Manual roll forming is a metalworking process that uses a series of consecutive stands with contoured rolls to gradually bend metal coil into desired cross-sectional profile shapes. Manual roll forming machines are an economical option for small to mid-scale production runs compared to fully automated roll formers. This comprehensive guide covers key aspects of manual roll formers from working principles, types, major components, specifications, applications, installation, operation, maintenance, suppliers, costs and more.
Overview of Manual Roll Forming
Roll forming is a continuous bending operation in which sheet or coil stock is passed through consecutive stands of rolls, each imparting an incremental amount of bend, to form the sheet into desired cross-section profile shapes.
Manual roll forming relies on manual feeding and control of the process rather than electronic automation. An operator manually feeds the coil/sheet stock into the roll former and controls each stand to achieve the desired bending. The operator has full control over the process and can make adjustments as needed.
Manual roll forming is ideal for low to medium production volumes, prototyping, and small shops with space/budget constraints. It offers flexibility, easy changeovers, and lower equipment costs compared to fully automated machines. However, manual operation has slower production rates and demands skilled labor.
Key Advantages of Manual Roll Forming
- Economical for low to medium volumes
- Flexible, easy changeovers between profiles
- Compact, lower cost equipment
- Simpler overall process
- Manual adjustments possible on the fly
- No programming knowledge needed
Limitations of Manual Roll Forming
- Slower production rates than automated
- Labor-intensive operation
- Higher labor costs
- Increased risk of errors
- Not ideal for mass production
- Requires skilled operators
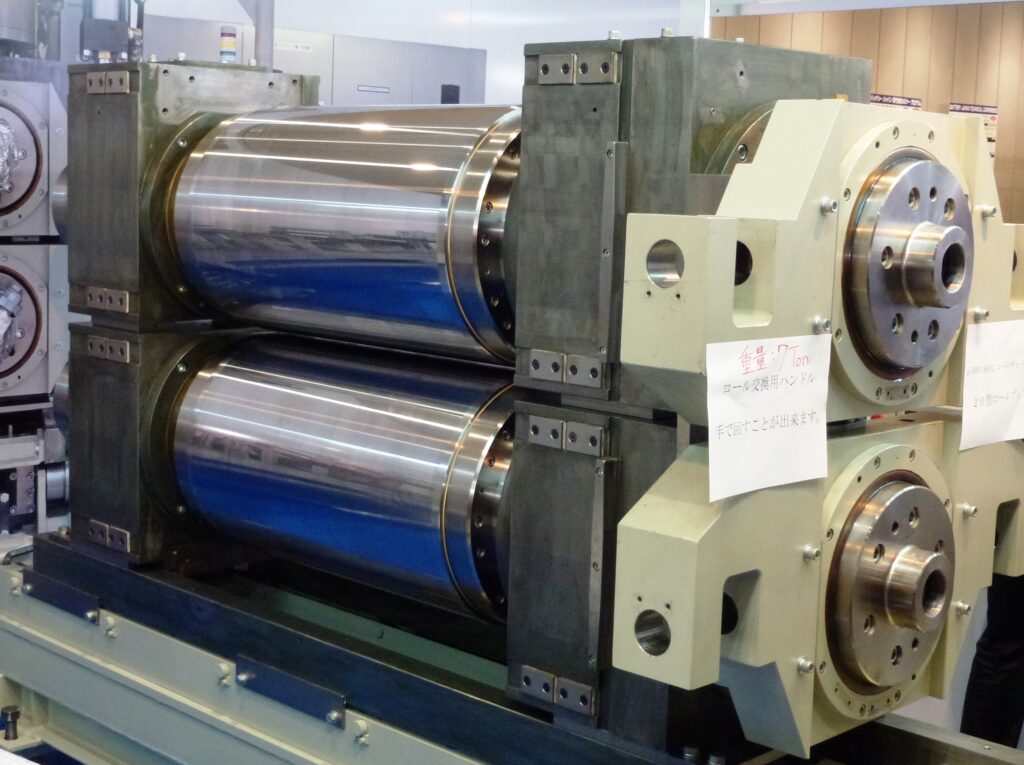
Types of Manual Roll Forming Machines
There are two main types of manual roll forming machines:
Pyramid-Type Roll Formers
Pyramid-type roll formers have each stand arranged diagonally one behind the other in a pyramid shape. This allows a compact footprint and easy operator access. However, design constraints can limit profile capabilities.
Key Features:
- Small footprint
- Easy operator access
- Lower cost
- Profile shape limitations
Inline Roll Formers
Inline roll formers have stands arranged longitudinally in a straight line. The linear design provides flexibility in profile shapes and number of stands. However, the larger footprint requires more space.
Key Features:
- Flexible profile capabilities
- Higher number of stands
- Larger footprint
- Easy length adjustments
Major Components of Manual Roll Formers
Manual roll forming machines consist of three major components – the roll stands, forming rolls, and decoiler:
Roll Stands
Roll stands hold the rolls in position and allow incremental bending of sheet. Number of stands determines profile complexity.
Forming Rolls
Forming rolls have machined contours that gradually bend the sheet when passed through roll gaps. Roll design determines profile shape.
ডিকয়লার
Decoiler holds the coil stock and feeds into the roll former. It provides proper tension and alignment of stock.
Other components like guides, gauges, guards, controls, and power transmission are integrated for smooth functioning.
Specifications of Manual Roll Formers
Key specifications to consider for manual roll forming machines:
Roll Former Type: Pyramid, Inline
Number of Stands: 10-16 typical
Rolls per Stand: 2-4
Roll Diameter: 100-200 mm
Roll Width: 50-120 mm
Forming Thickness: 0.3-3 mm
Forming Width: Up to 1000 mm
Feed Speed: 5-10 m/min
Drive Type: Electric, Hydraulic, Manual
Power: 3-5 kW
Voltage: 220-440V, 3 Phase
Applications of Manual Roll Formed Profiles
Manual roll forming can produce various open and closed structural sections for the following applications:
- Roofing and wall panels
- Steel doors
- Racking systems
- Solar panel frames
- Highway guard rails
- Agricultural equipment
- Rolling shutters
- Lighting poles
- HVAC ducting
- Metal furniture
- Automotive components
With quick roll changeover, various profiles can be produced on the same machine as per application requirements.
Installation of Manual Roll Forming Machines
Proper installation is key for optimum performance of manual roll formers. Here are important guidelines:
- Mount machine on flat, leveled, rigid concrete floor to prevent distortion
- Ensure sufficient clearance around for coil loading and formed profile exit
- Provide 3-phase electrical connections per machine ratings
- Install lockable power disconnect switch nearby
- Ground the machine properly for safety
- Supply adequate lighting for work area
- Position machine optimally for minimal operator movement
- Provide power transmission guards and safety signage
Operation of Manual Roll Forming Machines
Operating manual roll forming machines involves the following steps:
- Understand technical specifications of machine and profile
- Review and select correct rolls, stands as per profile
- Manual loading of coil on decoiler and thread into machine
- Set feed speed, roll gaps, guides
- Initiate machine start and observe initial forming
- Make minor adjustments to achieve desired bends
- Monitor pressure settings, roll alignment during operation
- Inspect quality of formed profile periodically
- Stop machine, change coil, rolls when required
- Maintain steady feed of material and profile exit
- Follow safety procedures at all times
Maintenance of Manual Roll Forming Machines
Regular maintenance is vital for maximum working life of roll formers. Key aspects include:
- Clean machine daily, remove metal chips, dust, dirt
- Lubricate all moving parts as per schedule
- Check roll wear, realign/replace as needed
- Verify proper roll gaps, power transmission tension
- Inspect electrical, hydraulics, drives; repair if issues
- Check decoiler system for coil loading/payout
- Confirm guides, guards, safety devices functioning
- Monitor overall operation for unusual noise, vibration
- Perform preventive maintenance during plant shutdowns
Proper maintenance and operation training of personnel is recommended.
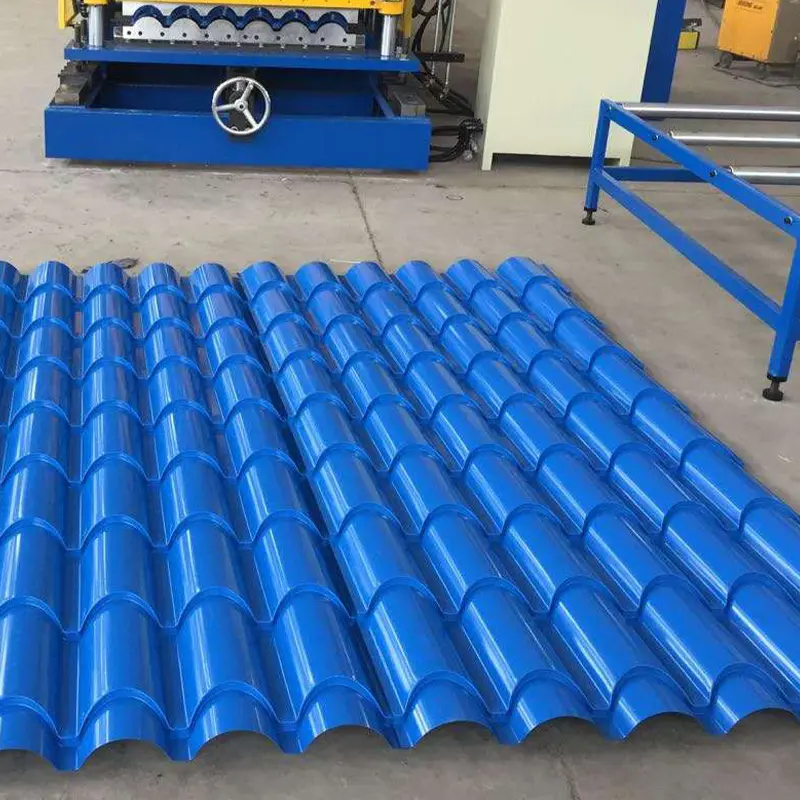
Choosing Suppliers of Manual Roll Forming Machines
Here are important factors to consider when selecting manual roll forming machine suppliers:
Technical Expertise
- Years of experience with technology
- In-house design, engineering capabilities
- Understanding of process requirements
- Provides design support, testing
Machine Quality
- Use of high-quality components
- Precise manufacturing and finishing
- Performance record, client reviews
- Reliability, durability of equipment
কাস্টমাইজেশন
- Ability to customize per application
- Range of model sizes offered
- Flexibility in features, accessories
Service Support
- Responsiveness to technical queries
- Maintenance and operator training
- Inventory of spare parts
- Warranties and service contracts
Pricing
- Overall value compared to quality
- Reasonable cost for features
- Clear breakdown of pricing
Cost Analysis of Manual Roll Forming Machines
Manual roll forming machine cost depends on factors like:
Machine Type and Size: Pyramid or inline design, width, number of stands
Production Capacity: Higher capacity increases cost
Level of Automation: Manual vs. motorized options
Raw Material: Stainless steel vs. mild steel fabrication
Additional Features/Accessories: Decoilers, guides, perforators etc.
Location: Imported machines usually cost more
Here is an approximate price range for different machine capacities:
Production Capacity | Indicative Pricing Range |
---|---|
Up to 20 feet/minute | $8,000 – $15,000 |
Up to 40 feet/minute | $15,000 – $35,000 |
Up to 60 feet/minute | $35,000 – $55,000 |
Up to 80 feet/minute | $55,000 – $75,000 |
Custom or large machines with more features will be priced higher. Get price quotes from shortlisted suppliers.
Pros and Cons of Manual vs. Automatic Roll Forming
Parameter | Manual Roll Forming | Automatic Roll Forming |
---|---|---|
Operational Speed | Slower production rate | High production rates |
Labor Requirements | Labor intensive, high cost | Lower labor, more automated |
Changeovers/Setups | Quick and easy | Slower changeovers |
Operating Costs | Higher operating costs | Lower operating costs |
Initial Investment | Lower equipment cost | Much higher equipment cost |
Ease of Use | Requires skilled operators | Minimal operator skill needed |
Process Control | Manual monitoring and adjustments | Automated monitoring and control |
Product Consistency | Higher variability | More consistent quality |
Profile Complexity | Simpler profiles feasible | Complex profiles achievable |
Ideal Volumes | Short runs, low volumes | Long runs, mass production |
Limitations and Challenges of Manual Roll Forming
Some key limitations and challenges with manual roll forming processes:
- Speed and productivity is low compared to automated machines
- Requires significant operator skill and diligence
- Higher risk of quality errors or deviations
- Frequent roll changing leads to downtime losses
- Size and weight of rolls makes changeovers cumbersome
- Difficult to achieve very complex or asymmetric profiles
- Consistency and precision is harder to maintain
- Not suitable for high volume or continuous production
- Safety hazards from manual feeding and operation
While economical for low volumes, automated roll forming is preferable for higher production rates, precision, and consistency.
Safety Tips for Manual Roll Forming Operation
- Wear protective gloves when handling sheet metal
- Ensure forming area is clear before machine start
- Stop operation to make adjustments; no live adjustments
- Keep hands away from roll bites and sheet entry areas
- Maintain a safe distance from moving components
- Monitor for any abnormal noise or vibration
- Follow lockout/tagout procedures during maintenance
- Keep work area clean and free of slip/trip hazards
- Know emergency stop procedures for the machine
- Review safety procedures regularly with operators
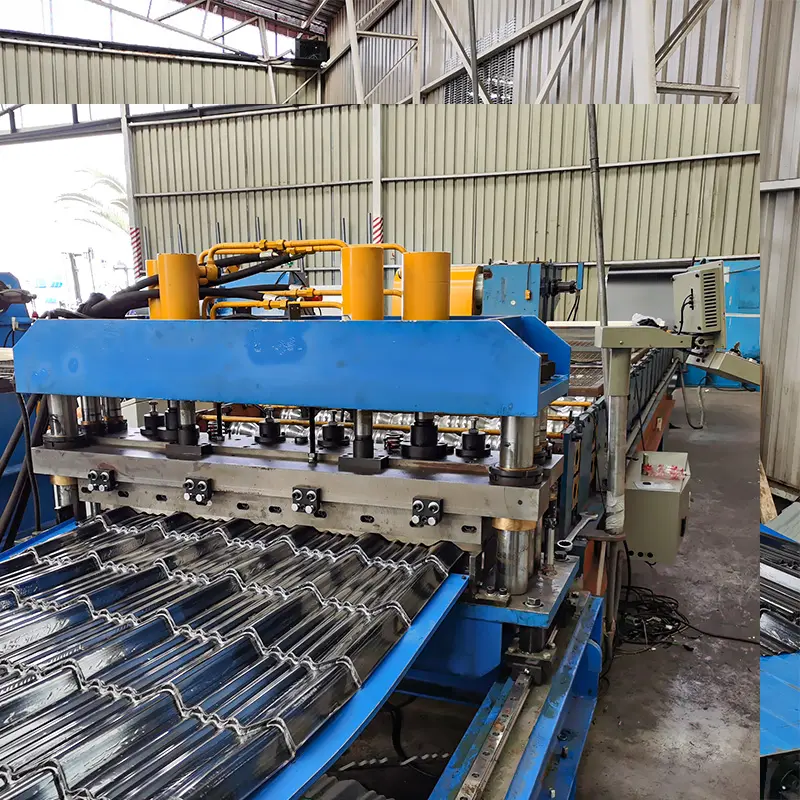
FAQ
What materials can be roll formed on a manual machine?
- Most ductile metals like low carbon steel, stainless steel, aluminum. Not suitable for hard metals or plastics.
What thickness range can be manually roll formed?
- Sheet thickness from 0.3mm to about 3mm can be typically processed.
What profiles can be formed on manual roll formers?
- Various open and closed sections like channels, rails, frames, columns etc. Complexity depends on number of stands.
How many operators are required?
- Typically 1-2 operators for tasks like feeding, adjustment, part offloading.
How quick are roll changes on manual machines?
- An experienced operator can change rolls sets in 30-60 minutes. More complex profiles take longer.
What maintenance is required?
- Daily cleaning, lubrication, periodic roll changes, electrical and mechanical inspection, alignment checks.
What safety equipment should be used?
- Gloves, eye protection, overalls, steel toe boots, hair/loose clothing coverage.
What defects can occur in manual roll forming?
- Wavy edges, twist, bow, flaring, splitting – often due to worn rolls, improper alignment, feed defects.
How is piece length controlled?
- By counting rotations of the main drive shaft via a digital counter or encoder.
Can existing machines be upgraded to motorized?
- Yes, retrofits are possible to add powered decoilers, drives, and controls for semi-automation.
উপসংহার
Manual roll forming provides a cost-effective forming solution for low to medium production volumes. With proper machine selection, installation, operation and maintenance, quality profiles can be produced for various applications. However, for higher volumes and advanced profiles, automated roll forming is recommended. This guide covers key considerations for manufacturers looking at manual roll forming processes.