Cutting: The metal material is cut to the required shape and size using cutting tools, such as saws or shears.
- Forming: The metal material is then bent and shaped into the desired form using specialized tools, such as presses, brakes, or rollers.
- Welding: The metal pieces are welded together to form the final part or component.
- Finishing: The finished parts are cleaned, smoothed, and painted or coated as required.
The advantages of traditional fabrication include the ability to customize parts and the availability of skilled labor. With traditional fabrication, parts can be customized to meet specific design requirements or unique specifications. Skilled metal fabricators can use their expertise to create parts that are tailored to the needs of the project. Additionally, traditional fabrication relies on skilled labor, which is often readily available in many areas. This means that businesses can quickly find skilled fabricators to complete their projects.
However, traditional fabrication can be time-consuming and labor-intensive, which can increase costs and lead times. It also requires specialized equipment and tools, which can be expensive to purchase and maintain.
Overall, traditional fabrication is a manual process that offers greater flexibility and customization than roll forming. However, it is better suited for lower volume production runs and may not be as cost-effective as roll forming for larger production runs. Businesses should weigh the pros and cons of both methods when deciding which one to use for their specific project needs.
Comparison of Purlin Roll Forming and Traditional Fabrication
Here’s a comparison of purlin roll forming and traditional fabrication, highlighting the differences in terms of speed, cost, accuracy, and customizability:
Speed: Purlin roll forming is faster than traditional fabrication since it relies on automated machines to produce parts quickly and efficiently. Traditional fabrication, on the other hand, is a manual process that can be time-consuming and labor-intensive.
Cost: Purlin roll forming is typically more cost-effective than traditional fabrication, especially for high volume production runs. Roll forming machines can produce parts quickly and with minimal labor, reducing costs associated with labor and production time. Traditional fabrication, on the other hand, may be more expensive due to the skilled labor and specialized equipment required.
Accuracy: Purlin roll forming is highly accurate since it relies on precision tools and processes to produce consistent and uniform parts. Traditional fabrication may be less accurate, as it involves manual cutting, bending, and shaping, which can lead to variations in the final product.
Customizability: Traditional fabrication offers greater customizability than purlin roll forming, as it allows for more flexibility in terms of design and customization. Roll forming machines are best suited for producing standardized parts in high volumes, whereas traditional fabrication can produce unique or custom parts.
Overall, the choice between purlin roll forming and traditional fabrication will depend on the specific needs of the project. Purlin roll forming is ideal for high-volume production runs that require consistent and uniform parts. Traditional fabrication is better suited for lower-volume production runs that require greater flexibility and customization. Businesses should carefully evaluate the advantages and disadvantages of each method and consider factors such as speed, cost, accuracy, and customizability when deciding which method to use.
In conclusion, purlin roll forming and traditional fabrication are two popular methods used to manufacture metal parts for construction projects. Purlin roll forming is faster, more accurate, and cost-effective for producing standardized parts in high volumes, while traditional fabrication offers greater customizability for unique or custom parts. Businesses and individuals should carefully evaluate the advantages and disadvantages of each method when deciding which one to use. Ultimately, the choice between purlin roll forming and traditional fabrication will depend on the specific needs of the project, including factors such as speed, cost, accuracy, and customizability.