Steel box plate making roll forming machine also named supermarket shelf panel roll forming machine is developed to produce shelf panels with the product display card position. A supermarket shelf panel is used to load the goods and also display the goods information and prices. Usually, the width of the panels is various.
Our intelligent box plate roll forming machine could make various sizes of shelf panel with thickness 0.5-0.8mm or more. Uncoiling, feeding, roll forming, punching, cutting, bending etc. process can be automatically realized on one line. Meantime, we have the roll forming machine to make step beam, upright rack and box beam. All these are components of Pallet racking system.
In warehouse pallet racking system, we are able to manufacture more machines like Step beam roll forming machine, Upright rack roll forming machine and box beam roll forming machine etc.
We make different solutions according to customers’ drawing, tolerance and budget, offering professional one-to-one service, adaptable for your all requirements. Whichever line you choose, the quality of SUNWAY Machinery will ensure you obtain perfectly functional profiles.
Profile Drawings
Production Line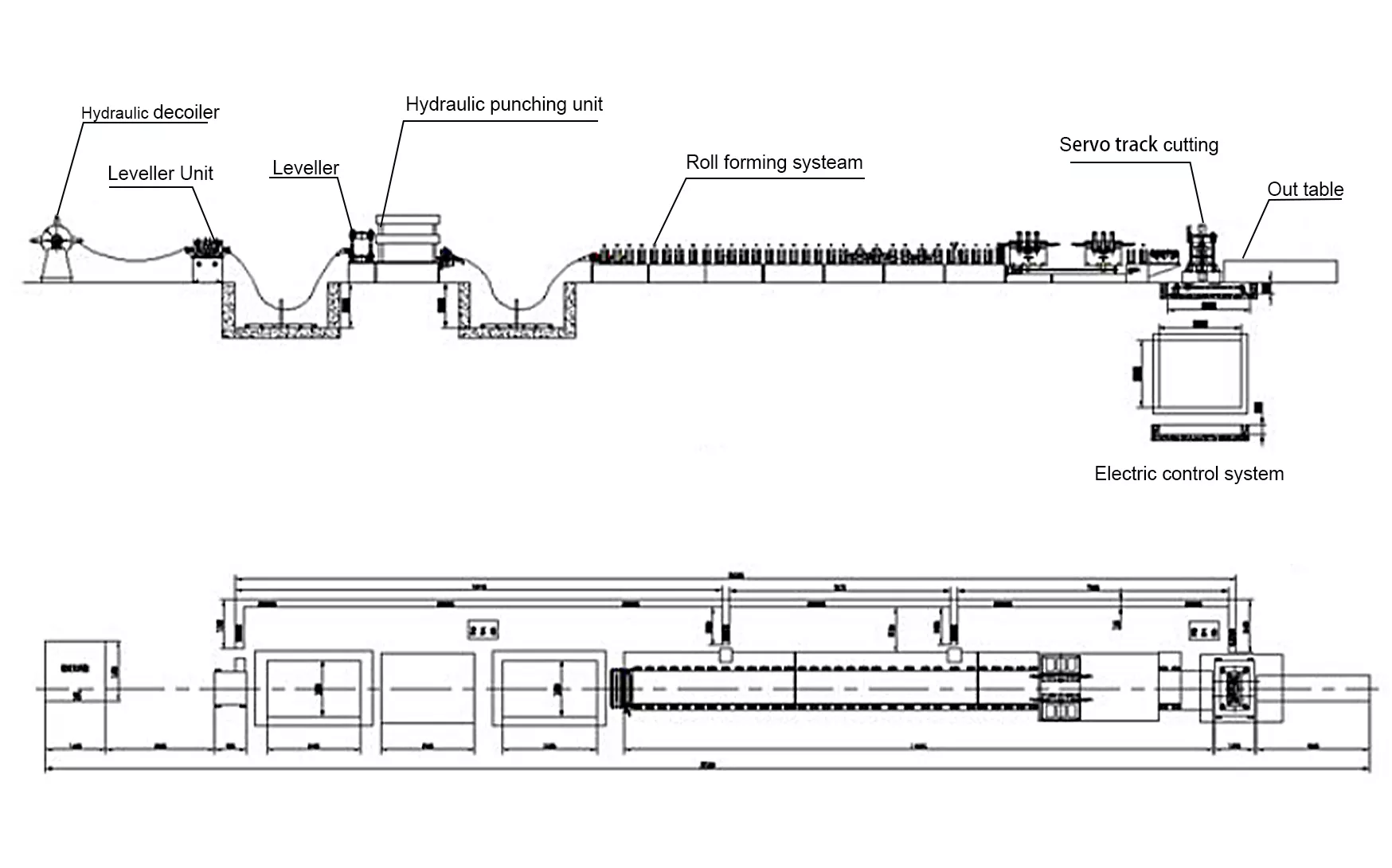
Product Details
Product Parameters
Box Plate Roll Forming Machine | ||
Machinable Material
|
A) Galvanized Coil |
Thickness(MM): 0.5-0.8 as per customer
|
B) PPGI, PPGL | ||
C) Cold-rolled Steel | ||
D) Carbon Steel | ||
Yield Strength | 250 – 350 Mpa | |
Tensil Stress | 350 Mpa-500 Mpa | |
Nominal Forming Speed(M/Min) | 3-10 | * Or According To Your Requirement |
Forming Station | About 18 | * According To Your Profile Drawings |
Decoiler | Manual Decoiler | * Hydraulic Decoiler (Optional) |
Driving System | Chain Drive | * Gearbox Drive (Optional) |
Machine Structure | Steel Plates Welded | * Cast Iron Stands (Optional) |
Rollers’ Material | GCr 15 | * Cr12Mov (Optional) |
Cutting System | Hydraulic Pre-cut | * Hydraulic Post Cut (Optional) |
Frequency Changer Brand | Yaskawa | * Siemens (Optional) |
Power Supply | 380V 50Hz | * Or According To Your Requirement |
Machine Color | Industrial Blue | * Or According To Your Requirement |
Application
What are the compents of steel roll forming machine?
A steel roll forming machine is a type of machinery used in the metalworking industry to shape continuous metal sheets or strips into desired profiles. The components of a typical steel roll forming machine may vary depending on its design and specific application, but here are the common components:
- Uncoiler: This component holds the coil of steel, which is the raw material for the roll forming process. It unwinds the coil and feeds it into the machine.
- Straightening Unit: The straightening unit consists of rollers or leveling devices that ensure the steel strip is flat and free from any deformations before entering the forming rolls.
- Roll Forming Stations: The roll forming stations are the heart of the machine. They consist of a series of forming rolls that progressively bend and shape the metal strip into the desired profile. Each roll forms a specific section of the profile, and the number of stations depends on the complexity of the final shape.
- Gears and Transmission System: The roll forming machine utilizes a system of gears, chains, and sprockets to transmit power from the motor to the forming rolls. These components ensure synchronized movement and control the speed of the material through the machine.
- Cutting Unit: Some roll forming machines have an integrated cutting unit that cuts the formed profile to the desired length. It may use techniques like shear cutting, rotary cutting, or flying cut-off depending on the machine design.
- Control System: Modern roll forming machines have advanced control systems that monitor and regulate various parameters such as speed, length, and shape of the profile. These systems often include human-machine interfaces (HMIs) or programmable logic controllers (PLCs) for easy operation and adjustment.
- Support and Frame Structure: The machine’s frame provides the structural support and rigidity required for the precise forming process. It is typically made of heavy-duty steel and engineered to withstand the forces involved.
- Safety Features: Roll forming machines incorporate safety features like emergency stop buttons, interlocks, guards, and sensors to ensure the operator’s safety during operation.
- Stacker or Conveyor: In some cases, a stacker or conveyor is included to collect and stack the finished profiles for further processing or packaging.
These are the main components of a steel roll forming machine, but the actual configuration and additional features may vary depending on the specific machine model and application.
application of box beam roll forming machine
A box beam roll forming machine is specifically designed to produce box-shaped beams or profiles from flat metal sheets or strips. These box beams typically have a rectangular or square cross-section and are widely used in various industries for structural applications. Here are some common applications of box beam roll forming machines:
- Construction Industry: Box beams are extensively used in the construction industry for various structural purposes. They are commonly employed in building frames, roof trusses, bridges, mezzanines, and industrial structures. The roll forming machine allows for efficient and precise production of box beams with consistent dimensions, which are essential for construction projects.
- Automotive Industry: Box beams find applications in the automotive industry for manufacturing components such as chassis frames, cross members, and structural supports. The roll forming machine enables the production of lightweight yet strong box beams that contribute to the overall structural integrity and safety of vehicles.
- Material Handling and Storage Systems: Box beams are utilized in material handling and storage systems such as shelving units, racks, pallets, and conveyor systems. These systems require sturdy and durable beams to support heavy loads and provide efficient storage solutions. The roll forming machine can produce box beams with specific dimensions and profiles to meet the requirements of such systems.
- Machinery and Equipment Manufacturing: Many machinery and equipment manufacturers utilize box beams in the construction of frames, support structures, and load-bearing components. The roll forming machine enables them to produce custom box beams that match their design specifications, ensuring proper fit and functionality within the equipment.
- Infrastructure and Transportation: Box beams are used in infrastructure projects like railway track support structures, highway guardrails, and overhead sign supports. They provide the required strength and stability for these structures while allowing for easy installation and maintenance. The roll forming machine enables the mass production of box beams, making them cost-effective for large-scale infrastructure projects.
- Renewable Energy Sector: Box beams are employed in renewable energy applications, such as solar panel mounting structures and wind turbine support systems. These structures need to withstand environmental conditions while providing a secure foundation for the renewable energy equipment. The roll forming machine facilitates the production of box beams with the necessary structural integrity for these applications.
These are just a few examples of the applications of box beam roll forming machines. The versatility and efficiency of these machines make them suitable for a wide range of industries where box beams are required for structural purposes.
how does a pedal plate roll forming machine work?
A pedal plate roll forming machine is designed to produce pedal plates, which are components used in the manufacturing of bicycles, motorcycles, and other vehicles. The machine operates through a series of steps to transform a flat metal strip or coil into the desired pedal plate shape. Here’s a general overview of how a pedal plate roll forming machine works:
- Material Feeding: The machine begins by feeding a metal strip or coil into the machine. The material is typically made of steel or aluminum and may be coated for additional protection.
- Straightening: The material passes through a straightening unit that ensures it is flat and free from any deformations. This process is important to maintain the accuracy and consistency of the final pedal plates.
- Roll Forming Stations: The machine consists of a series of roll forming stations, each equipped with a set of rolls that gradually shape the metal strip into the pedal plate profile. The rolls have specific contours and profiles that bend and shape the metal according to the desired design.
- Progression of Forming: As the metal strip moves through the roll forming stations, each set of rolls progressively adds more shape and details to the pedal plate. The strip is guided and supported by rollers and guides to ensure accurate forming and alignment.
- Cutting: Once the pedal plate profile is fully formed, a cutting unit comes into action to separate the formed pedal plates from the rest of the material. The cutting method can vary depending on the machine design and requirements, but common techniques include shear cutting or rotary cutting.
- Additional Operations: After the cutting process, the pedal plates may undergo additional operations such as hole punching, embossing, or any other required modifications. These operations can be integrated into the roll forming machine or performed in separate processes.
- Collection and Stacking: The finished pedal plates are then collected and stacked for further processing or packaging. Some machines may include an integrated stacking or conveyor system to facilitate this step.
- Control System: The pedal plate roll forming machine is typically equipped with a control system that monitors and regulates various parameters, such as speed, length, and shape of the pedal plates. This system ensures consistent and accurate production and allows for easy operation and adjustment.
It’s important to note that the exact configuration and features of a pedal plate roll forming machine may vary depending on the specific model and manufacturer. However, the overall process described above provides a general understanding of how such a machine typically operates to produce pedal plates.