Introduction
The metal forming industry has witnessed significant advancements over the years, and one of the most remarkable innovations is the Double Stage Cold Roll Forming Machine. This cutting-edge technology has revolutionized the way metal products are manufactured, providing cost-effective, efficient, and precise solutions for various industries.
What is a Double Stage Cold Roll Forming Machine?
A Double Stage Cold Roll Forming Machine is a sophisticated manufacturing equipment used to shape metal sheets into desired profiles or sections. Unlike traditional forming processes that involve heating and bending, cold roll forming operates at room temperature, ensuring dimensional accuracy and minimal material waste.
How Does a Double Stage Cold Roll Forming Machine Work?
The operation of a Double Stage Cold Roll Forming Machine involves a series of sequential processes. Initially, the metal sheet is fed into the machine, passing through two consecutive sets of rollers – the first stage and the second stage. These rollers gradually shape the metal sheet into the desired cross-sectional profile.
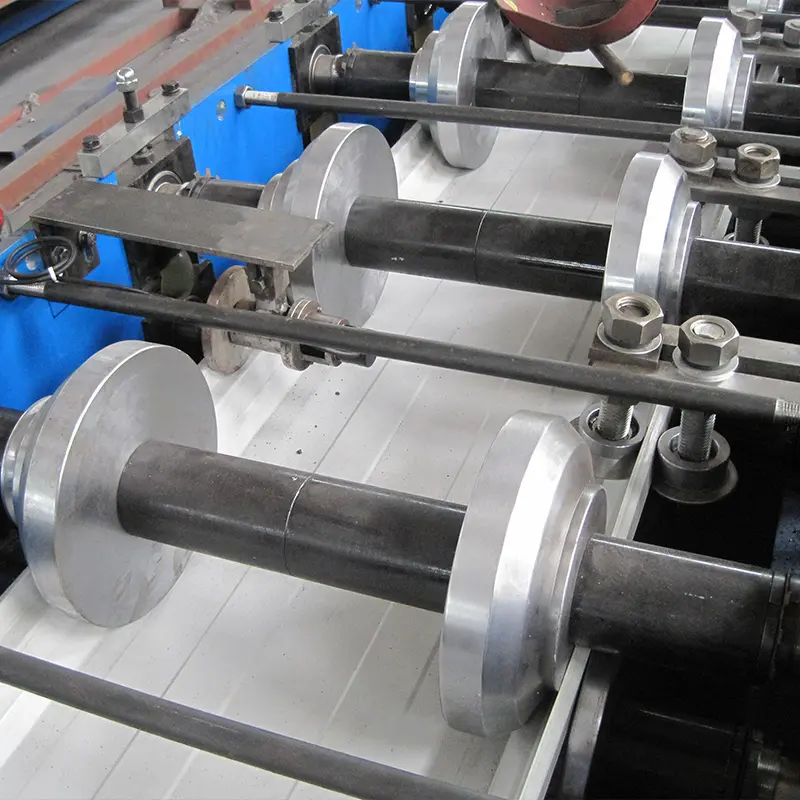
Advantages of Using a Double Stage Cold Roll Forming Machine
The use of a Double Stage Cold Roll Forming Machine offers several advantages, making it a preferred choice for metal fabrication:
- High Production Efficiency: Double stage forming reduces the number of passes required, resulting in faster production rates.
- Cost-Effectiveness: Cold roll forming consumes less energy and eliminates the need for post-forming heat treatments.
- Consistent Quality: Precise control over the forming process ensures uniformity in product dimensions.
- Versatility: The machine can produce complex profiles for diverse applications.
- Material Savings: Minimized material waste due to accurate forming, leading to cost savings and environmental benefits.
Applications of Double Stage Cold Roll Forming Machines
The Double Stage Cold Roll Forming Machine finds extensive use in various industries, including:
Automotive Industry
In the automotive sector, the machine is employed to manufacture components such as roof rails, door beams, and chassis members.
Construction Industry
For the construction industry, the machine produces profiles used in roofing, cladding, and framing systems.
Electrical Industry
In the electrical industry, the machine is utilized to fabricate cable trays, conduits, and other electrical enclosures.
Others
Additionally, the machine caters to applications in furniture manufacturing, aerospace, and consumer goods sectors.
Key Components of a Double Stage Cold Roll Forming Machine
The Double Stage Cold Roll Forming Machine comprises several essential components that contribute to its seamless functioning:
Rollers
The rollers are the heart of the machine, responsible for shaping the metal sheet into the desired profile.
Material Handling System
This system facilitates the smooth and precise movement of metal sheets through the machine.
Cutting System
The cutting system ensures accurate cutting of formed profiles to the desired length.
Control System
The control system regulates the machine’s operations, allowing for easy programming and adjustments.
Lubrication System
To reduce friction and wear, the machine relies on a lubrication system to maintain smooth roller movement.
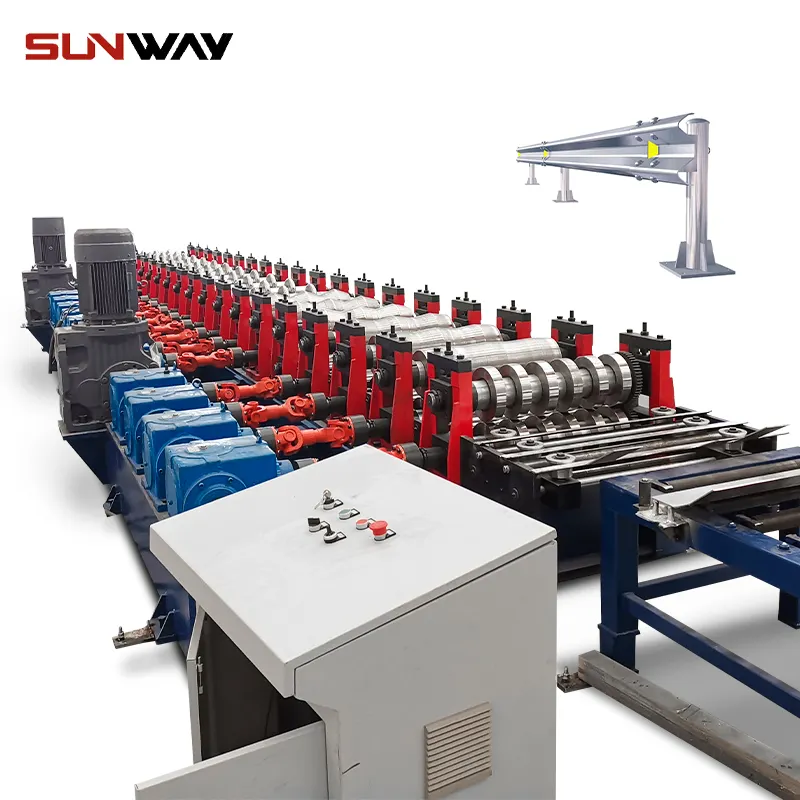
Factors to Consider Before Buying a Double Stage Cold Roll Forming Machine
Before investing in a Double Stage Cold Roll Forming Machine, certain crucial factors should be taken into account:
Production Requirements
Determine the expected production volume and speed requirements to select the right machine capacity.
Material Types and Thickness
Consider the range of materials the machine can process, including their thicknesses and strength.
Machine Configuration and Flexibility
Assess the machine’s flexibility to produce a variety of profiles and whether it allows for easy tooling changes.
Budget and Cost Considerations
Ensure the chosen machine aligns with budget constraints while still meeting the required specifications.
Maintenance and Troubleshooting Tips for Double Stage Cold Roll Forming Machines
To ensure optimal performance and longevity of the machine, regular maintenance and troubleshooting are essential:
Regular Maintenance Checks
Perform scheduled maintenance to identify and address potential issues before they escalate.
Lubrication and Cleaning
Keep the machine’s moving parts well-lubricated and free from debris for smooth operation.
Common Issues and Solutions
Understand and address common problems like misalignment, roller wear, or material jamming.
Safety Precautions When Operating a Double Stage Cold Roll Forming Machine
Operating a Double Stage Cold Roll Forming Machine involves inherent risks, and strict safety precautions must be followed:
Training and Certification
Ensure operators are adequately trained and certified to operate the machine safely.
Personal Protective Equipment (PPE)
Mandatory use of PPE, including gloves, safety glasses, and ear protection, is essential for operators’ safety.
Machine Guards and Safety Features
Install appropriate guards and safety interlocks to prevent accidents and injuries.
Emergency Procedures
Establish clear emergency procedures and conduct regular drills to prepare for unforeseen events.
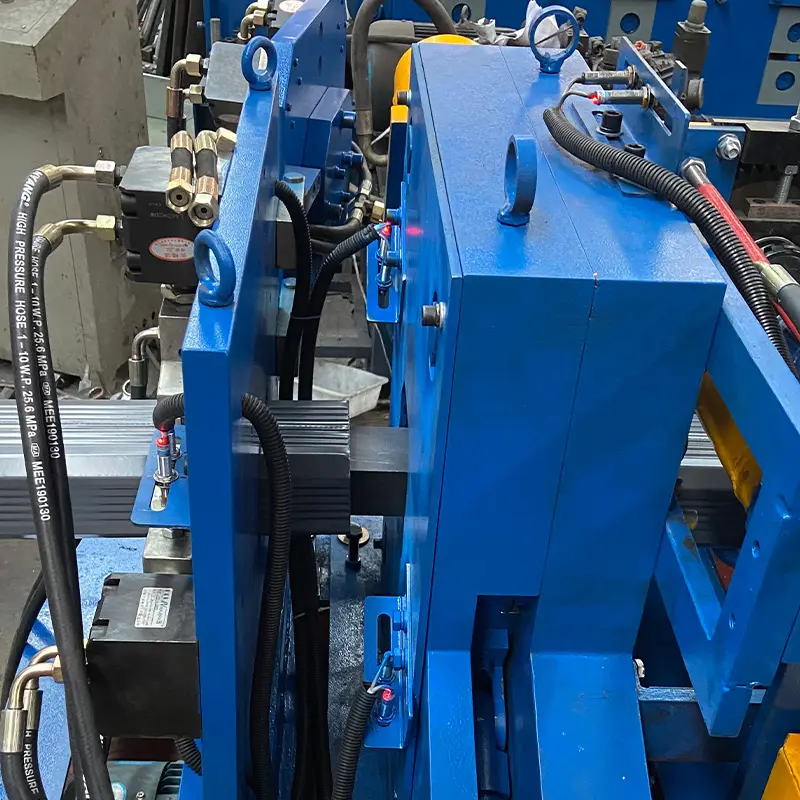
Innovations and Trends in Double Stage Cold Roll Forming Technology
The Double Stage Cold Roll Forming industry continues to evolve with various technological advancements and innovations. Some of the latest trends in Double Stage Cold Roll Forming technology include:
- Digital Integration: Manufacturers are integrating digital technologies into Double Stage Cold Roll Forming Machines, allowing for real-time monitoring, data analysis, and predictive maintenance. This helps in optimizing production processes and reducing downtime.
- Automated Tooling Change: Automation is becoming more prevalent in Double Stage Cold Roll Forming Machines, enabling quick and seamless tooling changes for different product profiles. This enhances the machine’s flexibility and reduces setup times.
- Multi-Material Forming: Advancements in material science have led to the development of high-strength and lightweight materials. Double Stage Cold Roll Forming Machines are now capable of processing a wide range of materials, including steel, aluminum, and composites.
- Energy Efficiency: Manufacturers are focusing on making Double Stage Cold Roll Forming Machines more energy-efficient by optimizing motor drives, reducing friction, and implementing energy recovery systems.
- Smart Control Systems: Intelligent control systems are being implemented to enhance precision and improve product quality. These systems use advanced algorithms to ensure consistent forming and reduce material waste.
Environmental Impact and Sustainability of Double Stage Cold Roll Forming Machines
As industries increasingly prioritize sustainability, Double Stage Cold Roll Forming Machines play a crucial role in promoting environmentally friendly manufacturing practices:
Energy Efficiency
The energy-efficient operation of Double Stage Cold Roll Forming Machines reduces overall energy consumption, contributing to lower carbon emissions and a smaller ecological footprint.
Material Waste Reduction
Precision forming and efficient material utilization result in reduced waste generation. Less material waste not only saves costs but also reduces the demand for raw materials and landfill space.
Recycling and Circular Economy
As Double Stage Cold Roll Forming Machines work with cold-formed metal sheets, the materials retain their original properties, making them highly suitable for recycling and the circular economy approach.
Comparison Between Single Stage and Double Stage Cold Roll Forming Machines
While both Single Stage and Double Stage Cold Roll Forming Machines serve similar purposes, there are notable differences between them:
Single Stage Cold Roll Forming Machines:
- Suitable for simple profiles with limited variations.
- Require multiple passes to achieve the desired profile.
- Lower production efficiency compared to double stage machines.
Double Stage Cold Roll Forming Machines:
- Ideal for complex profiles and diverse product ranges.
- Achieve the desired profile in two consecutive stages, reducing the number of passes and increasing production efficiency.
Case Studies: Successful Implementations of Double Stage Cold Roll Forming Machines
Several industries have adopted Double Stage Cold Roll Forming Machines with remarkable success. Here are some case studies:
- Automotive Component Manufacturing: A leading automotive manufacturer implemented a Double Stage Cold Roll Forming Machine to produce lightweight and high-strength chassis components. This not only reduced the overall weight of vehicles but also improved fuel efficiency.
- Construction Industry: A construction company utilized a Double Stage Cold Roll Forming Machine to produce custom-shaped roofing profiles. The machine’s flexibility allowed them to cater to various architectural designs, providing aesthetically pleasing and structurally sound roofing solutions.
Future Outlook for Double Stage Cold Roll Forming Machines
The future of Double Stage Cold Roll Forming Machines looks promising, with several developments on the horizon:
- Increased Automation: Automation will continue to play a significant role in Double Stage Cold Roll Forming, leading to higher productivity and reduced labor costs.
- Integration of AI and Machine Learning: The integration of AI and machine learning technologies will enable predictive maintenance and further enhance forming precision.
- Sustainable Manufacturing: Double Stage Cold Roll Forming Machines will continue to evolve to meet sustainability requirements, emphasizing energy efficiency and material waste reduction.
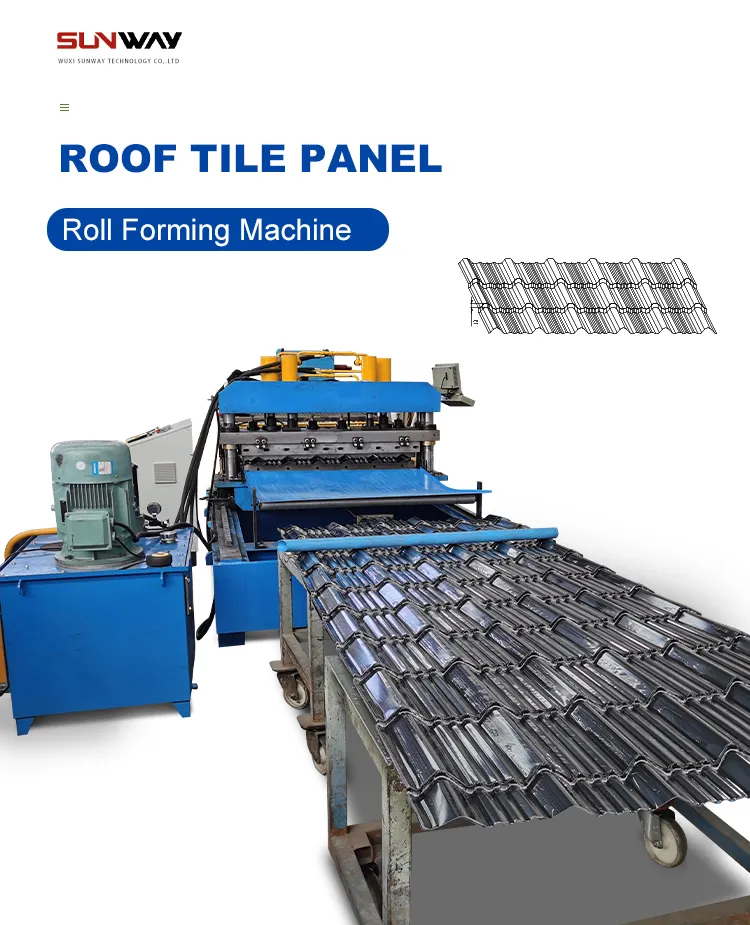
Conclusion
The Double Stage Cold Roll Forming Machine has transformed the metal forming industry, offering a cost-effective and sustainable solution for shaping metal sheets into complex profiles. Its advantages, versatility, and applications across various industries make it a valuable asset for manufacturers seeking efficient and precise metal fabrication solutions.
FAQs
- What is a Double Stage Cold Roll Forming Machine? A Double Stage Cold Roll Forming Machine is a manufacturing equipment used to shape metal sheets into desired profiles at room temperature, providing dimensional accuracy and minimal material waste.
- What are the advantages of using a Double Stage Cold Roll Forming Machine? The advantages of using a Double Stage Cold Roll Forming Machine include high production efficiency, cost-effectiveness, consistent quality, versatility, and material savings.
- In which industries is the Double Stage Cold Roll Forming Machine used? The machine finds applications in the automotive, construction, electrical, and other industries, producing components and profiles for various purposes.
- What are the key components of a Double Stage Cold Roll Forming Machine? The key components include rollers, material handling system, cutting system, control system, and lubrication system.
- How can the environmental impact of Double Stage Cold Roll Forming Machines be minimized? Environmental impact can be reduced through energy-efficient operations, material waste reduction, and embracing recycling and circular economy principles.