Introduction
In the world of metal fabrication, efficiency and precision are paramount. Manufacturers and construction industries seek innovative solutions to produce metal profiles with consistency and cost-effectiveness. Angle iron roll forming machines have emerged as a game-changer in this domain, revolutionizing the way angle iron profiles are manufactured. This article delves into the workings of an angle iron roll forming machine, its applications, advantages, and how it has transformed metalworking processes.
Understanding Angle Iron Roll Forming Machine
Angle iron roll forming machines are specialized equipment designed to transform flat metal strips or coils into precise angle iron profiles. The machine operates through a continuous bending process, where the metal undergoes a series of roll forming stations to achieve the desired shape. The process ensures uniformity and accuracy, making it ideal for mass production of angle iron profiles.
The Working Principle of Angle Iron Roll Forming Machine
The working principle of an angle iron roll forming machine is based on sequential roll forming. The machine consists of a series of rollers, each designed to bend the metal gradually. The flat metal strip passes through these rollers, and with each station, it takes on the shape of the angle iron profile. The rollers are strategically positioned to perform specific bends, and the material progresses through the stations until the final shape is attained.
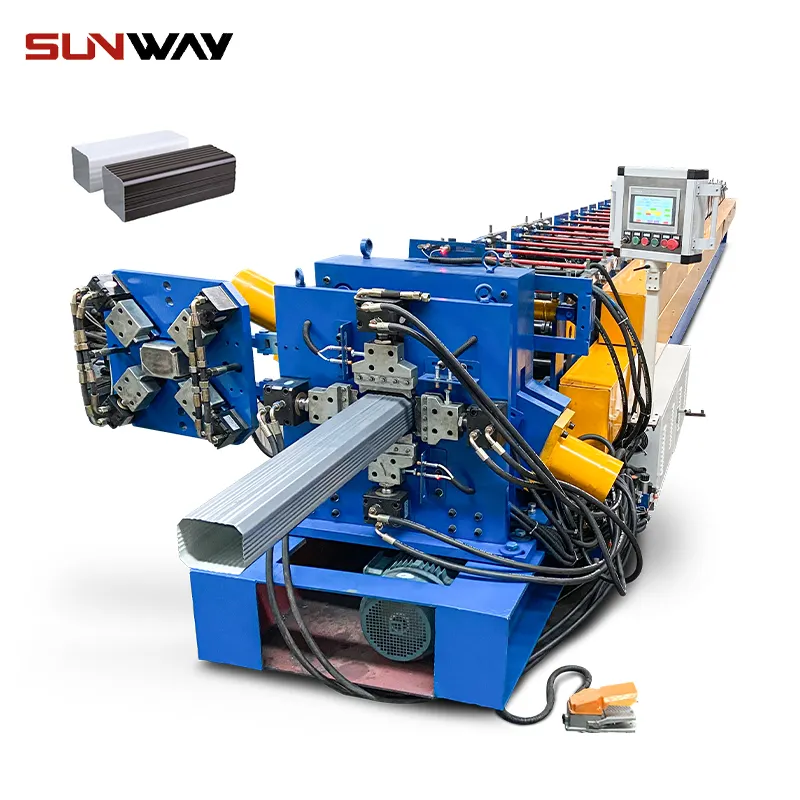
Key Components of Angle Iron Roll Forming Machine
To achieve efficient and precise roll forming, angle iron roll forming machines are equipped with several key components. These include:
- Decoiler: The decoiler holds the metal coil or strip, providing a continuous feed to the roll forming process.
- Rollers: The heart of the machine, these rollers are responsible for shaping the metal into the desired angle iron profile.
- Cutoff System: This system cuts the angle iron to the required length after forming, ensuring accurate and consistent pieces.
- Control Panel: The control panel allows operators to adjust settings, monitor the process, and ensure smooth operation.
Types of Angle Iron Roll Forming Machines
There are two primary types of angle iron roll forming machines:
Single-Station Angle Iron Roll Forming Machine
The single-station machine is suitable for manufacturing simple angle iron profiles with limited customization options. It is a cost-effective solution for smaller-scale production needs.
Multi-Station Angle Iron Roll Forming Machine
The multi-station machine is equipped with multiple roll forming stations, allowing for more complex and customized angle iron profiles. It is ideal for high-volume production and diverse profile requirements.
Advantages of Using Angle Iron Roll Forming Machine
Angle iron roll forming machines offer numerous advantages over traditional manufacturing methods:
- Efficiency: The continuous roll forming process ensures high-speed production with minimal material waste.
- Accuracy: The precision of roll forming guarantees uniform and consistent angle iron profiles.
- Cost-Effective: Reduced material wastage and increased productivity lead to cost savings in the long run.
- Versatility: The ability to create custom profiles makes it suitable for a wide range of applications.
Applications of Angle Iron Roll Forming Machine
Angle iron profiles find applications in various industries, including:
- Construction: Angle irons are widely used for structural support in building frameworks.
- Furniture: They serve as braces and supports in various furniture designs.
- Automotive: Angle iron profiles are used in vehicle frames and chassis.
- Storage Systems: They are employed in manufacturing shelving and storage racks.
- Appliances: Angle iron profiles are utilized in the assembly of appliances and machinery.
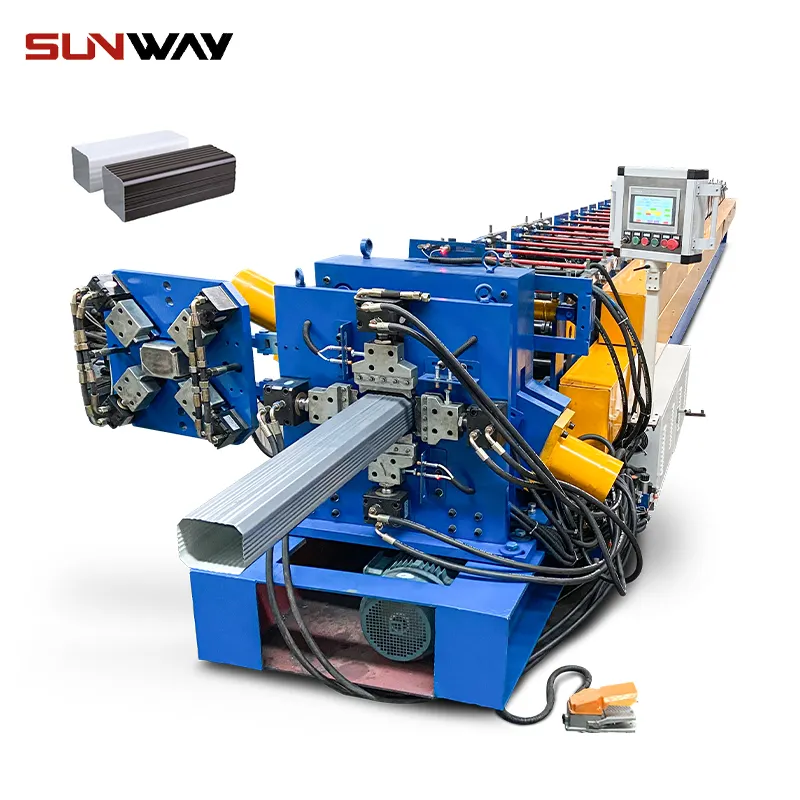
Choosing the Right Angle Iron Roll Forming Machine
Selecting the right angle iron roll forming machine is crucial for efficient production. Consider the following factors before making a decision:
Material Compatibility
Ensure that the machine is compatible with the types and thicknesses of metal you plan to use.
Production Speed and Efficiency
Assess the machine’s production speed and overall efficiency to meet your output requirements.
Customization Options
If you need to produce custom angle iron profiles, opt for a machine with flexible customization capabilities.
Budget Considerations
Evaluate the machine’s cost against its features and long-term benefits to make an informed investment.
Maintenance and Care of Angle Iron Roll Forming Machine
To ensure optimal performance and longevity, regular maintenance is essential. Some maintenance tips include:
- Lubrication: Regularly lubricate moving parts to reduce friction and wear.
- Inspections: Conduct routine inspections to identify any signs of wear or damage.
- Cleaning: Keep the machine clean and free from debris that could affect its operation.
Tips for Improving Efficiency and Productivity
Here are some strategies to enhance the efficiency and productivity of your angle iron roll forming process:
- Optimize Setup: Minimize changeover times by optimizing the setup process.
- Material Handling: Streamline material handling to reduce downtime between batches.
- Operator Training: Provide comprehensive training to operators for smooth operation.
Safety Precautions When Operating the Machine
Safety is paramount when operating an angle iron roll forming machine. Ensure the following precautions are observed:
- Training: Only trained personnel should operate the machine.
- Protective Gear: Operators must wear appropriate safety gear, including gloves and goggles.
- Emergency Stop: The machine should be equipped with an emergency stop button for immediate shutdown if required.
- Safety Guards: Install safety guards to prevent accidental contact with moving parts.
The Future of Angle Iron Roll Forming Technology
As technology continues to advance, angle iron roll forming machines will likely see further improvements. These may include:
- Automation: Increased automation for even higher production efficiency.
- Material Innovations: Utilizing new materials for enhanced performance and sustainability.
- Smart Controls: Integration of smart controls and data analytics for better process monitoring.
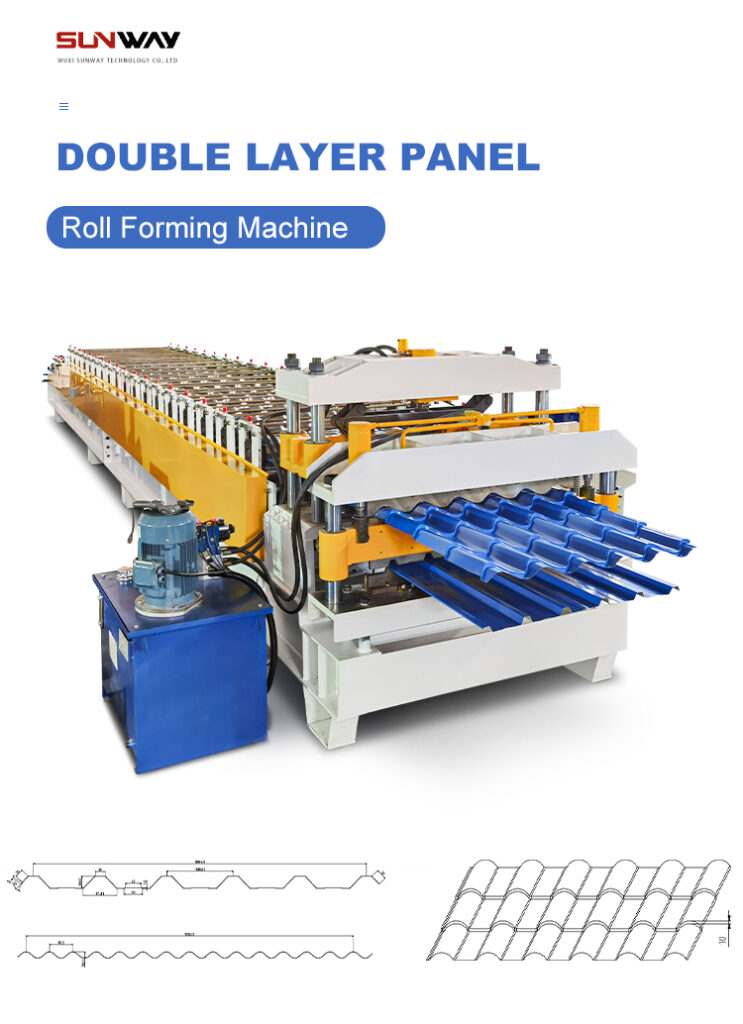
Conclusion
Angle iron roll forming machines have transformed metal profile production, offering speed,accuracy, and cost-effectiveness for various industries. By understanding the working principle and key components of these machines, manufacturers can make informed decisions about which type of angle iron roll forming machine suits their production needs best. The advantages of using such machines, including efficiency, accuracy, and versatility, make them a valuable asset in modern metalworking processes.
FAQs
What is the typical output capacity of an angle iron roll forming machine?
The output capacity of an angle iron roll forming machine can vary based on factors such as the machine’s size, speed, and complexity. However, it is not uncommon for these machines to produce hundreds of meters of angle iron profiles per hour.
Can angle iron roll forming machines handle different materials?
Yes, angle iron roll forming machines can handle various materials, including steel, aluminum, and other metals. The machine’s compatibility with different materials can be adjusted through settings and tooling changes.
Is it possible to create custom angle iron profiles with this machine?
Absolutely! Modern angle iron roll forming machines offer customization options, allowing manufacturers to create unique and tailored angle iron profiles according to their specific requirements.
How often should the machine be inspected and maintained?
Regular inspections and maintenance are essential to ensure the machine’s optimal performance and longevity. It is recommended to conduct routine inspections at least once a month and perform maintenance tasks, such as lubrication and cleaning, as needed.
Are angle iron roll forming machines user-friendly for operators?
Yes, angle iron roll forming machines are designed to be user-friendly, and with proper training, operators can quickly become proficient in operating these machines. Safety features and clear control panels contribute to an operator-friendly experience.