Roll forming allows continuous, efficient production of straight or curved plastic profile sections by gradually bending sheets through consecutive stands. Laminated polyethylene (PE) foam profiles made via roll forming find wide use for insulation, cushioning and shock absorption across industries.
This guide provides a comprehensive overview of laminated pe foam roll forming machine capabilities, workings, considerations and applications to help prospective buyers make optimal equipment decisions.
Overview of Laminated PE Foam Roll Forming Machines
Roll forming machines shape plastic sheets into various standard or customized cross-section profiles for industrial applications via a series of incremental roller bending stations.
Key attributes of laminated PE foam roll formers:
- Raw material: PE foam laminated with variety of sheet types
- Lamination methods: Adhesive, heat, ultrasonic etc.
- Profile types: U channel, rectangular, other heat insulation shapes
- Tooling flexibility: Quick changeovers for profile variations
- High production speeds up to 80 meter/minute
- Advanced process monitoring and control systems
Laminating PE foam to other sheets combines insulation abilities with strengths and surface properties using only thin adhesive layers. Roll formed laminates save energy in use while cutting transportation and inventory costs.
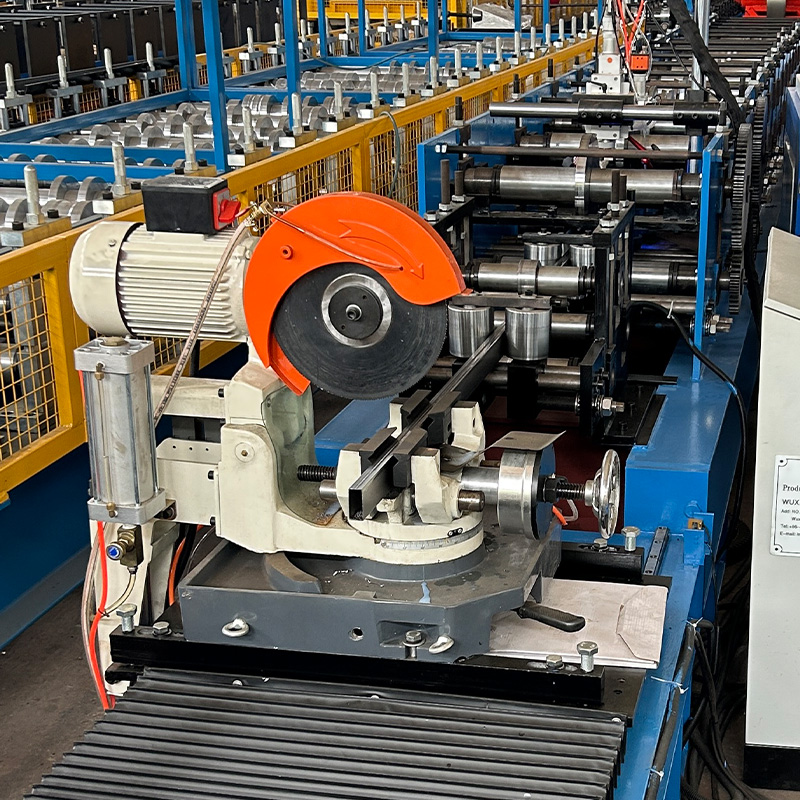
Types of Laminated PE Foam Roll Forming Machines
Machine Type | Description |
---|---|
Standard | Designed for high volume production of 1-2 profiles |
Quick changeover | Multiple tooling sets for fast profile variations |
Custom | Tailored around specialized insulation shapes |
Automatic cutoff | Integrated cross-cutting saw unit |
Secondary processing | Additional modules like punching, drilling, printing etc. |
Specialized capabilities:
- Multi-layer lamination
- Post-formation welding
- Detachable wrap film devices
- Vision systems for defect detection
- Stackers and bundling systems
Working Principle of Laminated PE Foam Roll Forming
The working principle focuses on bending plastic sheets through a series progressively arranged roller stations to create customized profile sections.
Steps:
- Plastic lamination sheet pays off mounted coil
- Sheet feeding tables guide strip through machine
- Forming heads apply incremental bends by pressing sheet around shaped rollers
- Separate cutoff saw trims formed profile to length
- Exit conveyors guide trimmed pieces for packaging/shipping
Advanced process control systems including PLC, HMI and sensors enable real-time monitoring and precision speed/tension regulation during production.
Easy interchangeability of tooling components like forming heads allows fast changeovers between different laminated foam profiles.
Process Flow of Laminated PE Foam Roll Forming
A typical process flow for laminated foam profile creation comprises:
1. Plastic Sheet Selection
- Polyethylene foams laminated with metal, plastic, paper sheets
- Adhesive selection for strength and temperature range
2. Sheet Preparation
- Cleaning, preheating, surface activation
3. Roll Lamination
- Binding foam with other sheets between roller beds
4. Roll Forming
- Multi-stage bending into structural shape
5. Secondary Processing (optional)
- Printing, hole punching, welding, coating
6. Product Cutoff and Handling
- Cutting laminated profiles to length
- Bundling and packing finished pieces
Quality checks performed at each stage sustain consistency. Individual sections can be enhanced with additional capabilities to impart special properties.
Design Considerations for Laminated PE Foam Roll Forming Lines
Key aspects of designing laminated foam profile roll forming systems include:
Sheet Material Selection
Common materials laminated with PE foam:
- PP, ABS, PVC plastic sheets
- Steel, Aluminium sheets
- Cardboard, textiles, reflective sheets
Each material adds unique structural, insulating or aesthetic properties.
Profile Shape and Size
Common roll formed foam laminate shapes:
- U channel for heat insulation
- Rectangular tube surrounds
- Custom enclosures, edge guards, corner pieces
Tooling flexibility allows fast transition between shapes.
Production Speed
Higher production rates via wider plastic sheets or faster roller movement increases output.
- Light duty: Up to 20 meters/minute
- Medium duty: 20-50 meters/minute
- Heavy duty: Over 50 meters/minute
Tooling and Stations
- Number of stands determined by profile complexity
- Quick changeover heads for shape variations
- Roller materials resistant to wear
- Integrated heating systems
Additional Capabilities
- Inline lamination |
- Printing
- Perforation
- Punching
- Cutoff
- Wrapping
- Vision inspection
- Bundling
-
Corrugated Panel Roll Forming Machine
-
Light Gauge Steel Roll Forming Machine
-
Steel Box Plate Making Roll Forming Machine
-
Din Rail Roll Forming Machine
-
Omega Purlin Roll Forming Machine
-
CZ Purlin Roll forming machine
-
Full automatic C purlin roll forming machine quick-change
-
Standing Seam Roof Panel Forming Machine
-
Roof Tile Roll Forming Machine
Key Components of Laminated PE Foam Roll Forming Machines
Component | Purpose |
---|---|
Decoiler | Smooth sheet payoff |
Feed tables | Guide strips into process flow |
Forming heads | Progressive profile bending |
Roller stations | House forming heads |
PLC control | Monitoring and precision |
HMI | Parameter input and monitoring |
Sensors | Feedback signals to detect issues |
Heating systems | Assist with lamination |
Secondary modules | Additional processing |
Exit tables | Support finished profiles |
Buying Considerations for Laminated PE Foam Roll Forming Machines
Key factors in purchasing laminated foam profile roll forming equipment:
Parameter | Guidelines |
---|---|
Type of profiles needed | U channel, rectangular, custom |
Material width | Optimal for high output rates |
Production speed | Balance cost against hourly output |
Raw material type | PE foam + sheet compatibility |
Tooling flexibility | Quick changeover performance |
Climate control | For consistent material properties |
Defect detection | Visual, ultrasonic, laser |
Secondary processing | Lamination method, printing etc. |
Controls sophistication | Sensor feedback, diagnostics etc. |
Supplier credentials | Experience, production expertise |
Evaluate options from multiple laminated foam profile machine manufacturers against current and future business requirements for optimal value.
Installation of Laminated PE Foam Roll Forming Machines
Proper machine installation lays the base for efficient functioning during mass production.
Key aspects:
- Stable, level foundation
- Adequate space for safe operation
- Power supply protections
- Decoiler mounting provisions
- Guarding around moving parts
- Control panel accessibility
- Confirm alignment, sensor signals
- Test run at low speeds
Ensure qualified technicians handle positioning, assembly, trial runs and training to prevent issues down the line.
Operation of Laminated PE Foam Roll Forming Lines
Follow standardized protocols during machine operation for consistency.
Safety Guidelines
- Allow only trained workers in work area
- Ensure no exposure near rotating tooling
- Barricade operational area appropriately
- Mandate hand gloves, shoes, glasses use
Production Workflow
1. Material Loading
- Mount plastic + foam coils on decoilers
- Thread sheets through components
2. Parameter Setting
- Enter dimensions, speeds, temperatures
3. Trial Run
- Inch at slower pace initially
- Confirm signal feedbacks
4. Production
- Run at specified rating
- Monitor for process deviations
- Conduct quality checks
Document all procedures for easy operator reference. Real-time monitoring necessary to catch defects early.
Maintenance of Laminated PE Foam Roll Forming Machines
Regular preventative maintenance activities sustain performance and minimize unplanned downtime losses.
Activity | Method | Frequency |
---|---|---|
Machine cleaning | Remove plastic dust and residue | Daily |
Sensor checks | Compare signal values to benchmarks | Weekly |
Oil lubrication | Replenish gearbox oil levels | Monthly |
Hydraulic inspection | Check fluid leaks, pipe condition | Monthly |
Belt tensioning | Use tension meter, adjust as needed | Quarterly |
Roller service | Refurbish or replace forming heads | Yearly or as needed |
Motor checks | Replace worn out motors | As needed |
Electrical safety | Confirm insulations, protect circuits | Quarterly |
Machine calibration | Reset benchmarks, tolerances | Yearly |
Schedule activities to utilize planned maintenance downtime optimally. Keep maintenance logs for analyzing recurring problems.
Choosing Laminated PE Foam Roll Forming Machine Manufacturers
Parameters for selecting suppliers:
Consideration | Guidelines |
---|---|
Product range | Variety of profile types producible |
Machine quality | Durability, precision, consistency |
Production expertise | Staff skill, plant sophistication |
Customization skills | Flexibility for profile variations |
Responsiveness | Speed of service and support |
Certifications | ISO, CE markings |
Pricing | Competitive quotes and transparency |
Post-sales support | Installation, maintenance etc. |
Talk to industry peers for supplier referrals. Evaluate options on production volume scalability and after-sales assistance too.
Pros and Cons of Laminated PE Foam Roll Forming Machines
Advantages
- High production rate with consistency
- Ideal for long production runs
- Customizable insulation laminate profiles
- Improved strength via lamination
- Automated process control benefits
- Limited manpower needed
- Lower costs than molding or machining
Limitations
- High initial capital investment
- Skill essential for operation and maintenance
- Design complexity limits profile shapes
When designed and operated properly, roll forming offers efficient, high quality production of customized laminated foam profiles.
Cost Analysis of Laminated PE Foam Roll Forming Lines
Machine Rating | Price Range |
---|---|
Light duty | $45000 to $65000 |
Medium duty | $65000 to $95000 |
Heavy duty | $95000 to $185000 |
Secondary processing modules | +$5000 per station |
Influencing cost factors:
- Production speed and width capacity
- Type and complexity of tooling
- Level of automation and control systems
- Manufacturer’s brand value and production scales
- Additional equipment integrations
Higher equipment investment generally gets compensated by operational cost savings down the line.
Applications of Laminated PE Foam Profile Roll Forming Machines
Industries utilizing roll formed laminated foam profiles:
HVAC and Construction:
- U channel insulation cladding
- Window/door weatherstrips
- Duct liners and edge protection
Automotive:
- Interior door panels, roof, trunk liners
- Engine bay cladding
- Anti-vibration components
Appliances and Consumer Goods:
- Refrigerator/oven/AC casing liners
- Furniture edge banding
- Electronics shielding
Packaging:
- Shock absorbing inserts
- Insulated containers
- Edge guards
Such profiles combine insulation, noise damping, shock absorption with surface durability economically.
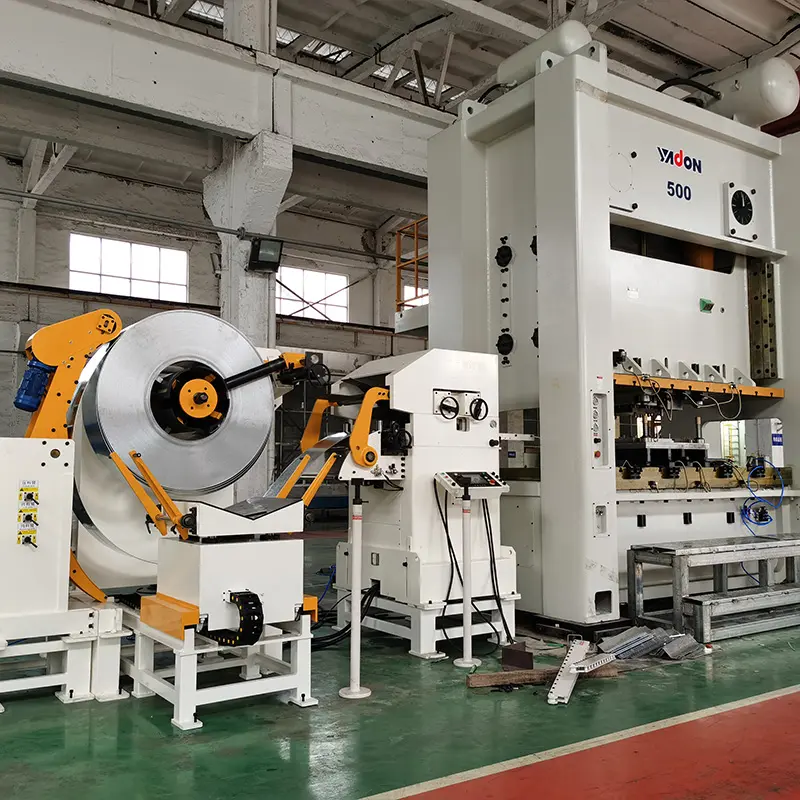
Conclusion
Laminated PE foam roll forming lines allow automated production of straight or curved profiles by bending plastic sheets reinforced with metal, plastic or paper outer layers.
When designed properly around production volume, line speed, profile type/complexity and any secondary processing needs – they consistently manufacture high quality, customizable laminated insulation components for industries like HVAC, construction, automotive etc.
Careful equipment selection coupled with standardized installation, operation and maintenance best practices results in good ROI via raw material savings, energy efficiency and scrap minimization.
Partnering with expert roll form machinery manufacturers helps translate application requirements into tailored forming solutions augmenting productivity and competitiveness. Leveraging such production innovation and customization accelerates development of improved insulated products.
FAQs
Q: What materials can be laminated with PE foam for roll forming?
A: PE foam provides good binding compatibility with sheets of PP, PVC, ABS, acrylic plastics along with aluminium, steel and even paper or textile. Adhesive type and process parameters need tuning for each combo.
Q: What CNC capabilities are needed for laminated profile roll forming?
A: Standard CNC 3-axis controls for incremental profile bending movements suffice for most designs. Complex shapes may utilize specialized 5-axis controls for optimal material flow and forming.
Q: How to calculate machine rating needed for my production scale?
A: Material width in mm multiplied by maximum line speed in m/min provides the hourly linear meter output. Comparing this against current and projected production volume requirements gives machine rating needs.
Q: Can polymer foam sheets be directly roll formed without lamination?
A: Yes, but doing so restricts profile geometry to mostly simpler shapes like tubes due to flexibility and springback tendencies needing more tooling stations. Lamination provides structural reinforcement allowing complex profile roll forming.
Q: How does roll formed laminated foam compare with extruded foam on insulation properties?
A: Directly extruded foam sheets generally offer slightly better insulation per unit thickness owing to inherent material expansion during exit. But thinner laminated foam can match insulation levels at lower overall weight.
Q: What regular maintenance helps sustain roll formed laminate quality?
A: Activities like machine cleaning, belt tensioning, lubrication, visual inspection, sensor checks, calibration, heating system health etc. are vital for uninterrupted production without quality fluctuations.
Q: Can decorative laminates be added to foam profiles via roll forming?
A: Yes, visual allure can be enhanced by using colored laminates or by post-production methods like painting, printing, hot stamping. Even embedding wires, beads is possible for lighting or heating effects.
Q: How to minimize scrap generation during foam laminate roll forming?
A: Scrap is unavoidable when stabilizing production but can be reduced via positive feed control, edge guiders, optical defect monitoring and precision cutting to length after line stabilization.