In the realm of modern construction, efficiency, precision, and cost-effectiveness are paramount. To meet these demands, innovative machinery and manufacturing techniques have become indispensable. One such groundbreaking invention is the furring channel roll forming machine, a versatile equipment that has transformed the production of furring channels, a vital component in various construction projects. In this article, we delve into the intricacies of furring channel roll forming machines, exploring their functions, benefits, installation process, and much more.
Understanding Furring Channels
Before we dive into the workings of a furring channel roll forming machine, it’s essential to understand what furring channels are and their significance in construction. Furring channels, often referred to as hat channels or resilient channels, are long, narrow metal strips that play a crucial role in supporting and leveling walls, ceilings, and other surfaces. These channels create a cavity between the surface material and the structure, providing space for insulation, soundproofing, and plumbing installations.
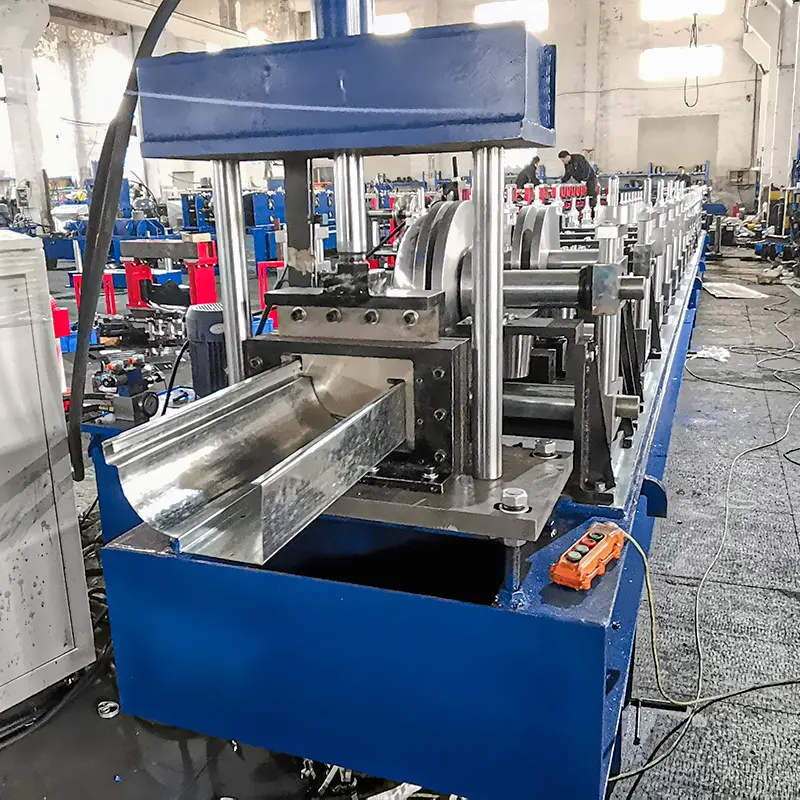
Types of Furring Channels
Furring channels come in various types, each designed to cater to specific construction requirements. Common types include:
- Metal Furring Channels: These are typically made from galvanized steel, offering exceptional strength, durability, and resistance to corrosion.
- Wood Furring Channels: Wooden furring channels, usually constructed from treated lumber, provide an alternative for applications where metal channels may not be suitable.
- Resilient Furring Channels: These channels have a resilient design that effectively dampens vibrations and reduces noise transmission, making them ideal for soundproofing applications.
Benefits and Applications of Furring Channels
The use of furring channels presents numerous advantages in construction projects. Some key benefits include:
- Leveling and Structural Support: Furring channels create a level and even surface, ensuring the proper installation of wallboards, drywall, and other cladding materials. They also offer structural support to bear the weight of the surface material.
- Thermal and Acoustic Insulation: The cavity formed by furring channels allows for the installation of insulation materials, enhancing the energy efficiency and soundproofing capabilities of a building.
- Plumbing and Wiring Concealment: The space behind furring channels provides a concealed pathway for plumbing pipes, electrical wiring, and other utilities.
- Moisture Protection: By creating an air gap between the surface material and the structure, furring channels help prevent moisture buildup and potential damage.
Given their versatility, furring channels find applications in various construction projects, including residential buildings, commercial spaces, hospitals, hotels, and more.
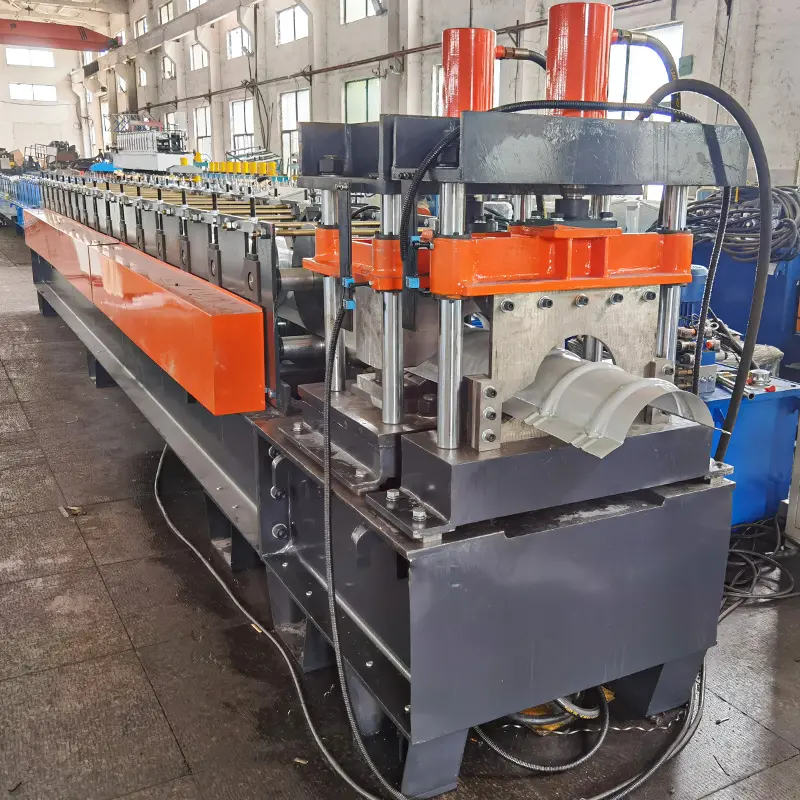
The Roll Forming Process
At the heart of the efficient production of furring channels lies the roll forming process. Roll forming is a continuous bending operation that transforms flat metal sheets or strips into desired profiles with consistent cross-sections. A furring channel roll forming machine is specially designed to automate this process, ensuring high precision and productivity.
How a Furring Channel Roll Forming Machine Works
A furring channel roll forming machine consists of several key components that work in harmony to produce furring channels. The primary components include:
- Decoiler: This component unwinds and feeds the metal coil into the roll forming machine, ensuring a continuous supply of material.
- Roll Forming Station: The roll forming station consists of a series of rollers arranged in a specific configuration. As the metal strip passes through these rollers, it gradually takes on the desired shape and profile.
- Cut-off System: Once the desired length of the furring channel is achieved, a cut-off system precisely trims the channel to the required size.
- Control System: The control system operates the various components of the machine, regulating the speed, length, and other parameters of the roll forming process.
By feeding the metal strip through the roll forming machine, the furring channel is shaped and cut according to precise specifications, ensuring consistent quality and accuracy.
Advantages of Using a Furring Channel Roll Forming Machine
The utilization of a furring channel roll forming machine brings forth a myriad of advantages for construction businesses and contractors. Let’s explore some of these benefits:
Cost-effectiveness
With traditional manufacturing methods, producing furring channels can be labor-intensive and time-consuming. However, a furring channel roll forming machine automates the process, significantly reducing manual labor requirements and increasing production speed. This automation results in cost savings, as businesses can produce furring channels in large quantities with fewer resources.
Customization Options
Furring channel roll forming machines offer flexibility in terms of customization. By adjusting the machine settings, manufacturers can produce furring channels of different dimensions, profiles, and material thicknesses, catering to the specific needs of their projects.
High Production Speed
The automated nature of furring channel roll forming machines enables rapid production rates. These machines can roll form furring channels at a consistent speed, allowing for efficient manufacturing processes and timely completion of construction projects.
Consistent Quality and Accuracy
The precise control offered by furring channel roll forming machines ensures consistent quality and accuracy in the manufactured channels. The uniformity of the channels enhances their structural integrity and facilitates seamless installation, leading to a superior end result.
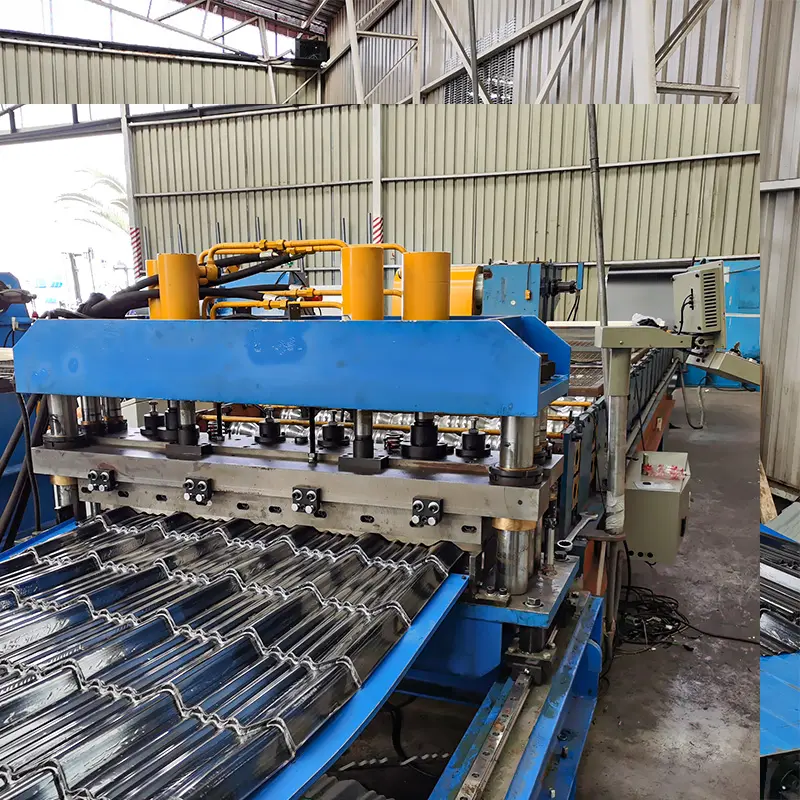
Factors to Consider When Choosing a Furring Channel Roll Forming Machine
When selecting a furring channel roll forming machine for your construction business, it’s crucial to consider several factors to ensure optimal performance and long-term reliability. These factors include:
Machine Specifications
Evaluate the specifications of the roll forming machine, such as the maximum coil width and thickness it can handle. Ensure that the machine can accommodate the dimensions and material thicknesses required for your specific furring channel profiles.
Material Compatibility
Different furring channels are made from various materials, including steel, aluminum, and wood. Verify that the roll forming machine is compatible with the materials you intend to use, ensuring efficient and precise forming processes.
Automation Features
Look for automation features that enhance productivity and reduce manual labor requirements. Features such as automatic coil feeding, length measurement, and cutting systems can significantly streamline the manufacturing process.
After-sales Support
Consider the availability of after-sales support and technical assistance from the manufacturer. Reliable customer support ensures that any issues or maintenance requirements are promptly addressed, minimizing downtime and maximizing machine performance.
Installation and Operation of a Furring Channel Roll Forming Machine
Installing and operating a furring channel roll forming machine requires careful attention to detail to ensure smooth operation and safety. Follow these essential steps:
Preparing the Machine for Operation
- Ensure that the machine is placed on a stable and level surface, providing a secure foundation.
- Connect the machine to a reliable power source and verify that all electrical connections are properly made.
- Familiarize yourself with the machine’s control panel and settings, ensuring you understand how to adjust the parameters according to your requirements.
Safety Precautions
- Always wear appropriate personal protective equipment (PPE), including gloves, safety glasses, and ear protection, when operating the machine.
- Familiarize yourself with the machine’s emergency stop button and its location for quick access in case of any unforeseen circumstances.
- Follow all safety guidelines provided by the manufacturer to minimize the risk of accidents or injuries.
Step-by-Step Installation Process
- Begin by installing the decoiler and properly aligning it with the roll forming machine.
- Adjust the decoiler to accommodate the coil of material you will be using, ensuring smooth unwinding during the roll forming process.
- Feed the metal strip through the roll forming station, making sure it aligns with the rollers and passes through them smoothly.
- Adjust the machine settings to achieve the desired furring channel dimensions and profiles.
- Activate the machine and monitor the forming process to ensure that the channels are being produced accurately and with consistent quality.
Maintenance Tips
Regular maintenance is crucial for optimal performance and longevity of the furring channel roll forming machine. Follow these maintenance tips:
- Clean the machine regularly to remove any debris or metal shavings that may accumulate during the roll forming process.
- Lubricate the machine’s moving parts as recommended by the manufacturer to minimize friction and ensure smooth operation.
- Inspect and tighten all bolts and fasteners periodically to prevent loosening due to machine vibrations.
- Schedule regular inspections by a qualified technician to identify any potential issues and address them promptly.
By following these installation and operation guidelines and adhering to proper maintenance practices, you can maximize the efficiency and lifespan of your furring channel roll forming machine.
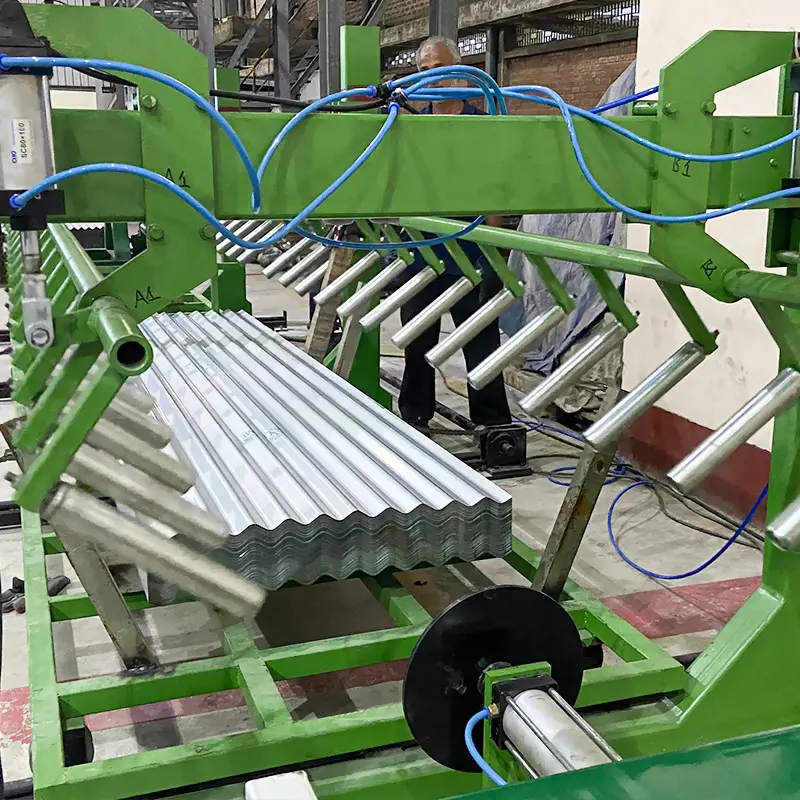
Case Studies and Success Stories
Real-world examples of utilizing furring channel roll forming machines demonstrate their effectiveness in various construction projects. Here are a few case studies highlighting the benefits experienced by businesses and contractors:
Case Study 1: Residential Building Construction
A construction company specializing in residential building projects integrated a furring channel roll forming machine into their manufacturing process. By using the machine, they achieved significant time savings and cost reductions compared to traditional methods. The machine’s ability to produce customized furring channels of consistent quality ensured a smooth and efficient installation process, resulting in high customer satisfaction.
Case Study 2: Commercial Space Renovation
In a large-scale commercial space renovation project, a contractor employed a furring channel roll forming machine to meet tight deadlines and ensure precise installations. The machine’s high production speed allowed for quick channel manufacturing, while its customization options enabled the contractor to adapt to various design requirements. This resulted in a successful project completion within the given timeframe.
These case studies exemplify how the incorporation of furring channel roll forming machines in construction processes can streamline operations, reduce costs, and enhance overall project outcomes.
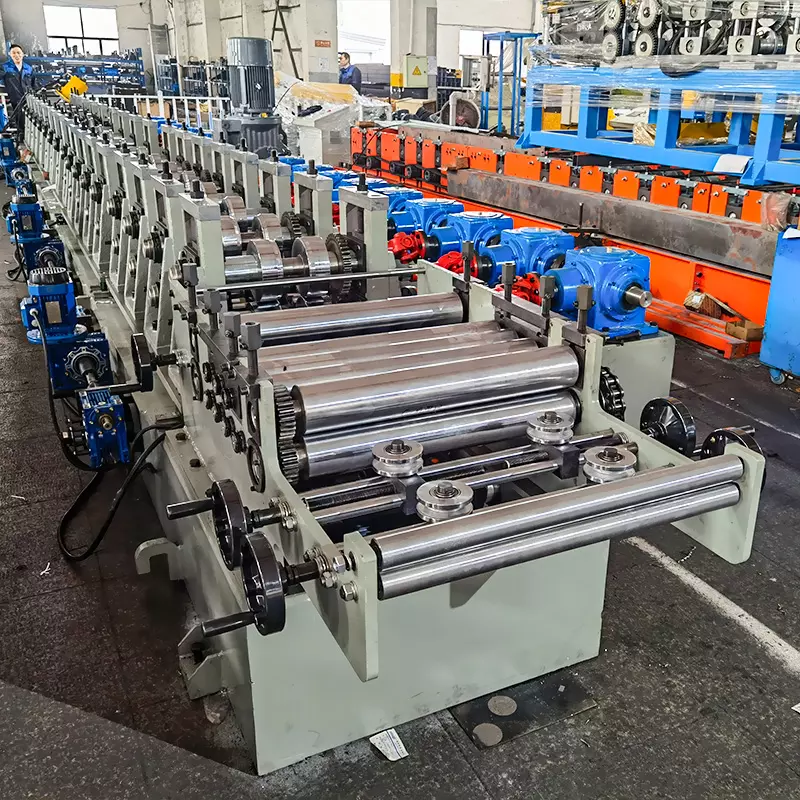
Future Trends and Innovations in Furring Channel Roll Forming
The field of furring channel roll forming continues to evolve, with emerging trends and innovations shaping the future of the industry. Some notable trends include:
Technological Advancements
Advancements in automation, machine control systems, and data analytics are revolutionizing the roll forming process. These technologies enable more precise control, real-time monitoring, and data-driven decision-making, enhancing efficiency and quality.
Sustainable Manufacturing Practices
The construction industry is increasingly focused on sustainability. Furring channel roll forming machines are being designed to minimize material waste, energy consumption, and environmental impact. Integration of eco-friendly materials and recycling capabilities are becoming important features of modern roll forming machines.
Integration with Other Construction Processes
Furring channel roll forming machines are being integrated with other construction processes, such as framing systems and panel production lines. This integration streamlines workflow, reduces production bottlenecks, and enhances overall productivity.
The future of furring channel roll forming promises even greater efficiency, sustainability, and integration with advanced construction practices, propelling the industry toward more innovative and eco-friendly solutions.
FAQs
FAQ 1: What is the difference between furring channels and hat channels? Furring channels and hat channels are terms often used interchangeably to refer to the same product. Both terms describe the metal strips used in construction for leveling, support, and insulation purposes.
FAQ 2: Can a furring channel roll forming machine produce channels of different sizes? Yes, a furring channel roll forming machine can be adjusted to produce channels of various sizes, allowing for customization according to project requirements.
FAQ 3: How long does it take to set up and operate a furring channel roll forming machine? The setup time for a furring channel roll forming machine varies depending on the specific machine model and the complexity of the installation. However, with proper guidance and preparation, the setup can typically be completed within a few hours. Once set up, the machine operates continuously, forming channels at a high production speed.
FAQ 4: Are furring channels suitable for both residential and commercial construction? Yes, furring channels are widely used in both residential and commercial construction. They provide structural support, leveling, and insulation benefits, making them applicable to a range of construction projects.
FAQ 5: Can a furring channel roll forming machine be used for other types of profiles? While a furring channel roll forming machine is specifically designed for producing furring channels, it can be adapted to manufacture other profiles with similar shapes and dimensions. However, the machine’s capabilities may vary depending on the specific design and features it offers.