Overview of Slide Rail Roll Forming Machines
Slide rail roll forming machines are used to produce long, straight metal parts with cross-sectional profiles by progressively bending a strip of sheet metal as it passes through a series of stands. The stands contain rollers that apply pressure to the sheet to gradually shape it.
Slide rail roll forming machines are advantageous for high volume production of parts with constant cross-sections like metal studs, roofing panels, highway signage, steel door panels etc. They offer high forming accuracy and fast production rates compared to press brakes or other bending methods.
Some key features of slide rail roll formers:
- Produce parts with complex cross-sections like C, U, Z, hat, box channels etc.
- Use coil raw material up to 1.6mm thickness, 1500mm width
- Form parts up to 10m length
- Quick roll set changeover
- PLC touchscreen controls -produce 20-50 meters/minute depending on part complexity
Types of Slide Rail Roll Forming Machines
There are two main types of slide rail roll forming machines:
Horizontal Roll Forming Machines
- Sheet metal fed horizontally into forming stands
- Suitable for small to medium parts
- Limited part width due to horizontal feed
- Lower cost compared to vertical machines
Vertical Roll Forming Machines
- Sheet metal fed vertically into forming stations
- Handles large width coils upto 1500mm
- Higher production rates possible
- Advanced features like automation, quick die change etc.
- Possibility to add additional operations like punching, cutting, stacking
- Higher initial capital cost
Main Components of a Slide Rail Roll Former
A slide rail roll forming system consists of the following main components:
- আনকোয়লার – Feeds raw coil stock into machine
- Forming stands -progressively shape the profile with upper and lower rolls
- Slide rails – Guide sheet through forming stands
- Servo motor drives – Adjust roll spacing and profiles
- Decoiler/Recoiler – Coils finished parts
- Cut-off press – Cuts parts to length
- Control panel – Adjusts machine settings and parameters
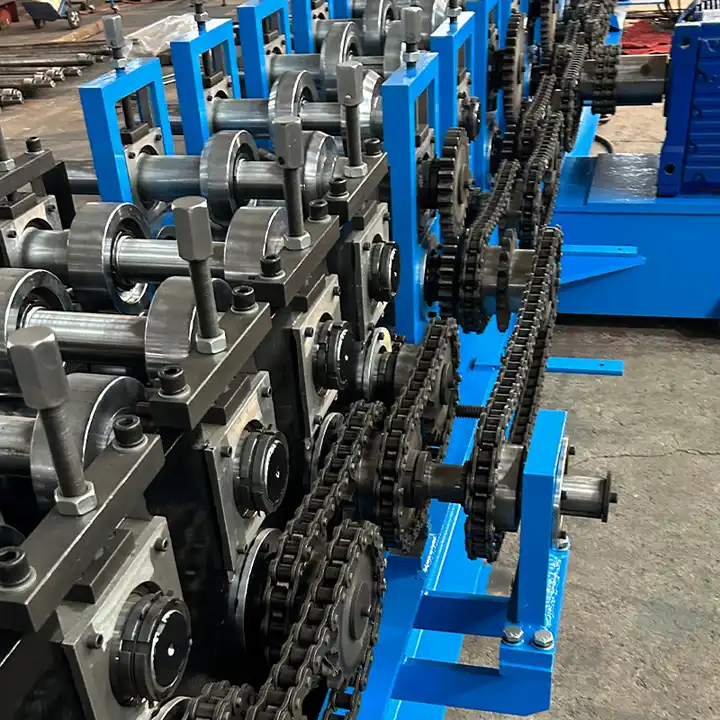
Typical Specifications of Slide Rail Roll Forming Machines
পরামিতি | Typical Values |
---|---|
গঠন গতি | 20 – 50 m/min |
Maximum Part Width | Up to 1500 mm |
Maximum Part Thickness | 0.5 to 1.6 mm |
Minimum Bending Radius | 1 x Material Thickness |
Forming Stands | 10 – 50 |
Main Drive Power | 5.5 – 22 kW |
Roller Diameter | 120 – 140 mm |
Roller Hardness | 50 – 55 HRC |
বেলন উপাদান | Alloy Steel |
Machine Weight | 8000 – 25000 kg |
Popular Standard Sizes
Machine Size | Coil Width Capacity |
---|---|
Small | 650 mm |
Medium | 800 – 1000 mm |
Large | 1300 – 1500 mm |
Applications of Slide Rail Roll Forming Machines
Slide rail roll formers are ideal for producing metal parts with the following profiles and applications:
পণ্য | Description |
---|---|
Roofing Panel | Trapezoidal, corrugated, galvalume sheets |
Drywall Studs | C-channel, U-channel interior wall studs |
Highway Guardrails | W-beam, thrie beam crash barriers |
Garage Doors | Ribbed steel door panels |
Rack Posts | Structural support columns for warehouses |
Solar Mounting | C-channel, Z-purlin for solar panel frames |
Highway Signs | Aluminum sign boards and supports |
HVAC Ducting | Spiral ducts for ventilation systems |
Choosing a Slide Rail Roll Forming Machine Supplier
When selecting a slide rail roll former, buyers should evaluate suppliers on the following parameters:
- Years of experience in roll forming equipment
- Range of machine sizes offered
- Use of quality components like European PLCs, motors, hydraulics
- Quick die changeover features
- Offer customized roll tooling as per part drawings
- Provide CAD support, simulations and design review
- Have in-house roll tooling design and manufacturing capability
- Offer operator training and after-sales support
- CE certifications for safety and quality
- Responsiveness to RFQs and technical queries
- Competitive pricing and financing options
Some of the leading slide rail roll former manufacturers are:
প্রতিষ্ঠান | Location |
---|---|
Shanghai Slitter | China |
Formtek | Taiwan |
SIPCO Machinery | China |
EWMenn | Germany |
DIMECO | USA |
Bradbury | USA |
How to Choose the Right Slide Rail Roll Former
When selecting a slide rail roll forming machine, users should consider the following factors:
Part Profile
- Choose machine capacity 25% more than max part width
- Select type of machine based on part length
- Ensure machine can handle thickness and bend radii required
Production Volume
- Higher volume applications need heavier duty machine
- Opt for quicker die change, automation features
- May require decoiler and finishing operations
Material Type
- Mild steel machines sufficient for most applications
- Stainless steels may need polished rolls
- Aluminum needs specialized tooling and oxidation prevention
Speed and Precision
- Machines with servo motor drives offer better speed control
- More number of forming stands increase precision
- Roll materials, bearings, guides influence finish quality
Budget
- Balance performance vs. initial cost
- Consider long term TCO including maintenance, downtime
- Local machines cheaper but may compromise quality
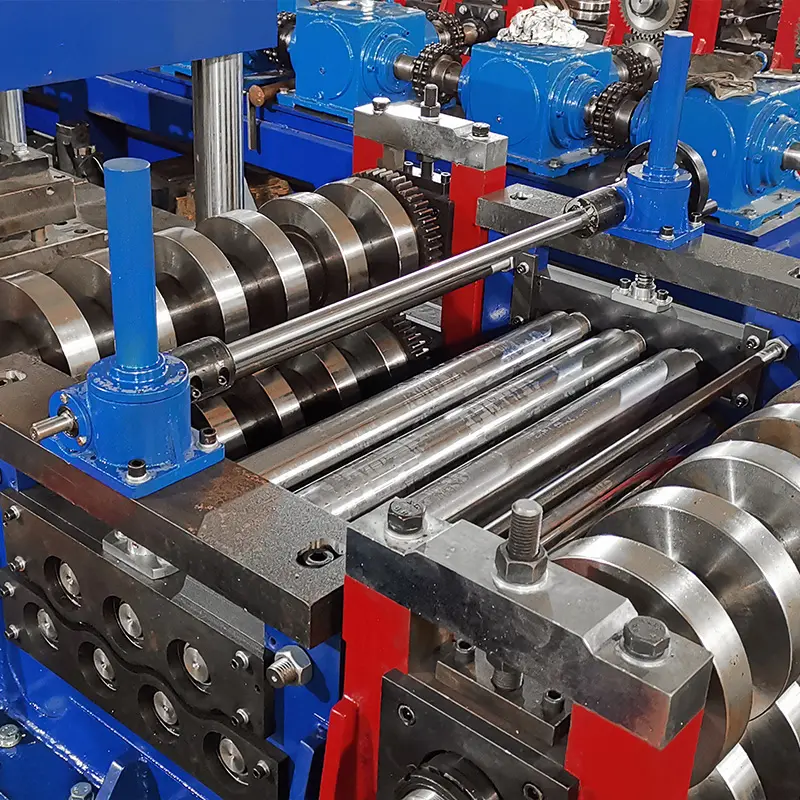
Pros and Cons of Slide Rail Roll Forming Machines
Advantages | Disadvantages |
---|---|
High production rates up to 50 m/min | Initial capital cost is high |
Consistent and accurate part dimensions | Regular maintenance required |
Flexible production using quick die change | Fixed tooling only makes one profile |
Low material waste | Skill needed to set up and operate |
Suitable for high volume production | Size limited by coil width capacity |
Automated processes possible | Changing profiles needs roll changeover |
Safer operation than press brakes | Limited thickness and strength of materials |
Slide Rail Roll Forming Machine Operation
Operating a slide rail roll former involves the following steps:
1. Mount Tooling
- Install correct upper and lower rolls on stands as per part profile
2. Thread Coil
- Place raw coil on decoiler and thread through stands
3. Set Parameters
- Input material specs, part length, speed on control panel
4. Initiate Process
- Start machine and feed metal sheet into forming section
5. Monitor Operation
- Check formed part shape and adjust settings if needed
6. Finish parts
- Cut formed sections to length with shears
- Remove waste and stack finished parts
Maintenance of Slide Rail Roll Formers
Regular maintenance is crucial for trouble-free operation and output quality. Main activities include:
- Daily cleaning of machine, especially forming rolls
- Lubricating bearings, gears, motors as per schedule
- Checking oil levels and pressures in hydraulics
- Inspecting all electrical connections and wiring
- Verifying proper functioning of sensors and switches
- Checking for any abnormal noise or vibration
- Monitoring roll and guide wear and replacing as needed
- Keeping tension consistent on rolls using load cells
- Scheduling preventive maintenance during plant shutdowns
Proper maintenance as per the manual will minimize unplanned downtime and extend machine life.
FAQ
Q: What materials can be formed on slide rail roll formers?
A: Most machines can form low carbon steel, stainless steel, or aluminum sheets up to about 1.5 mm thickness. With customized tooling, some can also form brass, copper.
Q: How quick is the die changeover?
A: On average, a die changeover takes 15-20 minutes on standard machines. More advanced ones have quick change systems that reduce this to under 5 minutes.
Q: What tolerances are achievable on slide rail roll formed parts?
A: Dimensions on roll formed parts can be held to +/- 0.5mm over 10 m part length for standard machines. With servo drives and more forming stands, tolerances of +/- 0.3mm are possible.
Q: What is the difference between horizontal and vertical roll forming machines?
A: Horizontal machines feed sheet horizontally into stands, limiting part width. Vertical machines feed sheet vertically allowing larger widths but take up more floor space.
Q: How long do slide rail roll forming machine lasts?
A: With proper maintenance and operation, the machine frame and mechanics can function for 15-20 years. Rolls, bearings, and electrical parts may need replacement every 5-8 years.
Q: What factors affect the roll forming speed?
A: Roll forming speed depends on material thickness, yield strength, number of forming stands, part complexity, straightness of raw material, and main drive power.
Q: How to get the best quality finish on roll formed parts?
A: Maintaining consistent roll pressures, using polished tooling, ensuring proper machine alignment, and tension control yields the best finish. Cleaning rolls also improves surface quality.
Q: What safety aspects should be considered when using roll formers?
A: Key safety features are emergency stops, light curtains near forming area, overload protection, guards on moving parts, and training operators on procedures. Proper PPE when handling coils is also important.