Barrel corrugated forming machines are industrial equipment used for producing corrugated sheets and panels from metal coils. These versatile roll forming systems allow efficient, high-volume production of curved corrugated sheets ideal for roofing, siding, drainage, and decorative purposes across industries.
In this comprehensive guide, we will explore all key aspects of barrel corrugated forming machines from working principles, main parts, technical specifications, to applications and cost considerations. Whether you are looking to purchase these machines or just researching the latest advancements in this domain, this content has got you covered!
How Barrel Corrugated Forming Machines Work
Barrel corrugated forming utilizes a unique roll forming technique to shape metal coil stock into sinusoidal wave-like corrugated panels. Here are the key steps involved:
- Feeding – Coiled aluminum, galvanized steel, stainless steel or other metal sheets get loaded into a de-coiler. This supplies continuous strips of metal sheet to the forming section.
- Corrugation forming – As the metal sheet passes between different sets of gear-like forming rolls, it gets gradually bent and shaped into curved corrugations by each roller set applying targeted pressure.
- Cutting – Formed metal gets cut at required lengths by built-in cutting tools to produce finished corrugated sheets as per dimensions.
- Collection – Conveyors collect fabricated corrugated sheets and transport them for storage or additional fabrication.
So in summary, barrel corrugators progressively shape flat metal coils into rippled corrugated sheets through controlled deformation using an interconnected arrangement of custom metal forming rollers. Users can produce high volumes of uniform curved corrugated metal effortlessly.
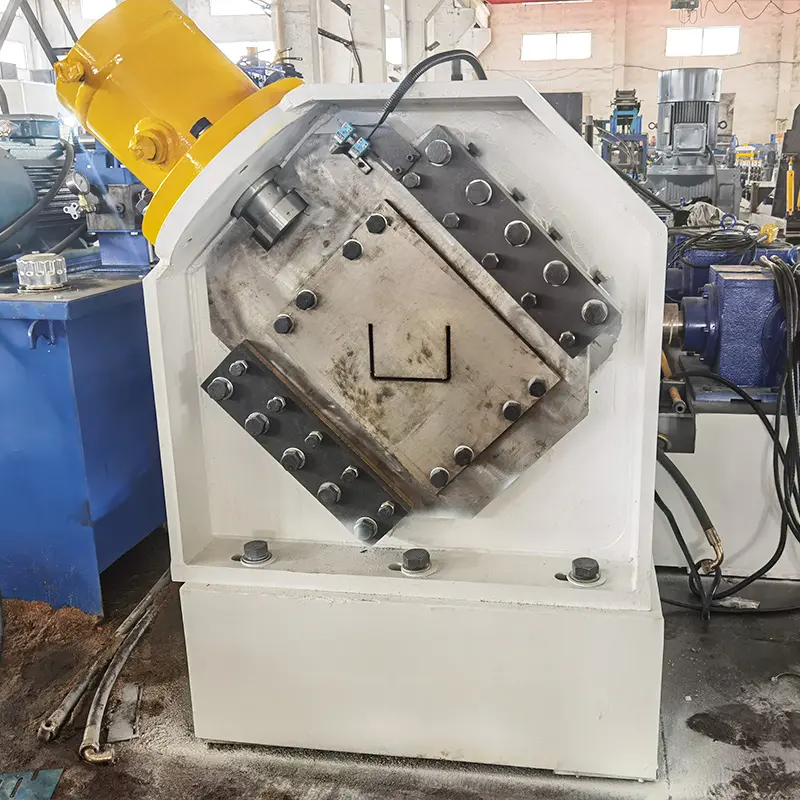
Main Parts of Barrel Corrugated Machines
Barrel corrugators comprise two key sections – the forming section with rolling dies, guides, and accessories – and the electrical control system to manipulate sheet forming:
Forming Section Parts
- De-coiler – Feeds continuous metal sheet stock
- Guiding rollers – Aligns metal sheets
- Corrugation rollers – Forms rippled curved sheets
- Profile cutting tools – Trims formed sheets
- Supporting rolls – Assists sheet movement
- Conveyors – Transports finished sheets
Electrical Control System
- PLCs – Controls roller sequencing
- HMI touchscreen – Inputs configurations
- Servo motors – Drives rollers with precision
- Sensors – Enable automation & safety
The modular forming section coupled with smart programmable controls enables adjusting sheet dimensions, corrugation profiles, outputs via recipes rather than mechanical changes.
Specifications
Barrel corrugators can produce profiles with standard specifications or custom sizes as per application requirements:
Parameters | Typical Range |
---|---|
Sheet Width | Up to 2500 mm |
Sheet Length | 300 mm to 10000 mm |
Sheet Thickness | 0.15 mm to 2.0 mm |
Corrugation Height | 5 mm to 100 mm |
Corrugation Pitch | 6 mm to 230 mm |
Production Speed | 1 m/min to 15 m/min |
Production Volume | 100 mt/month to 2000 mt/month |
Working Principle
The working principle involves:
- Progressive indirect compression – Unlike direct roller pressure, each roller set incrementally forms the curves through regulated nips
- Low radial forces – Curved profile of rolls allows gradual bending rather than high radial stress
- Synchronized positioning – Precisely aligns corrugation crests & troughs using servomotors
These enable achieving very fine corrugations throughout sheet length without defects or damage.
Advantages
- Highly versatile – Produces varied corrugation dimensions and metals
- Superior quality – Smooth uniform finish without flaws
- High productivity – Fast, efficient forming in high volumes
- Compact, modular – Adapts even in space constraints
- Smart automation – For consistency with easy changeovers
- Lower maintenance – Compared to direct forming methods
Applications
Major application areas include:
- Roofing, Cladding – Sinusoidal profile roof sheets, wall cladding
- Interior Design – Decorative corrugated metal for aesthetics
- Fencing – Rippled fence sheets offer strength
- Drainage Solutions – Allows flow for drainage pipes, culverts
And many more across construction, infrastructure, manufacturing verticals.
Cost Considerations
Parameters | Indicative Price Range |
---|---|
Manual Barrel Corrugator | $5000 to $15000 |
Automatic Barrel Corrugator | $15000 to $50000 |
Heavy-duty Industrial Spec | $50000 to $200000 |
Costs vary based on:
- Degree of automation & output rates
- Construction materials & durability
- Additional customizations & accessories
- Associated tooling, handling, infrastructure
- Geographic location & import duties
Reaching out to vendors for quotations based on your specific production requirements is recommended.
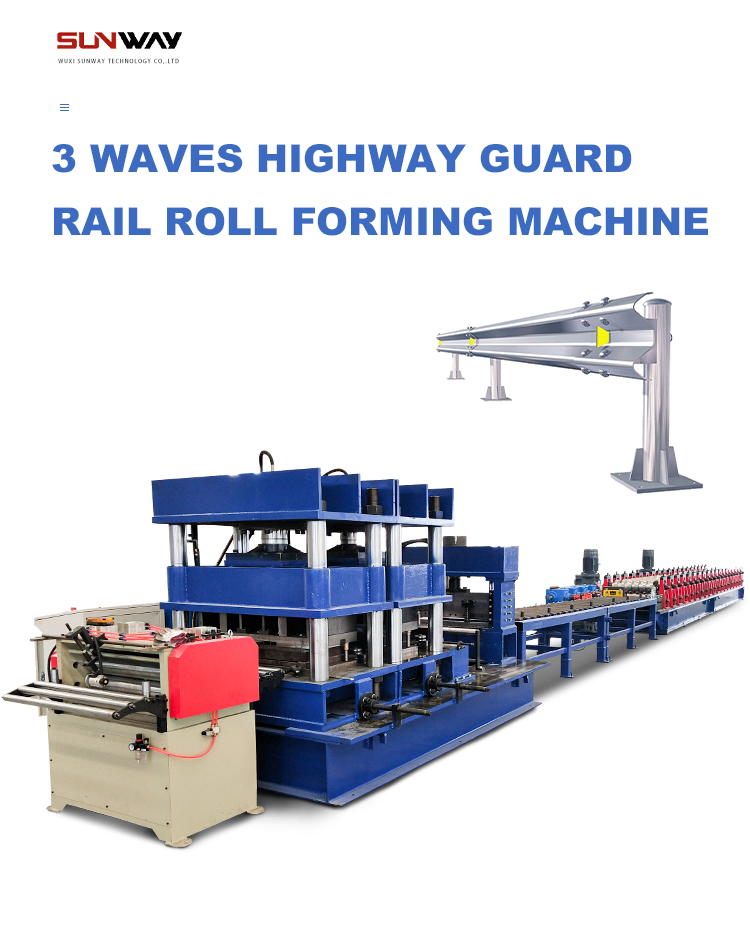
FAQ
Q: Are barrel corrugators better than direct sheet corrugators?
A: Yes, barrel corrugators offer better quality sheets with lower defects compared to direct corrugation under high pressures between rollers.
Q: Can these form very large 5 meter width sheets?
A: Yes, custom built heavy-duty corrugators are available to form extra wide coil sheets upto 5 meters.
Q: Can these machines make curved sheets only?
A: No, most barrel corrugators can also produce conventional straight corrugated sheets alongwith curved profiles.
Q: How easy is it to alter formed profiles?
A: Simple software changes allow adjusting parameters like pitch, depth and more for fast flexibility.
Q: What accuracy and finish levels are possible?
A: Advanced machined roller dies can achieve under +/- 0.5 mm dimensional accuracy and less than 1 micron surface roughness.