Overview of Cold Roll Forming Machines
A cold roll forming machine is an advanced metalworking machine that shapes sheet metal into specific profiles without the need for heat. By using a series of precisely positioned rollers, the machine gradually forms the material into the desired shape. This process ensures high accuracy, efficiency, and cost savings compared to traditional metal bending techniques.
Cold roll forming is widely used in construction, automotive, racking & shelving, and renewable energy industries due to its ability to produce high-quality, complex profiles at high speeds.
In this guide, we’ll explore:
✅ How cold roll forming works
✅ Advantages of cold roll forming
✅ Best materials for cold roll forming
✅ Applications in different industries
✅ How to choose the right cold roll forming machine
Let’s get started!
How Does a Cold Roll Forming Machine Work?
Unlike hot rolling, where metal is shaped at high temperatures, cold roll forming shapes metal at room temperature. This process enhances the material’s strength and surface finish while maintaining precision.
Step-by-Step Breakdown of the Cold Roll Forming Process
Step | Description |
---|---|
1. Coil Feeding | A metal coil is loaded onto the decoiler, feeding the material into the machine. |
2. Leveling & Straightening | The coil passes through a leveling unit to remove any irregularities. |
3. Roll Forming Stages | Multiple rollers gradually shape the material into the desired profile. |
4. Cutting & Punching | A hydraulic or servo-driven cutting system trims the profile to the required length. |
5. Product Collection | The finished product exits the machine and is stacked or packaged for transport. |
👉 Did you know? Cold roll forming machines can operate at speeds of 10-100 meters per minute, making them highly efficient for mass production!
Advantages of Cold Roll Forming Machines
Cold roll forming offers numerous benefits, making it a preferred metal shaping method across industries.
Key Benefits of Cold Roll Forming
Advantage | Explanation |
---|---|
Higher Strength | Cold working increases material tensile strength. |
Precision & Consistency | Ensures uniform dimensions in every product. |
Cost-Effective | Reduces material waste and lowers production costs. |
Minimal Material Stress | Gradual shaping prevents cracks and defects. |
Energy Efficient | No heating required, reducing energy consumption. |
Automation Friendly | Can be integrated with CNC and AI monitoring for improved precision. |
Compared to hot rolling, cold roll forming provides up to 30% higher material efficiency and cost savings!
Best Materials for Cold Roll Forming
The success of cold roll forming depends on choosing the right material. Each material has unique properties that affect the forming process.
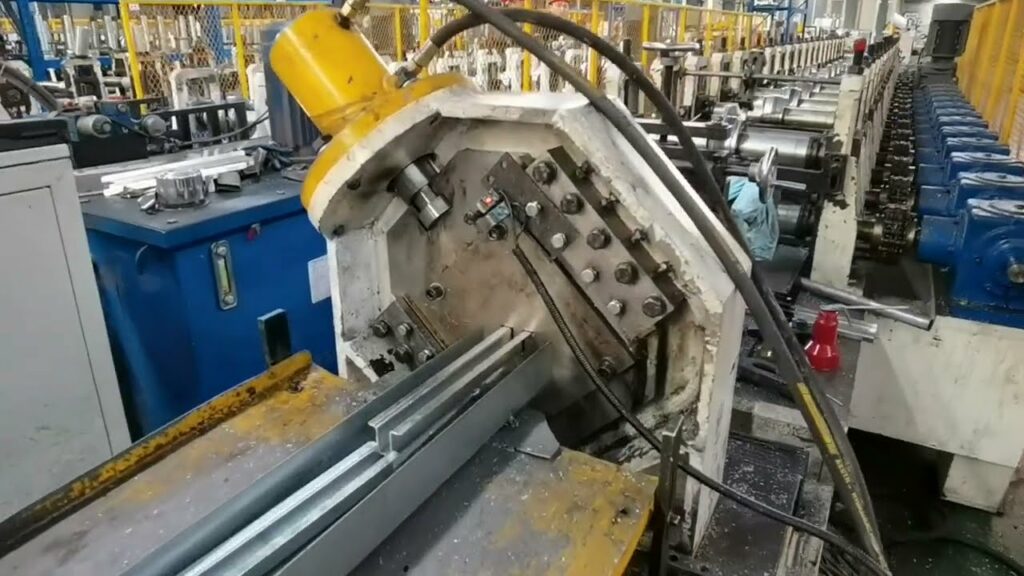
Most Common Materials Used in Cold Roll Forming
Material | Properties | Common Applications |
---|---|---|
Galvanized Steel | Corrosion-resistant, strong | Roofing, wall panels, HVAC ducts |
Stainless Steel | Rust-resistant, durable | Automotive, medical equipment |
Aluminum | Lightweight, corrosion-resistant | Solar mounting brackets, window frames |
Copper | Excellent conductivity, aesthetic appeal | Electrical components, decorative trims |
Cold Rolled Steel (CRS) | Smooth finish, high strength | Industrial shelving, construction beams |
Sunway Machine provides custom cold roll forming solutions for specialized materials like solar mounting brackets, ensuring high strength and precision.
Industries Using Cold Roll Forming Technology
Cold roll forming is used across various industries, from construction to renewable energy, due to its ability to produce complex profiles efficiently.
Key Industries Benefiting from Cold Roll Forming Machines
Industry | Application | Example Products |
---|---|---|
Construction | Roofing, wall panels | Metal cladding, C & Z purlins |
Automotive | Structural components | Chassis parts, door beams |
Racking & Shelving | Storage solutions | Warehouse racks, supermarket shelves |
Renewable Energy | Solar panel mounting systems | PV mounting brackets |
HVAC | Air duct systems | Ventilation ducts, support channels |
Sunway Machine specializes in cold roll forming machines for racking & shelving, solar energy, and steel structures, ensuring high precision and durability.
Choosing the Right Cold Roll Forming Machine
Investing in a cold roll forming machine requires careful consideration of production needs, material compatibility, and automation level.
Key Factors to Consider When Buying a Cold Roll Forming Machine
Factor | Importance |
---|---|
Production Volume | Choose a machine that meets your output needs. |
Material Type | Ensure the machine can handle the required metal thickness. |
Profile Complexity | Simple vs. multi-profile machines. |
Automation Level | CNC and AI integration for high efficiency. |
Budget & ROI | Consider long-term savings from reduced waste and labor costs. |
Manufacturer Reputation | Work with a trusted brand like Sunway Machine. |
Tip: Investing in a high-quality machine now will save you money on maintenance and downtime in the future.
Cold Roll Forming Machine Maintenance & Troubleshooting
Regular maintenance is essential to ensure optimal performance and extend the lifespan of your cold roll forming machine.
Essential Maintenance Tips
Maintenance Task | Frequency | Purpose |
---|---|---|
Lubrication of rollers | Weekly | Prevents wear and tear |
Checking alignment | Monthly | Ensures profile accuracy |
Inspecting electrical components | Quarterly | Prevents breakdowns |
Cleaning machine parts | Daily | Removes dust and debris |
Replacing worn-out rollers | As needed | Maintains profile precision |
Common Problems & Solutions
Issue | Cause | Solution |
---|---|---|
Profile distortion | Misaligned rollers | Adjust roller settings |
Inconsistent cuts | Dull cutting blades | Replace or sharpen blades |
Material slippage | Poor grip on material | Increase roller pressure |
Machine vibration | Loose components | Tighten bolts and check stability |
Regular maintenance prevents costly breakdowns and improves machine efficiency!
Cold Roll Forming vs. Other Metal Forming Methods
When choosing a metal forming method, manufacturers often compare cold roll forming with press braking, stamping, and extrusion. Each method has its own strengths, making them suitable for different applications.
Comparison Between Cold Roll Forming and Other Metal Forming Methods
Feature | Cold Roll Forming | Press Braking | Stamping | Extrusion |
---|---|---|---|---|
Process Type | Continuous rolling of metal | Bending metal sheets using a press | Punching and shaping metal | Pushing material through a die |
Production Speed | High-speed, continuous operation | Slower, batch-based process | High-speed but produces more waste | Medium-speed |
Material Waste | Minimal waste | Higher material waste | Significant waste | Minimal |
Best For | Long, continuous profiles | Short, angular bends | Complex, small parts | Hollow sections and tubes |
Energy Consumption | Low (no heating required) | High (requires large presses) | Medium (press power needed) | High (requires heat or force) |
Cost Efficiency | Most cost-effective for high-volume production | Suitable for low-volume, custom parts | Good for mass production but with high tooling costs | Expensive due to material loss and energy use |
Verdict: Cold roll forming is the best choice for continuous, high-volume production with minimal material waste, making it ideal for roofing sheets, steel framing, and industrial shelving.
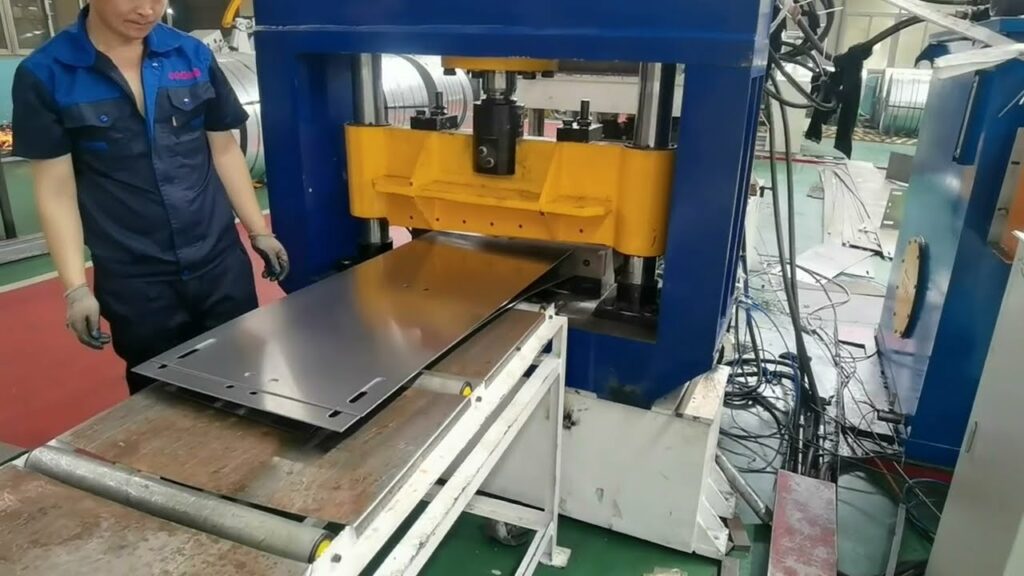
Automation in Cold Roll Forming Machines
Automation is transforming the roll forming industry, making cold roll forming faster, more precise, and cost-effective.
Key Benefits of Automated Cold Roll Forming
Feature | Benefit |
---|---|
CNC Control Systems | Ensures precise measurements and reduces human error |
AI-Based Quality Inspection | Detects defects in real-time, minimizing waste |
IoT & Remote Monitoring | Allows operators to monitor machine performance from anywhere |
Automated Changeover | Reduces downtime when switching between profiles |
Energy Efficiency | Optimized power consumption lowers operational costs |
Automation reduces production costs by up to 30% while improving product consistency!
Sunway Machine offers fully automated cold roll forming machines, designed for smart manufacturing and Industry 4.0 compliance.
Buying a Cold Roll Forming Machine: Key Considerations
Purchasing a cold roll forming machine is a major investment, and several factors must be considered to ensure reliability and efficiency.
Checklist for Buying a Cold Roll Forming Machine
Factor | Importance |
---|---|
Production Volume | Choose a machine that meets your output needs |
Material Type | Ensure the machine can handle the required metal thickness |
Profile Complexity | Simple vs. multi-profile machines |
Automation Level | CNC and AI integration for high efficiency |
Budget & ROI | Consider long-term savings from reduced waste and labor costs |
Manufacturer Reputation | Work with a trusted brand like Sunway Machine |
Tip: Investing in a high-quality machine now will save you money on maintenance and downtime in the future.
Cold Roll Forming Machine Cost Analysis
The price of a cold roll forming machine varies based on machine specifications, automation level, and customization.
Cost Breakdown
Cost Factor | Estimated Impact |
---|---|
Machine Size & Complexity | Larger machines with more rollers cost more |
Automation Level | CNC-controlled machines are more expensive but save labor costs |
Customization | Custom tooling and dies increase upfront costs |
Brand & Manufacturer | Premium brands charge higher but offer better durability |
Shipping & Installation | Import duties and setup costs add to the total price |
New vs. Used Cold Roll Forming Machines
Machine Type | Price Range | Pros | Cons |
---|---|---|---|
New Cold Roll Forming Machine | 50,000−50,000 – 50,000−500,000 | Latest technology, warranty, high efficiency | Higher initial investment |
Used Cold Roll Forming Machine | 20,000−20,000 – 20,000−200,000 | Lower cost, immediate availability | May require repairs, shorter lifespan |
Pro Tip: If you’re considering a used machine, ensure it has a complete maintenance history and spare parts availability to avoid hidden costs.
Common Cold Roll Forming Machine Issues & Troubleshooting
Even high-quality machines can experience operational issues. Here are some common problems and their solutions.
Troubleshooting Guide
Issue | Cause | Solution |
---|---|---|
Profile distortion | Misaligned rollers | Adjust roller settings |
Inconsistent cuts | Dull cutting blades | Replace or sharpen blades |
Material slippage | Poor grip on material | Increase roller pressure |
Machine vibration | Loose components | Tighten bolts and check stability |
Uneven coating on galvanized steel | Incorrect roller pressure | Adjust roller pressure and speed |
Regular maintenance prevents costly breakdowns and improves machine efficiency!
FAQ: Cold Roll Forming Machines
1. What is a cold roll forming machine used for?
Cold roll forming machines continuously shape metal into specific profiles, commonly used in construction, automotive, and industrial applications.
2. What are the advantages of cold roll forming over press braking?
✅ Higher speed production
✅ Less material waste
✅ Better consistency in product dimensions
✅ More cost-effective for large-scale production
3. Can cold roll forming machines handle different materials?
Yes! Cold roll forming machines can work with steel, aluminum, copper, and coated metals, depending on the application.
4. How long does a cold roll forming machine last?
With proper maintenance, a high-quality cold roll forming machine can last 10-20 years or more.
5. Where can I buy a high-quality cold roll forming machine?
For top-tier cold roll forming machines, visit WUXI SUNWAY MACHINERY CO., LTD.
Final Thoughts
The cold roll forming process is essential for high-speed, cost-effective, and precise metal fabrication. Whether you’re in construction, automotive, or renewable energy, cold roll forming ensures high-quality results with minimal waste.
WUXI SUNWAY MACHINERY CO., LTD is a leading manufacturer of cold roll forming machines, offering customized solutions, expert support, and competitive pricing.
Want to optimize your production? Contact us today!