Unistrut roll forming machines are used to form U-channel metal studs and joists from coiled steel. These machines are a key piece of equipment in the structural framing industry. This guide provides a comprehensive overview of unistrut roll forming machine types, components, suppliers, applications, operation, and more.
Overview of Unistrut Roll Forming Machines
Unistrut roll forming machines take flat strip steel coil as input and progressively form it into U-channel shapes through a series of rolling and bending operations. The steel profiles produced are used for structural framing in walls, roofs, mezzanines, solar panel mounts, and numerous other applications.
Key details about unistrut roll forming machines:
- Also called C/U channel roll formers or stud and track roll forming machines
- Available in manual, semi-automatic, and fully automatic versions
- Production capacities from 10 to 200 feet/minute
- Form U-channel, C-channel, studs, tracks, furring channels
- Use CAD software for profile design and roll tooling setup
- Roller boxes house bearing blocks with forming rollers
- Rollers are machined to shape to bend and form the steel strip
- Punching units to punch service holes in the profile flanges
- Decoilers hold steel coil inputs up to 5 tons
- Feed tables with edge guides align the strip
- Programmable controls for automatic production
- Range of widths up to 2.5″, thicknesses 22 to 16 gauge
Unistrut Roll Former Types
There are three main types of unistrut roll forming machines:
Machine Type | Description |
---|---|
Manual | Basic machines with manual material feeding and cutoff. Low production rates. |
Semi-Automatic | Automated feeding and cutting but manual part offloading. Intermediate rates. |
Fully Automatic | Automated coil loading, feeding, forming, cutting, part stacking. Highest throughput. |
Unistrut Roll Former Components
Unistrut roll forming machines consist of the following main components:
- Decoiler: Holds the steel coil, allows controlled unwinding. Has a payoff reel and coil mandrel.
- Feed table: Supports and guides the strip feeding into the roll forming section. Has edge guides.
- Forming section: Roller boxes with machined rollers make progressive bends to shape the strip.
- Punching unit: Optional station with punch and die for punching service holes.
- Cutoff press: Shears the formed profile to desired lengths. Manual or automated.
- Stacking table: Collects cut parts as they exit the machine. Can have automated stacking.
- Electrical cabinet: Houses the controls, drives, and automation system.
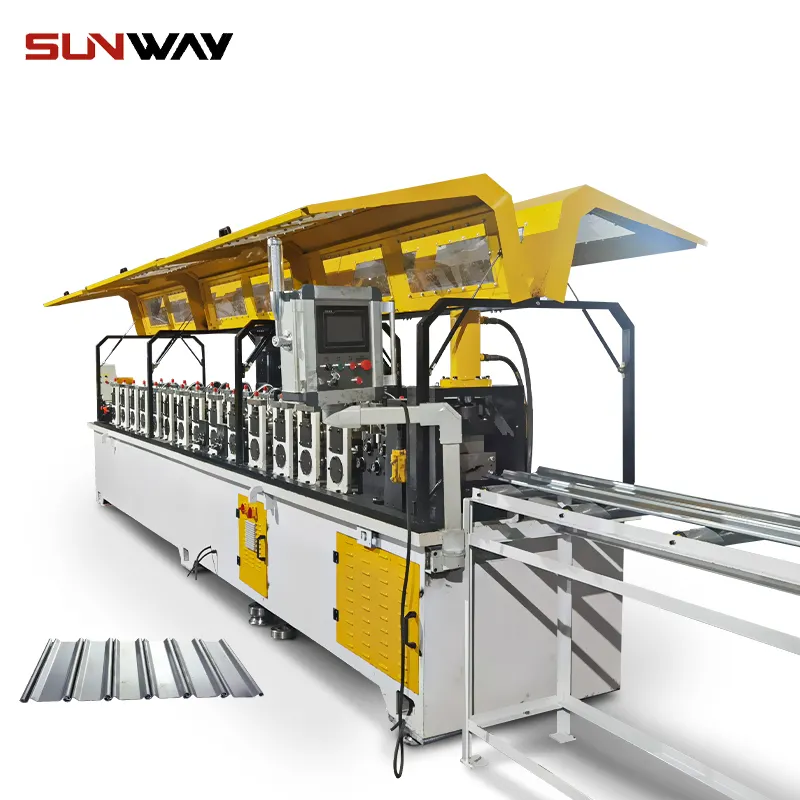
Applications of Unistrut Roll Forming Machines
Unistrut roll forming machines produce standardized and custom U-channel metal framing profiles for the following applications:
- Drywall and curtain wall construction
- Roof trusses, purlins, eave struts
- Electrical trunking and cable trays
- Solar panel mounts
- Mezzanine and storage platforms
- Material handling systems
- Agricultural buildings
- Transmission towers
- Scaffolding
- Greenhouses
- Pallet racking
- Conveyor systems
Common materials rolled include galvanized steel, stainless steel, and aluminum.
Unistrut Roll Former Specifications
Unistrut roll forming machines are available with a range of specifications to suit different production requirements:
Parameter | Typical Range |
---|---|
Width Capacity | 1.5 – 3 inches |
Thickness Capacity | 0.7 – 2 mm (22 – 16 gauge) |
Profile Height | 1 – 6 inches |
Production Speed | 10 – 200 feet/minute |
Drive Power | 5 – 15 kW |
Working Precision | ±0.5 mm |
Coil Weight Capacity | 1 – 5 tons |
Coil ID | 20 – 32 inches |
How to Choose a Unistrut Roll Forming Machine
Follow these tips for selecting the right unistrut roll former:
- Determine needed profile dimensions and production rate
- Choose between manual, semi-auto, and automatic versions
- Consider coil capacity, line speed, and power requirements
- Select number of forming stands based on profile complexity
- Include decoiler, feed table, cutoff press, and other auxiliaries
- Get punching, notching, drilling units if needed
- Choose reputable manufacturers like Metform, Rollformer, Bradbury
- Look for rugged design, precision machining, high quality components
- Seek machines with fast changeover, easy operation, and maintenance access
- Compare options between suppliers on build quality, features, price
- Check lead time, shipping terms, payment options, and warranty
- Require run samples, factory acceptance testing, and operator training
Careful specification matching will ensure you get a unistrut roll former optimized for your production needs.
Unistrut Roll Forming Machine Manufacturers
There are many competent unistrut roll former manufacturers across the world. Some of the top global suppliers include:
Company | Location |
---|---|
Metform | United States |
Rollformer | China |
Bradbury | United States |
Samco Machinery | China |
Metecno | Italy |
Shanghai Metal Corporation | China |
Jouan Metal | China |
Ernst Machine Tools | United Kingdom |
Technoshell Automations | India |
Ferracci Machines | Italy |
When comparing manufacturers, look at production capacity, experience with your product type, quality certifications, customization capabilities, and after-sales service. Visit reference plants to inspect build quality if possible.
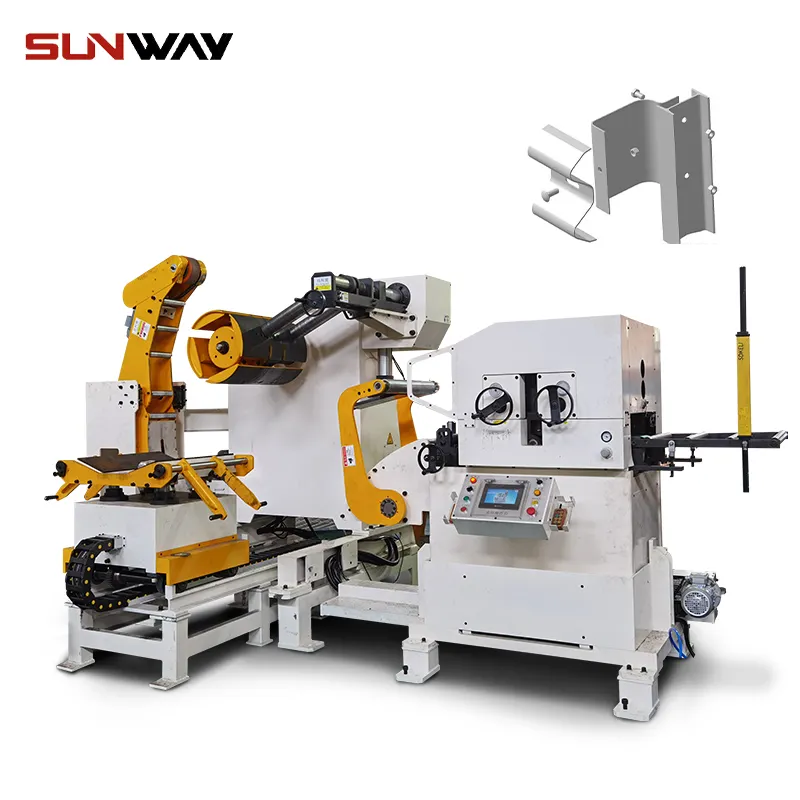
Unistrut Roll Former Costs
Unistrut roll forming machine prices depend on the size, production rate, level of automation, and optional features. Typical price ranges:
- Small manual machines: $8,000 – $15,000
- Medium semi-auto roll formers: $20,000 – $60,000
- Large high-speed automated machines: $80,000 – $150,000
Additional costs for decoilers, installation, spare parts, operator training should also be accounted for. Request quotes from several suppliers and compare life cycle costs when making purchase decisions.
How to Install Unistrut Roll Forming Machines
Proper installation of unistrut roll formers improves performance and longevity. Follow these best practices:
- Prepare flat, level, and vibration-free foundation, typically reinforced concrete
- Provide adequate space around machine for operation, maintenance, and material handling
- Use precision instruments to properly level and align machine
- Bolt machine baseplates securely per manufacturer instructions
- Install all safety guards and interlocks before operation
- Electrically ground per local codes and connect power as per manual
- Perform test runs and trial forming to verify correct functioning
- Fine tune processes and make final adjustments based on initial production
How to Operate a Unistrut Roll Former
Here are some tips for safe and optimal unistrut roll former operation:
- Study the operating manual thoroughly before use
- Program the machine settings and download forming profiles
- Ensure all guards are in place prior to powering up
- Feed coil of the specified dimensions into the decoiler
- Thread strip through the roller boxes and align in feed table
- Adjust edge guides and support rollers to center the strip
- Set speed, guide height, and cutoff length per profile
- Initiate automatic operation and monitor forming process
- Inspect first pieces for accuracy before continuous runs
- Periodically measure profile dimensions for quality control
- Stop machine safely if jams, defects, or errors occur and resolve issues
- Maintain steady coil supplies to minimize downtime
- Keep work area clean and clear of obstructions
Unistrut Roll Former Maintenance
Regular maintenance is vital for optimum performance and longevity of unistrut roll formers. Key activities include:
- Clean machine daily using compressed air and vacuum
- Lubricate bearings and sliding parts with oil or grease
- Inspect machine for loose fasteners, leaks, unusual noises
- Verify electrical connections are tight and panels debris-free
- Check rollers, strippers, guides for wear and replace as needed
- Change hydraulic oil and filters per manufacturer schedule
- Inspect drive chains, sprockets, gears for stretch or damage
- Verify pneumatic lines and valves have no leaks or blockages
- Complete partial disassembly for deep cleaning after long runs
- Retighten gibs to eliminate play in guiding components
- Update machine software and test revisions before production
Unistrut Roll Forming Troubleshooting
Some common unistrut roll former issues and solutions:
Problem: Inaccurate profile dimensions
- Check roller adjustment and gap spacing
- Replace worn or damaged forming rollers
- Adjust feed speed or metal thickness
Problem: Strip jamming in machine
- Check for feed misalignment and straighten material
- Clean buildup from forming rollers and stripper plates
- Adjust roller box spacing and stripper pressure
Problem: Excessive strip curling
- Increase edge guide pressure to flatten strip
- Check if forming steps are evenly staggered
- Try slower feed speed and ensure proper lubrication
Problem: Burrs or scratches on formed profile
- Replace worn forming rollers and strippers
- Increase inter-roller spacing slightly
- Polish roller surfaces if needed
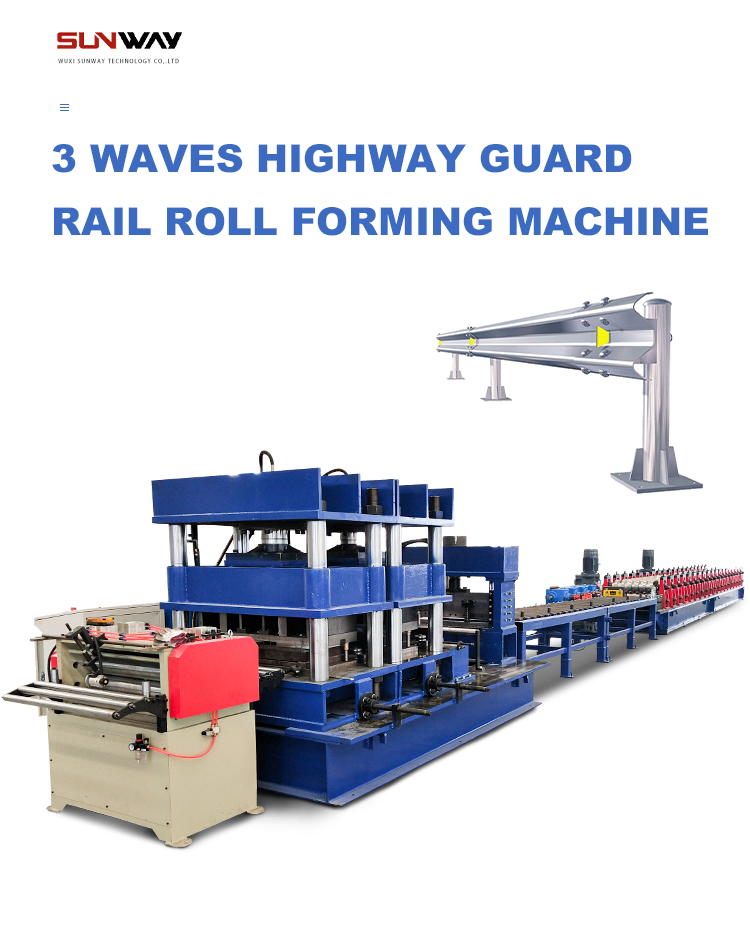
FAQs
Q: What thickness of steel coil can be formed on unistrut roll formers?
A: Typical thickness capacity is 22 gauge (0.7mm) to 16 gauge (1.6mm) steel. Maximum capacities around 14 gauge (2mm) are possible on some heavy duty machines.
Q: What length of profile can be produced on unistrut roll forming machines?
A: Standard lengths range from 8 to 24 feet. Custom or automated cutoff presses can produce parts from just a few inches long to over 30 feet.
Q: How fast is the production rate of unistrut roll forming machines?
A: Production speed varies by machine size but is typically 10 to 200 linear feet per minute. Larger automated machines with faster line speeds maximize throughput.
Q: What are the power requirements for unistrut roll forming machines?
A: Most unistrut roll formers require 3-15 kW of power depending on the motor sizes and number of driven sections. Voltages of 220V, 380V, or 480V at 50 or 60 Hz are usually required.
Q: What safety measures should be used with unistrut roll forming machines?
A: Safety measures like guarding, emergency stops, light curtains, lockout/tagout devices, and strict operating procedures should be implemented to protect operators.
Q: What factors affect the price of unistrut roll forming machines?
A: Key pricing factors are production speed, automation level, size and thickness capacity, number of forming heads, brand reputation, and optional features.
Q: Should unistrut roll forming machines be installed on reinforced concrete?
A: Yes, a reinforced concrete slab is recommended to provide a stable foundation immune to vibration and twisting forces during operation.
Q: How often should unistrut roll forming machine maintenance be performed?
A: Daily cleaning and weekly inspections are advised. Full maintenance including oil changes, part replacement, and overhauls should be done every 6-12 months.
Q: What is the typical useful life of a unistrut roll forming machine?
A: With proper installation, operation, and maintenance, quality unistrut roll formers will last 15-25 years in full time production conditions.