A roller shutter roll forming machine, also known as a roll former, is a metalworking machine used to convert coils of sheet metal into custom profiles. Roll forming is a continuous bending operation in which sheet or strip metal is gradually formed into the desired cross-sectional configuration through a series of consecutive forming stations. Roller shutter roll forming machines offer several advantages that make them an invaluable asset for manufacturers.
High production speed and efficiency
One of the biggest advantages of roller shutter roll forming machines is their exceptionally high production speed and efficiency. The roll forming process allows for a continuous and rapid rate of production that simply cannot be matched by other smaller scale forming methods. A roller shutter roll former is able to produce linear metal profiles at feed rates from 1 to 200 meters per minute depending on the complexity of the profile design and thickness of the metal coil. This represents a massive time savings over manual fabrication methods. The automated nature of roll forming results in labor cost savings as well. Only one or two operators are needed to monitor the equipment and feed in new coils, eliminating the need for teams of workers.
Flexibility and customization ability
Another major advantage of roller shutter roll forming machines is their inherent flexibility and customization capabilities. With the proper roll tooling, a roller shutter roll former can produce virtually any type of profile from simple to highly complex geometries. Roll formers can process sheet metal and coils ranging from 0.15 mm thick up to 3 mm thick steel and even thicker aluminum. The formed parts can have straight, curved, or tapered sections. This makes roll forming ideal for producing profiles for roller shutters, roofing and siding, racking, solar panel frames, metal furniture, shelving, automation equipment, and countless other applications. Manufacturers can easily customize roll forming lines to meet their specific product requirements.
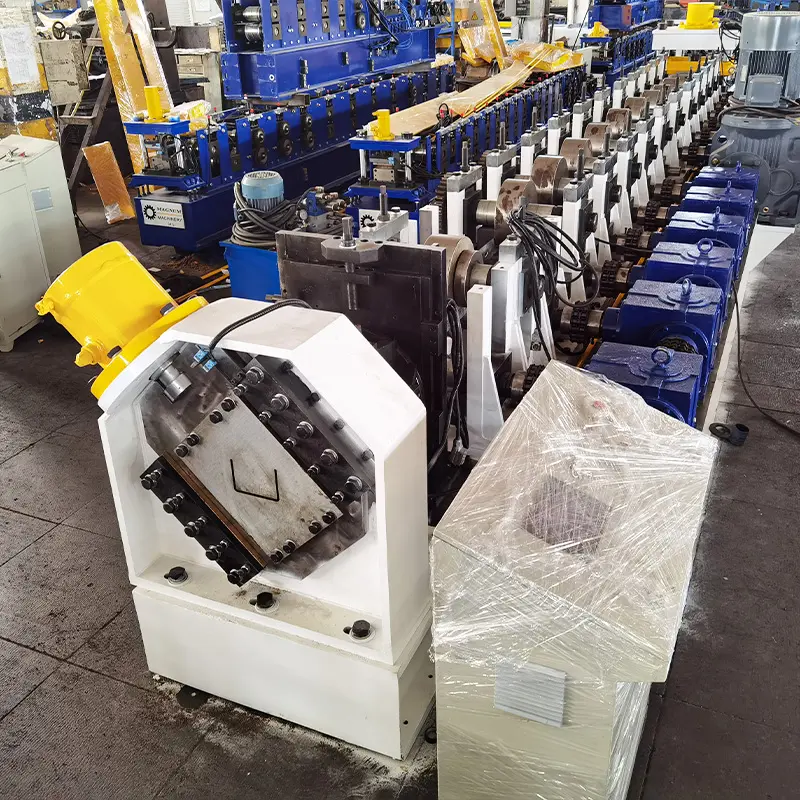
High precision and repeatability
The roller shutter roll forming process delivers an extremely high degree of precision and repeatability compared to other metal forming techniques. The multiple bending steps through incremental roll stations enable tight tolerances down to +/- 0.1 mm. Once the roll tooling is set up properly, the machines produce consistent output roll after roll. This ability to hold tight tolerances results in high quality finished products. The roll formed parts have excellent flatness free of undesirable ripples, waves, bowing, and other defects prevalent with other forming methods. The reliability and precision of roller shutter roll formers make them well-suited for volume production.
Material savings OF roller shutter roll forming machine
Roller shutter roll forming machines provide great material savings compared to other metal fabrication processes. The rolls incrementally form the sheet metal into the desired shape without the need to cut away excess material. Roll forming has minimal material waste, with efficiencies over 90 percent in many cases. This is a huge advantage considering the high cost of sheet metal stock. Manufacturers can stretch their material budget further and avoid unnecessary scrap using roller shutter roll forming technology.
Versatility of Inline Operations
A major advantage of roller shutter roll forming lines is the ability to integrate inline secondary processing operations for improved efficiency. Common inline operations include:
- Cutoff die punching
- End cropping
- Holes punching
- Notching
- Embossing
- Decoiling and recoiling
- Welding
- Marking
- Straightening
Performing multiple operations in a single automated production line eliminates handling of parts between steps. This streamlines production, reduces labor, and improves overall quality control. Inline processing with a roller shutter roll former allows manufacturers to create finished or semi-finished products in one continuous operation.
Durability and Reliability
Roller shutter roll forming machines are known for their exceptional durability and reliability even under demanding industrial production settings. Well-built roll forming lines are constructed from heavy gauge steel frames, quality bearings and hydraulic components, and hardened roll tooling. Operated properly, it is not uncommon for these machines to deliver over 20 years of productive service. Downtime is minimal compared to other metalworking equipment. The simplicity of the technology with its rotating rollers makes maintenance straightforward. Roll formers withstand high production volumes and 24/7 operation in the harshest manufacturing environments. This durability and reliability results in high machine availability and productivity.
Energy Efficiency
From an operational standpoint, roller shutter roll forming equipment is extremely energy efficient. The lines consume relatively little electrical power despite their high throughput capacity. Most of the energy goes directly into the useful forming work rather than being wasted. The process does not require heating, cooling, or drying of materials which reduces consumption. Without heavy presses or stamping actions, power demand stays relatively constant even under full load. This equates to substantial cost savings, smaller electricity bills, and a reduced environmental impact for manufacturers compared to other processes.
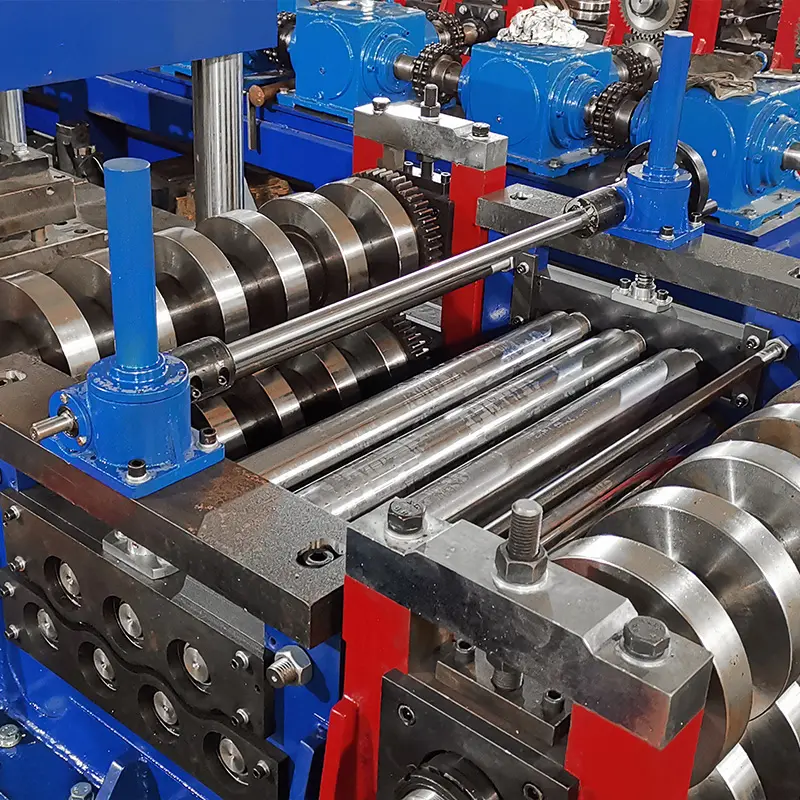
Lower Capital Investment
Perhaps the most important advantage of roller shutter roll formers is that they represent a much lower capital investment than other mass production metalworking machines. Roll forming lines have a favorable cost in relation to their output capacity. The simplicity of the technology brings down costs. A basic roller shutter roll former capable of producing small profiles may cost as little as $50,000. Higher capacity, complex lines range from $500,000 to $2 million. This reasonable pricing makes roller shutter roll formers very accessible to small and mid-sized manufacturers. The equipment pays for itself quickly and allows producers to reap the benefits of series production without a massive upfront expenditure or debt burden.
FAQ
What types of profiles can be produced on a roller shutter roll former?
Roll formers can produce nearly any type of open and closed profile from basic shapes such as tubes, rails, bars, and studs to complex geometries like roofing panels, racking, highway guardrails, drainage channels, door frames, roller shutter slats, and more. The key is having the proper roll tooling matched to the desired profile.
What thickness of material can be roll formed?
Roll forming machines can process sheet metal and coiled stock ranging from very thin foil of 0.15 mm up to approximately 3 mm thickness steel and 6 mm aluminum depending on the machine’s capacity. Thicker materials require more robust machine frames and larger roll tooling.
Can a roll former make curved profiles?
Yes, with the right roll tool design and equipment adaptations, curved profiles with radii down to approximately 150 mm can be roll formed. This does have more complexity than straight profiles.
How long does it take to set up a roll former for a new profile?
The time required to changeover a roller shutter roll forming machine depends on the complexity of the new profile design and how much the tooling must be altered. Simple profile changeovers can be done in 30 minutes to 2 hours. More significant roll changes may take 8 hours or more.
What determines the production speed of a roll former?
The maximum production speed depends on the profile shape, metal thickness, number of processing stations, tooling design, and main drive power. Simple small profiles in light gauge metal can run at up to 200 meters per minute. Heavier profiles typically operate in the 15 to 60 meter per minute range.
How much material waste is created in roll forming?
Roll forming is very material efficient with less than 10 percent scrap in most cases. The rollers progressively form the profile to shape without cutting away excess material. Any scrap is just the material remaining at the ends after cutoff.
What are typical maintenance needs for roller shutter roll formers?
General maintenance involves cleaning, inspecting, and lubricating components. Guidance systems, bearings, chains, and gears will need periodic replacement after extensive runtimes. Rollers may need refinishing after prolonged use. With proper care, many roll formers operate reliably for over 20 years.
Are there safety concerns with roll forming equipment?
Roll formers have safety guards to protect workers from the moving components. Operators should receive thorough training and wear protective equipment. With correct operation and maintenance, roll forming lines have excellent safety records.
This covers the major advantages and common FAQs regarding roller shutter roll forming machines. In summary, the flexibility, speed, precision, durability, and cost-effectiveness of roll formers make them a worthwhile investment for any manufacturer working with sheet metal.