Corrugated Panel Double Layer Machine Features
Trapezoidal & corrugated panel double layer machine can produce two different kind shapes sheets according to the client’s profile drawings and requirements. The steel trapezoidal sheets are new building materials with various thickness and colors.
Applications
The finished products are used as the roof and walls of gymnasiums, airports, theatres, factories, warehouses, garages, exhibition centers etc.
Process Flow
Uncoiler — feeding— roll forming— cutting — output
Machine Configurations
1. Uncoiler |
2. Guide feeder
|
3. roll former |
4. Hydraulic cutting unit
|
5. PLC Control System |
6. Hydraulic station
|
7. Output conveyor |
Profile Drawings for Reference
Photos for Reference
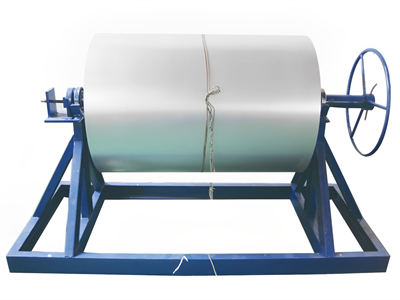
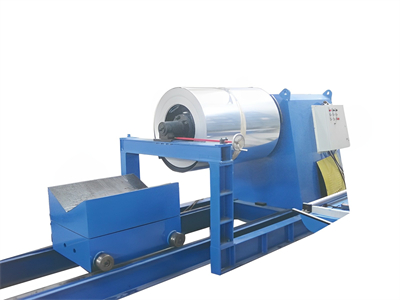
What is panel roll forming machine?
A panel roll forming machine is a type of industrial machinery used for the continuous bending and shaping of metal sheets or strips into desired panel profiles. It is commonly used in the manufacturing industry, particularly in the production of roofing panels, wall cladding panels, and other similar building components.
The roll forming process involves feeding a flat metal sheet or coil through a series of rolls arranged in a sequence. Each set of rolls gradually bends the metal sheet into the desired shape, with each roll contributing to a specific section of the panel profile. The rolls are typically designed to progressively shape the metal, and the final product emerges from the machine as a fully formed panel with a consistent shape and dimensions.
Panel roll forming machines are designed to handle a variety of materials, including steel, aluminum, and other metals, with varying thicknesses. The machines can be customized to produce different panel profiles, such as corrugated panels, standing seam panels, or trapezoidal panels, among others.
These machines are known for their high efficiency and productivity, as they can produce panels in a continuous manner without the need for manual intervention for each individual panel. They often incorporate automated features for material feeding, cutting, and stacking, further streamlining the production process.
Panel roll forming machines are widely used in the construction industry, providing manufacturers with a cost-effective and efficient solution for producing large quantities of panels with consistent quality and dimensional accuracy.
application of ag panel roll forming machine
AG panel roll forming machine is specifically designed for the production of AG panels, which are widely used in the agricultural industry for roofing and siding applications. Here are some of the applications of AG panel roll forming machines:
- Agricultural Buildings: AG panels are commonly used for roofing and siding agricultural structures such as barns, sheds, livestock shelters, and storage buildings. The roll forming machine enables the efficient production of AG panels with the required dimensions and profiles to suit the specific needs of these buildings.
- Grain Storage Facilities: AG panels are often utilized in the construction of grain storage facilities, including silos and grain bins. The roll forming machine can produce the curved panels needed for these structures, ensuring a secure and weather-resistant enclosure for storing grains.
- Poultry Houses: AG panels are an ideal choice for constructing poultry houses and chicken coops. They provide a durable and easy-to-clean surface, ensuring a safe and hygienic environment for poultry farming.
- Greenhouses: AG panels are also used in the construction of greenhouse structures. The panels offer excellent light transmission properties, allowing sunlight to reach the plants while providing insulation and protection from the elements.
- Equipment Shelters: AG panels are employed in the construction of equipment shelters, machinery storage sheds, and workshops on farms. These panels offer a cost-effective and durable solution for protecting agricultural equipment and tools from the weather.
- Riding Arenas and Equestrian Facilities: AG panels can be used to construct riding arenas, horse stalls, and equestrian facilities. They provide a robust and low-maintenance enclosure for horses and riders.
- Rural Fencing: AG panels can be utilized as fencing panels for rural properties and farms. The roll forming machine can produce customized panels with specific profiles, enabling the creation of sturdy and long-lasting fences for securing livestock and marking property boundaries.
- Agricultural Trailers: AG panels can be used to manufacture trailer sides and roofing for agricultural trailers and transport vehicles. The panels offer lightweight yet strong construction, allowing for efficient transportation of agricultural products and equipment.
The AG panel roll forming machine allows for the efficient production of AG panels, meeting the specific requirements of the agricultural industry. The versatility and durability of AG panels make them a popular choice for various applications in the agricultural sector.
how does metal roof panel roll forming machine work?
A metal roof panel roll forming machine is a specialized piece of equipment designed to manufacture metal roof panels efficiently and accurately. Here’s a general overview of how a metal roof panel roll forming machine works:
- Material Feeding: The process begins with loading a coil of metal sheet material onto a decoiler, which is typically located at the beginning of the machine. The coil unwinds as the machine operates, providing a continuous supply of material.
- Material Straightening and Guiding: The metal sheet passes through straightening rollers that remove any coil-set or unevenness in the material. This ensures that the sheet is fed into the roll forming process with proper alignment. Guiding devices, such as entry guides and side guides, help keep the material in the correct position as it enters the forming section.
- Roll Forming Stations: The heart of the machine is the series of roll forming stations. Each station consists of a set of rollers, also known as forming rolls or roll tooling, arranged in a specific sequence. These rolls gradually shape the metal sheet into the desired profile as it passes through them.
- Progressive Forming: The metal sheet is progressively bent and formed as it goes through each roll forming station. Each set of rolls contributes to a specific section of the roof panel profile, gradually shaping it into the required dimensions and features. The number of roll forming stations varies depending on the complexity of the roof panel profile.
- Cutting and Shearing: In some cases, the machine may incorporate a cutting or shearing mechanism. This allows the roof panels to be cut to the desired length while still being produced in a continuous roll-formed process. The cutting mechanism can be placed at a specific station or at the end of the roll forming line.
- Post-Forming Operations: After the roll forming and cutting processes, additional operations may be performed to enhance the functionality or aesthetics of the roof panels. These operations can include embossing, punching holes or slots, adding stiffening ribs, applying coatings, or any other customized requirements.
- Stacking and Packaging: Once the roof panels are formed and any additional operations are completed, they are typically stacked or collected for further handling or packaging. This can involve an automatic stacking system or manual intervention, depending on the machine’s design and the desired output.
Throughout the process, modern roll forming machines often incorporate computer numerical control (CNC) systems or programmable logic controllers (PLCs) to control the machine’s operations, monitor parameters, and ensure precise and consistent panel production.
By utilizing a continuous roll forming process, metal roof panel roll forming machines can efficiently produce high-quality roof panels in large volumes, with consistent shapes, dimensions, and profiles, ready for use in construction projects.
Reviews
There are no reviews yet.