Corrugated roofing sheets are a staple in the construction and roofing industry, prized for their durability, versatility, and cost-effectiveness. In this comprehensive guide, we’ll dive deep into the world of corrugated roofing sheets, exploring everything from types and manufacturing processes to installation and maintenance. Buckle up as we take a detailed journey through this essential material!
Overview of Corrugated Roofing Sheets
Corrugated roofing sheets are characterized by their wavy or rippled surface, which provides enhanced strength and rigidity. This design not only improves the structural integrity of the sheets but also offers superior protection against weather elements like rain, snow, and hail. Typically made from materials such as metal, plastic, or fiber-cement, corrugated roofing sheets are widely used in residential, commercial, and industrial applications.
Key Benefits:
- Durability: Corrugated sheets are resistant to impact, corrosion, and UV damage.
- Cost-Effective: Generally more affordable compared to other roofing materials.
- Versatility: Suitable for a range of applications from residential homes to industrial buildings.
- Ease of Installation: Lightweight and easy to handle, making them quick to install.
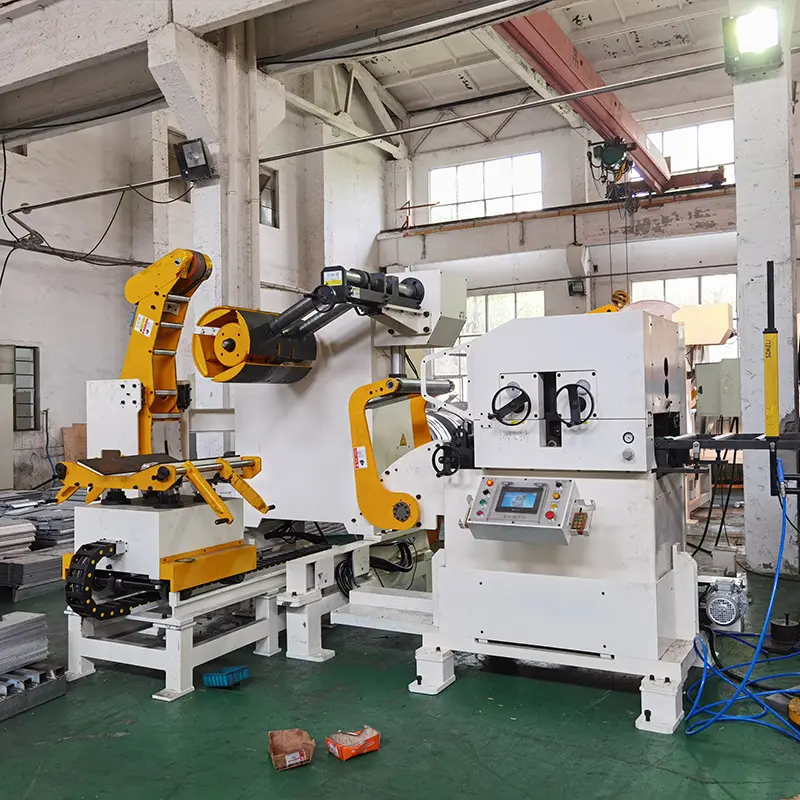
Roll Forming Machine Guide
Roll forming machines are used to create corrugated roofing sheets by shaping a continuous strip of metal into a desired profile. These machines are essential in producing high-quality, consistent sheets efficiently.
How Roll Forming Machines Work:
- Material Feeding: The raw metal strip is fed into the machine.
- Forming: As the strip passes through a series of rollers, it is gradually shaped into the corrugated profile.
- Cutting: The machine cuts the formed strip to the desired length.
- Stacking: The finished sheets are stacked for further processing or shipping.
Key Roll Forming Machine Features:
- Speed: Influences production efficiency.
- Accuracy: Ensures uniformity in sheet dimensions.
- Adjustability: Allows for customization of sheet profiles.
Types of Corrugated Roofing Sheets
Corrugated roofing sheets come in various materials, each offering unique properties suited to different needs. Here’s a breakdown of the most common types:
Metal Corrugated Roofing Sheets
Metal sheets are popular for their strength and longevity. They come in several types, including:
- Galvanized Steel Sheets: Coated with zinc to prevent rust. Ideal for industrial buildings.
- Aluminum Sheets: Lightweight and resistant to corrosion. Perfect for coastal areas.
- Copper Sheets: Highly durable and aesthetically pleasing. Often used for historical or high-end projects.
- Stainless Steel Sheets: Extremely resistant to rust and corrosion, suitable for harsh environments.
Plastic Corrugated Roofing Sheets
Made from polymers, these sheets offer flexibility and weather resistance.
- Polycarbonate Sheets: Known for high impact resistance and thermal insulation. Often used in skylights and greenhouses.
- PVC Sheets: Lightweight and cost-effective. Commonly used in residential applications.
Fiber-Cement Corrugated Roofing Sheets
These sheets combine cement and fibers to create a durable, weather-resistant roofing material.
- Asbestos-Free Fiber-Cement Sheets: A safer alternative to traditional asbestos sheets, used in a variety of applications.
Working Process of Corrugated Roofing Sheets
Creating corrugated roofing sheets involves several key steps, each contributing to the final product’s quality and durability.
1. Raw Material Preparation:
- Metal Sheets: The base material is typically a flat metal strip or coil.
- Plastic Sheets: Polymer resin is prepared and mixed with additives.
- Fiber-Cement: Cement and fibers are mixed and formed into sheets.
2. Shaping:
- Roll Forming: Metal strips are passed through rollers to create corrugated profiles.
- Extrusion: Plastic materials are heated and forced through molds to form corrugated sheets.
- Molding: Fiber-cement mixtures are pressed into molds to achieve the corrugated shape.
3. Cutting and Finishing:
- Sheets are cut to size and undergo finishing processes such as coating or painting to enhance durability and aesthetics.
4. Quality Control:
- Sheets are inspected for defects, measured for consistency, and tested for strength.
Key Components and Their Functions
Understanding the components of corrugated roofing sheets and their functions can help you appreciate their performance and application.
Components of Metal Corrugated Roofing Sheets:
Component | Function |
---|---|
Zinc Coating | Provides rust resistance and prolongs lifespan. |
Metal Core | Offers structural strength and durability. |
Paint Coating | Enhances aesthetics and protects against corrosion. |
Corrugation Profile | Increases rigidity and load-bearing capacity. |
Components of Plastic Corrugated Roofing Sheets:
Component | Function |
---|---|
Polymer Resin | Provides flexibility and impact resistance. |
Additives | Enhance UV resistance and color retention. |
Corrugation Profile | Improves structural strength and insulation. |
Components of Fiber-Cement Corrugated Roofing Sheets:
Component | Function |
---|---|
Cement | Provides strength and weather resistance. |
Fiber Additives | Reinforce the sheet and prevent cracking. |
Corrugation Profile | Adds rigidity and enhances load-bearing capacity. |
Machine Speed and Efficiency
The efficiency of a roll forming machine significantly impacts production rates and quality.
Machine Speed:
Machine Type | Speed (meters/min) |
---|---|
Standard Roll Forming | 10-20 |
High-Speed Roll Forming | 30-50 |
Customized Roll Forming | 20-40 |
Machine Efficiency:
Machine Type | Efficiency (%) |
---|---|
Standard Roll Forming | 85-90 |
High-Speed Roll Forming | 90-95 |
Customized Roll Forming | 80-90 |
Customized Mechanical Parameters
Different applications may require specific mechanical parameters to ensure optimal performance.
Parameters for Customized Machines:
Parameter | Range |
---|---|
Sheet Thickness | 0.3-1.2 mm |
Sheet Width | 600-1200 mm |
Roller Material | Alloy Steel, Carbide |
Forming Speed | 20-50 meters/min |
Cutting Type | Hydraulic, Pneumatic |
Applications of Corrugated Roofing Sheets
Corrugated roofing sheets are versatile and used in a variety of settings.
Applications and Uses:
Application | Use Case |
---|---|
Residential Roofing | Protects homes from weather and provides insulation. |
Industrial Buildings | Used for warehouses, factories, and sheds. |
Agricultural Structures | Covers barns, greenhouses, and animal shelters. |
Commercial Buildings | Applied in offices, shops, and malls for cost-effective roofing. |
Installation, Operation, and Maintenance
Proper installation, operation, and maintenance are crucial for maximizing the lifespan and performance of corrugated roofing sheets.
Installation Guidelines:
Step | Description |
---|---|
Preparation | Ensure the surface is clean and dry. |
Laying Sheets | Align sheets correctly and secure them with fasteners. |
Sealing Joints | Apply sealant to prevent leaks. |
Final Inspection | Check for proper installation and any defects. |
Operation Tips:
Tip | Description |
---|---|
Regular Inspections | Check for damage or wear periodically. |
Cleaning | Remove debris to prevent clogging and damage. |
Repairs | Address any issues promptly to avoid further damage. |
Maintenance Checklist:
Task | Frequency |
---|---|
Inspect Roof | Monthly or after severe weather. |
Clean Surface | Bi-annually or as needed. |
Check Fasteners | Annually, tighten or replace as needed. |
Suppliers and Price Range
Finding a reliable supplier for corrugated roofing sheets can impact both quality and cost.
Suppliers and Pricing:
Supplier | Price Range (per square meter) | Specialization |
---|---|---|
Supplier A | $5-$10 | Metal Corrugated Sheets |
Supplier B | $4-$8 | Plastic Corrugated Sheets |
Supplier C | $6-$12 | Fiber-Cement Corrugated Sheets |
Supplier D | $7-$15 | Custom Orders |
How to Choose a Supplier:
Criteria | Description |
---|---|
Reputation | Look for customer reviews and ratings. |
Product Range | Ensure they offer the type of corrugated sheets you need. |
Pricing | Compare prices and check for any hidden costs. |
Quality Assurance | Verify if they have quality control measures. |
Delivery Time | Check their delivery schedules and terms. |
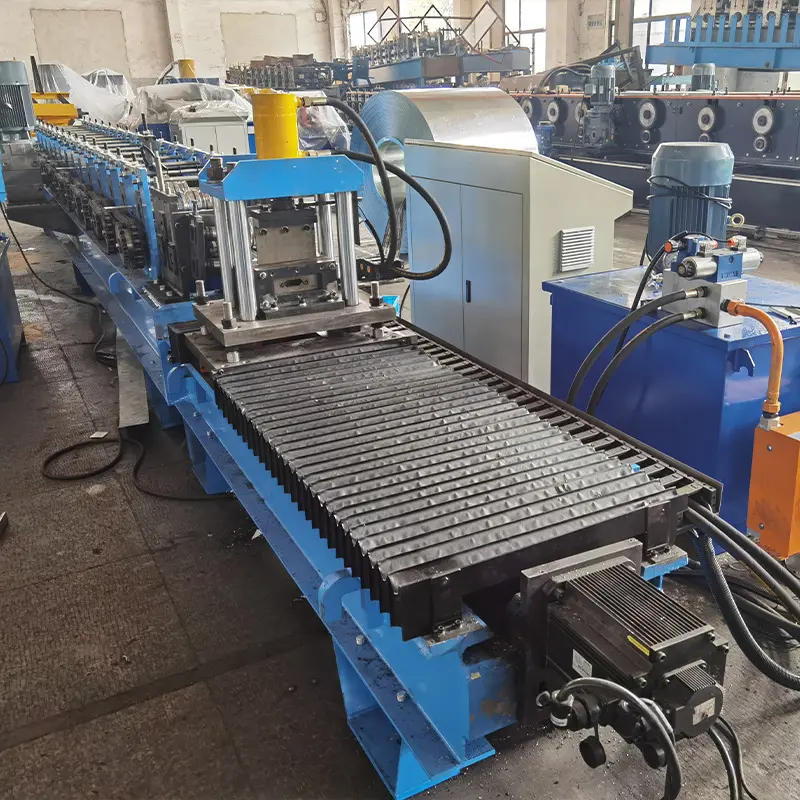
Comparing Pros and Cons of Corrugated Roofing Sheets
When choosing corrugated roofing sheets, consider the pros and cons of each type to make an informed decision.
Metal Corrugated Roofing Sheets:
Pros | Cons |
---|---|
Durability | Can be prone to rust if not properly coated. |
Strength | Heavy, which might require more robust support. |
Aesthetic Options | Available in various colors and finishes. |
Plastic Corrugated Roofing Sheets:
Pros | Cons |
---|---|
Lightweight | Can become brittle over time, especially in extreme temperatures. |
Impact Resistance | May not be as strong as metal alternatives. |
UV Resistance | Generally good, but can degrade over time. |
Fiber-Cement Corrugated Roofing Sheets:
Pros | Cons |
---|---|
Weather Resistance | Heavier and more challenging to install. |
Fire Resistance | Can be more expensive compared to other options. |
Low Maintenance | Requires less frequent upkeep. |
FAQ
Here’s a handy FAQ section addressing common questions about corrugated roofing sheets:
Question | Answer |
---|---|
What are corrugated roofing sheets made of? | They can be made from metal, plastic, or fiber-cement. |
How long do corrugated roofing sheets last? | Metal sheets can last 20-50 years, while plastic and fiber-cement sheets have a lifespan of 10-30 years. |
Can corrugated roofing sheets be painted? | Yes, metal sheets can be painted, and plastic sheets can be colored during manufacturing. |
Are corrugated roofing sheets suitable for all climates? | They are versatile but choose the material based on your climate (e.g., metal for coastal areas, plastic for mild climates). |
How do I install corrugated roofing sheets? | Follow proper guidelines including surface preparation, alignment, and securing with fasteners. |