Introduction
The Ameco roll forming machine is a versatile and efficient manufacturing tool used in various industries for shaping continuous metal sheets into desired profiles. It offers numerous benefits, including increased productivity, cost savings, and customization options. In this article, we will explore the features, applications, working principles, and factors to consider when choosing an Ameco roll forming machine.
What is Ameco Roll Forming Machine?
The Ameco roll forming machine is a precision engineering tool designed to shape metal sheets into specific profiles through a continuous bending process. It consists of a series of rolls that gradually shape the metal as it passes through the machine. This versatile machine can produce complex profiles with high precision and consistency.
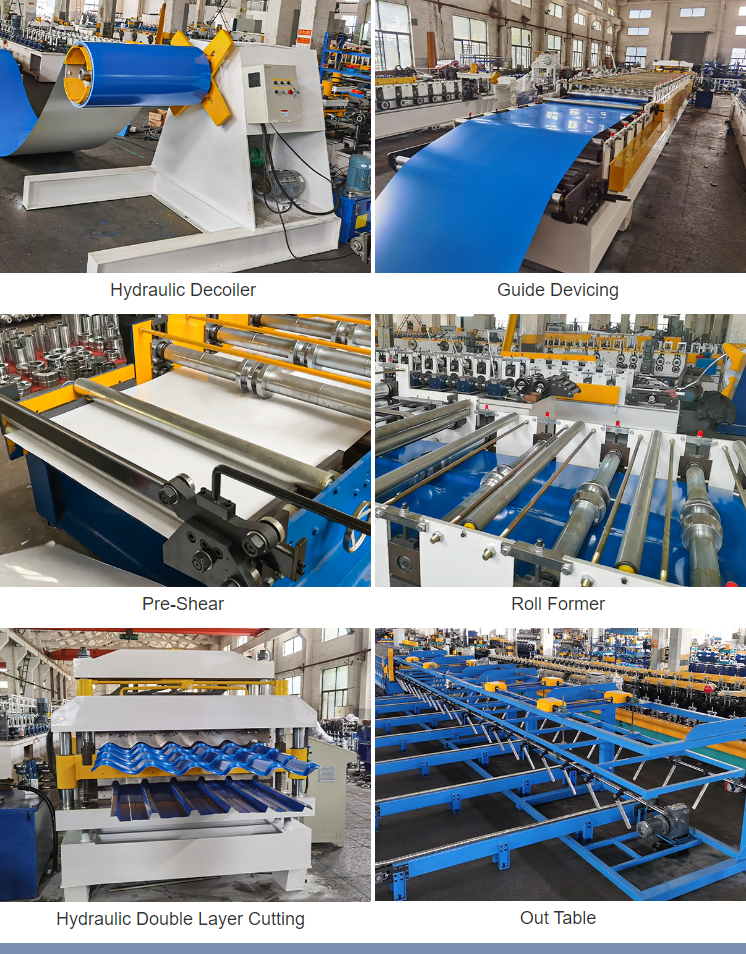
Benefits of Ameco Roll Forming Machine
Increased Efficiency and Productivity
One of the significant advantages of the Ameco roll forming machine is its ability to significantly increase efficiency and productivity. The continuous roll forming process allows for high-speed production, reducing cycle times and increasing output. By automating the shaping process, the machine eliminates the need for manual labor, minimizing errors and increasing overall production capacity.
Cost Savings
The Ameco roll forming machine offers cost-saving benefits compared to other metal shaping methods. The continuous process reduces material waste as the machine precisely shapes the metal sheets with minimal scrap. Additionally, the machine’s high-speed production capability helps manufacturers meet tight deadlines and reduce labor costs.
Versatility and Customization
With the Ameco roll forming machine, manufacturers have the flexibility to create a wide range of profiles for various applications. The machine allows for customization, enabling manufacturers to produce specific shapes and dimensions to meet their customers’ requirements. Whether it’s complex automotive parts or simple construction components, the Ameco roll forming machine can deliver the desired results.
Quality and Precision
The Ameco roll forming machine ensures consistent quality and precision in every profile it produces. The machine’s precise control over the shaping process guarantees uniform dimensions and tolerances, resulting in high-quality finished products. This level of precision is crucial in industries such as automotive and construction, where accuracy is paramount.
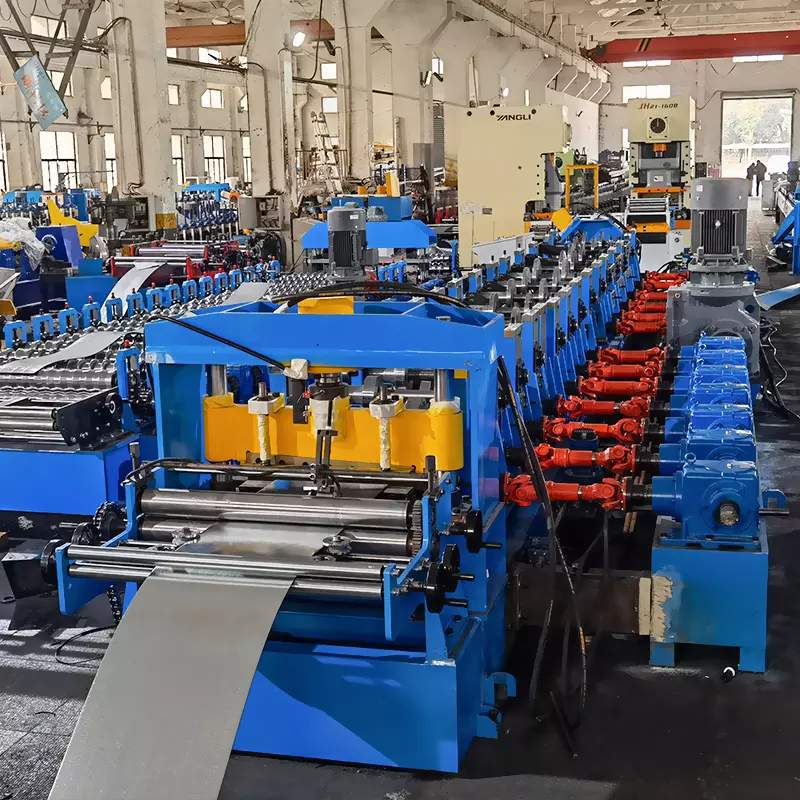
Industries and Applications
The Ameco roll forming machine finds application in various industries due to its versatility and efficiency. Some common industries where the machine is used include:
Automotive
In the automotive industry, the Ameco roll forming machine is used to produce parts such as chassis components, seat tracks, and structural reinforcements. The machine’s ability to shape complex profiles with tight tolerances makes it an ideal choice for automotive manufacturers.
Construction
In the construction industry, the Ameco roll forming machine is utilized to manufacture building components such as roofing panels, wall studs, and window frames. The machine’s high-speed production capability and customization options enable efficient construction processes.
HVAC
The HVAC industry benefits from the Ameco roll forming machine’s ability to shape ductwork components with precise dimensions. The machine can produce various profiles for air conditioning ducts, ventilation systems, and other HVAC applications.
Furniture
The furniture industry utilizes the Ameco roll forming machine to manufacture metal parts for furniture frames, shelves, and drawers. The machine’s versatility allows furniture manufacturers to create unique profiles and designs.
How Does Ameco Roll Forming Machine Work?
The Ameco roll forming machine follows a series of steps to transform a metal sheet into a desired profile. The typical roll forming process involves the following stages:
Material Feeding
The process begins with the feeding of a metal coil into the roll forming machine. The coil unwinds, and the metal sheet passes through a series of rollers, which gradually shape the material.
Roll Forming Process
As the metal sheet progresses through the machine, each set of rollers shapes the material further. The rollers are precisely positioned and designed to gradually bend the metal into the desired profile. Multiple roll stations may be used to achieve complex profiles.
Cutting and Shearing
Once the metal sheet has been formed into the desired profile, the Ameco roll forming machine incorporates cutting and shearing mechanisms to separate the shaped part from the remaining material. Various cutting methods, such as flying cut-off or post-cutting, can be employed depending on the specific application.
Additional Operations
In some cases, additional operations may be required after the roll forming process. These operations can include punching holes, embossing patterns, or adding surface finishes. These steps are integrated into the machine, ensuring the final product meets the required specifications.
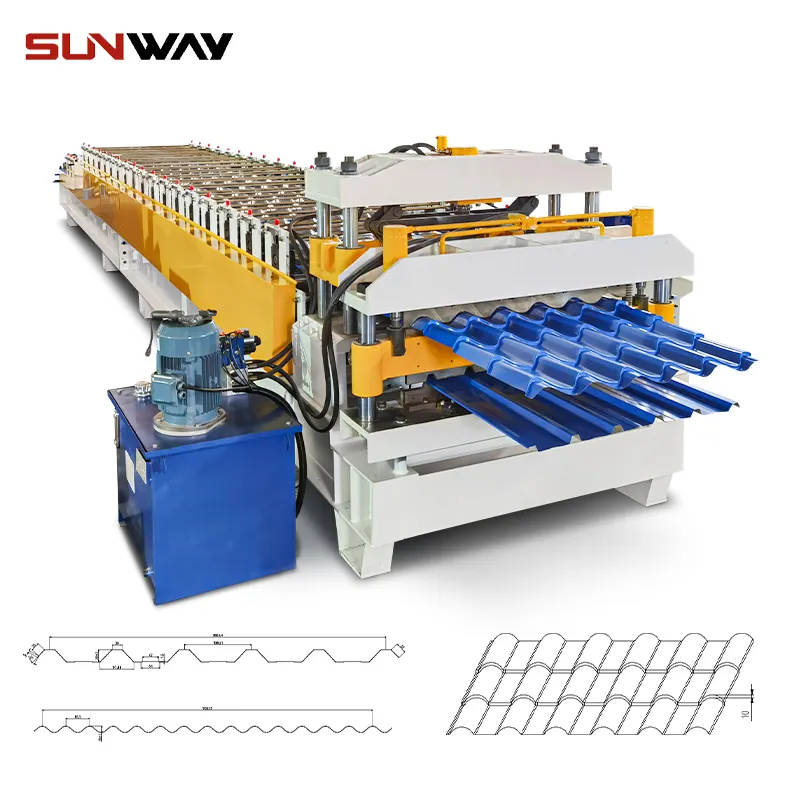
Factors to Consider When Choosing an Ameco Roll Forming Machine
Selecting the right Ameco roll forming machine for your manufacturing needs involves considering several factors:
Production Volume and Speed
The production volume and desired speed are crucial factors when choosing an Ameco roll forming machine. Evaluate your production requirements and select a machine that can handle the desired output without compromising quality.
Material Thickness and Width
Consider the thickness and width of the materials you will be working with. Different machines are designed to accommodate specific material dimensions, so ensure the machine you choose can handle your required material specifications.
Tooling Options
The availability of different tooling options is important when selecting an Ameco roll forming machine. Determine the range of profiles and shapes you need to produce, and ensure the machine’s tooling options can accommodate your requirements.
Machine Flexibility
Evaluate the flexibility of the machine in terms of profile changes and adjustments. A machine that allows for quick and easy tooling changes will enable you to adapt to different production needs efficiently.
Maintenance and Support
Consider the availability of maintenance support and spare parts for the chosen Ameco roll forming machine. Ensure the manufacturer provides proper technical assistance, training, and quick access to spare parts to minimize downtime and ensure smooth operation of the machine in the long run.
Common Challenges and Solutions
While the Ameco roll forming machine offers numerous benefits, there are some common challenges that manufacturers may encounter during operation. Understanding these challenges and implementing appropriate solutions is essential for maximizing productivity. Here are a few common challenges and their solutions:
Material Jamming
Material jamming can occur when the metal sheet gets stuck or tangled within the machine, causing production delays and potential damage to the machine. To prevent material jamming, regular maintenance and cleaning of the machine’s rollers and feeding mechanisms are essential. Proper lubrication and adjustments can help minimize friction and ensure smooth material flow.
Profile Distortion
Profile distortion refers to deviations from the desired shape during the roll forming process. This can happen due to improper tooling alignment, inconsistent material thickness, or machine calibration issues. Regular inspection and calibration of the machine, along with precise tooling adjustments, can help minimize profile distortion and maintain dimensional accuracy.
Tooling Wear and Replacement
Over time, the tooling used in the Ameco roll forming machine may wear out and require replacement. Excessive tooling wear can lead to inconsistencies in profile shapes and dimensions. It is important to monitor tooling condition regularly and schedule timely replacements to maintain product quality and minimize downtime.
Machine Calibration
Accurate machine calibration is crucial for achieving precise profiles and dimensional tolerances. Improper calibration can lead to variations in product dimensions and compromised quality. Regular calibration checks and adjustments should be performed to ensure optimal performance and consistent results.
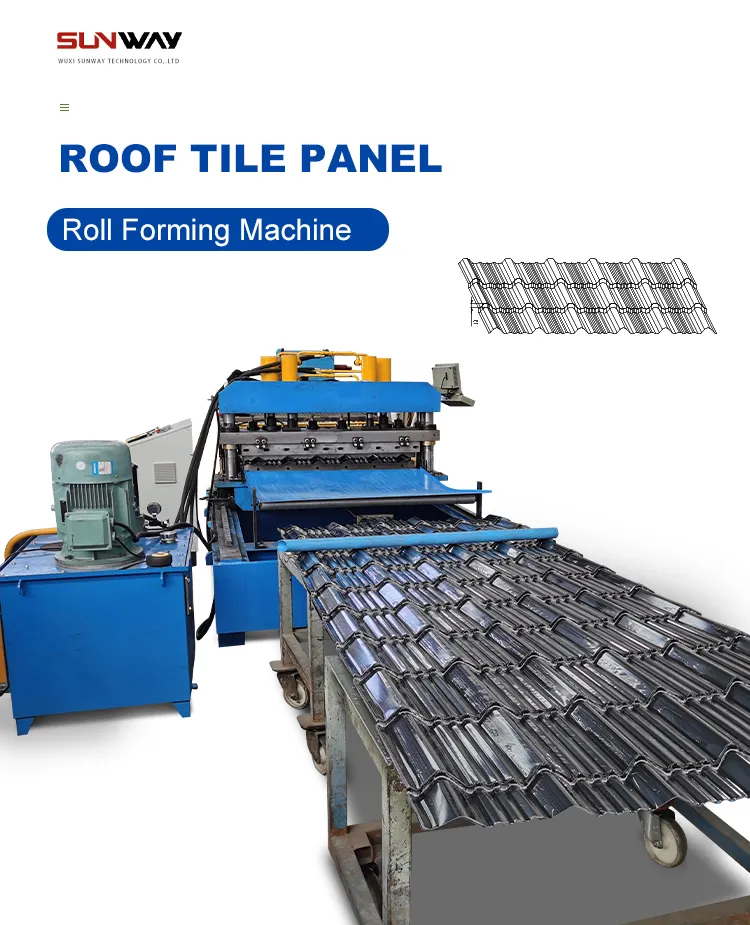
Maintenance Tips for Ameco Roll Forming Machine
To ensure the longevity and efficient operation of your Ameco roll forming machine, regular maintenance is essential. Here are some maintenance tips to keep your machine in optimal condition:
Regular Cleaning and Lubrication
Clean the machine regularly to remove debris, dust, and accumulated residue that may hinder its performance. Lubricate moving parts and rollers as per the manufacturer’s recommendations to minimize friction and ensure smooth operation.
Inspection and Adjustment
Perform routine inspections of the machine’s components, including rollers, gears, and electrical connections. Check for signs of wear, misalignment, or damage and make necessary adjustments to maintain optimal performance.
Tooling Maintenance
Inspect the condition of the tooling regularly and clean it to remove any buildup or debris. Replace worn-out or damaged tooling to ensure consistent profile shapes and dimensions. Proper storage of spare tooling is also important to prevent damage and maintain their longevity.

Conclusion
The Ameco roll forming machine is a valuable asset for manufacturers in various industries, offering increased efficiency, cost savings, and customization options. By understanding its working principles, applications, and maintenance requirements, businesses can leverage the benefits of this versatile machine to enhance their production capabilities and deliver high-quality products.
FAQs
1. How long does it take to set up an Ameco roll forming machine for a new profile? Setting up an Ameco roll forming machine for a new profile can vary depending on the complexity of the profile and the operator’s familiarity with the machine. Generally, it may take a few hours to set up the tooling, perform initial calibration, and fine-tune the machine for optimal performance.
2. Can the Ameco roll forming machine handle different types of metals? Yes, the Ameco roll forming machine can handle various types of metals, including steel, aluminum, copper, and stainless steel. However, different material properties may require specific adjustments and tooling considerations to achieve desired results.
3. Is operator training required to operate an Ameco roll forming machine? Yes, operator training is crucial for safe and efficient operation of the Ameco roll forming machine. Proper training ensures that operators understand the machine’s functions, safety protocols, and maintenance requirements, minimizing the risk of accidents and optimizing productivity.
4. Can the Ameco roll forming machine produce both simple and complex profiles? Yes, the Ameco roll forming machine is capable of producing both simple and complex profiles. Its versatility allows for customization and adaptation to a wide range of profile shapes and dimensions. The machine’s multiple roll stations and adjustable tooling options enable the production of intricate profiles with high precision.
5. What support does Ameco provide for maintenance and technical assistance? Ameco provides comprehensive support for maintenance and technical assistance. They offer training programs for operators and maintenance personnel, ensuring they have the necessary knowledge and skills to operate and maintain the machine effectively. Ameco also provides access to spare parts and offers prompt technical support to address any issues that may arise during machine operation.