A Z profile forming machine is used to transform flat metal sheets and coils into sectional Z profiles with customized dimensions. It works by feeding the raw material through a series of vertical and horizontal rolls that progressively form the material into the desired shape through bending and pressing.
Z profile forming machines offer efficient, automated production of Z sections used extensively in construction, infrastructure, transportation and manufacturing applications. Their key capabilities are:
Forming Capability
- Produce sectional Z, C, Sigma, Omega and custom profiles
- Width range up to 1000mm
- Thickness up to 8mm for mild steel
- Works with variety of materials – steel, stainless steel, aluminum etc.
Automated Features
- Programmable for custom profiles via touchscreen
- Automatic material feeding and cutoff
- Minimum manual intervention required after setup
Benefits
- High productivity up to 40 meters/minute
- Consistent and uniform finished profiles
- Reduced labor compared to manual fabrication
- Flexible production volumes in short lead times
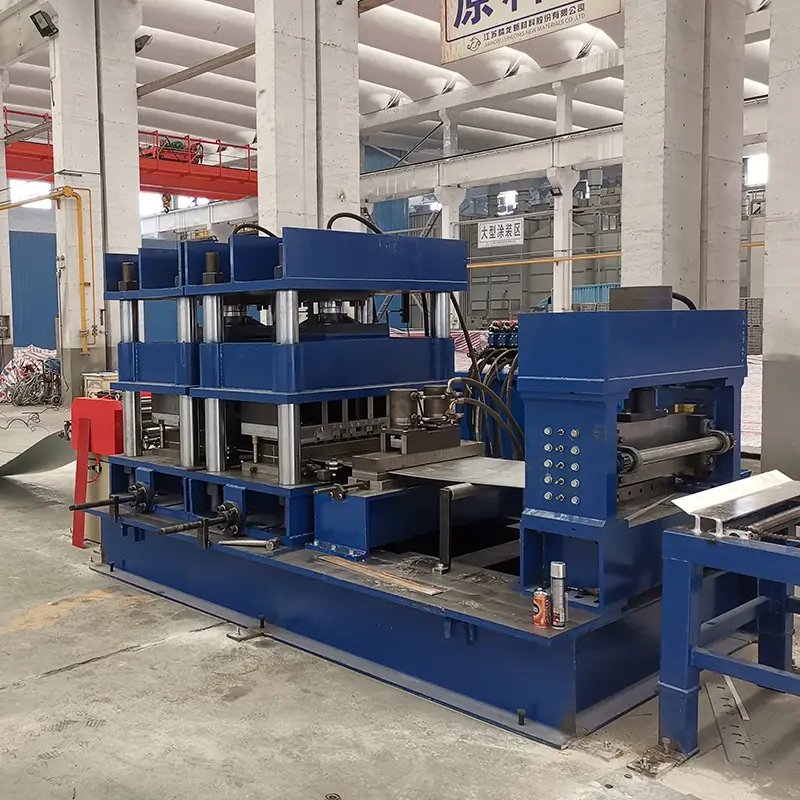
Components of Z Profile Forming Machine
The major components of a Z profile forming machine are:
Table: Components of Z Profile Forming Machine
Component | Description |
---|---|
Uncoiler | Feeds raw steel coil to forming section |
Straightening machine | Corrects coil curvature for proper feeding |
Feed rollers | Pulls metal sheet into forming section |
Forming rolls | Progressively bend metal into Z shape |
Punch/Shear | Cuts formed profile to desired length |
Controller | Touchscreen to input profile design data |
Hydraulic system | Applies pressure on rolls to form metal |
Conveyor | Transports finished profiles for storage/packing |
Working Process of Z Profile Forming Machine
The working process on a Z profile forming machine follows continuous roll forming principles:
- Raw steel coil loaded onto uncoiler mandrel
- Sheet passes through straightening machine
- Feed rollers pull flattened sheet into forming section
- Sheet moves through series of top and bottom vertical forming rolls
- Rolls bend sheet progressively into Z shape through steps
- Formed profile extracted on other end and cutoff by punch/shear
- Hydraulic pressure on rolls can be varied for custom shapes
- Touchscreen controller allows fast design data inputs
- Conveyor system transports finished Z profiles from machine
Types of Z Profile Forming Machines
Machine Type | Description |
---|---|
Mechanical | Basic model with manual adjustment of forming rolls |
Hydraulic | Automated roll adjustment via hydraulics |
CNC | Fully programmable using computer numerical control |
Servo-motor | Advanced CNC with servo motors for precision |
-
Corrugated Panel Roll Forming Machine
-
Light Gauge Steel Roll Forming Machine
-
C Section Bracing Omega Storage Rack Upright Post Roll Forming Machine
-
Steel Box Plate Making Roll Forming Machine
-
Box Beam Steel Roll Forming Machine For Shelf Column
-
Pallet Racking Step Beam P Beam Roll Forming Machine
-
Warehouse Shelf Upright Roll Forming Machine
-
Din Rail Roll Forming Machine
-
Omega Purlin Roll Forming Machine
Materials for Z Profile Forming
Z profile forming machinery can handle a wide range of materials including:
- Low carbon steel
- High strength steel
- Stainless steel
- Aluminum (series 1000, 3000, 5000 & 6000)
- Galvanized steel
- Pre-painted steel
Max thickness capacity varies by model from 6mm to 12mm. Machines with higher tonnage have more power to form thicker material.
Design and Customization
- Width – Customizable from 50mm to 1000mm
- Height – Up to 300mm by adjusting roll position
- Thickness – Up to 12mm based on machine capacity
- Length – Adjustable cutoff from 0.5m to 6m
- Angle – Vary lip angle from 30 to 140 degrees
- Curvature – Straight or add sweep via custom top rolls
Advanced touchscreen control allows fast design edits. Custom profiles stored for future repeat orders.
Slicing Method
The punching unit uses ultra-durable tools made from tool steel to shear the profiles:
- Rotary flying punch and die system
- Flywheel mechanism for extra cutting force
- Adjustable stroke length up to 100mm
- cutting capacity – 8mm thickness mild steel
Blades have Teflon inserts to prevent material sticking. Rapid replaceable modular tooling to minimize changeover times.
Key Z Profile Forming Machine Suppliers
Supplier | Location | Models | Price Range |
---|---|---|---|
ETP | India | MANZ, AUTOSLIT | $100,000 to $250,000 |
Formtek | Taiwan | FZM, ERW | $80,000 to $150,000 |
Jinan FA | China | JFZ, JFD | $50,000 to $280,000 |
Anant Engineering | India | SPEL, ZPRO | $35,000 to $185,000 |
Gensco Equipment | USA | GZF, ERW | $250,000 to $480,000 |
Installation and Operation
Task | Details |
---|---|
Installation | Level concrete floor <br> 3-phase power supply <br> Air compressor |
Space Required | 16ft x 65ft approx |
Power Required | 25 to 60kW |
Air Pressure | 4 to 6 bar |
Operation | 1 to 2 semi-skilled operators |
Lifespan | Over 100,000 hours under maintenence |
Maintenance of Z Profile Forming Machine
Activity | Frequency |
---|---|
Cleaning | Daily |
Inspection | Weekly |
Lubrication | Monthly |
Tool Changes | As needed |
Operator Training | Initial and refresher |
Choosing the Right Z Profile Forming Machine Supplier
Here are key considerations for selecting supplier:
Table: How to Choose Z Profile Forming Machine
Parameter | Evaluation Criteria |
---|---|
Technology | Advanced CNC/servo-motor preferred |
Build Quality | Rugged frames withstand vibration |
Testing Standards | ISO, CE marked electrical parts |
Reliability | Evidence of repeat clients |
Line Integration | Offering allied machines preferred |
Customization | Dimension/profile flexibility |
Service Record | Response time and quality |
Training Offered | Installation guidance + operator manuals |
Pricing | Competitive pricing for features |
Financing Options | Available payment terms |
Pros and Cons of Z Profile Forming Machines
Pros | Cons |
---|---|
Highly productive automated process | High machine cost due to heavy-duty construction |
Zero shape limit – produce any custom profile | Significant operating power requirement |
Superior and uniform finished quality | Setup can take time initially |
Saves time and cost vs manual fabrication | Limited thickness capacity on lower tonnage models |
Just-in-time low volume production | Requires floor space and proper foundations |
Easy integration with allied machines | Operating skill development takes time |
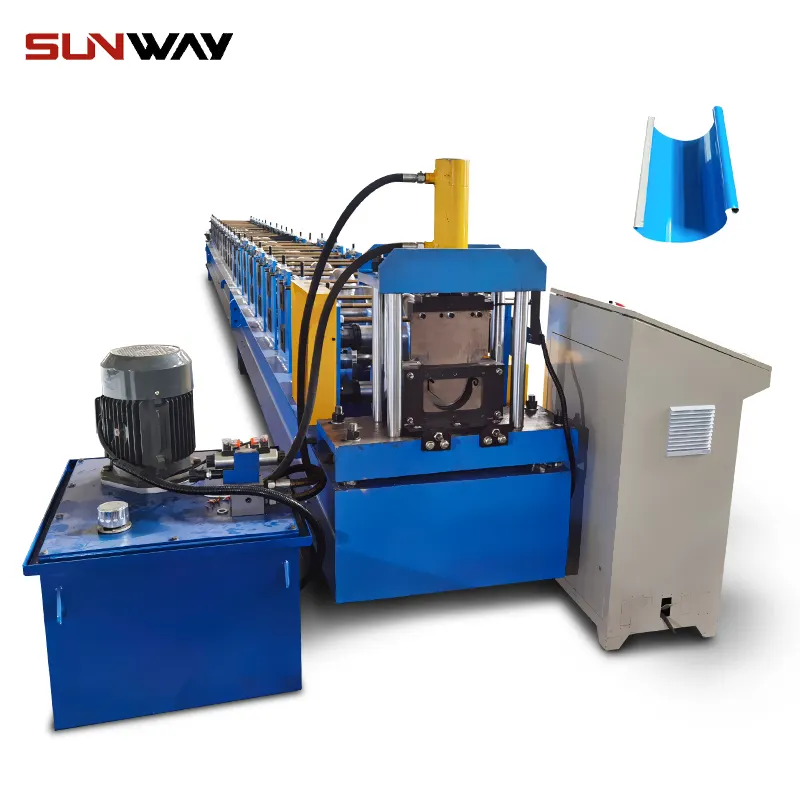
FAQ
What is the difference between CNC and servo motor Z profile machines?
CNC Z profile machines allow customization of parameters like width, height, angles etc via an onboard computer interface. Servo motor models enhance the precision further by incorporating servomotors to independently control the position and velocity of forming rolls. This enables intricate profile shapes to be formed with high accuracy and repeatability.
What allied machines can be integrated with Z profile forming lines?
- Decoilers for sheet preparation
- Embossing machinery
- Profile punches
- Cutoff saws
- Drilling machines
- Marking stations
- Packaging equipment
What quality standards should Z profile machine manufacturers follow?
Reputable manufacturers comply with international standards like ISO 9001 as well as CE directives covering design, performance and safety of machinery. Certified electrical components and strict dimensional tolerances also demonstrate product quality levels. Client references offer credibility.
What level of operators are required for Z profile machines?
Z profile machinery can be run by operators with ITI/diploma qualifications after product-specific training. One operator typically manages the uncoiling and feeding sections, while second operator attends to formed profile output as well as cutoff.
What auxiliary equipment do Z profile forming lines require?
- Decoiler handling equipment like lift trucks for loading raw coils
- Conveyor systems to manage finished profile lengths
- Packaging infrastructure – bundling machines, strapping tools
- Inspection tables for quality checks
- Material handling solutions – cranes, forklifts etc.