Trim roll forming is a metalworking process that forms metal coils into customized profiles with trim cuts. Trim roll forming machines are used to create trim profiles for various applications like building construction, infrastructure, transportation, packaging, and more. This comprehensive guide provides a detailed overview of trim roll forming machine types, main components, technical specifications, applications, advantages, and more.
Overview of Trim Roll Forming
Trim roll forming is a specialized sheet metal fabrication process used to form metal coil stock into customized trim profiles. It combines conventional roll forming with additional trim cutting stations integrated into the line.
Roll forming shapes flat sheet metal stock into profiles by progressively bending the material through consecutive pairs of contoured rolls. Trim roll forming takes this a step further by cutting the edges and creating finished parts with tight tolerances.
The main advantages of trim roll forming are:
- High production rates and low cost per unit compared to other cutting methods
- Flexibility to create customized and complex trim shapes
- Consistent quality and dimensional accuracy better than +/- 0.5 mm
- Minimal scrap waste since trim cuts are made in-line
- Applicable to a wide range of metals like steel, aluminum, copper, brass
Trim roll forming machines are available in different configurations to produce straight or coiled profiles at rates over 100 meters per minute.
The addition of trimming and slitting stations allows creating finished parts without any secondary operations. This makes trim roll forming ideal for high-volume production of metal trim parts used in construction, infrastructure, transportation, packaging, appliance manufacturing and more.
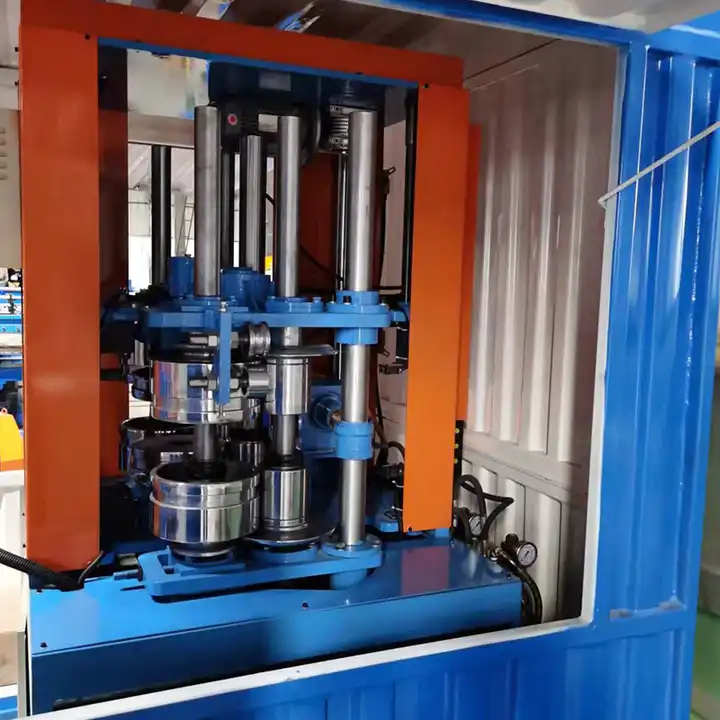
Types of Trim Roll Forming Machines
Trim roll forming machines can be categorized based on production line configuration, number of forming stations, type of cutting method and profile shape capabilities:
Based on Production Line
- In-line machines: All forming and cutting operations are integrated into one continuous production line. This allows higher outputs with easier part transfer.
- Near-line machines: Forming line is separated from the cutting line. Formed profiles are manually or automatically transferred to the trim line. Provides more flexibility for profile shapes.
- Off-line machines: Forming and trimming are done on completely independent lines in separate areas. Lower output but allows forming standard profiles and custom trimming.
Based on Forming Stations
- Fixed cut-length machines: Cut profile to predefined lengths after forming. Used for high-volume production of standard length parts.
- Variable length machines: Cut profiles on demand to any length within machine capacity. Preferred for low to medium volumes.
Based on Cutting Method
- Punching: Hydraulic or servo-electric punches make holes or notches at preset positions along the profile. Allows extensive customization.
- Shearing: Rotary flying cutters slice profiles at an angle to required length. Faster than punching but with shape limitations.
- Sawing: Circular saw blades cut profiles perpendicular to length. Produces quality trim edges but slower than shear trimming.
- Laser cutting: A laser beam makes trim cuts by melting metal locally. Allows complex contours without dies but has lower throughput.
Based on Profile Shape Capabilities
- Fixed profile: Dedicated roll sets produce the same pre-designed profile repeatedly in high volumes. Lower cost, faster changeovers.
- Adjustable profile: Roll sets have some flexibility to adjust dimensions and create a limited range of similar profiles.
- Universal profile: Fully modular forming stations with quick change tooling allow producing any custom profile within machine capacity. Most flexible but higher cost.
Main Components of Trim Roll Forming Lines
Trim roll forming lines comprise feeding equipment, forming stations, cutting zones, and exit conveyors.
The main components are:
- Decoiler: Feeds flat sheet metal coil stock into the roll former. Includes decoiler mandrel, coil car, threader, straightener, and feeder.
- Forming stations: Progressively bend and shape the strip through consecutive roll stands. Contains top and bottom rolls, housings, gearing, drive, controls.
- Punching and cutting zone: Punch, shear or saw profiling tools make trim cuts to the formed section. Contains cutters, strippers, tool holders, controls.
- Exit conveyor: Transports finished trim parts out of the system. Can include part counting, stacking, bundling equipment.
- Safety equipment: Light curtains, guarding, interlocks ensure operator safety during automated production.
- Controls: PLC automates and monitors line speed, feeds, forms, cuts, exit to optimize production. HMI allows monitoring and parameter changes.
Other components like loop controls, straigteners, lubrication systems support quality high-speed production on trim roll forming machines.
Typical Specifications of Trim Roll Forming Machines
Trim roll formers are available in a wide range of sizes and specifications to match production requirements:
Specification | Typical Values |
---|---|
Line speed | 10 – 120 m/min |
Strip width capacity | 50 – 2100 mm |
Strip thickness range | 0.3 – 4 mm |
Min. profile length | 300 mm |
Max. profile length | Unlimited with cut-to-length |
Length tolerance | +/- 1 mm |
Hole punching tolerance | +/- 0.5 mm |
Hole size range | 8 – 100 mm dia. |
Installed power | 15 – 150 kW |
Noise level | <85 dB |
Production environment | 10 – 40°C, <90% humidity |
Machines can be supplied in standard designs or custom engineered to specification. Capacities up to 2500 mm width and 6 mm thickness are possible for specialty applications.
Applications of Trim Roll Formed Profiles
Trim roll forming allows cost-efficient mass production of finished metal trim parts. Typical applications include:
Building and Construction
- Window and door frames
- Curtain walling, cladding, façades
- Roofing and flashing
- Interior partition frames
- Lighting troffers, downlighters
- Decorative molding and trim
- Balustrades, handrails
Infrastructure and Transportation
- Road barrier strips
- Crash barriers
- Rail coach panels
- Truck and trailer panels
- Shipbuilding panels
Storage, Racking and Shelving
- Upright columns
- Shelf support braces
- Cross beams
- Gondola shelving
- Decorative support trims
Furniture
- Desk and cabinet frames
- Drawer channels and runners
- Chair and table legs
- Decorative trims
Electrical and Appliances
- Motor and pump housings
- Electrical enclosures and chassis
- Control panels
- Refrigerator liners
- Oven and AC ducts
- Drum and cylinder cladding
Other Applications
- Signage and displays
- Playground equipment
- Agricultural equipment
- Automotive components -defense applications
Nearly any application requiring linear trim profiles can benefit from trim roll forming for consistent quality at high outputs.
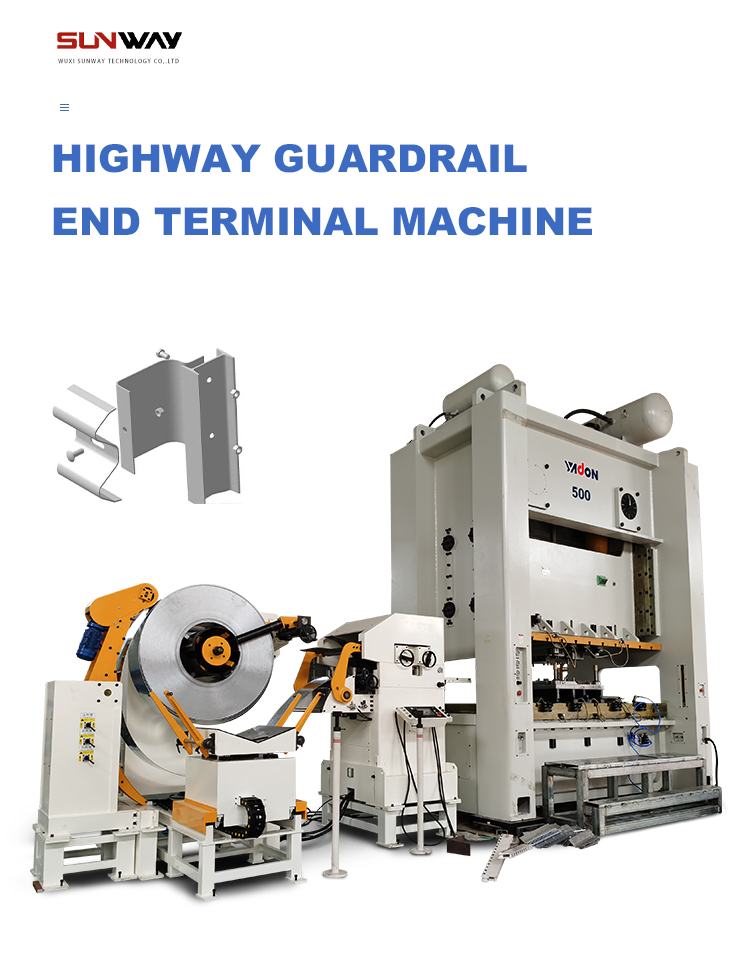
Benefits and Advantages of Trim Roll Forming
Some of the main benefits offered by trim roll forming machines are:
- High production speed – Up to 100+ meters per minute
- Low cost – High volumes reduce cost per piece significantly
- Material savings – Low scrap loss compared to other cutting methods
- Flexibility – Various profiles possible from same line
- কাস্টমাইজেশন – Unique shapes achievable via tooling design
- Consistency -parametric control of forming guarantees uniformity
- Automation – 24/7 untended production after setup
- Simplicity – Coils to finished parts in one process
- Quality – Accuracy better than 1 mm on all features
- Scalability – Lines available from 1 m up to 3 m width
- Reliability – Robust industrial construction for heavy duty operation
When high volumes of precision metal trim parts are needed, trim roll forming provides an efficient and cost-effective fabrication solution.
Limitations of Trim Roll Forming
While offering many benefits, trim roll forming also has some limitations:
- High initial tooling cost – Dies, punches and custom roll sets require upfront investment
- Setup time – Tool changes may take several hours for profile changeovers
- Repeat orders – Best suited for continuous high-volume production, not prototypes or small batches
- Shape constraints – Extensive bending and hemming may exceed roll former capacity
- Thickness limits – Typically 0.5 to 6 mm strip thickness range
- Material options – Mainly carbon steel, aluminum and stainless steel
- Secondary operations – May need additional steps like welding, hardware insertion, painting
- Precision limits – Tolerances around ±0.5 mm, not for fine precision parts
For short run or highly complex components, other processes like CNC punching, laser/waterjet cutting may be more suitable.
Step-by-Step Process of Trim Roll Forming
A typical trim roll forming process consists of:
1. Decoiling
- Sheet metal coils loaded onto powered decoiler
- Threading strip through the roll former
- Using loop control and straightener for stable unwinding
2. Feeding
- Feed rolls pull strip through stations at set speed
- Servo feed motors synchronized to roll forming
- Accumulator tower stabilizes material flow
3. Roll forming
- Sheet passes through progressive stations
- Contoured rolls gradually bend strip into profile
- Successive bending, flattening, and calibration
4. Pre-cutting
- Punching stations make holes or notches
- Rotary shears put angled edge cuts
- Mills, saws, or lasers cut patterns if needed
5. Trimming
- Flying shear or saw cuts parts to length
- Scrap strips trimmed automatically
- Transverse cut accuracy within ±1 mm
6. Exit and stacking
- Formed and trimmed parts exit on conveyor
- Counting, bundling, stacking for easy handling
- Offline finishing if needed
How to Choose a Suitable Trim Roll Forming Machine
Selecting the right trim roll forming machine depends on factors like:
- Annual volume – higher volumes need heavier duty equipment
- Strip width – standard versus custom widths available
- Metal thickness – machines range from 0.3 mm to 7 mm capacity
- Profile shape – simple C and U shapes easiest to produce
- Length variability – fixed versus variable length capability
- Secondary operations – punching, notching, milling, drilling
- Line speed – linear meters per minute rating
- Tooling requirements – initial tooling investment
- Precision needs – dimensional and cut tolerances
- Automation level – ease of setup, changeovers, operation
- Budget – initial cost and operating expense considerations
Work closely with trim roll forming machine manufacturers to select optimal specifications matching product needs. Prioritize speed, flexibility, precision, and reliability for best results.
Leading Manufacturers of Trim Roll Forming Machines
Some of the top global suppliers of trim roll forming machines are:
প্রতিষ্ঠান | Country |
---|---|
Foshan YSD Roll Forming Machinery | China |
Botou Xianfa Roll Forming Machine Factory | China |
JIDET | China |
Formtek | Taiwan |
DIMECO | USA |
স্যামকো মেশিনারি | Canada |
Bradbury Group | UK |
Metform International | UK |
Gasparini | ইতালি |
Dreistern | Germany |
These manufacturers offer standard and custom trim roll forming lines across a wide range of sizes and specifications. They also provide line integration, tooling, upgrades, and local service support.
Pricing of Trim Roll Forming Machines
Trim roll forming machine prices depend on factors like:
- Line width and speed
- Level of automation and extras
- Standard versus custom-built
- Added options like punching, sawing etc.
- Geographic location of supplier
Typical price ranges are:
Machine Rating | Price Range |
---|---|
Up to 800 mm width | $40,000 – $180,000 |
1000 – 1600 mm width | $80,000 – $350,000 |
2000 – 2500 mm width | $200,000 – $750,000 |
Larger or highly customized lines can cost over $1 million. Secondary equipment like decoilers, exit tables, and tooling add to the initial machine investment.
Operating costs include utilities, labor, maintenance, consumables, and tooling replacement over time. Exact production costs depend on application-specific factors.
How to Install, Operate and Maintain Trim Roll Lines
Installation
- Floor should be flat and level for machine alignment
- Lifting equipment needed for roll former placement
- Utilities like power, compressed air should be available
- Safety guarding and markings need to be in place
Operation
- Manuals detail step-by-step operating procedures
- Program control settings, speeds, feeds
- Monitor line operation, make adjustments
- Oil and maintain as specified
Maintenance
- Daily: visual checks, clean debris, safety checks
- Weekly: lubricate bearings, inspect chains, drives
- Monthly: check belt tension, fastener torque
- Yearly: overhaul, gearbox oil change, hydraulics inspection
Preventive maintenance minimizes unplanned downtime for maximum production. Keep spare parts, rolls, and consumables in stock for quick changeovers.
Guide to Choosing the Right Trim Roll Forming Machine Supplier
Choosing the right trim roll forming machine supplier is key to getting equipment that meets needs and provides value over the long run. Here is a checklist of factors to evaluate potential suppliers on:
- Reputation – Proven history and customer reviews
- Specialization – Focus on roll forming equipment
- কাস্টমাইজেশন – Ability to tailor machine to needs
- Design experience – Solutions for diverse applications
- Quality standards – Strict tolerances and high uptime
- Production capacity – Ability to deliver on schedule
- Range of services – Installation, training, maintenance
- Customer support – Responsiveness to issues, local presence
- Pricing – Competitive rates and payment terms
- Certifications – ISO, CE markings etc.
Visit supplier factories to inspect manufacturing practices firsthand. Getting references from existing customers also provides valuable insights. Prioritize suppliers who understand the application and deliver high-quality, reliable equipment with strong after-sales service support.
Pros and Cons of Trim Roll Forming
Pros | Cons |
---|---|
High production speeds | High initial tooling cost |
Low cost per piece | Long tooling lead times |
High consistency and repeatability | Setup time for changeovers |
Minimal scrap waste | Mostly limited to high volumes |
Automated process | Shape limitations on complex profiles |
Quick delivery for stocked profiles | Size constraints based on machine capacity |
Simple integration | Limited choice of materials |
Wide range of profile capabilities | Secondary finishing may be needed |
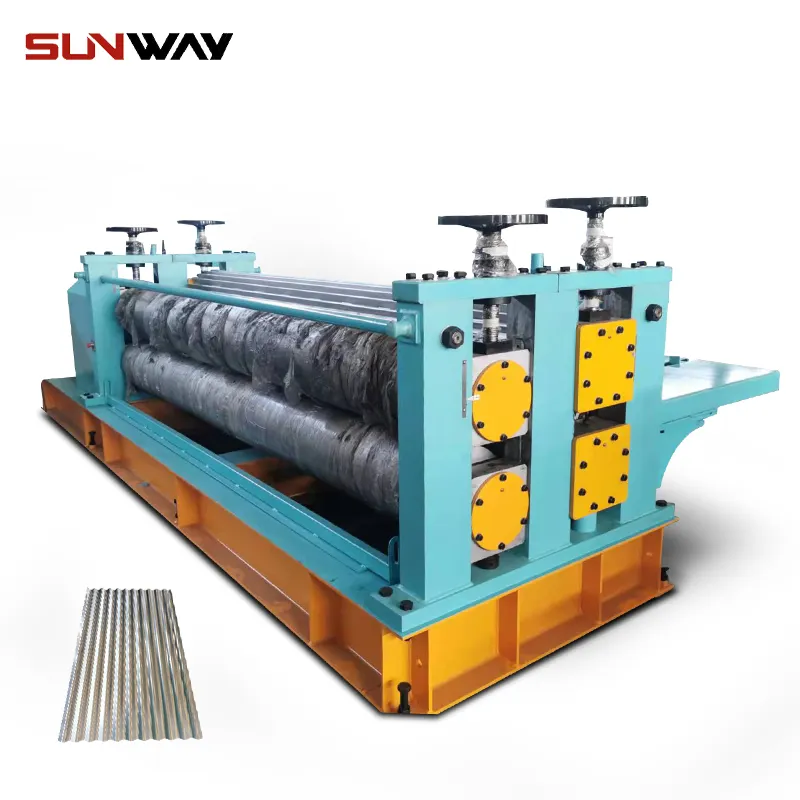
Applications and Limitations
অ্যাপ্লিকেশন
- Building construction trims and panels
- Infrastructure cladding and barriers
- Transportation and automotive components
- Shelving, racks, conveyors
- Electrical and HVAC ducting
- Furniture frames and supports
- Agricultural and machinery housings
- Packaging and containers
- Appliance casing and trim
- Display framing and signage
Limitations
- Very short production runs under 1000 pieces
- Small batch prototyping
- Low sheet metal thickness under 0.5 mm
- High precision components under 0.2 mm tolerance
- Intricate geometries requiring multiple bends
- Large sheet size over 2500 mm width
- Stainless steel or other niche alloys
- Welded fabrications and assemblies
FAQs
What is trim roll forming?
Trim roll forming is the process of shaping metal coil stock into custom profiles using a series of rolling stations, combined with edge trimming cuts to create finished parts.
What equipment is used?
The main equipment includes a decoiler, feed system, forming stations, cutting tools, and exit conveyor. Controls automate the complete process from coiled raw material to formed and trimmed profiles.
What metals can be trim roll formed?
Most common materials are low carbon steel, stainless steel, and aluminum. Other roll formable metals include copper, brass, titanium, and nickel alloys.
What thicknesses and widths can be processed?
Standard machines handle material from 0.3 mm to 7 mm thickness, in widths ranging from 50 mm to 2500 mm. Special units are available beyond these limits.
How fast is the process?
Production line speeds typically range from 10 to 120 meters per minute, depending on part size and complexity.
What tolerances are achievable?
Roll formed parts can be made with a dimensional tolerance within +/- 0.5 mm and cut length tolerance around +/- 1 mm.
What are the typical applications?
Construction trims, infrastructure panels, transportation components, storage/conveyor profiles, HVAC ducts, agricultural equipment, packaging forms, and appliance housings.
What are the key benefits compared to other methods?
High speeds, lower costs, material savings, quick delivery, automation, and flexibility to make custom parts are the main advantages versus other fabrication techniques.
What should I look for when choosing a machine supplier?
Key factors include reputation, experience, quality standards, design customization abilities, production capacity, service support, certifications, and value pricing.
What maintenance is required?
Daily checks, weekly lubrication, monthly inspections, and annual overhauls of all components. Keeping spare parts inventory allows minimizing downtime.
Are secondary finishing steps needed?
For some applications, additional operations like hardware insertion, welding, painting or packaging may be required after roll forming. The machine supplier can advise on integration needs.