ক wall sheet roll forming machine is an essential equipment for producing wall panels, roof panels, C & Z purlins and other structural building components from metal coils. This guide provides a comprehensive overview of wall sheet roll forming technology, types of machines, key specifications, applications, installation and maintenance requirements, supplier selection factors, comparative analysis and FAQs.
Overview of Wall Sheet Roll Forming
Roll forming is a continuous bending operation that forms metal coils into customized longitudinal profiles through a series of sequential rolling stands. Wall sheet roll formers transform flat metal sheets into finished wall, roof and structural framing products for buildings.
Core Advantages of Roll Formed Wall Sheets
- Highly customizable profiles
- Superior structural strength
- Lightweight compared to other wall materials
- Quick and efficient production
- Consistent quality and dimensional accuracy
- Cost-effective for mass production
- Minimal waste generation
Types of Profiles Produced
Wall sheet roll forming machines can produce various standard and custom profiles as per application requirements:
Table 1: Common Roll Formed Wall Sheet Profiles
Profile Type | Description |
---|---|
Trapezoidal roof & wall sheets | Wavy corrugated profile, popular for cladding |
Sinusoidal roof & wall sheets | Smooth curved corrugations for aesthetic finish |
Standing seam roof sheets | Interlocking panels with raised seams |
Ribbed wall sheets | Narrow raised longitudinal ribs for strength |
Structural C & Z purlins | Weight-bearing frame components |
Architectural wall panels | Decorative fluted, curved, textured sheets |
Perforated wall sheets | Holes for ventilation and sound absorption |
Key Components of a Wall Sheet Roll Former
The main sections of a typical wall profile roll forming machine include:
Table 2: Components of a Wall Sheet Roll Forming Machine
Component | Description |
---|---|
আনকোয়লার | Holds and rotates the metal coil |
ডিকয়লার | Straightens the strip from the coil |
Feeder | Feeds the strip at a set speed |
Punching Unit | Punches holes if required for fastening |
Forming stations | Progressive bending and profiling stands |
Cutting unit | Cuts sheets to specified length |
Stacker | Collects formed sheets automatically |
PLC control | Controls machine parameters and interlocks |
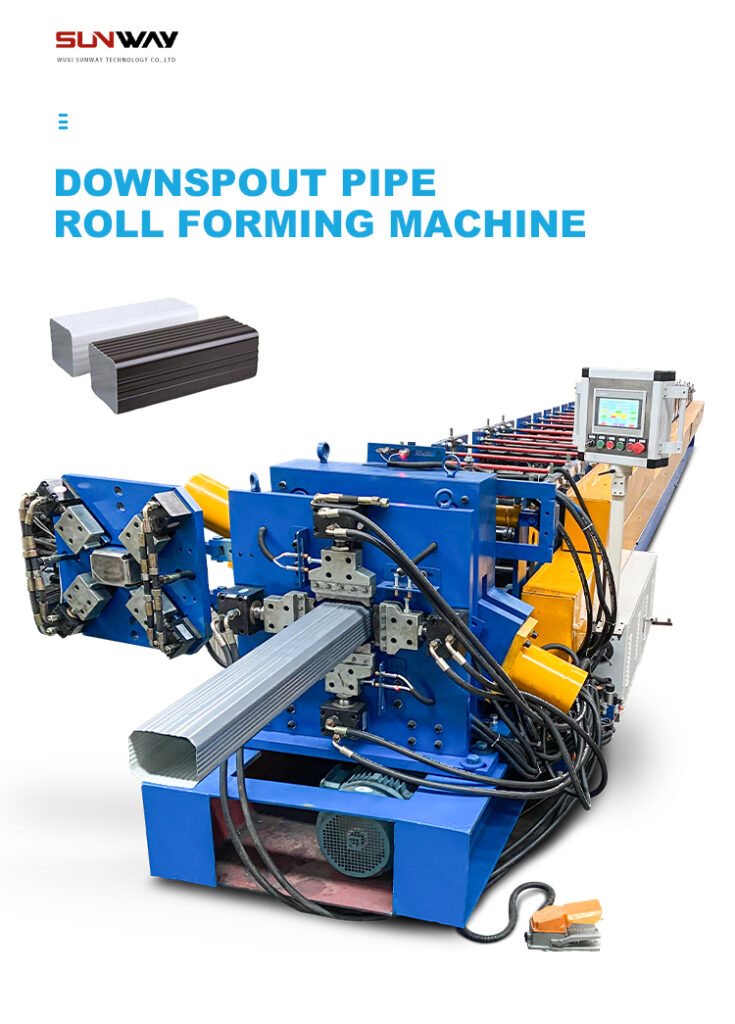
Specifications of Wall Sheet Roll Formers
Key technical parameters and dimensional factors determine the production capacity, profile capabilities and performance of wall sheet roll forming machines.
Production Capacity Factors
Table 3: Technical Factors Affecting Production Capacity
Parameter | Typical Range |
---|---|
Forming speed | 10 – 25 m/min |
Working width | 1000 – 2500 mm |
Sheet thickness | 0.3 – 2.0 mm |
Main drive power | 5.5 – 15 kW |
Cutting length | 500 – 6000 mm |
Material yield strength | 250 – 550 MPa |
Higher production speeds, wider coil widths, thinner gauges and lower yield strength materials allow faster forming and increased output.
Profile Dimensional Factors
Table 4: Technical Limits for Profile Shapes
Dimension | Typical Range |
---|---|
Profile depth | 10 – 150 mm |
Wave height | 15 – 115 mm |
Flange width | 45 – 300 mm |
Rib width | 10 – 45 mm |
Bend radius | 2 – 8 mm |
Punching diameter | 10 – 20 mm |
Deeper and more complex shapes may require heavier machines and multi-pass processes.
Design and Construction Parameters
Table 5: Standard Machine Design Features
Feature | Description |
---|---|
Forming stations | 10 – 20 stands for sequential bending |
Roller types | Vertical, horizontal, oblique, edge rollers |
Roller material | Alloy steel or hard chrome plated |
Roller diameter | 100 – 160 mm |
Roller adjustment | Keyed shafts, screw down, auto actuators |
ফ্রেম | All-welded steel construction |
Strip guidance | Roller guides, strip edge shielding |
Safety | Emergency stops, overload protection |
Machine size | Length 15 – 40 m; Height 2 – 2.5 m |
Noise level | ≤80 db with acoustic covers |
Applications of Wall Sheet Roll Forming Machines
Wall sheet roll forming machines produce panels and profiles from steel, aluminum and other metals for the following structural applications:
Table 6: End Use Applications of Roll Formed Wall Sheets
আবেদন | Description |
---|---|
Wall cladding | Trapezoidal, ribbed and corrugated sheets for exterior walls |
Roofing | Standing seam, corrugated roof panels |
Interior walls | Decorative roll formed sheets for partitions |
Structural framing | Purlins, girts, eaves for buildings |
Agricultural buildings | Low cost roofing and walls for farms |
Prefabricated buildings | Faster construction with premade panels |
Container construction | Assembling homes, offices from roll formed sheets |
Solar structures | Structural profiles for PV panel mounts |
Acoustic barriers | Sound dampening perforated sheets |
Key advantages of roll formed panels in these applications include lightweight, high strength, quick installation, design flexibility, corrosion resistance and longevity.
Installation and Operation
Proper installation and operation practices are vital for optimum performance of wall sheet roll forming lines.
Installation Guidelines
- Foundations should be concrete or sturdy steel structures
- Leveling and alignment of forming stands is critical
- Roller adjustment should be precise with uniform gaps
- Test run to verify profiles before production
- Safety barriers, guards and fences should be in place
Operation and Maintenance
Table 7: Operation and Maintenance Requirements
Activity | Frequency |
---|---|
Inspect formed profiles | Each sheet or shift |
Check roller adjustment | Weekly |
Verify strip guidance | Daily |
Lubricate bearings | Monthly |
Inspect chains, gears, sprockets | Quarterly or 5000 hours |
Replace worn rollers | After 100,000 cycles or as needed |
Calibrate sensors, actuators | As needed |
Update machine software | As needed for upgrades |
Regular preventive maintenance improves product quality and avoids unplanned downtime.
Supplier Selection Considerations
Choosing the right roll forming machine supplier is key to getting capable and reliable equipment for wall sheet production.
Table 8: Key Criteria for Evaluating Roll Former Suppliers
Parameter | Importance |
---|---|
Technical expertise | High |
Customization capabilities | High |
Build quality and precision | High |
Line integration experience | Medium |
Local presence and support | Medium |
Production capacity | Low |
International experience | Low |
Cost competitiveness | Medium |
In addition to technical parameters, factors like responsiveness, transparency, lead time, payment terms, warranties and after-sales service should be evaluated during supplier selection.
Comparative Analysis
Machine Type | Advantages | Limitations |
---|---|---|
Mechanical | Simple and robust Easy maintenance Proven reliability | Limited forming capacity Lower precision Slower speed |
Servo motor | High speed and accuracy Quick changeovers Advanced automation | Higher cost Complex programming Sensitive sensors |
হাইড্রোলিক | Powerful forming force Deep drawing ability | Oil maintenance Slower than servos Environment risks |
Cost Analysis
Table 9: Price Range of Wall Sheet Roll Forming Machines
Capacity | Price Range |
---|---|
Small (up to 30,000 tons/year) | $50,000 – $150,000 |
Medium (up to 100,000 tons/year) | $150,000 – $350,000 |
Large (above 100,000 tons/year) | $350,000 – $1,000,000 |
Cost depends on speed, width, material thickness range, profile complexity, automation level and customization requirements. Local support and transportation costs also affect pricing.
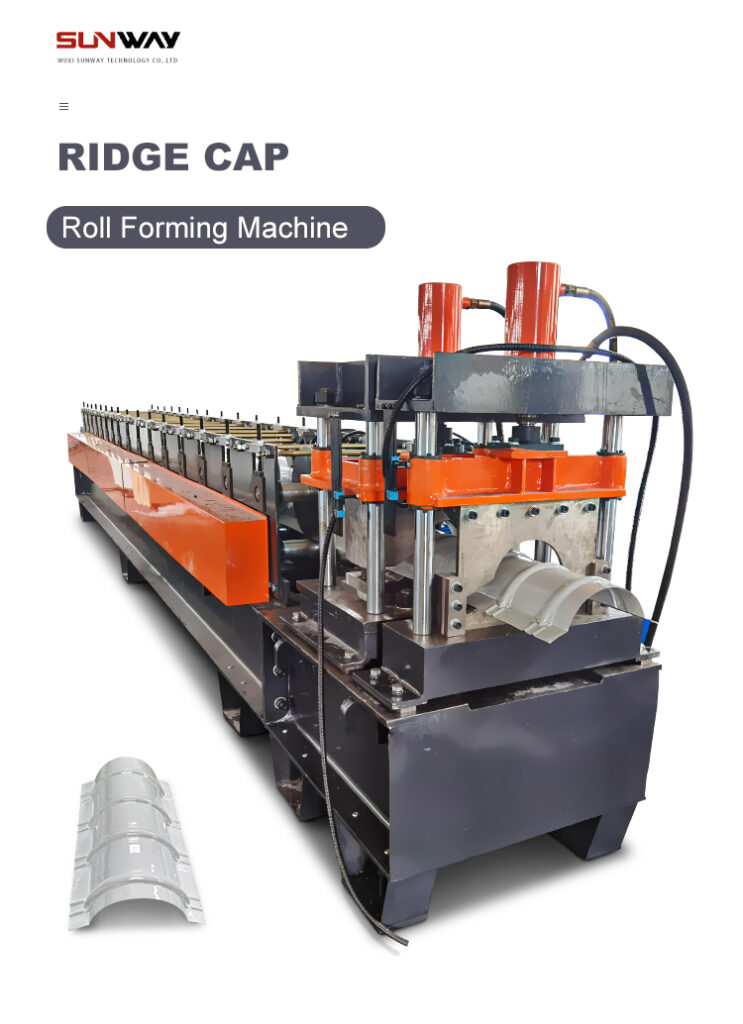
FAQs
What materials can be roll formed into wall sheets?
- Cold rolled steel, galvanized steel, stainless steel, aluminium sheets up to 2 mm thickness. Not recommended for thicker plates above 3 mm.
What should be the flatness and surface finish of the coil?
- Coil flatness tolerance up to 3 mm per meter width is acceptable. Surface defects may mark the finished profiles.
What are the power requirements?
- Wall sheet roll formers typically need 15 – 30 kW installed power depending on speed and capacity. Three phase 415 V AC supply is preferred.
How to adjust the roll forming stands?
- Stands are adjusted by laser alignment or numerically controlled actuators. Keyed shafts, screwn down and shims allow manual adjustment along with Gauging stations.
What safety measures are required?
- Emergency stop buttons, overload protection, strip containment guides, safety fences and light curtains to stop on obstruction. Acoustic covers reduce noise.
What digital controls are included?
- PLC or HMI touchscreen controls for production monitoring, parameters adjustment and automated sequencing of machine. Servo systems allow precision control.
What is the normal maintenance routine?
- Daily cleaning, weekly lubrication and inspection, monthly sensor calibration and quarterly gearbox oil change are typical maintenance tasks. Rollers require replacement based on wear.
In summary, wall sheet roll forming machines offer efficient, customized production of metal wall panels and framing components for buildings. This guide has provided a holistic overview of the technology, process, specifications, applications, operation, supplier selection and costs to inform purchase and use of this versatile equipment.