Light steel keel roll forming machines are an essential equipment used for manufacturing light steel keels and frames for the construction industry. This guide provides a comprehensive overview of light steel keel roll forming machines covering their working, types, main components, specifications, applications, advantages, limitations and more.
Overview of Light Steel Keel Roll Forming Machines
Light steel keel roll forming machines are designed to cold-form different light steel sections and profiles used as load bearing members in light steel framed buildings and structures. They continuously form structural C,U,Z,Sigma and other shaped profiles from steel coil of thickness 0.7-2.0mm into required cross-sections by gradually bending the strip through a series of roller dies.
Compared to other steel structural members, light steel keels and studs formed by these machines offer advantages like light weight, high strength, easy and fast installation, design flexibility, environment friendly construction and more. They find wide applications in walls, floors, roofs and frameworks for residential, commercial and industrial buildings.
The most important components of a light steel roll forming machine include the decoiler unit, feeder, pre-cutter, roll forming stations, post-cutter and other auxiliary devices. Based on number of profiles produced, they are available in single and multi-profile designs from various manufacturers around the world.
Main Features of Light Steel Keel Roll Formers:
- Cold roll high strength light steel coils into C,U,Z,Sigma and custom profiles
- Form keels up to 2mm thickness and 200mm height
- Output up to 120m/min with tolerance +/-0.5mm
- PLC controller for automatic production
- Roller dies made of wear-resistant materials like GCr15 steel
- Computerized hydraulic decoiler for feeding coil strips
- Servo motors for precision feeding and cutting
- Easy size changeovers with quick change forming rollers
- Safety devices like strip breakage detection sensors
- Optional inline punching units and stackers
Working Principle of Light Steel Keel Rolling Machines
The working principle involves continuously forming structural light steel sections from steel coil by passing it through a series of roller dies that gradually bend the strip into the required profile shape.
Steps in Light Steel Profile Roll Forming Process:
- Decoiling – The decoiler feeds the light gauge steel coil strip into the roll former
- Feeding – Feed rollers grip the strip and pull it through the forming stations
- Pre-cutting – Cuts the strip to preset lengths for forming keel frames
- Roll forming – Strip passes through series of stands with roller dies to bend it
- Post-cutting – Cuts formed profiles to required lengths
- Counting and stacking – Formed keels are counted and stacked automatically
The roller dies are the key forming parts arranged in stands along the machine line. As the strip passes through each stand, the rollers make gradual bends until the final profile shape is achieved. The number of stands required depends on the complexity of the section.
Precise feed control, well aligned roller dies and optimal pass schedules are critical to achieve the tight tolerances and high quality demanded for structural light steel profiles.
Advanced machines also integrate inline processes like punching holes, embossing logos and automated stacking for complete production in a single line.
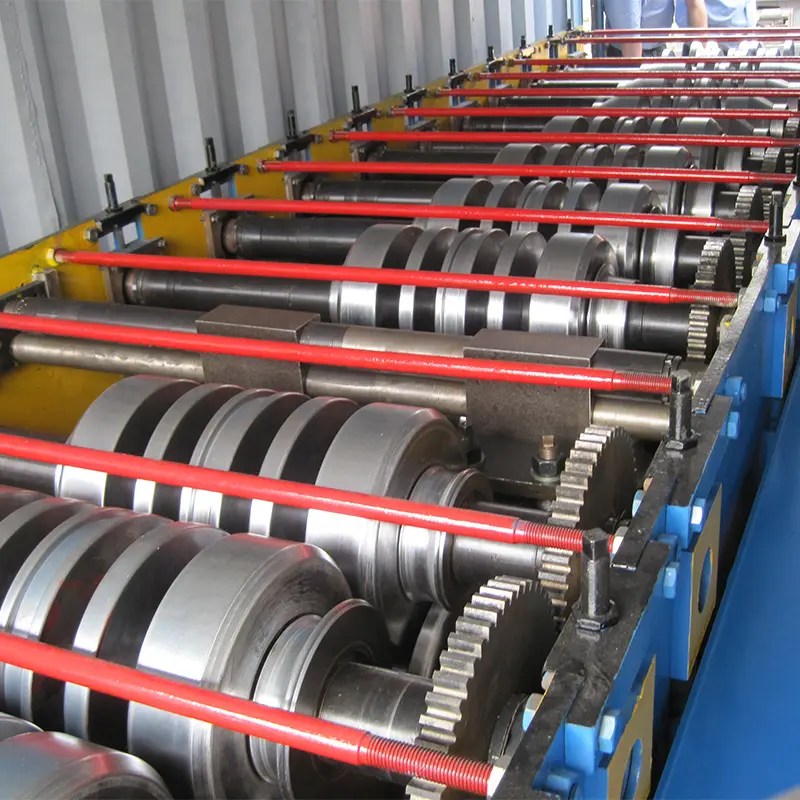
Types of Light Steel Keel Roll Forming Machines
Light steel keel roll forming machines are available in different configurations designed to produce various types and sizes of profiles as per application requirements:
Types of Light Steel Roll Forming Machines
Machine Type | Description |
---|---|
Single Profile | For rolling one profile shape like C, U or Sigma continuously |
Double Profile | Produces two profiles simultaneously like C + U |
Multi Profile | 3 or more profiles like C, U, Z, Sigma together |
Fixed Size | Limited to rolling profiles of fixed heights and thicknesses |
Adjustable | Forms adjustable range of profile sizes |
Manual | Basic models with manual size changing |
Automatic | Motorized roll and screw adjustments for size changes |
Standard | For regular light steel structures |
Heavy Duty | For special large or thick profiles |
Factors for Selecting Type of Roll Former:
- Number and types of profiles required
- Range of sizes and thicknesses
- Production speed and output
- Frequency of size changeovers
- Level of automation needed
- Available space and budget
Getting the right type of roll forming machine is important to match the production demands and get optimum efficiency.
Main Components of Light Steel Keel Roll Machines
Light steel keel roll forming machines consist of several important components and auxiliary devices for smooth and efficient operation:
Core Components of a Roll Forming Line:
- Decoiler: Feeder unit that holds the steel coil and uncoils the strip
- Feeding System: Rollers that grip and feed the strip through the stations
- Pre-Cutting Unit: Shears the strip to pre-cut lengths before forming
- Forming Stations: Roller dies mounted in stands to bend the strip
- Post-Cutting Unit: Cuts profiles to final required lengths
- Stacking System: Counts, collects and stacks the formed sections
Other Auxiliary Parts:
- Strip Accumulator: Holds excess strips to avoid stoppages
- Punching Unit: To punch web holes in the profiles
- Control Panel: Housing the PLC controller and operation switches
- Safety Devices: Limit switches, breakage sensors, safety guards etc.
Key Aspects:
- The decoiler, feeding system and cutters ensure continuous smooth material flow
- The profiler sections with roller dies are the heart to form the shapes
- Automated stacking improves efficiency and minimizes effort
- Advanced computerized controls make the processes automatic
- Safety devices are critical for safe working during high speed production
Proper selection, setup and maintenance of each component is vital for optimal performance of the roll forming system.
Specifications of Light Steel Keel Roll Forming Machines
Light steel keel roll forming machines are available in a range of sizes and capacities to produce profiles for different applications. Below are the key technical specifications considered while selecting a roll former:
Typical Specifications of Light Steel Roll Forming Machines
Parameter | Typical Range |
---|---|
Roller Diameter | 100-150 mm |
Max Coil ID | 1000-1500 mm |
Max Coil OD | 1500-2500 mm |
Max Strip Width | 1200-1500 mm |
Min Strip Thickness | 0.3-0.7 mm |
Max Strip Thickness | 1.5-2.5 mm |
গঠন গতি | 10-120 m/min |
Tolerance | +/- 0.5 mm |
Max Profile Height | 150-250 mm |
Power Consumption | 15-50 kW |
Voltage | 380-415V, 50Hz |
- Size and speed determine production capacity
- Coil and strip sizes affect model selection
- Power rating depends on tonnage and automation
- Voltage, frequency should match power supply
Consult manufacturers to get machines matching the required production specifications. Custom built models are also available.
Applications and Uses of Light Steel Keel Roll Forming
The light steel profiles produced by keel roll forming find wide applications in residential and commercial building construction:
Typical Applications of Roll Formed Light Steel Keels/Studs
আবেদন | Description |
---|---|
Wall Frames | Load bearing studs in walls for houses, offices etc |
Floor Joists | C or U studs supporting floor slabs |
Roof Trusses | For rafters, purlins in industrial roofs |
Structural Framing | Columns, beams framework in buildings |
Prefab Houses | Whole structural frames for fast construction |
Furniture | Profiles for racks, storage, furniture etc |
Infrastructure | Highway signs, solar mounts, poles etc |
- Provide strength while being lightweight
- Easy to handle and fast to install on site
- Design flexibility for custom profiles
- Consistent quality with close tolerances
- Cost effective material utilization
- Eco-friendly green construction
Light steel profiles enhance strength, speed up construction and offer sustainability.
How to Choose a Light Steel Roll Forming Machine Supplier
Choosing the right light steel roll forming machine manufacturer is key to get equipment that meets the production needs efficiently. Below are important factors for selecting a good supplier:
Key Considerations for Choosing a Roll Forming Machine Supplier
পরামিতি | বিস্তারিত |
---|---|
অভিজ্ঞতা | Many years of experience in roll forming |
Production Capabilities | Type and size of machines they offer |
কাস্টমাইজেশন | Ability to customize profiles if needed |
Quality | Good tolerances, reliability and durability |
Certifications | ISO and other standards compliance |
Automation | Level of automation possible |
Services | Installation, commissioning, support etc |
Reputation | Reliable after-sales service record |
Pricing | Competitive pricing for value offered |
Lead Time | On time delivery as per schedule |
- Interview multiple manufacturers before deciding
- Visit facilities to inspect first-hand if possible
- Ask for client references to check quality satisfaction
- Ensure supplier understands requirements clearly
- Optimize automation features suiting budget
Choosing the right partner ensures long lasting efficient roll forming production.
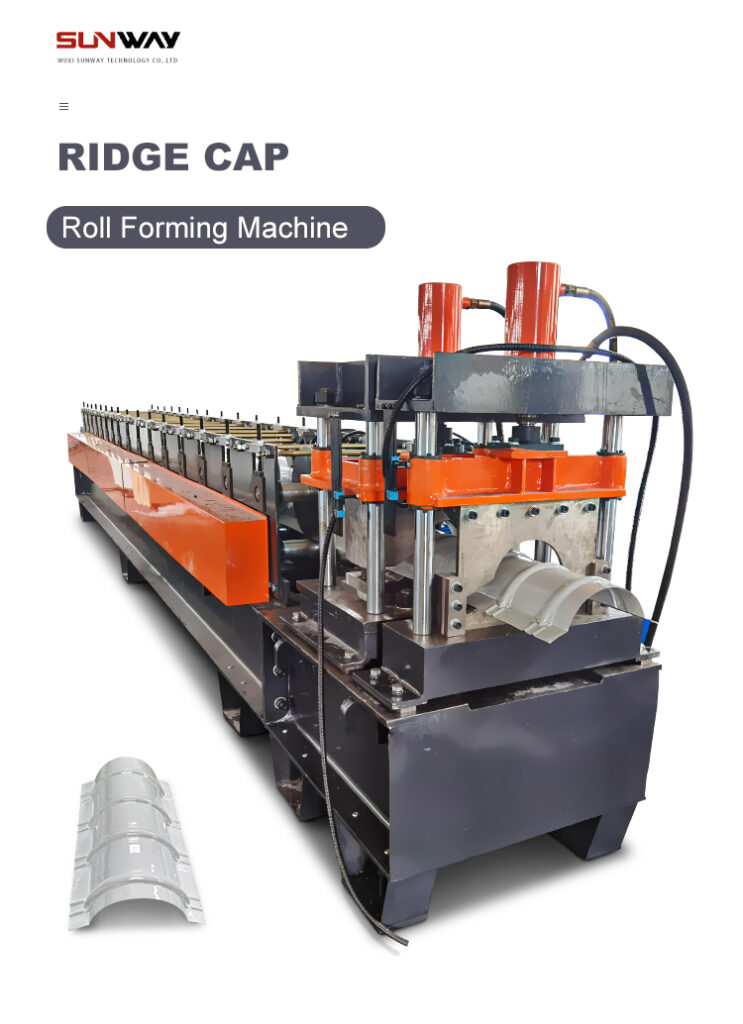
Pros and Cons of Light Steel Keel Roll Forming
Advantages of Light Steel Roll Forming Machines:
- High production speed and output
- Consistent quality with close tolerances
- Flexibility to produce different profiles
- Lower fabrication costs compared to other methods
- Minimal material wastage
- Lower energy consumption than hot forming
- Safer with reduced risks than hot processes
- Automated production improves efficiency
- Allows innovative steel building designs
- Overall economical construction solution
Limitations of Light Steel Roll Forming:
- Higher initial machine investment cost
- Regular maintenance required for quality
- Size changeovers can affect productivity
- Limited to certain mild steel grades and thicknesses
- Design complexity affects production rate
- Risk of deformities if parameters not set correctly
- Noise generation requiring safety precautions
- Skilled technicians needed for operation
Proper machine selection and process control minimizes the limitations for cost effective production.
Installation and Operation of Light Steel Keel Roll Machines
Correct installation and operation procedures are vital for smooth functioning and optimum performance of light steel roll forming machines.
Installation Guidelines
- Select flat, level concrete foundation with sufficient strength
- Ensure adequate space around for material movement
- Lifting tools required for unloading heavy components
- Prepare grouted foundation bolts as per layout drawings
- Assemble machine frame, stands, and roll forming sections
- Install hydraulic power packs and electrical connections
- Align roller dies and devices as per specification
Operation Guidelines
- Strictly follow manufacturer’s operational instructions
- Ensure all safety devices and guards are intact
- Select correct roller dies for profile shape required
- Set strip feeding, pre-cut and post-cut lengths
- Adjust decoiler, rollers for smooth material flow
- Gradually increase speed during test runs, verify formations
- Ensure formed profiles adhere to tolerances
- Conduct trial production runs before actual use
- Perform regular maintenance for continuous production
Proper installation and operation training by the supplier is highly recommended for optimal performance.
Maintenance of Light Steel Keel Roll Forming Machines
Regular maintenance is crucial for trouble-free operation and maximum production uptime of the roll forming lines.
Recommended Maintenance Activities and Frequency
Activity | Frequency |
---|---|
Cleaning | Daily |
Inspection | Daily |
Bolt tightening | Weekly |
Lubrication | Weekly |
Alignment checks | Monthly |
Hydraulic oil replacement | 6 Months |
Wear checks on rollers, bearings, guides | 6 Months |
Replacement of damaged/worn parts | As needed |
Overhaul | Annual |
Key Maintenance Tips:
- Keep machines clean, inspect wear, damage daily
- Lubricate bearings, sliding parts regularly
- Perform periodic alignment, adjustments
- Use genuine spare parts for replacements
- Keep hydraulic systems clean, change oil periodically
- Schedule annual overhaul after production season
- Maintain maintenance logs for records
- Train technicians on proper methods
Proper maintenance improves production, reduces breakdowns and extends machine service life.
How to Select Right Light Steel Roll Forming Machine
Choosing the optimal light steel roll forming machine is important for efficient profile production. Below are tips for selecting the right roll former:
- Analyze part profiles, sizes, production volume required
- Determine suitable machine type – single, multi, heavy-duty etc.
- Consider automation features like auto size changeovers
- Ensure machine capacity matches desired output levels
- Check reliability and durability of components
- Select reputable manufacturer with quality certifications
- Compare suppliers on pricing, services, delivery terms
- Evaluate after-sales support for periodic maintenance
- Consider possibilities for future upgrades, expansions
- Review safety aspects, ease of operation
- Physical trial of machine operation is recommended
The correct forming machine ensures fast payback on investment via years of trouble-free production. Discuss specific needs with expert suppliers to choose the optimal roll former.
Costs Related to Light Steel Keel Roll Forming
The costs associated with procuring and operating light steel roll forming machines include:
Roll Forming Equipment Cost Components
Cost Factor | বিস্তারিত |
---|---|
Machine cost | Capital cost depending on type, size, features |
Auxiliary equipment | Decoilers, stackers, conveyors etc |
Design and tooling | For custom profile tooling if needed |
Handling and installation | Unloading, positioning, utilities connections |
Site preparation | Leveling, foundation, space provisions |
Spare parts | Initial essential spare parts kit |
প্রশিক্ষণ | Operator training for production |
Freight and taxes | Added costs based on location |
Operational Costs
- Raw material coils
- Utility bills for electricity and oil
- Consumables like lubricants
- Salaries for operators
- Maintenance and repairs
- Tooling changeovers, reworks if any
- Safety gear, accessories
Cost Optimization:
- Choose machine size suiting production needs
- Standard models are economical for regular profiles
- Automation improves productivity and ROI
- Schedule reasonable production cycles
- Train personnel for efficient working
- Maintain machines well to minimize breakdowns
- Utilize production capacity optimally
Selecting the right forming machine and using it efficiently is key to derive maximum return on investment.
Light Steel Roll Forming Machine Manufacturers
Some leading manufacturers of light steel keel roll forming machines include:
Key Light Steel Roll Forming Machine Brands
প্রতিষ্ঠান | Location |
---|---|
Botou Xianfa | China |
Gasparini S.p.A. | ইতালি |
Bradbury Group | UK |
Formtek | USA |
Metform | Turkey |
Jouanel | ফ্রান্স |
DIMECO | USA |
স্যামকো মেশিনারি | China |
An Sheng Machinery | China |
Zeman Bauelemente | Austria |
- Established manufacturers with decades of experience
- Offer standard and customized roll forming solutions
- Advanced technology for high production efficiency
- Key presence in Asia, Europe, North America markets
- Compliant with CE, ISO, and other global standards
- Provide installation support, operator training
- Have extensive service networks
Review multiple suppliers before selecting light steel roll forming equipment for specific production needs and budget.
Light Steel Roll Forming Machine Pricing
The price range for light steel keel roll forming machines depends on:
Cost Influencing Factors
- Type of machine – single profile, multi profile, heavy duty etc
- Production speed and output capacity
- Level of automation – manual, semi, fully automatic
- Additional accessories like punching, stacking units
- Roller size, tooling, and raw material requirements
- Brand, manufacturing country, quality standards
Approximate Price Range
Capacity | Price Range |
---|---|
Up to 30 m/min | $8,000 – $15,000 |
31-60 m/min | $16,000 – $50,000 |
61-100 m/min | $51,000 – $150,000 |
Above 100 m/min | $150,000+ |
- Entry level basic machines are economical
- Medium capacity automated lines offer good value
- Heavy duty high speed models are premium priced
- Custom built roll formers are costlier
- Consider long term production needs for ideal investment
Discuss specific profile requirements with vendors to get accurate price quotations for optimal equipment selection.
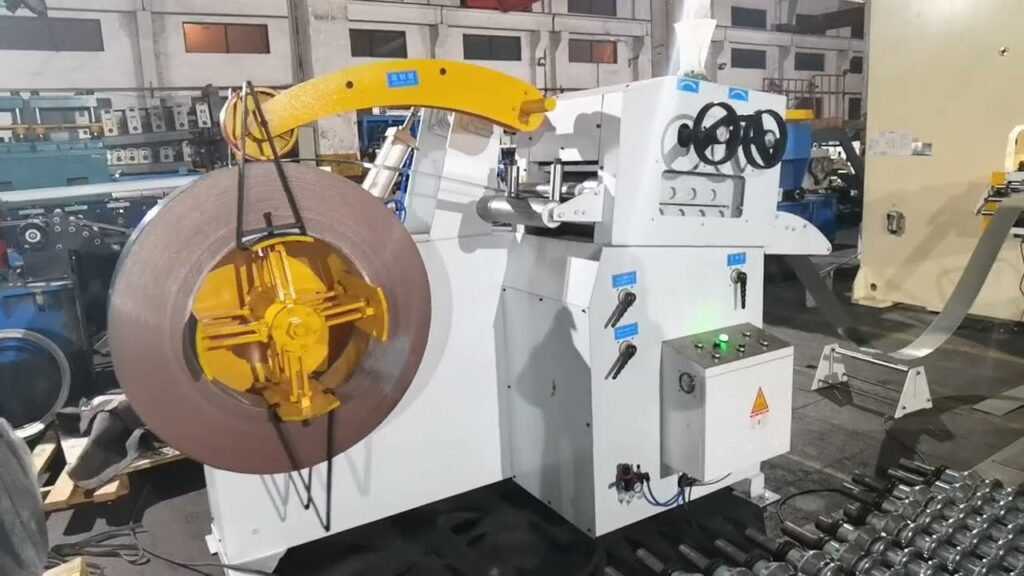
FAQs
Q: What materials can be roll formed into light steel keels?
A: Low carbon steels like SS400, SAE1010, Q235 with thickness 0.5-2mm having good cold formability are commonly used.
Q: What profiles can be produced on light steel roll machines?
A: C, U, Z, Sigma, L shaped profiles are commonly rolled. Custom shapes are also possible.
Q: How to calculate production rate for a roll forming line?
A: Production rate = Forming speed x Number of profiles x 60. For example 40 m/min x 2 profiles x 60 = 4800 keels per hour.
Q: What maintenance is required for light steel roll forming machines?
A: Regular maintenance like cleaning, lubrication, inspection of components, alignment checks, spare parts replacement and annual overhauls are recommended. Proper maintenance minimizes breakdowns.
Q: How to change profile sizes on adjustable roll forming machines?
A: Adjustable machines have powered roll and screw settings to alter roller positions. Operators select required profile on the control panel for automated size changeover.
Q: What safety precautions are important for roll forming operation?
A: Safety guards, light curtains, emergency stops, strip detection sensors should be functional. Workers should wear protective gear and be trained on safe working procedures.
Q: How much area is needed to install a light steel roll forming machine?
A: Approximately 30-50 sq.ft area is needed for a standard roll former. More space is required for material movement for larger machines. Proper layout by the manufacturer is important.
Q: What factors determine if a profile can be roll formed?
A: Key factors are type of steel grade, thickness, width, total bend angle, bend radii, direction changes. Feasibility studies are done to design suitable roll tooling.
Q: What is the typical tolerance that can be achieved in roll forming?
A: Light steel profiles are normally formed within +/- 0.5mm tolerance. Precision roller dies, good alignment and feed control help achieve tight tolerances.