Aluminum corrugated metal, often referred to as corrugated aluminum sheets or panels, is a versatile and durable material widely used in construction, architecture, and various industries. With its unique wave-like pattern, corrugated aluminum not only enhances aesthetic appeal but also provides significant structural strength. Whether you’re working on a roofing project or an industrial cladding application, this guide will walk you through everything you need to know about aluminum corrugated metal, including its types, manufacturing process, applications, and much more.
What Is Aluminum Corrugated Metal?
Aluminum corrugated metal is a type of metal sheet that features parallel ridges and grooves, giving it a wavy or “corrugated” appearance. The aluminum material makes these sheets lightweight, corrosion-resistant, and highly durable, making them perfect for outdoor and industrial use. Commonly, these sheets are used in roofing, siding, fencing, and other exterior applications because they provide excellent weather resistance and structural support.
Corrugated aluminum sheets come in a variety of sizes, thicknesses, and patterns, which makes them suitable for a wide range of projects, from small residential renovations to large-scale industrial structures.
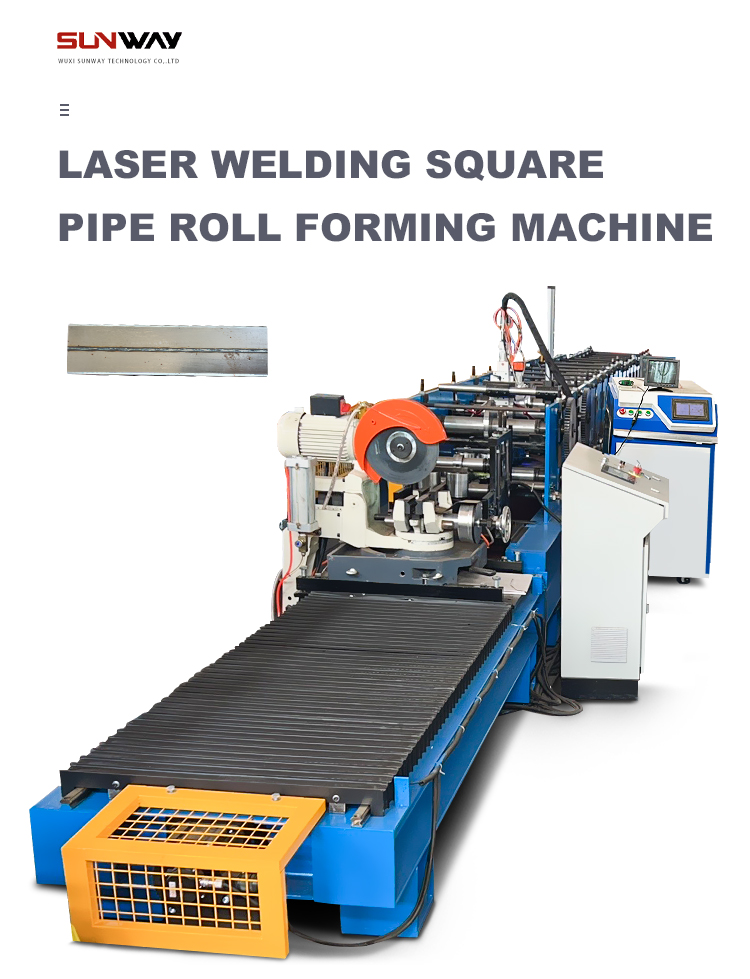
The Versatility of Corrugated Aluminum Sheets
Corrugated metal sheets have been in use for over a century, but the shift towards aluminum has gained popularity because of the numerous advantages aluminum offers compared to other metals like steel. Aluminum is lighter, more corrosion-resistant, and requires less maintenance, which is why it’s often chosen over galvanized steel or iron for exterior building applications.
These sheets are especially valuable in harsh environments. The wavy design enhances structural strength while maintaining flexibility. Additionally, aluminum sheets are often coated with additional layers to improve their durability and aesthetic properties.
A Guide to Aluminum Corrugated Metal Sheets
When choosing aluminum corrugated metal, it’s crucial to understand the different types and how each type meets specific requirements. Whether you’re looking for flexibility in design, high load-bearing capacity, or maximum corrosion resistance, there are multiple options available.
Types of Aluminum Corrugated Metal Sheets
Type | Description | Best For | Key Properties |
---|---|---|---|
Mill Finish Aluminum Corrugated Sheet | Basic aluminum sheet without any coating, featuring a natural finish. | Basic cladding, industrial use | Affordable, simple, lightweight |
Polyester Painted Aluminum Corrugated Sheet | Coated with polyester paint to enhance visual appeal and durability. | Residential roofing, siding | Resistant to UV rays, available in various colors |
PVC Coated Aluminum Corrugated Sheet | Plastic-based coating provides a smooth surface with added durability. | Exterior applications in corrosive environments | Excellent corrosion resistance, smooth surface |
Anodized Aluminum Corrugated Sheet | Anodized for enhanced strength and resistance to oxidation. | Decorative facades, architectural use | Scratch-resistant, long-lasting |
Stucco Embossed Corrugated Sheet | Textured surface resembling stucco. | Aesthetic roofing and wall cladding | Textured, hides scratches and dents well |
Perforated Aluminum Corrugated Sheet | Corrugated sheets with small perforations. | Ventilation panels, acoustic systems | Airflow, sound dampening, lightweight |
Alu-zinc Corrugated Sheet | A combination of aluminum and zinc for improved strength and durability. | Heavy-duty roofing, industrial structures | Combines both aluminum’s light weight and zinc’s strength |
Aluminum Alloy 3003 Corrugated Sheet | Contains manganese to improve corrosion resistance. | Marine environments, high-corrosion areas | Highly resistant to saltwater, durable |
5052-H32 Aluminum Corrugated Sheet | Made from an alloy with magnesium, offering higher strength. | Load-bearing applications, structural components | High strength-to-weight ratio |
Aluminum Composite Corrugated Sheet | A sandwich panel with an aluminum core for extra strength. | High-performance projects | Lightweight, highly durable, excellent thermal insulation |
Overview of Different Types of Aluminum Corrugated Metal Sheets
This table summarizes the various types of aluminum corrugated metal sheets available, providing essential details on their properties and best-use scenarios.
The Manufacturing Process of Aluminum Corrugated Metal
The process of making aluminum corrugated metal involves several stages, each designed to enhance the material’s structural integrity and visual appeal. Here’s a step-by-step breakdown of how aluminum corrugated metal is produced:
- Aluminum Ingot Casting: The process begins with the melting of aluminum ingots in a furnace, where the molten aluminum is then cast into large, flat sheets.
- Sheet Rolling: These flat sheets are rolled into thin aluminum strips of the required thickness. During this step, any necessary alloying elements like magnesium or manganese may be added to enhance the material’s properties.
- Corrugating Process: The flat aluminum sheets are then fed through corrugating rollers, which create the wavy pattern by applying pressure. This process increases the sheet’s rigidity without adding extra weight.
- Cutting and Trimming: Once corrugated, the sheets are cut to the required length and width depending on the application. Custom shapes can also be achieved using specialized cutting tools.
- Surface Treatment: After corrugation, surface treatments like painting, anodizing, or coating with protective materials (e.g., polyester or PVC) are applied. This step enhances the corrosion resistance and appearance of the metal.
- Quality Control: Finally, the sheets go through quality control to ensure uniformity and strength. They are tested for thickness, strength, and coating durability.
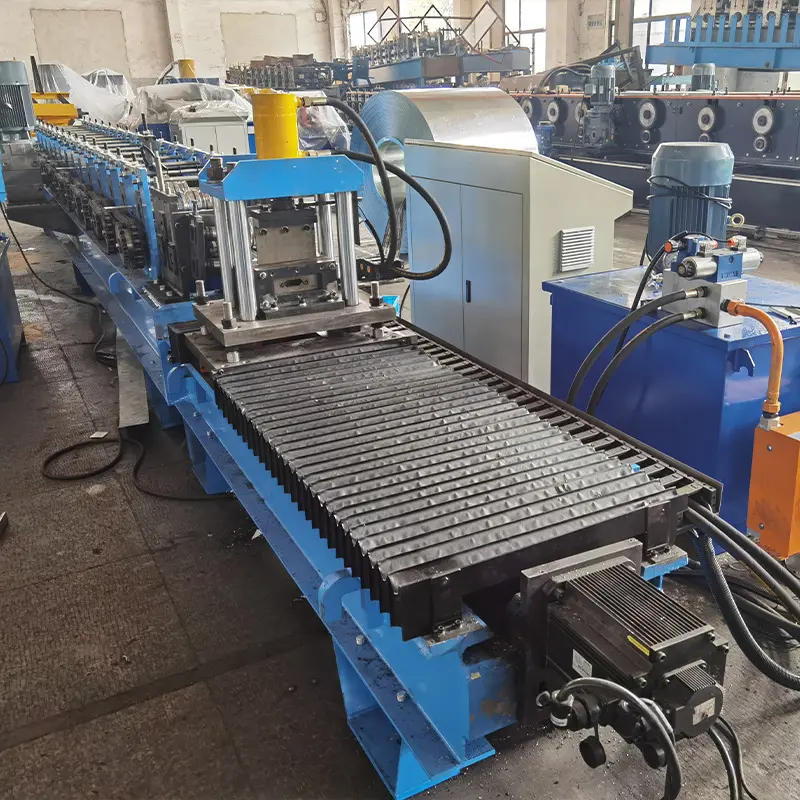
Key Components and Functions in Aluminum Corrugated Metal Production
Component | Function |
---|---|
Roller Presses | Forms the corrugated pattern by applying consistent pressure to flat aluminum sheets. |
Furnace | Melts raw aluminum ingots to create sheets or strips. |
Cutting Machines | Cuts the corrugated sheets into customized sizes. |
Surface Coating Equipment | Applies protective coatings such as paint, anodizing, or PVC. |
Quality Control Sensors | Ensure that the sheets meet required specifications in thickness, strength, and surface quality. |
Key Components in the Aluminum Corrugation Process
Understanding the equipment involved in the production process helps to ensure the quality of the final product.
Machine Efficiency and Performance in Aluminum Corrugating
Different machines are used during the production process, and their efficiency can vary based on multiple factors such as machine speed, production output, and energy consumption.
Machine Performance Metrics for Aluminum Corrugation
Machine Type | Speed (m/min) | Efficiency (%) |
---|---|---|
Standard Corrugation Machine | 15–20 m/min | 90% |
High-Speed Corrugation Machine | 30–35 m/min | 95% |
Precision Corrugation Machine | 10–15 m/min | 92% |
Machine Speed and Efficiency for Aluminum Corrugation
Choosing the right machine is crucial for optimizing production time and ensuring high-quality output.
Customization of Aluminum Corrugated Metal Sheets
Customization options play a significant role in how aluminum corrugated metal is applied across different industries. Manufacturers can produce sheets with specific dimensions, thickness, and surface finishes to meet the unique requirements of a project.
Customizable Mechanical Parameters
Parameter | Customizable Range |
---|---|
Sheet Thickness | 0.4 mm to 2.5 mm |
Sheet Width | 600 mm to 1250 mm |
Corrugation Height | 8 mm to 35 mm |
Surface Finish | Mill finish, painted, anodized, stucco embossed |
Alloy Options | 3003, 5052, 1100, 6061 |
Customizable Parameters in Aluminum Corrugated Metal
Customizing these parameters allows for flexibility in design and performance, tailoring the material to the specific needs of a project.
Applications of Aluminum Corrugated Metal Sheets
Aluminum corrugated sheets are used in a variety of sectors, each requiring different properties like corrosion resistance, durability, or aesthetic appeal. Here are some of the common applications:
Application Area | Description |
---|---|
Roofing | Lightweight and durable, aluminum corrugated sheets are perfect for roofing in residential and industrial buildings. |
Siding and Cladding | Provides an attractive, low-maintenance finish to building exteriors. |
Industrial Panels | Used in factories and warehouses for walling and partitions. |
Fencing | Aluminum sheets make excellent barriers due to their weather-resistant properties. |
Shipping Containers | Provides protection against harsh marine environments. |
Decorative Architectural Elements | Used in modern architecture for facades and aesthetic panels. |
Common Applications of Aluminum Corrugated Metal Sheets
Each of these applications benefits from the unique properties of aluminum, such as its resistance to corrosion and its light weight.
Installation, Operation, and Maintenance of Aluminum Corrugated Sheets
Installing aluminum corrugated metal sheets requires precision to ensure proper alignment and maximum durability. Once installed, maintenance is minimal due to the metal’s natural resistance to corrosion and wear.
Installation and Maintenance Guidelines
Step | Guidelines |
---|---|
Installation | Ensure sheets are aligned with overlaps to prevent water leakage. Use aluminum or stainless-steel fasteners to avoid galvanic corrosion. |
Operation | The sheets require no special operation once installed, but regular inspections for fastener integrity and surface damage are advised. |
Maintenance | Aluminum sheets need minimal maintenance; periodic washing with water can help retain their appearance. Any minor scratches can be buffed out or painted over. |
Price Range and Suppliers of Aluminum Corrugated Metal
When it comes to sourcing aluminum corrugated sheets, prices will vary based on the type of material, thickness, and surface finish.
Supplier and Price Range Information
Supplier | Price Range (per sq meter) | Shipping Options |
---|---|---|
Metal Depot | $15 – $25 | Global shipping available |
Aluminum Sheet Co. | $12 – $22 | Free shipping in North America |
Industrial Metal Supply | $18 – $28 | Bulk order discounts |
McElroy Metal | $20 – $30 | Custom fabrication services available |
Corrugated Metals, Inc. | $17 – $26 | Expedited shipping available |
How to Choose the Right Supplier for Aluminum Corrugated Metal
Choosing the right supplier is critical to ensuring you get high-quality aluminum corrugated metal for your project. Here are some things to consider:
Factors to Consider When Choosing a Supplier
Factor | What to Look For |
---|---|
Reputation | Look for suppliers with positive customer reviews and long-standing credibility in the industry. |
Quality | Ensure the supplier offers high-quality, tested materials with appropriate certifications. |
Customization Options | Make sure the supplier can meet any specific design or technical requirements. |
Delivery Time | Check that the supplier can meet your project deadlines without delay. |
Price Transparency | Compare prices from multiple suppliers to ensure you’re getting value for money. |
Advantages and Disadvantages of Aluminum Corrugated Metal
While aluminum corrugated metal is highly popular, like any material, it has its pros and cons.
Advantages
- Lightweight: Compared to steel, aluminum is significantly lighter, making it easier to transport and install.
- Corrosion Resistance: One of aluminum’s key strengths is its ability to resist rust and corrosion, especially in humid or salty environments.
- Durability: Despite being lightweight, aluminum corrugated metal is strong and can withstand harsh weather conditions.
- Recyclability: Aluminum is a sustainable choice because it’s fully recyclable without loss of quality.
- Aesthetic Appeal: The wide variety of finishes and coatings makes aluminum corrugated sheets aesthetically versatile.
Disadvantages
- Higher Cost: Aluminum tends to be more expensive than other metals like steel.
- Lower Strength: While durable, aluminum is not as strong as some other metals, such as galvanized steel, which may limit its use in heavy-duty applications.
- Thermal Conductivity: Aluminum conducts heat more readily than steel, which can be a drawback in applications requiring thermal insulation.
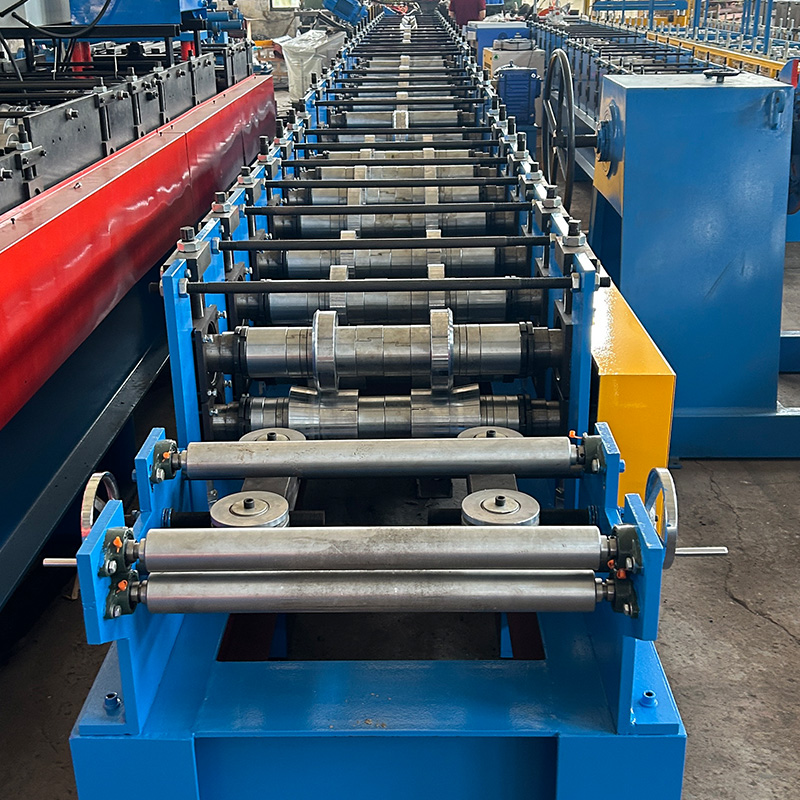
FAQ
Question | Answer |
---|---|
Can aluminum corrugated sheets be painted? | Yes, aluminum sheets can be coated with polyester or other paints for added protection and color. |
How long do aluminum corrugated sheets last? | With proper installation and minimal maintenance, these sheets can last for over 50 years. |
Are aluminum corrugated sheets recyclable? | Yes, they are 100% recyclable and are often used in sustainable building projects. |
What is the standard thickness for aluminum corrugated metal? | The thickness typically ranges from 0.4 mm to 2.5 mm, depending on the application. |
Do aluminum corrugated sheets provide good insulation? | While aluminum is a good conductor of heat, it can be paired with insulation materials to improve its thermal properties. |
What is the maximum length for aluminum corrugated sheets? | Sheets can be produced in custom lengths, with some manufacturers offering lengths up to 12 meters. |
In conclusion, aluminum corrugated metal is an excellent choice for many applications due to its lightweight nature, corrosion resistance, and durability. Whether you’re looking to upgrade your home’s roofing or working on a large industrial project, these sheets offer a versatile solution with various customization options. By understanding the types, uses, and factors for choosing the right supplier, you can confidently select the best aluminum corrugated metal for your needs.