Corrugated iron sheets, an essential material in modern construction, have been a trusted choice for decades. Known for their strength, durability, and versatility, these sheets have found applications across various sectors—from residential roofing to industrial building projects. In this comprehensive guide, we will explore everything there is to know about corrugated iron sheets. We’ll delve into the types available, their manufacturing process, components, applications, installation, and much more. So, if you’re considering using corrugated iron sheets for your next project, read on to make an informed decision!
Overview of Corrugated Iron Sheets
Corrugated iron sheets are thin metal sheets with a wavy or corrugated pattern, enhancing their strength and load-bearing capacity. These sheets are typically made from steel or iron and are coated with zinc, aluminum, or other protective layers to prevent corrosion. The corrugated design not only adds to the structural integrity but also allows for effective water runoff, making them an ideal choice for roofing and cladding.
Key Characteristics:
- Material: Typically made from steel or iron.
- Coating: Zinc, aluminum, or color coatings to prevent rust and corrosion.
- Design: Wavy, corrugated pattern for added strength.
- Applications: Roofing, cladding, fencing, and more.
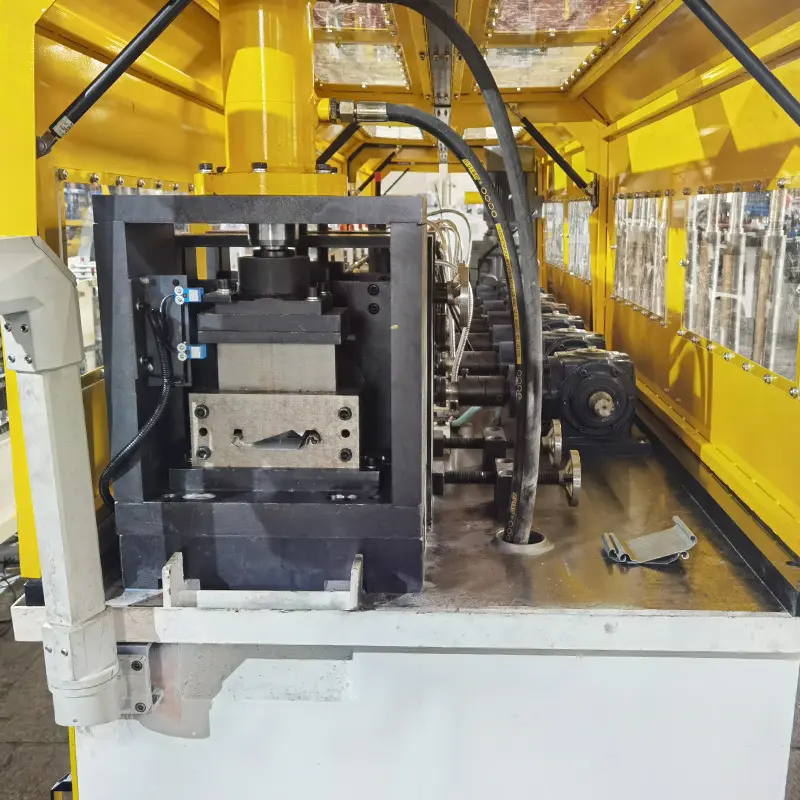
Corrugated Iron Sheets Guide
Choosing the right corrugated iron sheet involves understanding the various options available and their specific uses. This guide will take you through the different types, working processes, and factors to consider when selecting the perfect corrugated iron sheet for your project.
Types of Corrugated Iron Sheets
Corrugated iron sheets come in various types, each tailored for specific applications and environments. Understanding the differences between these types can help you select the best option for your needs.
Type of Corrugated Iron Sheet | Material | Coating | Common Applications | Special Features |
---|---|---|---|---|
Galvanized Corrugated Sheets | Steel | Zinc | Roofing, Fencing | Corrosion-resistant |
Color Coated Corrugated Sheets | Steel/Iron | Paint/Polymer | Roofing, Cladding | Aesthetic appeal, UV-resistant |
Aluminum Corrugated Sheets | Aluminum | None | Industrial Roofing | Lightweight, Rust-proof |
Stainless Steel Corrugated Sheets | Stainless Steel | None | Marine Applications | High corrosion resistance |
Asbestos Corrugated Sheets | Cement & Fibers | None | Old constructions, Fireproofing | Fire-resistant, Not used in new constructions due to health risks |
Fiber Cement Corrugated Sheets | Cement & Fibers | None | Roofing, Wall Cladding | Fire-resistant, Durable |
Bitumen Corrugated Sheets | Bitumen | None | Temporary Structures | Waterproof, Flexible |
Polycarbonate Corrugated Sheets | Polycarbonate | None | Greenhouses, Skylights | Transparent, UV-resistant |
PVC Corrugated Sheets | PVC | None | Carports, Sheds | Lightweight, Easy to install |
Copper Corrugated Sheets | Copper | None | Aesthetic Cladding | Elegant appearance, Durable |
The Working Process of Corrugated Iron Sheets
The production of corrugated iron sheets involves several key steps, ensuring the final product is strong, durable, and fit for purpose. Let’s walk through the process:
- Raw Material Selection: The process begins with selecting high-quality raw materials, typically steel or iron. The chosen metal should have the right balance of strength, flexibility, and corrosion resistance.
- Sheet Formation: The selected metal is passed through a series of rollers that form the distinctive corrugated pattern. The corrugations are created to specific dimensions, with varying depths and pitches depending on the intended use.
- Coating: To protect the metal from rust and corrosion, a coating is applied. Galvanizing (coating with zinc) is the most common method, but other coatings like aluminum or paint are also used depending on the requirements.
- Cutting and Shaping: The coated sheets are then cut to the desired size and shape. Customization options include different lengths, widths, and the ability to add perforations for specific applications.
- Quality Control: Finally, each sheet undergoes a rigorous quality control process to ensure it meets industry standards. Tests include checking for uniformity in corrugation, coating adherence, and overall structural integrity.
Key Components and Their Functions
Understanding the components of corrugated iron sheets and their specific functions can help in selecting the right product and ensuring it meets your project’s needs.
Component | Function |
---|---|
Base Metal (Steel/Iron) | Provides the primary structural strength. |
Corrugation | Adds rigidity and load-bearing capacity. |
Coating (Zinc, Aluminum, Paint) | Protects against rust and corrosion. |
Cutting/Edges | Customizable to fit specific project needs. |
Fasteners (Nails, Screws) | Secure the sheets to the framework. |
Machine Speed and Efficiency
When producing corrugated iron sheets, the efficiency of the machines involved can significantly affect the final product’s quality and the production cost. Here’s a look at the typical machine speeds and efficiencies in the manufacturing process.
Machine Type | Speed (meters per minute) | Efficiency (%) |
---|---|---|
Roll Forming Machine | 20-30 | 85-90 |
Cutting Machine | 15-25 | 80-85 |
Coating Machine (Galvanizing) | 10-20 | 75-80 |
Packaging Machine | 5-10 | 90-95 |
Customized Mechanical Parameters
Customization is often required in construction projects. The table below outlines the mechanical parameters that can be adjusted when ordering corrugated iron sheets.
Parameter | Customization Options |
---|---|
Sheet Thickness | 0.2mm to 1.2mm |
Corrugation Depth | 10mm to 30mm |
Length | Up to 12 meters |
Coating Thickness | 15 microns to 275 microns |
Color Options (for Coated Sheets) | RAL colors, Custom colors |
Applications of Corrugated Iron Sheets
Corrugated iron sheets are incredibly versatile and are used in a wide range of applications across different industries. Here are some of the most common uses:
Application | Details |
---|---|
Residential Roofing | Popular for roofing houses due to durability and water resistance. |
Industrial Roofing | Used in factories, warehouses, and other large structures. |
Cladding | Provides aesthetic and protective outer layers for buildings. |
Fencing | Durable and easy-to-install solution for property boundaries. |
Sheds and Outbuildings | Ideal for creating quick, weather-resistant structures. |
Greenhouses | Polycarbonate sheets used for light transmission in greenhouses. |
Skylights | Transparent sheets allow natural light while providing protection. |
Temporary Structures | Bitumen and PVC sheets often used for temporary shelters. |
Water Tanks | Corrugated sheets are sometimes used in constructing water tanks. |
Decorative Cladding | Copper and color-coated sheets used for decorative purposes. |
Installation, Operation, and Maintenance
Proper installation, operation, and maintenance are crucial to ensure the longevity and performance of corrugated iron sheets. Here’s a guide to help you through these processes.
Process | Description |
---|---|
Installation | Ensure proper alignment, use the right fasteners, and follow manufacturer guidelines. |
Operation | Once installed, check for any immediate signs of stress or misalignment. |
Maintenance | Regularly inspect for rust, recoat if necessary, and clean debris from the roof. |
Suppliers and Price Range Details
Finding the right supplier for your corrugated iron sheets can make a significant difference in cost and quality. Here’s a list of well-known suppliers and their typical price ranges.
Supplier | Location | Price Range (per sq. meter) | Specialties |
---|---|---|---|
ABC Roofing | USA | $7 – $15 | Galvanized and Color Coated Sheets |
BlueScope Steel | Australia | $10 – $20 | High-quality Steel and Aluminum Sheets |
Tata Steel | India | $5 – $12 | Durable and Affordable Options |
ArcelorMittal | Global | $8 – $18 | Extensive Range of Steel Products |
Nippon Steel | Japan | $9 – $17 | Innovative Coatings and Designs |
POSCO | South Korea | $8 – $16 | Advanced Technology in Steel Production |
JSW Steel | India | $6 – $14 | Cost-effective and Durable Sheets |
ThyssenKrupp | Germany | $10 – $20 | High Strength and Customized Options |
China Steel Corporation | Taiwan | $7 – $15 | Competitive Pricing and Wide Availability |
Gerdau | Brazil | $6 – $14 | Sustainable and Recycled Steel Products |
How to Choose a Supplier
Choosing the right supplier for your corrugated iron sheets is critical to ensure you get the best product for your money. Here are some factors to consider:
- Reputation: Look for suppliers with a solid reputation in the market. Reviews and testimonials from previous customers can provide valuable insights.
- Product Range: Ensure the supplier offers a variety of options, including different materials, coatings, and customization possibilities.
- Pricing: Compare prices across different suppliers, keeping in mind that cheaper isn’t always better. Consider the balance between cost and quality.
- Customer Support: Good customer support can make a significant difference, especially if you need advice or encounter issues during installation.
- Delivery and Logistics: Check if the supplier can deliver to your location and what their shipping times are like. Timely delivery can keep your project on schedule.
- Certifications: Ensure the supplier’s products meet industry standards and are certified for quality.
Comparing Pros and Cons
Every product has its advantages and limitations, and corrugated iron sheets are no different. Here’s a comparison to help you weigh your options.
Aspect | Advantages | Limitations |
---|---|---|
Durability | Long-lasting, especially with proper coating | Susceptible to rust if not coated properly |
Cost | Affordable compared to other roofing materials | Prices vary depending on the material and coating |
Installation | Relatively easy to install | Requires careful handling to avoid damage |
Aesthetics | Available in various colors and finishes | May not suit all architectural styles |
Maintenance | Low maintenance, especially with coatings | Regular checks required to prevent corrosion |
Environmental Impact | Recyclable materials | Energy-intensive production process |
Weather Resistance | Excellent water runoff and wind resistance | Can be noisy during rain or hail |
FAQs
Here are some frequently asked questions about corrugated iron sheets, answered in a tabular format for easy reference.
Question | Answer |
---|---|
What is the lifespan of corrugated iron sheets? | With proper maintenance, they can last up to 50 years. |
Can corrugated iron sheets be painted? | Yes, they can be painted, especially if they are pre-coated or treated for paint adherence. |
Are corrugated iron sheets environmentally friendly? | They are recyclable, but the manufacturing process can be energy-intensive. |
How do I prevent rust on corrugated iron sheets? | Opt for galvanized or coated sheets, and ensure regular maintenance to catch any early signs of corrosion. |
What is the best material for coastal areas? | Stainless steel or aluminum corrugated sheets are best due to their high corrosion resistance. |
Can corrugated iron sheets be used for walls? | Yes, they are often used for cladding and walling in addition to roofing. |
Do corrugated iron sheets require insulation? | Insulation is recommended, especially in areas with extreme temperatures, to prevent heat loss or gain. |
What is the standard size of corrugated iron sheets? | Sizes can vary, but a common size is 6 feet in length and 2.5 feet in width. |
Are corrugated iron sheets fire-resistant? | Metal sheets are generally fire-resistant, but the level of resistance depends on the material and coating. |
How are corrugated iron sheets fixed to the roof? | They are usually fixed with nails or screws, with washers to ensure a tight seal. |
Conclusion
Corrugated iron sheets are a reliable, versatile, and cost-effective solution for various construction needs. Whether you’re roofing a home, cladding a building, or setting up a temporary structure, these sheets offer unmatched durability and weather resistance. By understanding the types, components, working processes, and installation methods, you can make the best choice for your specific project. Remember, choosing the right supplier and maintaining your corrugated sheets properly will ensure they serve you well for years to come.
In the world of construction materials, few options offer the blend of affordability, strength, and longevity that corrugated iron sheets do. They may not be the most glamorous material, but they certainly get the job done—reliably and effectively.