A downpipe roll forming machine is equipment used to form metal sheets into rounded rainwater downpipes and drainpipes. This guide provides a comprehensive overview of downpipe roll forming machines made in China, covering types, technical specifications, suppliers, applications, installation, operation and more.
Overview of China Downpipe Roll Forming Machines
Downpipe roll forming machines are an efficient way to manufacture corrosion-resistant metal rain gutter and drainage pipes for buildings. China has become a leading global supplier of quality roll forming equipment at competitive prices.
Key benefits of China downpipe roll forming machines:
- Highly automated operation for mass production of pipes
- Flexible production of different pipe sizes and metal thicknesses
- Consistent quality and dimensional accuracy of pipes
- Robust all-steel welded framing structure for stability
- Lower equipment cost compared to European or American roll forming lines
Roll formed downpipes offer advantages over extruded pipes:
- Formed from corrosion resistant pre-coated metal coils
- Smooth surfaces free of welds, seams and imperfections
- Consistent circumferential strength and rigidity
- Lower cost for bulk production quantities
This guide covers the main types, technical parameters, suppliers, applications and operation of China downpipe roll forming equipment.
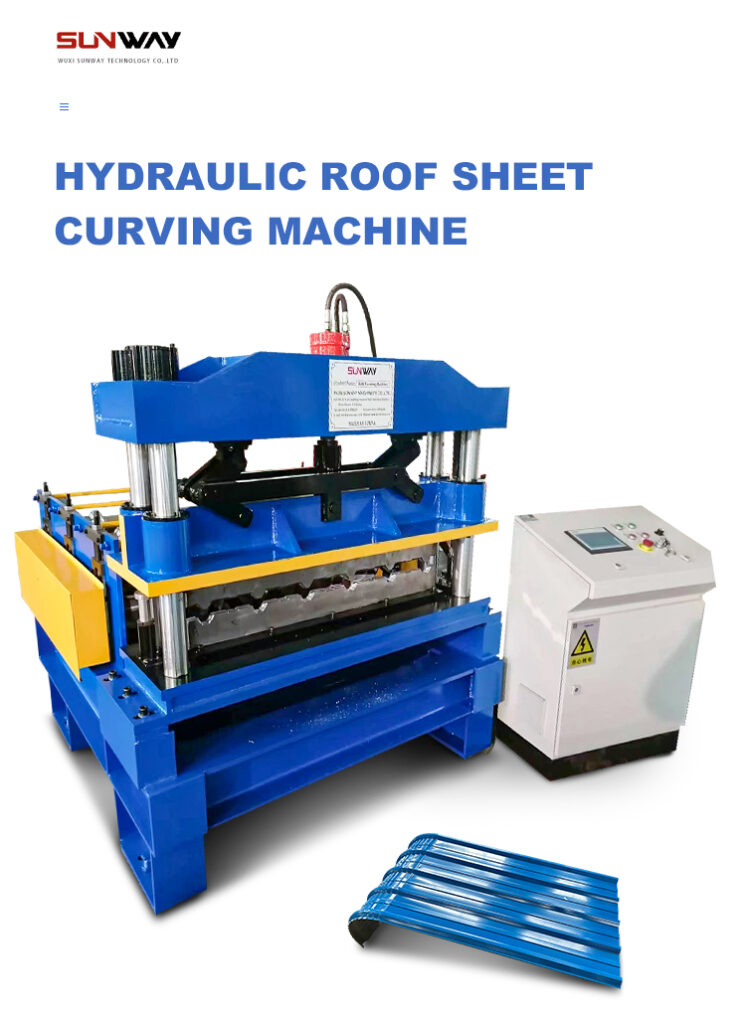
Types of China Downpipe Roll Forming Machines
China downpipe roll forming machines are available in manual, semi-automatic and fully automatic configurations to suit different production needs.
Manual Downpipe Roll Forming Machines
Manual downpipe roll forming machines have a simple mechanical design for small scale production.
Features:
- Compact all-steel welded framing and rolling components
- Manual material feeding and pipe cutting
- Guide rollers to support sheet alignment
- Changeover of forming rollers for different pipe sizes
- Typical speed of 10-15m/min
Advantages:
- Lower investment cost
- Simple operation and maintenance
- Flexible for small batch production
Limitations:
- Labour intensive material handling
- Lower efficiency and inconsistent quality
- Frequent roll changeovers required
Semi-Automatic Downpipe Roll Forming Machines
Semi-automatic downpipe roll forming machines have powered forming rolls and automated sheet feeding to improve efficiency.
Features:
- Servo motor driven forming rolls
- Powered unwinding of coil material
- Automated feed of sheet into rolls
- Manual pipe cutting
- Touchscreen controls
- Speeds up to 25m/min
Advantages:
- Improved efficiency over manual machines
- Consistent quality with automated processes
- Simpler changeovers between production runs
- Higher hourly output up to 200-300m/hr
- Lower labour requirements
Limitations:
- Manual offloading and cutting increases process times
- Frequent roll changeovers required for different sizes
Fully Automatic Downpipe Roll Forming Machines
Fully automatic downpipe roll forming machines complete all material handling and pipe cutting automatically for maximum efficiency.
Features:
- Servo motor driven forming rolls
- Powered material coil unwinding
- Automatic feeding, rolling and cutting
- Integrated offloading and stacking
- PLC and touchscreen control
- Speeds up to 35m/min
Advantages
- High production rates up to 500m/hr
- Automated changeovers between sizes
- Consistent quality with minimum labour
- Lower long term operating costs
Limitations:
- Higher initial capital investment
- Specialist maintenance skills required
Technical Specifications
China downpipe roll forming machine manufacturers offer equipment in a range of sizes and capabilities to produce different pipe dimensions.
Typical technical specifications:
Specification | বিস্তারিত |
---|---|
Forming Stations | 10-16 |
Maximum Forming Speed | Up to 35m/min |
Minimum Pipe Diameter | 80mm |
Maximum Pipe Diameter | 200mm |
Minimum Material Thickness | 0.3mm |
Maximum Material Thickness | 1.2mm |
Main Drive Power | 5.5kW-11kW |
Voltage | 380V 3-phase |
Machine Dimensions | 10m-18m Length x 1.5m Width x 1.8m Height |
Machine Weight | 3000kg-8000kg |
- More advanced fully automatic lines have faster speeds, quick changeover times, and produce larger diameter pipes.
- Specifications can be customized according to client’s production requirements.
Downpipe Roll Forming Machine Applications
China downpipe roll forming machines are versatile metal forming equipment suitable for:
- Rainwater Downpipes – Round gutter downpipes for roof drainage systems
- Floor Drains – Square or rectangular drains for landscape applications
- Vent Pipes – Exhaust ventilation pipes for HVAC systems
- Structural Pipes – Circular hollow tubes as structural framing members
- Decorative Pipes – Unique shapes for architectural accents
The most common application is aluminum and galvanized steel downpipes for buildings. Hot-dip galvanizing or aluminum-zinc coating provides corrosion protection for long service life.
Downpipe roll forming allows high volume, low cost production. Formed pipes are an economical alternative to cast iron, PVC and soldered copper pipes.
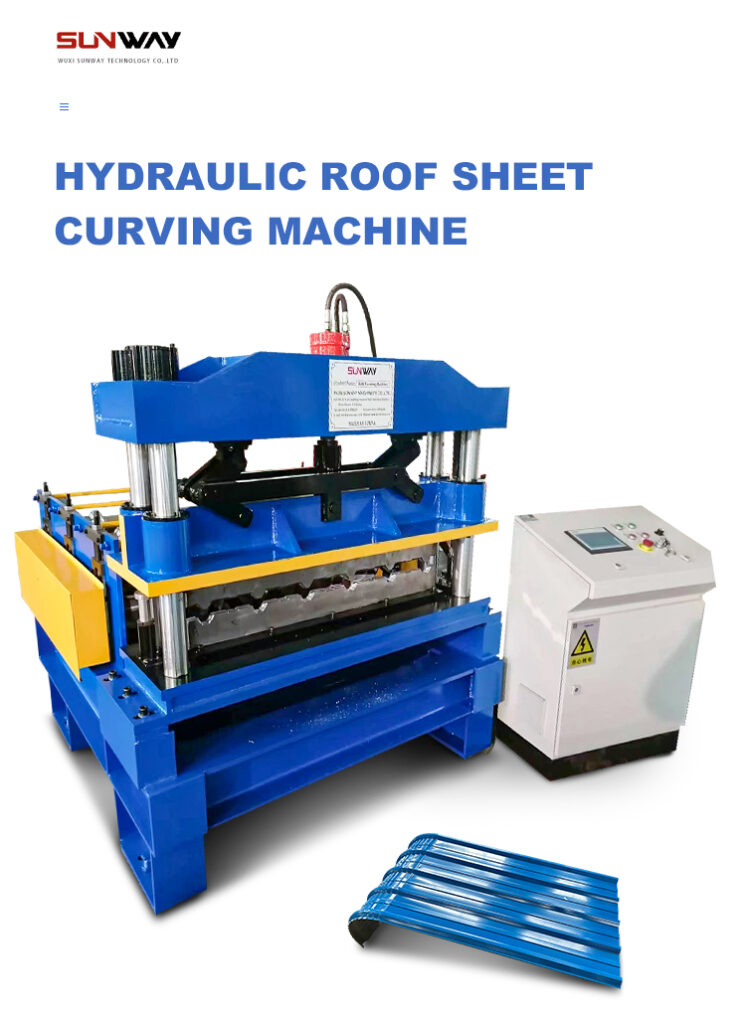
Downpipe Roll Forming Machine Suppliers in China
China has numerous manufacturers providing competitive downpipe roll forming equipment:
Notable Suppliers
প্রতিষ্ঠান | Location | Product Range |
---|---|---|
Jinan Saimei | Shandong | Manual, Semi & Fully Automatic |
Botou Yixinda | Hebei | Semi & Fully Automatic |
Wuxi Guanyuantong | Jiangsu | Semi & Fully Automatic |
Dongguan Jingxin | Guangdong | Manual & Semi Automatic |
- Larger state owned enterprises and private companies located in coastal provinces.
- Offer complete lines and individual roll forming machine components.
- Standard or customised roll tooling for specific pipe profiles.
- Provide line installation assistance, training and after-sales support.
Purchasing Considerations
- Evaluate supplier’s reputation, manufacturing capabilities and quality control.
- Source important components like bearings, motors, PLCs from reliable brands.
- Prioritise suppliers who can provide effective technical support and service.
- Compare options on offered pipe sizes, speeds, features and prices.
- Choose semi or fully automatic lines for efficient higher volume production.
- Manual machines suit very small scale or intermittent production.
Downpipe Roll Forming Machine Prices
Machine Type | Size Range | Speed | Price Range |
---|---|---|---|
Manual | 80-150mm Dia. | 10-15m/min | $5,000 – $8,000 |
Semi-Automatic | 80-200mm Dia. | 15-25m/min | $15,000 – $35,000 |
Fully-Automatic | 80-200mm Dia. | 25-35m/min | $50,000 – $120,000 |
- Prices vary based on production speed, automation features, and maximum pipe diameter.
- Larger size, faster and fully automated lines carry higher costs.
- Manual roll forming machines are most affordable for small workshops.
- Payback period can be as little as 1-2 years with labour savings.
- Request quotations from multiple suppliers for best price.
Downpipe Roll Forming Machine Installation
Proper installation is key for optimized functioning of downpipe roll forming lines.
Installation Guidelines
- Prepare flat, level, and vibration-free foundation for machinery.
- Bolt machine securely onto foundation. -Align machine components and rolls accurately.
- Connect electric power supply according to specifications.
- Install safety guarding around moving parts.
- Test run the line empty to verify correct functioning.
- Make any adjustments to roll alignment before production.
Installation Timeframe
- Small manual lines require 2-3 days for installation.
- Larger automatic lines need 4-6 weeks including foundation works.
Personnel Requirements
- Construction crew for foundation preparation.
- Mechanical technicians for assembly of the line.
- Electricians to complete power connections.
- Supplier’s engineers to oversee the installation process.
Correct machine installation is vital for smooth production operation and performance.
Downpipe Roll Forming Machine Operation
Operating downpipe roll forming machines requires trained personnel for efficient functioning:
Operation Guidelines
- Carefully thread coil material through feeding equipment.
- Adjust rollers as per required pipe diameter.
- Set the forming speed within machine capabilities.
- Closely monitor pipe quality and dimensional accuracy.
- Apply lubricants to prevent sticking and Scratching.
- Perform regular maintenance according to schedules.
- Ensure all safety mechanisms are functioning.
- Keep work area clean and organized.
Staff Requirements
- Operator to control line settings and monitor operation.
- Helpers to handle raw material and finished pipes.
- Electrician for maintenance of electrical components.
- Mechanic to maintain fittings and roll tooling.
- Manager for production planning and quality control.
Shifts Per day
- Typically 1 or 2 shifts of 8 hours each.
- 3 shifts possible for high volume production needs.
Proper operating procedures optimize productivity while minimizing quality defects.
Downpipe Roll Forming Machine Maintenance
Regular maintenance keeps downpipe roll forming equipment in good working order:
Daily/Weekly Maintenance
- Clean machine surfaces of dirt and debris
- Check oil levels in gearboxes and lubricate moving parts
- Inspect roll tooling condition and make minor adjustments
- Check electrical wiring and motor functioning
- Confirm alignment of forming rolls
- Test functionality of safety mechanisms
Monthly Maintenance
- Thorough inspection of all structural components
- Repair or replace any damaged or worn parts
- Backup control system software and data
- Confirm functioning of pneumatic and hydraulic elements
- Check overall machine alignment and make adjustments
Annual Maintenance
- Complete overhaul of mechanical assemblies
- Replace bearings and other critical spares
- Update machine software/firmware if required
- Implement any engineering changes by supplier
- Repaint any areas showing surface corrosion
Scheduled maintenance minimizes unplanned downtime and improves equipment lifetime.
How to Choose a China Downpipe Roll Forming Machine Supplier
Here are key factors when selecting a Chinese downpipe roll forming machine supplier:
- Product Quality – Build quality, component brands, reliability track record
- Technical Expertise – Engineering skills for the equipment type or features required
- Customization Capability – Ability to modify designs to suit unique needs
- Production Capacity – Scale and output volume of supplier to meet demands
- Certifications – Relevant quality management system certification
- Pricing – Equipment purchase and maintenance service pricing
- Lead Time – Timeframe for manufacturing and delivering equipment
- Aftersales Service – Installation support, maintenance, spare parts supply
- Prior Clientele – Reputable companies previously supplied by vendor
Carefully vetting and qualifying suppliers using the above criteria minimizes project risks and ensures satisfactory outcomes.
Pros and Cons of China Downpipe Roll Forming Machines
Pros
- Advanced automation for efficient high volume production
- Robust all-steel construction for durability
- Lower capital cost versus European or American machines
- Formed pipes have uniform roundness and smooth surface
- Ideal for manufacturing downpipes and drains in longer lengths
- Easy to changeover rolls for different pipe sizes
- Compact footprint requiring small factory space
Cons
- Requires skilled personnel for specialized operation
- Sophisticated fully automatic lines have steeper learning curve
- Preventative maintenance is crucial to maximize uptime
- Limited flexibility to produce non-standard pipe geometries
- Higher maintenance costs and downtime versus simpler designs
- Longer lead times for delivery of equipment from China
Downpipe Roll Forming vs Extrusion of Pipes: A Comparison
Downpipe roll forming and pipe extrusion are two common metal pipe manufacturing processes with relative advantages and limitations.
Parameter | Downpipe Roll Forming | Pipe Extrusion |
---|---|---|
Method | Rolls progressively cold form flat strip into tubular shape | Heated billet is pushed through die to form pipe |
Materials | Galvanized steel, aluminum | Wider range – steel, aluminum, thermoplastics |
Diameters | 50mm-250mm typically | 15mm-600mm range |
Wall thickness | 0.5mm-2.0mm | 1mm-10mm range |
Surface finish | Smooth, mark free | Moderately smooth finish |
Joints | No joints, continuous lengths | Seamless continuous or need joining |
Production rate | High – to 300m/min | Lower – to 10m/min |
Initial cost | Moderate $50,000+ | High $250,000+ for larger sizes |
Running cost | Lower | Higher energy usage |
Shape options | Round, square profiles | Wide range of shapes |
Strength | High circumferential strength | Better longitudinal strength |
Defects | Minimal | More prone to cavities |
অ্যাপ্লিকেশন | Rainware, fence tubes | Wider structural use |
In summary, downpipe roll forming is best suited for high speed manufacturing of smaller diameter round drainage pipes; while extrusion offers more flexibility but lower volumes.

FAQ
Q: What size companies use downpipe roll forming machines?
A: From small workshops producing 100kg/day up to large factories making 10+ tons per day. Larger automatic lines suit bigger demand.
Q: Can these machines make square or rectangular tubes?
A: Yes, die tooling can be modified to produce square drain pipes or rectangular tubing. But round sections are most common.
Q: What thickness of metal sheet can be formed into pipes?
A: Typically 0.3-1.2mm gauge material. Thinner foils can wrinkle while thicker sheets are hard to shape.
Q: How long are the formed downpipe lengths?
A: Standard lengths are 6 or 8 meters. Automatic cut-offs can produce any required lengths.
Q: What is the typical lifetime of a downpipe roll forming machine?
A: Approximately 10 years or more if proper maintenance is followed. Key parts may need replacement over time.
Q: What defects can occur in roll formed downpipes?
A: Wavy sections, scratches, deformations if the process is not set correctly. Control systems minimize defects.
Q: Can I get a downpipe machine customized to my requirements?
A: Yes, reputable suppliers can modify designs as per your unique specifications and production needs.
Q: Is operator training provided with the machine installation?
A: Suppliers typically provide 1-2 weeks of on-site operation and maintenance training to the personnel.
This covers the main frequently asked questions on downpipe roll forming line capabilities, applications and operation. Reach out to suppliers for quotes or details on custom roll forming solutions.
উপসংহার
China downpipe roll forming machines enable efficient high-speed production of rainwater drainage pipes at competitive prices. This equipment guide has covered the main types, technical parameters, suppliers, applications, installation and operational aspects to consider. Fully automatic lines deliver maximum productivity but require higher investment. Semi-automatic and manual options work well for small to mid-sized pipe manufacturing needs. Carefully selecting reputable suppliers and implementing scheduled maintenance practices is key to keeping the machines functioning optimally. Compared to other pipe production methods like extrusion, downpipe roll forming is an economical solution ideal for metal rainwater and structural tubing.