Overview of the Roll Forming Process
The roll forming process is a continuous metal shaping technique that transforms sheet metal into customized profiles using a series of precisely positioned rollers. This process is widely used in automotive, construction, racking & shelving, and renewable energy industries due to its ability to create high-quality, consistent, and cost-effective metal profiles.
Unlike press braking or stamping, roll forming allows for high-speed production with minimal material waste, making it ideal for large-scale manufacturing. In this guide, we will explore:
✅ How roll forming works
✅ Types of roll forming machines
✅ Advantages of roll forming
✅ Common materials used in roll forming
✅ Industry applications
Let’s dive into the details!
How Does the Roll Forming Process Work?
The roll forming process involves continuously feeding a metal strip through a series of rollers, which gradually shape it into the final desired profile.
Step-by-Step Breakdown of the Roll Forming Process
Step | Description |
---|---|
1. Coil Loading | A metal coil is placed on the decoiler, feeding the material into the machine. |
2. Leveling & Guiding | The metal strip passes through a leveling unit, ensuring uniform thickness and alignment. |
3. Roll Forming Stages | The material moves through multiple roller stations, gradually forming the desired profile. |
4. Cutting & Punching | A cutting mechanism (hydraulic or servo-driven) trims the formed profile to the required length. |
5. Product Collection | The finished product exits the machine and is collected for further processing or shipment. |
👉 Did you know? Roll forming machines can operate at speeds of 10-100 meters per minute, making them significantly faster than other metal forming methods!
Types of Roll Forming Machines
Different industries require various roll forming machines based on profile complexity, material type, and production volume.
Machine Type | Features | Best For |
---|---|---|
Single Profile Roll Forming Machine | Designed to form one specific profile | Roofing sheets, wall panels |
Multi-Profile Roll Forming Machine | Capable of adjusting to produce different profiles | Racking & shelving, automotive parts |
CNC Roll Forming Machine | Computer-controlled for high precision | Complex and customized profiles |
Portable Roll Forming Machine | Compact and mobile | On-site construction work |
High-Speed Roll Forming Machine | Operates at high production speeds | Large-scale manufacturing |
WUXI SUNWAY MACHINERY CO., LTD specializes in customized roll forming machines designed for various industrial applications, ensuring high precision, durability, and efficiency.
Advantages of the Roll Forming Process
Why is roll forming the preferred method for metal profile manufacturing? Let’s break it down:
Key Benefits of Roll Forming
Advantage | Explanation |
---|---|
High Efficiency | Continuous production allows for faster output than stamping or press braking. |
Cost-Effective | Reduces material waste and labor costs. |
Precision & Consistency | Ensures uniform dimensions across all produced parts. |
Minimal Material Stress | Unlike press braking, roll forming applies gradual shaping, preventing cracks. |
Automation-Friendly | Can be integrated with CNC and AI monitoring for improved precision. |
Versatile Applications | Suitable for a wide range of industries, including construction, automotive, and renewable energy. |
👉 Compared to traditional metal forming, roll forming provides up to 30% higher efficiency and cost savings!
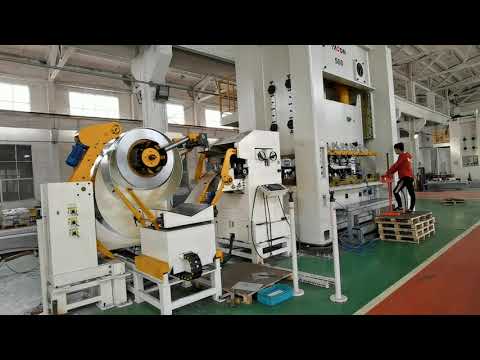
Best Materials for Roll Forming
The type of metal used in roll forming depends on the industry application and required profile strength.
Most Common Materials Used in Roll Forming
Material | Properties | Common Applications |
---|---|---|
Galvanized Steel | Corrosion-resistant, durable | Roofing, wall panels, HVAC ducts |
Stainless Steel | High strength, rust-resistant | Automotive, medical equipment |
Aluminum | Lightweight, flexible, corrosion-resistant | Solar mounting brackets, window frames |
Copper | Excellent conductivity, aesthetic appeal | Electrical components, decorative trims |
Cold Rolled Steel (CRS) | Smooth finish, strong | Industrial shelving, construction beams |
Sunway Machine provides custom roll forming solutions for specialized materials like solar mounting brackets, which require high precision and durability.
Industries Using Roll Forming Technology
Roll forming is used across various industries due to its ability to produce complex profiles efficiently.
Key Industries Benefiting from Roll Forming
Industry | Application | Example Products |
---|---|---|
Construction | Roofing, wall panels | Metal cladding, C & Z purlins |
Automotive | Structural components | Chassis parts, door beams |
Racking & Shelving | Storage solutions | Warehouse racks, supermarket shelves |
Renewable Energy | Solar panel mounting systems | PV mounting brackets |
HVAC | Air duct systems | Ventilation ducts, support channels |
Sunway Machine specializes in roll forming machines for racking & shelving, solar energy, and steel structures, ensuring high precision and durability.
Common Problems & Solutions in the Roll Forming Process
Even with high-quality machines, roll forming can face technical challenges. Here’s how to solve them:
Issue | Cause | Solution |
---|---|---|
Profile distortion | Misaligned rollers | Adjust roller settings |
Inconsistent cuts | Dull cutting blades | Replace or sharpen blades |
Material slippage | Poor grip on material | Increase roller pressure |
Machine vibration | Loose components | Tighten bolts and check stability |
👉 Regular machine maintenance is the key to avoiding production delays and ensuring long-term machine performance.
Roll Forming Automation: The Future of Metal Fabrication
As industries move toward Industry 4.0, automation in roll forming machines is enhancing efficiency, precision, and cost savings. Modern roll forming lines integrate CNC controls, AI monitoring, and real-time data analytics for optimized production.
Key Benefits of Automated Roll Forming Machines
Feature | Benefit |
---|---|
CNC Control Systems | Ensures precise measurements and reduces human error |
AI-Based Quality Inspection | Detects defects in real-time, minimizing waste |
IoT & Remote Monitoring | Allows operators to monitor machine performance from anywhere |
Automated Changeover | Reduces downtime when switching between profiles |
Energy Efficiency | Optimized power consumption lowers operational costs |
👉 Automation reduces production costs by up to 30% while improving product consistency!
Sunway Machine offers fully automated roll forming machines, designed for smart manufacturing and Industry 4.0 compliance.
Buying a Roll Forming Machine: What to Consider?
Purchasing a roll forming machine is a major investment. Here’s a step-by-step guide to choosing the right machine for your business.
Checklist for Buying a Roll Forming Machine
Factor | Importance |
---|---|
Production Volume | Choose a machine that meets your output needs |
Material Type | Ensure the machine can handle the required metal thickness |
Profile Complexity | Simple vs. multi-profile machines |
Automation Level | CNC and AI integration for high efficiency |
Budget & ROI | Consider long-term savings from reduced waste and labor costs |
Manufacturer Reputation | Work with a trusted brand like Sunway Machine |
Tip: Investing in a high-quality machine now will save you money on maintenance and downtime in the future.
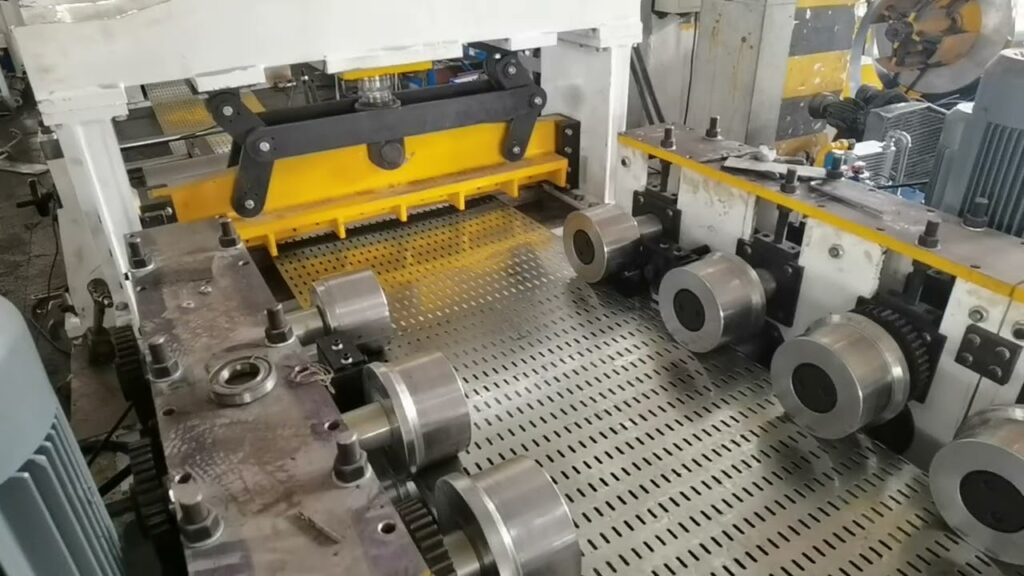
Roll Forming vs. Stamping: Which is Better?
Both roll forming and stamping are widely used in metal fabrication, but they serve different purposes.
Comparison Between Roll Forming and Stamping
Feature | Roll Forming | Stamping |
---|---|---|
Production Speed | High-speed continuous process | Slower, batch-based operation |
Material Waste | Minimal waste | More material scrap |
Setup Time | Longer initial setup, but fast production | Shorter setup, but slower production |
Best For | Long, continuous profiles | Complex, short-length parts |
Verdict: If you need continuous, high-volume production with minimal waste, roll forming is the ideal choice.
Future Trends in the Roll Forming Industry
The roll forming industry is evolving rapidly, incorporating new technologies to improve efficiency and sustainability.
1. AI & Predictive Maintenance
- AI sensors detect wear and tear before breakdowns occur.
- Predictive maintenance reduces downtime and repair costs.
2. Eco-Friendly Manufacturing
- Energy-efficient roll forming machines reduce carbon footprints.
- Recyclable materials are becoming standard in production.
3. Smart Factories & IoT Integration
- Machines can communicate with each other for optimized workflow.
- Remote monitoring and control improve efficiency.
By staying ahead of these trends, businesses can remain competitive and profitable.
FAQ: Roll Forming Process & Machines
1. How long does it take to set up a roll forming machine?
Setup time varies, but with quick-change tooling, it can take as little as 30 minutes.
2. Can roll forming machines be customized?
Yes! Sunway Machine offers custom roll forming machines tailored to specific profiles and materials.
3. What industries benefit most from roll forming?
Industries like construction, automotive, racking & shelving, and renewable energy rely heavily on roll forming for cost-effective, high-precision metal profiles.
4. How does roll forming compare to extrusion?
✅ Roll forming is best for thin sheet metal and continuous profiles.
✅ Extrusion is ideal for thicker materials like aluminum and plastic.
5. Where can I buy a high-quality roll forming machine?
For top-tier roll forming machines, visit WUXI SUNWAY MACHINERY CO., LTD.
Final Thoughts
The roll forming process is the future of high-speed, cost-effective metal fabrication. Whether you’re in construction, automotive, or renewable energy, roll forming ensures precision, efficiency, and minimal waste.
WUXI SUNWAY MACHINERY CO., LTD is a leading manufacturer of roll forming machines, offering customized solutions, expert support, and competitive pricing.
Want to optimize your production? Contact us today!