Light steel roll forming machines have become an integral part of the manufacturing industry, offering efficient and cost-effective solutions for producing a wide range of building materials such as roofing, wall cladding, and even structural framing. However, have you ever wondered how these machines are made? From the raw materials to the finished product, the process of manufacturing light steel roll forming machines is a fascinating and intricate one. In this post, we’ll take a closer look at each step of the process, including the raw materials, design, manufacturing of these machines. So, let’s dive in and explore the journey from raw material to finished product for light steel roll forming machines.
Raw Materials of light steel roll forming machines
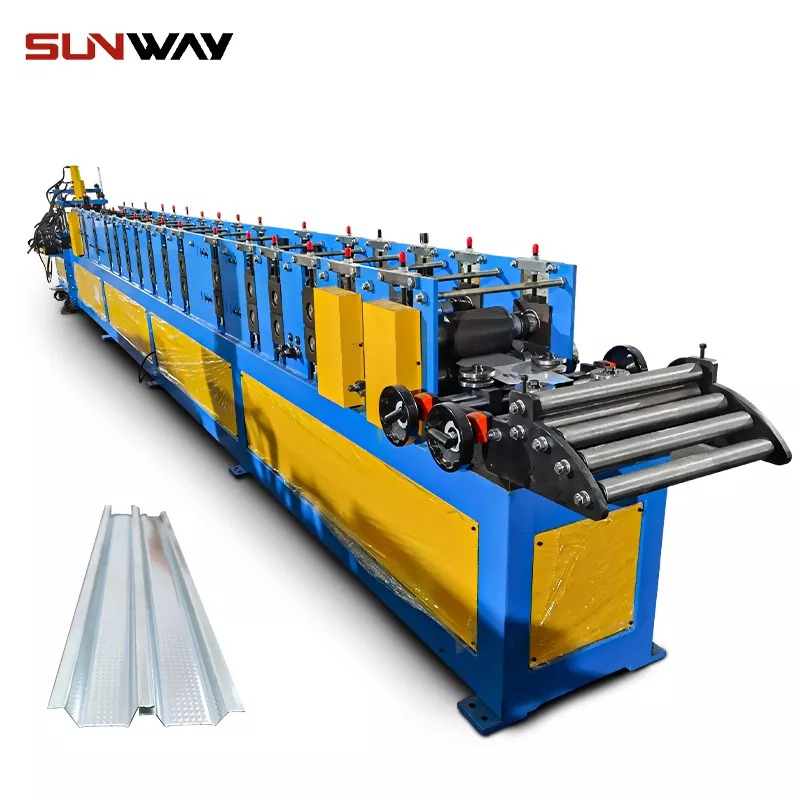
The production of light steel roll forming machines begins with the selection of high-quality raw materials. These raw materials are essential for ensuring the durability, strength, and precision of the final product.
The primary raw material used in the production of light steel roll forming machines is steel. Steel sheets and coils are typically used, with the specific grade of steel varying depending on the intended use of the machine. For example, machines designed for heavy-duty use may require thicker, stronger steel than machines designed for lighter applications.
Other raw materials used in the manufacturing process may include aluminum, brass, copper, and various alloys. These materials are often used for specific components of the machine, such as bearings, gears, and other mechanical parts.
In addition to the raw materials themselves, other materials such as lubricants, adhesives, and coatings may also be used during the manufacturing process. These materials help to ensure that the finished product is not only strong and durable, but also performs optimally and resists corrosion over time.
Overall, the selection and use of high-quality raw materials are crucial for ensuring the quality and longevity of light steel roll forming machines.
Design of light steel roll forming machine
The design process of creating a light steel roll forming machine is a crucial step in the manufacturing process. It involves the use of computer-aided design (CAD) software and other tools and technologies to create a detailed and accurate plan for the machine.
The first step in the design process is to determine the specific requirements and specifications of the machine. This includes determining the intended use of the machine, the size and shape of the components, and the necessary manufacturing processes.
Once the requirements and specifications have been established, designers will use CAD software to create a 3D model of the machine. This model allows them to visualize the machine and make any necessary adjustments before manufacturing begins.
During the design process, designers may also use other tools and technologies, such as simulation software, to test the performance of the machine. This can help to identify any potential problems or design flaws before the manufacturing process begins.
Once the design is complete, the CAD files are sent to the manufacturing team, who will use them to produce the necessary components for the machine. The precision and accuracy of the design are critical at this stage, as even small variations in the dimensions or shape of the components can impact the overall performance of the machine.
Overall, the design process of creating a light steel roll forming machine involves the use of advanced tools and technologies to ensure precision and accuracy in the final product. By taking the time to design the machine properly, manufacturers can create a product that performs optimally and meets the specific needs of their customers.
Manufacturing Process of light steel roll forming machines
The manufacturing process of light steel roll forming machines involves several stages, each of which is crucial for creating a high-quality, durable product. Here are the step-by-step manufacturing processes involved in creating light steel roll forming machines:
- Cutting: The first step in the manufacturing process is to cut the raw materials into the required size and shape. This is typically done using a variety of cutting tools, including shears, laser cutters, or plasma cutters.
- Bending: Once the raw materials have been cut to size, they are then bent into the required shapes using bending machines. This process is critical for creating the various components of the machine, including the frame, rollers, and other structural components.
- Welding: The components are then welded together using various welding techniques, such as MIG or TIG welding. Welding is critical for ensuring that the machine is strong and durable, as it creates a bond between the various components.
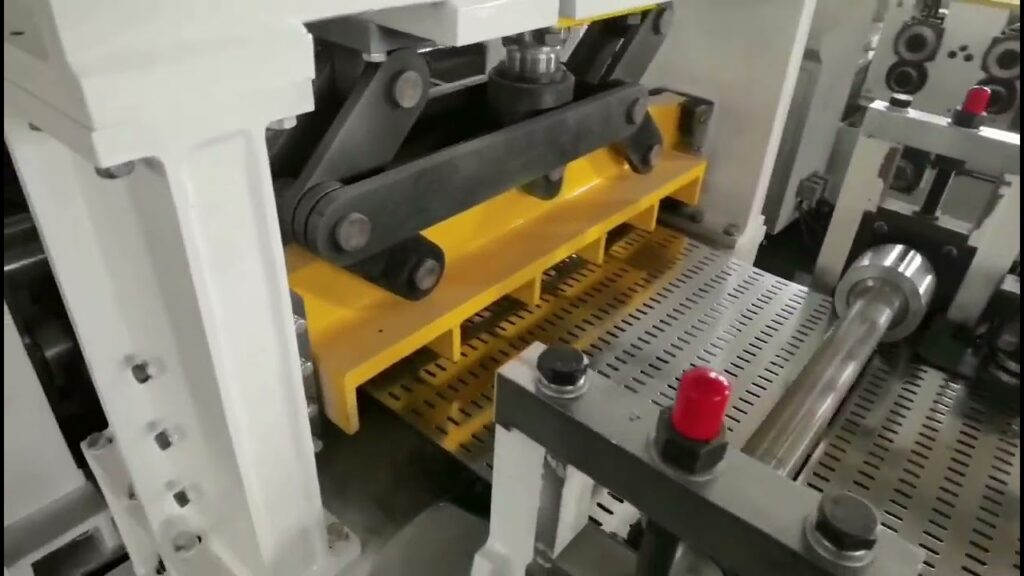
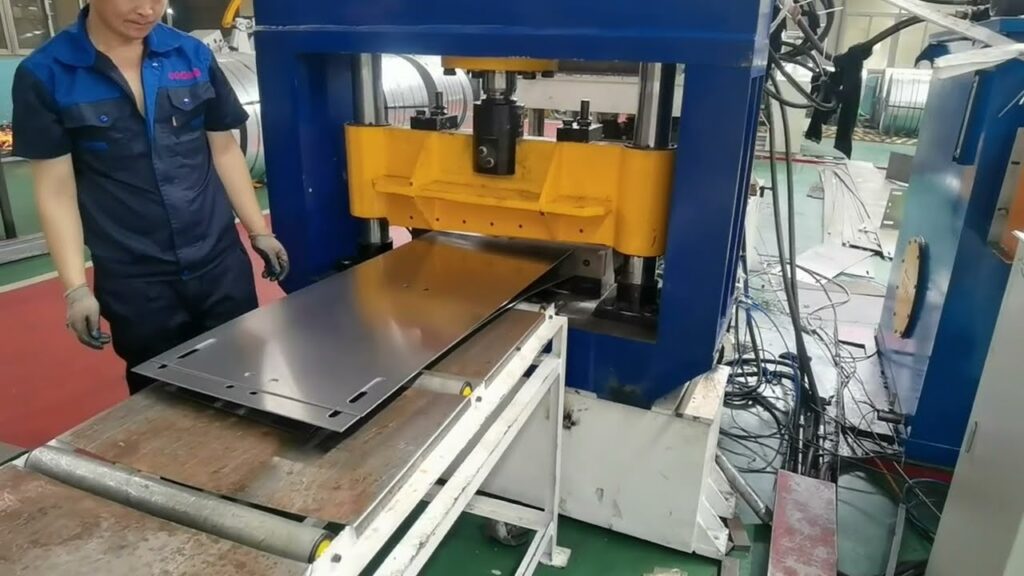
Assembly: Once the components have been welded together, they are then assembled into the final product. This typically involves fitting the various components together, such as attaching the rollers and other moving parts to the frame.
Finishing: After assembly, the machine is then finished to ensure that it meets the required specifications. This can include grinding, painting, or applying other finishes to the machine to improve its appearance and durability.
Quality Control: Throughout the manufacturing process, various quality control measures are taken to ensure that the machine meets the required standards and specifications. This can include inspections, testing, and other quality control measures to identify and correct any issues.
Overall, the manufacturing process of light steel roll forming machines is complex and involves several stages. By carefully cutting, bending, welding, and assembling the various components of the machine, manufacturers can create a high-quality product that meets the specific needs of their customers.
Finished Product of light steel roll forming machine
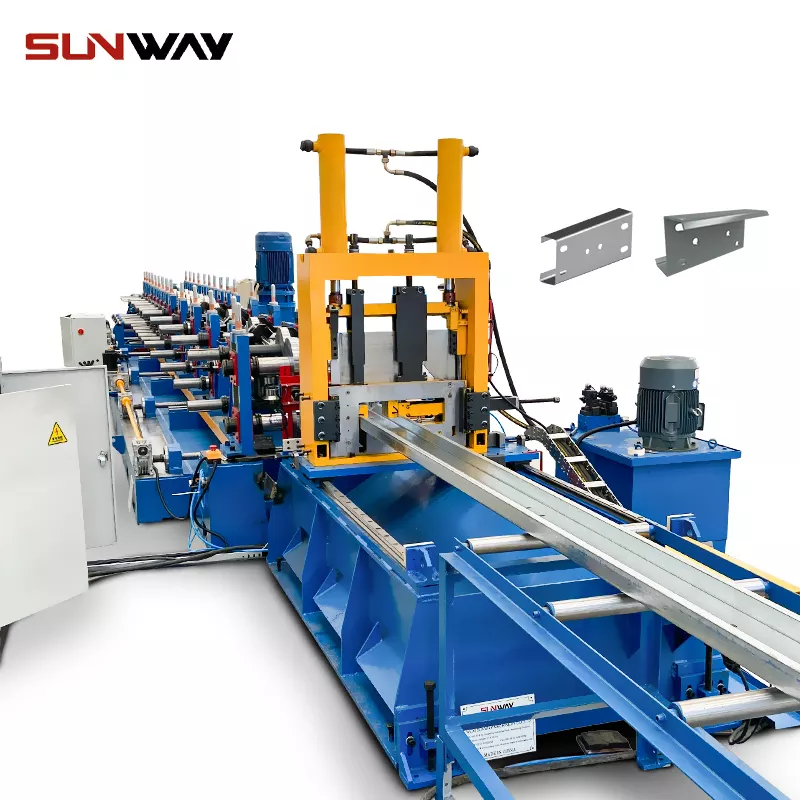
The finished product of a light steel roll forming machine is a versatile and efficient tool used in the manufacturing of a wide range of building materials. These machines are designed to take raw materials such as steel coils or sheets and transform them into specific shapes and sizes required for roofing, wall cladding, and other applications.
A light steel roll forming machine typically consists of a frame, rollers, cutting mechanisms, and various other components. The machine operates by feeding the raw material through the rollers, which shape it into the required profile. The material is then cut to length and fed out of the machine, ready for use in the manufacturing process.
One of the main advantages of using a light steel roll forming machine is its efficiency. These machines can produce large quantities of material quickly and accurately, reducing the time and labor required for the manufacturing process. Additionally, the use of roll forming machines results in high-quality, precise products that meet the required standards and specifications.
In addition to their efficiency, light steel roll forming machines also offer versatility in terms of the shapes and sizes of the products they can produce. By changing the rollers and other components of the machine, manufacturers can create a wide range of profiles to meet specific customer requirements.
In summary, the production of light steel roll forming machines involves a complex process from the selection of high-quality raw materials to the design, manufacturing, and quality control stages. The finished product is a versatile and efficient tool used in the manufacturing of a wide range of building materials. With their ability to produce precise, high-quality products quickly and efficiently, light steel roll forming machines play a critical role in the manufacturing industry.