Introduction
In the world of modern manufacturing, precision and efficiency are paramount. Industries relying on sheet metal production seek reliable methods to meet their demands for high-quality products with consistent shapes and dimensions. This is where the trapezoidal roll forming machine steps in as a game-changer. In this article, we explore the functionalities, advantages, and applications of this versatile machine.
What is a Trapezoidal Roll Forming Machine?
A trapezoidal roll forming machine is an automated production line designed to shape sheet metal into trapezoidal profiles. This machine takes flat metal coils and gradually bends them into the desired trapezoidal shape through a series of rolling stands. The process ensures precise forming and consistency throughout the length of the material.
How Does a Trapezoidal Roll Forming Machine Work?
The roll forming process starts with an uncoiler, where the metal coil is loaded onto the machine. The material is then fed through a series of rollers, each responsible for specific bending and forming operations. These rollers are strategically positioned to gradually shape the metal into the desired trapezoidal profile. The final product is then cut to the required length before being collected.
Advantages of Using a Trapezoidal Roll Forming Machine
Trapezoidal roll forming machines offer several advantages over traditional bending and shaping methods:
- High Efficiency: The continuous and automated process ensures a high production rate, reducing manufacturing time significantly.
- Consistent Quality: The machine’s precision and repeatability guarantee uniform products without variations in shape or dimensions.
- Material Savings: Minimal scrap generation due to accurate forming reduces material wastage and saves costs.
- Flexibility and Customization: These machines can be tailored to produce various trapezoidal profiles, meeting diverse customer needs.
- Labor Reduction: Automated operation reduces the need for extensive manual labor, saving on workforce expenses.
- Integration with Other Processes: Roll-formed trapezoidal profiles seamlessly fit into downstream assembly and construction processes.
- Reduced Lead Times: Quick production turnaround enables faster project completion and delivery.
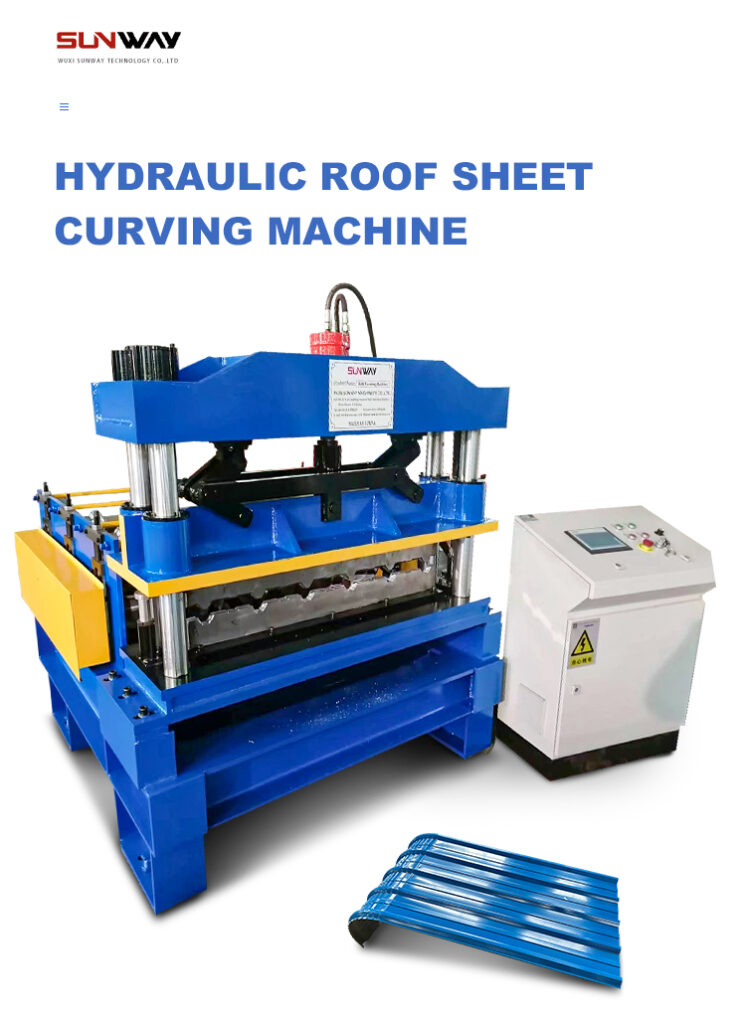
Types of Trapezoidal Roll Forming Machines
Trapezoidal roll forming machines come in various configurations to cater to different production requirements:
Single Station Roll Forming Machine
The single station machine performs all forming steps in one place, ideal for low to medium production volumes.
Duplex Roll Forming Machine
The duplex machine has two independent roll forming stations, allowing simultaneous production of two different profiles.
Triplex Roll Forming Machine
This type has three forming stations and offers even greater flexibility and higher production capacity.
Automated Roll Forming Lines
Automated lines combine multiple roll forming machines with additional processes like punching and notching, streamlining the entire production workflow.
Key Components of a Trapezoidal Roll Forming Machine
To understand the intricacies of the machine’s operation, it’s essential to know its key components:
Uncoiler
The uncoiler holds the metal coil and feeds it into the roll forming machine gradually.
Feeding System
The feeding system guides the material through the machine and ensures smooth, even feeding.
Roll Forming Unit
The heart of the machine, the roll forming unit, consists of multiple rollers that shape the material step by step.
Cutting System
The cutting system, typically using flying shears, trims the formed profile to the desired length.
Control Panel and Software
The control panel allows operators to set various parameters, while the software governs the machine’s operation.
Factors to Consider When Choosing a Trapezoidal Roll Forming Machine
Selecting the right roll forming machine for your specific needs requires careful consideration of the following factors:
Material Compatibility
Ensure the machine is compatible with the types and thicknesses of metal you intend to use.
Production Speed
Consider the required production rate and choose a machine that meets your volume demands.
Customization Options
Check if the machine can be adjusted to produce various trapezoidal profiles to cater to different customer requirements.
Machine Size and Space Requirements
Determine the available space in your facility and select a machine that fits appropriately.
Budget and Cost Considerations
Balance your budget constraints with the desired features and capabilities of the machine.
Maintenance and Care for a Trapezoidal Roll Forming Machine
To ensure the longevity and optimal performance of the machine, regular maintenance is essential. Some maintenance tips include:
Regular Inspection and Cleaning
Frequent inspections and cleaning help identify and address potential issues before they escalate.
Lubrication of Moving Parts
Proper lubrication of the machine’s moving parts, such as rollers and bearings, ensures smooth operation and reduces wear and tear.
Replacing Worn-Out Components
Regularly check for worn-out or damaged components and replace them promptly to prevent further damage and maintain efficiency.

Safety Precautions While Operating a Trapezoidal Roll Forming Machine
Safety should always be a top priority when operating any industrial machinery. Here are some essential safety precautions for using a trapezoidal roll forming machine:
Operator Training and Certification
Only trained and certified operators should be allowed to run the machine to avoid accidents and ensure proper handling.
Proper Use of Personal Protective Equipment (PPE)
Operators should wear appropriate PPE, including safety glasses, gloves, and ear protection, to protect themselves from potential hazards.
Emergency Stop Procedures
The machine should be equipped with easily accessible emergency stop buttons to halt operations in case of an emergency.
Lockout/Tagout Procedures
Establish lockout/tagout procedures to ensure the machine is safely shut down during maintenance or repair work.
Common Quality Issues and Troubleshooting in Roll Forming
Despite its efficiency, roll forming may encounter some quality issues. Understanding common problems and their solutions is crucial:
Uneven Material Feeding
Inconsistent material feeding can lead to irregular profiles. Check the feeding system for misalignments and adjust accordingly.
Forming Defects
Address issues like improper roll settings or worn-out rollers to eliminate forming defects.
Cutting Irregularities
If the cutting system produces uneven cuts, examine the blades and replace them if necessary.
Electrical and Software Issues
Regularly inspect the control panel and software for any malfunctions, and consult a technician for timely repairs.
Applications of Trapezoidal Roll Forming Machines
The versatility of trapezoidal roll forming machines allows for a wide range of applications in various industries:
Roofing and Cladding Sheets
Trapezoidal profiles are commonly used in roofing and cladding systems for their durability and weather resistance.
Wall Panels
The machine can produce aesthetically pleasing wall panels used in architectural and construction applications.
Purlins and Girts
In the construction of steel structures, trapezoidal profiles serve as essential components like purlins and girts.
Shelving and Racking Systems
The precise forming capability of the machine makes it ideal for manufacturing shelving and racking systems used in warehouses and storage facilities.
Automotive and Aerospace Components
Trapezoidal roll forming machines play a vital role in producing components for automotive and aerospace industries, where precision and consistency are critical.
Future Trends in Trapezoidal Roll Forming Technology
As technology advances, so does the roll forming industry. Some future trends to look out for include:
- Advanced Materials: Roll forming machines will adapt to process new materials, such as lightweight alloys and advanced composites.
- Smart Automation: Integration of artificial intelligence and machine learning will enhance machine efficiency and productivity.
- Energy Efficiency: Roll forming machines will incorporate energy-saving features to reduce their environmental impact.
- Increased Customization: Machines will offer more flexible customization options to cater to diverse customer demands.
Environmental Impact and Sustainability Considerations
Manufacturers are increasingly focusing on sustainability and reducing their environmental footprint. Trapezoidal roll forming machines contribute to sustainability in several ways:
- Material Efficiency: The minimal waste generated during roll forming reduces the overall material consumption.
- Energy Efficiency: Automation and advanced technology lead to more energy-efficient operations.
- Recyclability: Many materials used in roll forming, such as steel, are highly recyclable, promoting a circular economy.
- Reduced Emissions: By optimizing production processes, roll forming machines can help reduce greenhouse gas emissions.
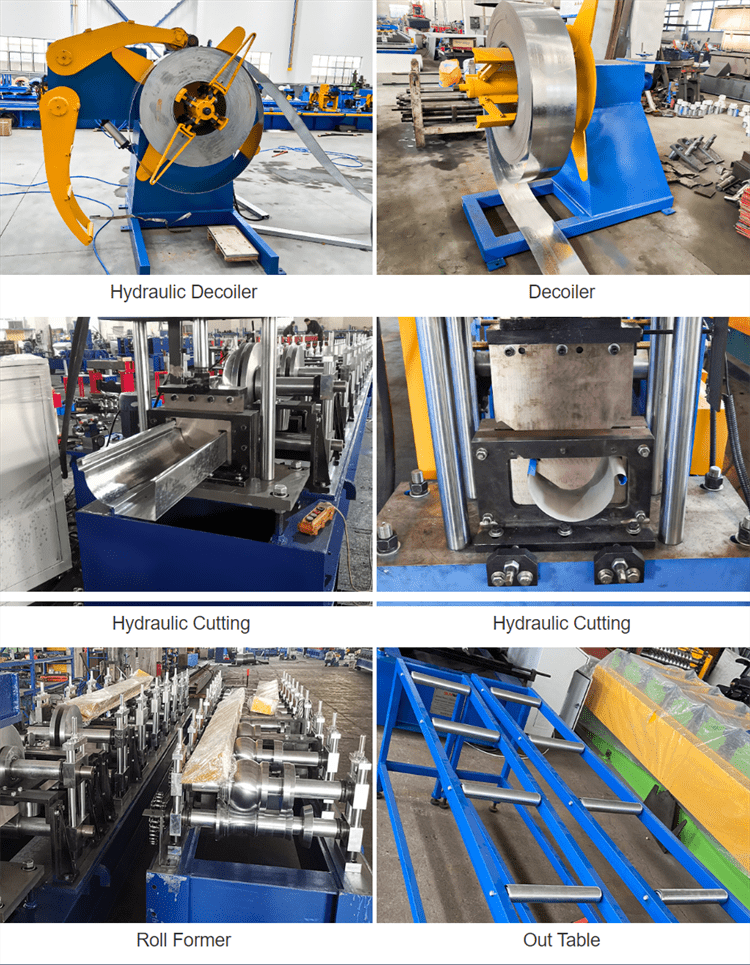
Conclusion
The trapezoidal roll forming machine is a remarkable innovation that has revolutionized the sheet metal production industry. Its efficiency, consistency, and versatility make it a valuable asset for various applications. As technology continues to advance, we can expect even more developments in roll forming machinery, further driving efficiency and sustainability in the manufacturing sector.
FAQs
Q1: Can a trapezoidal roll forming machine produce other shapes besides trapezoids?
A1: Yes, depending on the machine’s design and adjustments, it can produce various other profiles, such as corrugated sheets or custom shapes.
Q2: Is it necessary to have specialized training to operate a trapezoidal roll forming machine?
A2: Yes, operating the machine requires specialized training to ensure safe and proper handling. Certified operators are essential for efficient and accident-free production.
Q3: What are the typical materials used in trapezoidal roll forming?
A3: Common materials include steel, aluminum, and other metals with good formability. The choice depends on the specific application and desired properties.
Q4: Can a trapezoidal roll forming machine handle thick materials?
A4: Yes, some machines can handle thick materials, but it depends on the machine’s capacity and design. It’s crucial to choose a machine that suits the material thickness you intend to work with.
Q5: Are trapezoidal roll forming machines suitable for small-scale production?
A5: Yes, trapezoidal roll forming machines come in various sizes, including models suitable for small-scale or custom production requirements.