Introduction
When it comes to manufacturing high-quality corrugated roof panels efficiently, a corrugated roof roll forming machine plays a vital role. This machine automates the process of shaping metal sheets into corrugated profiles, providing numerous benefits in terms of cost, speed, and precision. In this article, we will explore the features, advantages, working principles, and applications of corrugated roof roll forming machines.
What is a Corrugated Roof Roll Forming Machine?
A corrugated roof roll forming machine is a specialized piece of equipment used in the metalworking industry to produce corrugated roof panels. It is designed to shape metal coils or sheets into uniform corrugated profiles with precise dimensions. The machine operates by feeding the metal material through a series of rollers, which gradually bend and form the material into the desired shape.
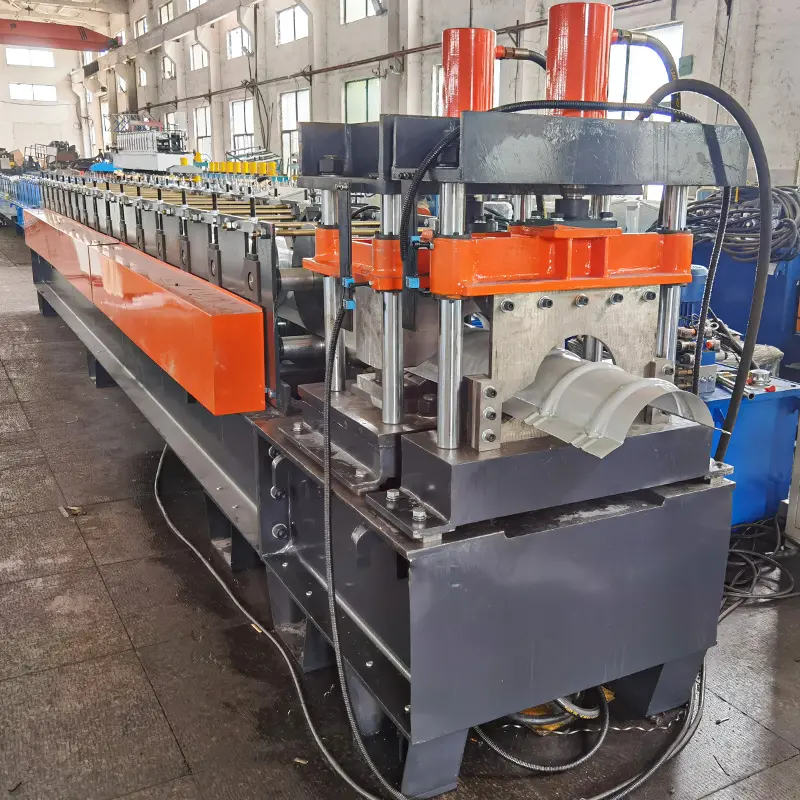
Benefits of Using a Corrugated Roof Roll Forming Machine
Using a corrugated roof roll forming machine offers several advantages over traditional manufacturing methods. These benefits include:
- Cost-Effective Production: Roll forming machines allow for continuous and high-volume production, resulting in lower production costs per unit.
- Versatility: Corrugated roof roll forming machines can produce a wide range of corrugated profiles, providing versatility in design and application.
- Increased Efficiency: The automated process of the machine ensures consistent quality, reduces material waste, and improves overall production efficiency.
- Time-Saving: With high-speed operation and quick setup times, corrugated roof roll forming machines can significantly reduce production lead times.
- Customization Options: Advanced machines offer customization features, allowing manufacturers to create corrugated panels of various lengths, thicknesses, and shapes.
Types of Corrugated Roof Roll Forming Machines
Corrugated roof roll forming machines come in different types, each catering to specific production requirements. The common types include:
1. Single-Layer Corrugated Roof Roll Forming Machine
The single-layer corrugated roof roll forming machine is designed to produce single-layer corrugated panels. It is suitable for applications where a single layer of metal is sufficient for roofing or cladding purposes.
2. Double-Layer Corrugated Roof Roll Forming Machine
The double-layer corrugated roof roll forming machine is capable of producing two different corrugated profiles simultaneously. This type of machine is ideal for scenarios where a combination of two different layers is required.
3. High-Speed Corrugated Roof Roll Forming Machine
High-speed corrugated roof roll forming machines are designed for manufacturers with high-volume production requirements. These machines can produce corrugated panels at an accelerated rate, ensuring optimal efficiency and productivity.
How Does a Corrugated Roof Roll Forming Machine Work?
A corrugated roof roll forming machine follows a sequential process to transform flat metal sheets into corrugated profiles. The general working principles include:
- Material Feeding: The machine takes in metal coils or sheets and feeds them through a set of rollers, ensuring a continuous material flow.
- Roll Forming: The rollers gradually shape the material, bending it into the desired corrugated profile. The number and configuration of the rollers determine the final shape.
- Cutting and Shearing: Once the corrugated profile is formed, the machine can incorporate cutting and shearing mechanisms to trim the panels to the required length.
- Stacking and Packaging: The finished corrugated panels are stacked and packaged for easy transportation and storage.
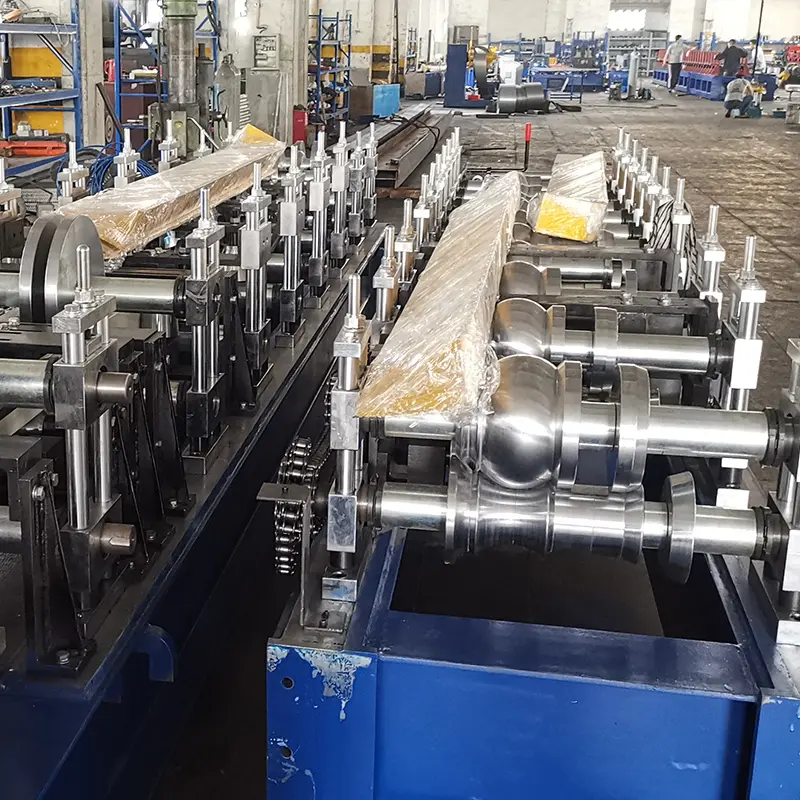
Factors to Consider When Choosing a Corrugated Roof Roll Forming Machine
When selecting a corrugated roof roll forming machine, several factors should be taken into consideration to ensure optimal performance and suitability for specific production needs. These factors include:
- Material Compatibility: The machine should be compatible with the specific metal materials used in the production process, such as galvanized steel, aluminum, or stainless steel.
- Production Speed: Different machines offer varying production speeds, so it’s essential to choose one that matches the required output and production capacity.
- Customization Options: Advanced machines provide flexibility in terms of panel length, width, thickness, and shape, allowing for customization based on project requirements.
- Reliability and Durability: A reliable and durable machine minimizes downtime, ensures consistent production, and provides a longer lifespan.
- Price and Return on Investment: Consider the initial cost of the machine, maintenance expenses, and the expected return on investment over its operational lifespan.
Maintenance and Care for a Corrugated Roof Roll Forming Machine
To ensure the longevity and optimal performance of a corrugated roof roll forming machine, proper maintenance and care are essential. Here are some maintenance practices to follow:
- Regular Cleaning and Lubrication: Keep the machine clean and free from debris. Regularly lubricate the moving parts to prevent friction and ensure smooth operation.
- Inspection and Repair: Conduct periodic inspections to identify any worn-out or damaged components. Replace or repair them promptly to prevent further damage and maintain efficiency.
- Safety Precautions: Follow safety guidelines and ensure operators are trained to operate the machine safely. Regularly inspect safety features and make any necessary adjustments.
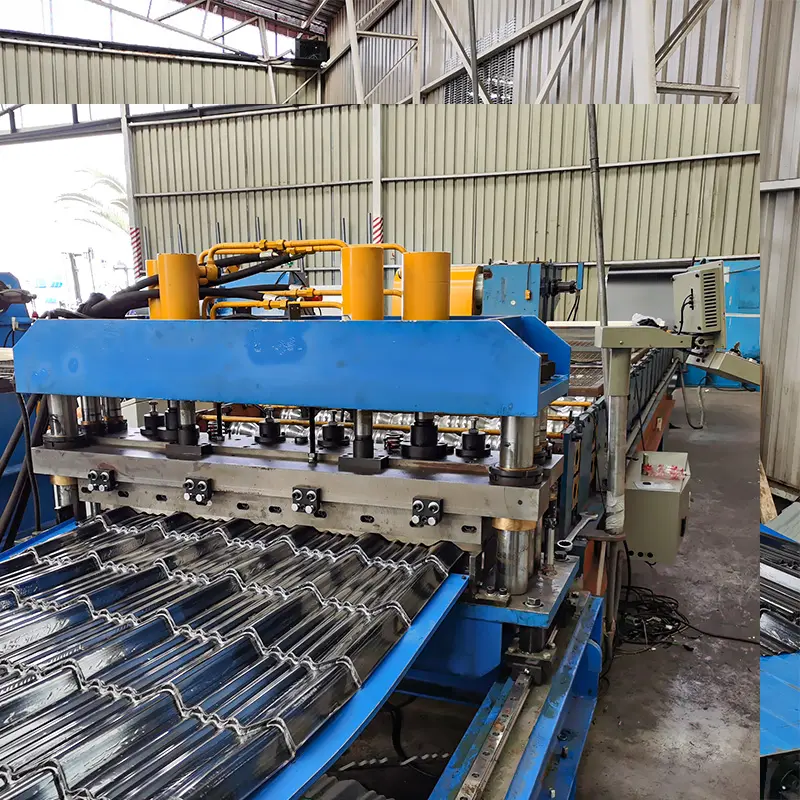
Applications of Corrugated Roof Roll Forming Machines
Corrugated roof roll forming machines find applications in various industries. Some of the common areas where these machines are used include:
- Construction Industry: Corrugated roof panels are widely used in residential and commercial construction projects for roofing and cladding applications.
- Agriculture and Farming: These machines are utilized in the agricultural sector for creating structures such as barns, sheds, and storage facilities.
- Industrial and Commercial Buildings: Corrugated roof panels are popular in industrial and commercial buildings, providing durability and aesthetic appeal.
Advancements in Corrugated Roof Roll Forming Technology
Advancements in technology have contributed to the continuous improvement of corrugated roof roll forming machines. Some notable advancements include:
- Automation and Control: Modern machines feature advanced automation and control systems, allowing for precise control over the forming process and reducing human error.
- Digital Integration: Corrugated roof roll forming machines can now be integrated with digital systems, enabling real-time monitoring, data analysis, and remote control.
- Energy Efficiency: Manufacturers have developed energy-efficient machines that optimize power consumption and reduce environmental impact.
- Advanced Tooling and Roller Designs: Innovative tooling and roller designs enhance the accuracy and quality of the formed corrugated profiles.
- Safety Enhancements: Safety features such as emergency stop buttons, safety guarding, and sensors have been incorporated into modern machines to ensure operator safety.
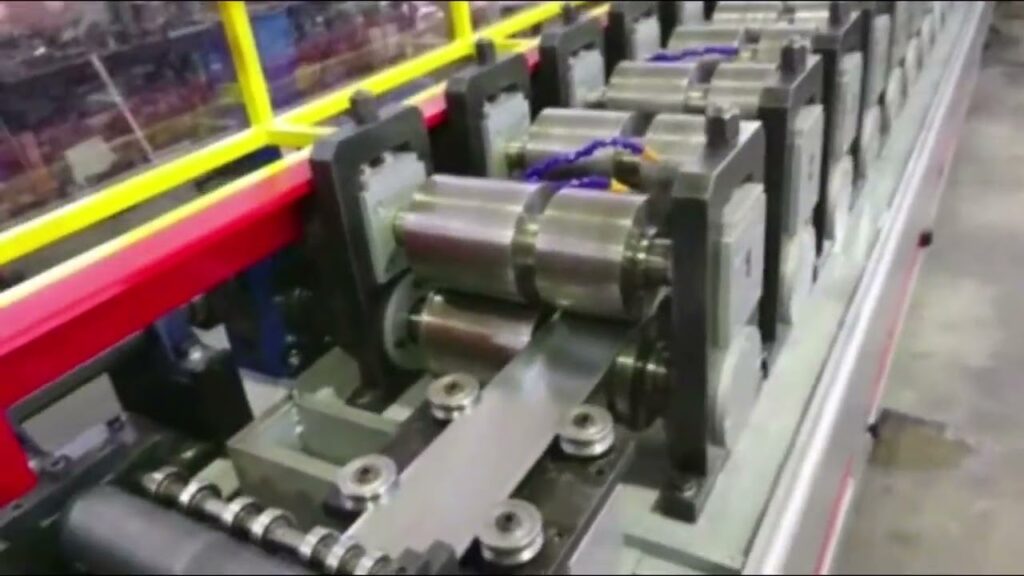
Conclusion
Corrugated roof roll forming machines revolutionize the production of corrugated roof panels by offering cost-effectiveness, efficiency, versatility, and customization options. These machines play a crucial role in the construction, agriculture, and industrial sectors, providing durable and aesthetically pleasing roofing and cladding solutions. With ongoing advancements in technology, corrugated roof roll forming machines continue to evolve, delivering improved performance, reliability, and automation.
FAQs
1. How long does it take to set up a corrugated roof roll forming machine?
The setup time for a corrugated roof roll forming machine depends on various factors such as the complexity of the profile, machine type, and operator experience. Generally, it can take anywhere from a few minutes to a couple of hours to set up the machine.
2. Can a corrugated roof roll forming machine handle different materials?
Yes, corrugated roof roll forming machines can handle various materials such as galvanized steel, aluminum, and stainless steel. However, it is essential to ensure that the machine is compatible with the specific material being used.
3. Are corrugated roof roll forming machines safe to operate?
Corrugated roof roll forming machines are designed with safety features to ensure the operator’s safety. It is important to follow the manufacturer’s guidelines, provide proper training to operators, and regularly inspect and maintain safety features to ensure safe operation.
4. Can a corrugated roof roll forming machine produce customized profiles?
Yes, advanced corrugated roof roll forming machines offer customization options. Manufacturers can adjust parameters such as panel length, width, thickness, and shape to meet specific project requirements.
5. How often should a corrugated roof roll forming machine be maintained?
Regular maintenance is crucial to keep a corrugated roof roll forming machine in optimal condition. It is recommended to perform routine cleaning, lubrication, and inspections. The frequency of maintenance depends on factors such as machine usage, operating conditions, and the manufacturer’s recommendations.